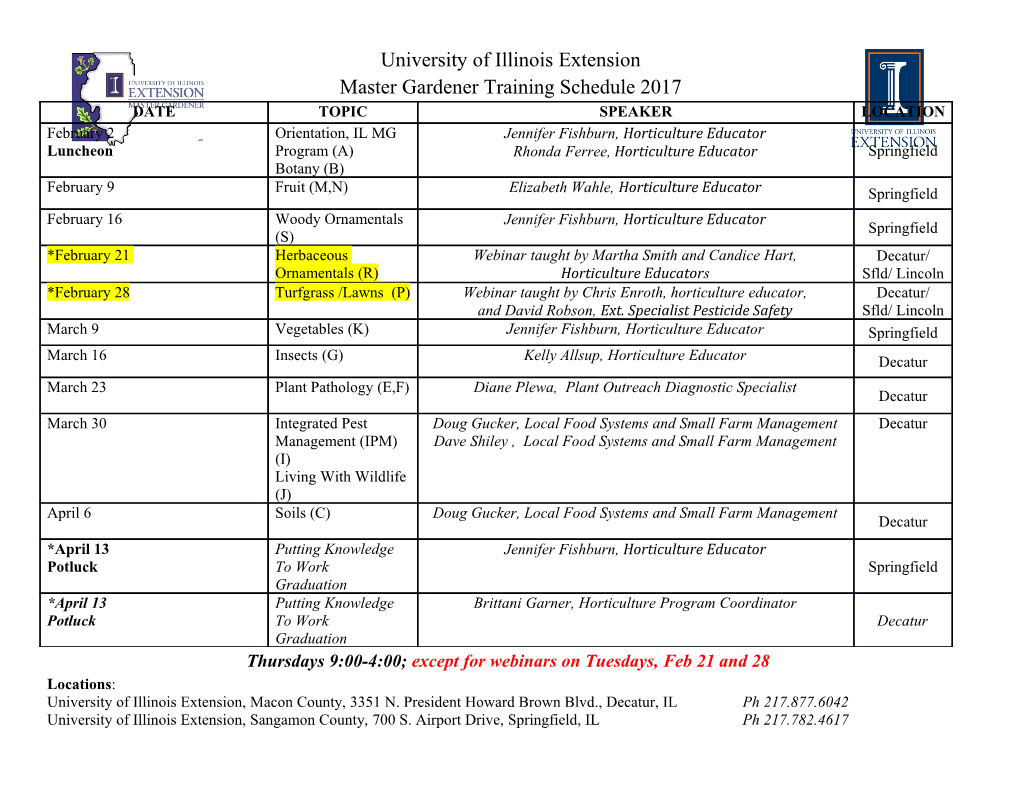
International Journal of Research Studies in Science, Engineering and Technology Volume 4, Issue 7, 2017, PP 1-12 ISSN : 2349-476X Kaizen and 5S as Lean Manufacturing Tools for Discreat Production Systems: A Study of the Feasibility in a Textile Company C.P.Carvalho¹, L.W.N.Gonçalves² and M.B.Silva¹, ¹Department of Chemistry, School of Engineering of Lorena, São Paulo State University, Lorena, São Paulo, Brazil ²Industrial Engineering Department, Salesian University Center of São Paulo, Lorena, Brazil. *Corresponding Author:C.P.Carvalho,¹Department of Chemistry, School of Engineering of Lorena ,São Paulo State University, Lorena, São Paulo, [email protected] Received Date: 21-09-2017 Accepted Date: 25-09-2017 Published Date: 07-10-2017 ABSTRACT At present there is a growing search for entrepreneurs about process optimization tools, where the greatest need and purpose is to keep their organizations active in the competitive market. It is seen that a company needs to ensure the high quality of its products and the continuous improvement of its processes, and this explains the concern to eliminate wastes in the production line. Such wastes can be defined as production elements that absorb resources and increase the cost without adding value to the product. There are numerous tools that help minimize waste during production, and many of them are part of a line of thinking called Lean Manufacturing (LM). In this context, it is hoped to demonstrate together the theme Lean the relevance of the theme Kaizen and 5S's, where in the business scope Kaizen is a tool that allows to reduce costs and to improve productivity, and already the 5S to organize the environment and to generate better This work presents the study of the applicability of LM in a textile company in its continuous production system. By combining the two tools of the LM, Kaizen and 5S, simulation had an impact in reducing the main losses presented in the production flow. The justification for this work is based on the fact that LM tools in continuous production systems. Keywords: Continuous manufacturing, Textile, Lean Manufacturing, Kaizen, 5S INTRODUCTION transportation, over processing, inventory, handling, and defective products. Value to the In the last two decades, many Brazilian textile customer and, at the same time, consume the companies have faced the effects of least amount of resources. Nowadays, the globalization. The competition imposed by the concept of LM is a well-publicized subject in emerging countries has become fierce in price. the literature. Hines [3] presented the concept of To survive in this scenario, some organizations process improvement with the implementation began implementing programs to improve their of LM. competitiveness. Most of these programs were based on Japanese production concepts. The In this way, this work deals with the LM theme concepts of lean production, lean manufacturing with emphasis on the application of Kaizen, as (LM), were based on the Toyota Production well as notes about 5S, which, when applied System [1]. The word LM is believed by accurately, tend to generate better organization, Womack, Jones and Ross [2] in his work called optimization of processes and consequently The Machine that Changed the World. The goal profitability of the organizations that use these of LM is to eliminate wastes in manufacturing methods. processes by removing items that do not add This paper will present some processes observed value to the product or service under the as critical in the company studied. Through this, customer's vision. Ohno [1] describes seven possible and even demonstrative solutions with types of production wastes that may derive from before and after application of the improvement the following: overproduction, waiting, will be presented. International Journal of Research Studies in Science, Engineering and Technology V4 ● I7 ● 2017 1 Kaizen and 5S as Lean Manufacturing Tools for Discreat Production Systems: A Study of the Fiseability in a Textile Company At the end of the project it is expected that the The Lean methodology and its tools have been company studied obtain better gains, both in used in different scenarios and segments, and quality and financial, after all, each day the the more their domain evolves and continues to market becomes more competitive and be dissipated, the more criticisms also arise. The constantly changing. Therefore, organizations literature on lean management seems to tend to adopt flexible management models, converge to the assumption that efficacy would aiming at the implementation of strategic tools be limited to contexts of discrete and repetitive to remain competitive and achieve longevity in manufacturing, where it was initially developed the current market [4]. [8]. Discrete manufacturing companies such as the automotive and electronics have great There is a great need for an organizational benefits with this practice, however, few studies planning in order to promote constant appear to prove this success in adopting Lean in improvements, thus minimizing errors, a universal format for all types of organizations. eliminating waste and reducing costs. For this, organizations must take into account critical According to Werekema [9] one of the factors such as committed team, effective important points to be highlighted is that the leadership, aligned goals, and culture of adoption of Lean Manufacturing represents a continuous improvement, as well as having a process of changing the organization's culture full understanding of the internal and external and, therefore, is not easy to achieve. Therefore, environment of their business [5]. using one or more Lean tools does not guarantee that you will succeed in implementing lean In describing LM, Bahmu [6] in his literary production. review mentions that Lean's goal is to meet customer demand by minimizing waste, also It is argued that some articles mention cites that Lean practices seek to produce low limitations to the implementation of lean cost and low response time. manufacturing and suggest that this is due to the differences between the pioneer industry and the LITERATURE REVIEW one that is trying to apply [3,10]. These In this section, topics related to the LM theme differences may include volume or variety [11]. will be presented, where Kaizen and 5S tools It is known that Toyota Production System is will be presented, which are used to optimize based on the total elimination of waste, and the processes in various conditions, whether two fundamental pillars that give support to the business or private. system are: Just-in-time and Automation. Lean Therefore, according to Scheunemann [12] Just- in-time is a flow process, whose purpose is the The LM solutions to increase production exact control of the items in the production efficiency with the applicability of one or more process, where the inputs arrive at the process at tools is needed, such as: Kanban, Kaizen, TPM, the right time and in the necessary quantity. A 5S, SMED and VSM, the latter is the main tool company that establishes this flow integrally can utilized in this article and will be mentioned in the reach zero stock. We have that automation is topic below The Lean Production System is a set defined as the mechanization of the operation, of activities aimed at increasing the capacity to while Automation with human touch, confers respond to changes and minimizing waste in human intelligence to the machine. production, establishing a truly innovative According to Azharul [13] despite the great management organization. These organizations potential of strategies to achieve lean have the following principles: to have (and production, many studies report failures in the maintain) the right items in the right places, at expected result of the lean application, so it has the right time, and in the right quantity; Create what is essential or monitoring each process to and nurture effective relationships within the enable an application of this tool. Value Chain; Work towards Continuous Improvement in search of Optimum Quality in Kaizen the first unit delivered. The Lean Production Continuous improvement is a concept that has system looks for economy and consistency in great relevance in an industrial context. In other movement through the study of methods and words, for a change to improve processes. The work times, drawing attention to simple, low- most famous concepts associated with cost solutions [7]. continuous improvement also did not arise from 2 International Journal of Research Studies in Science, Engineering and Technology V4 ● I7 ● 2017 Kaizen and 5S as Lean Manufacturing Tools for Discreat Production Systems: A Study of the Fiseability in a Textile Company the Toyota automotive industry already Womack and Jones [15] characterize the term mentioned, the organization is responsible for Kaizen as "incremental continuous developing the Kaizen philosophy. improvement" in activities normally performed by groups of employees who collaborate to It is possible to say that philosophy is a method eliminate waste or problems in the production of eliminating despair based on good sense, line by using the value stream mapping without using cheap solutions to help the technique. As Scotelano [16] states, this stems motivation and creativity of employees to from the philosophy of eliminating waste based improve the practice of work processes, in the on common sense and the use of low cost pursuit of continuous improvement. The word solutions that support
Details
-
File Typepdf
-
Upload Time-
-
Content LanguagesEnglish
-
Upload UserAnonymous/Not logged-in
-
File Pages12 Page
-
File Size-