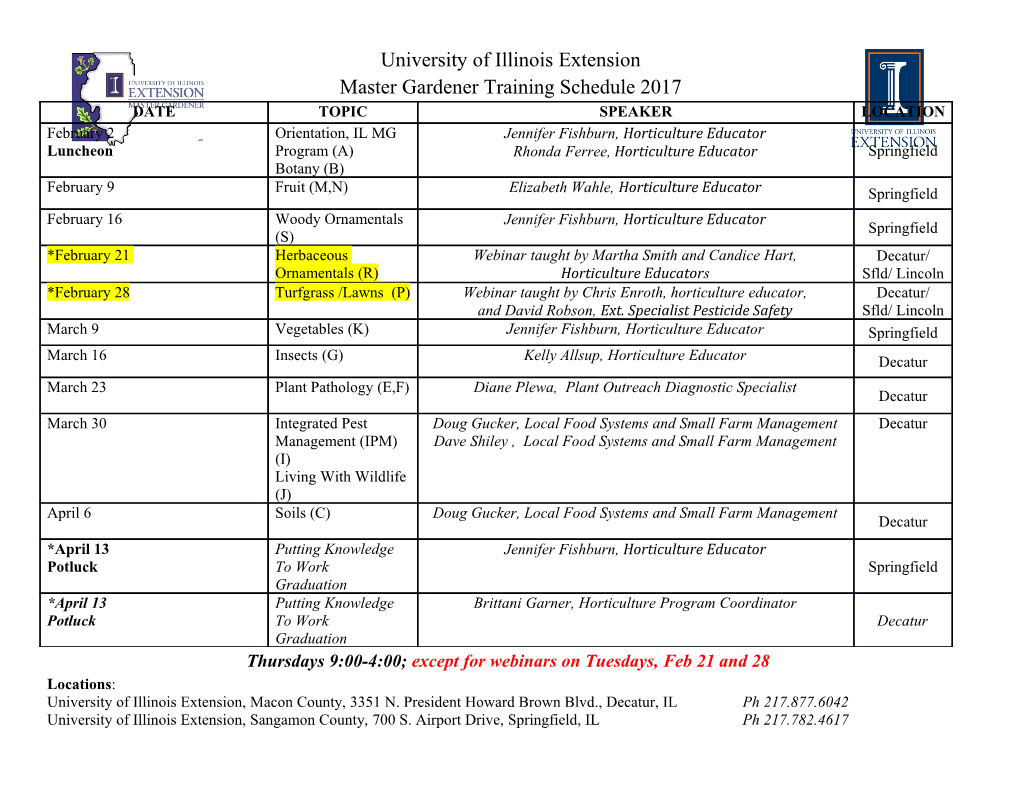
Vickers® General Product Support Hydraulic Hints & Trouble Shooting Guide Revised 8/96 694 General Hydraulic Hints . 3 Troubleshooting Guide & Maintenance Hints . 4 Chart 1 Excessive Noise . 5 Chart 2 Excessive Heat . 6 Chart 3 Incorrect Flow . 7 Chart 4 Incorrect Pressure . 8 Chart 5 Faulty Operation . 9 Quiet Hydraulics . 10 Contamination Control . 11 Hints on Maintenance of Hydraulic Fluid in the System. 13 Aeration . 14 Leakage Control . 15 Hydraulic Fluid and Temperature Recommendations for Industrial Machinery. 16 Hydraulic Fluid and Temperature Recommendations for Mobile Hydraulic Systems. 19 Oil Viscosity Recommendations . 20 Pump Test Procedure for Evaluation of Antiwear Fluids for Mobile Systems. 21 Oil Flow Velocity in Tubing . 23 Pipe Sizes and Pressure Ratings . 24 Preparation of Pipes, Tubes and Fittings Before Installation in a Hydraulic System. 25 ISO/ANSI Basic Symbols for Fluid Power Equipment and Systems. 26 Conversion Factors . 29 Hydraulic Formulas . 29 2 General Hydraulic Hints Good Assembly Pipes Tubing Do’s And Don’ts Practices Iron and steel pipes were the first kinds Don’t take heavy cuts on thin wall tubing of plumbing used to conduct fluid with a tubing cutter. Use light cuts to Most important – cleanliness. between system components. At prevent deformation of the tube end. If All openings in the reservoir should be present, pipe is the least expensive way the tube end is out or round, a greater to go when assembling a system. possibility of a poor connection exists. sealed after cleaning. Seamless steel pipe is recommended No grinding or welding operations for use in hydraulic systems with the Ream tubing only for removal of burrs. should be done in the area where pipe interior free of rust, scale and dirt. DO NOT over ream tubing as it can hydraulic components are being weaken the connection. Early classifications of pipe wall installed. thicknesses were: standard, extra heavy Do not allow chips to accumulate in the All cylinder, valve, pump and hose and double extra heavy. tubing. They can be difficult to remove connections should be sealed and/or after bending. Today, pipes are classified by schedule capped until just prior to use. number as specified by the American Follow the manufacturers Mineral spirits should be kept in safety National Standards Institute (ANSI). The recommendations on the use of flaring containers. schedule numbers vary from 10 through tools. Don’t overtighten the feed screw 160. The larger the number, the heavier handle on a compression type flaring tool. Air hoses can be used to clean fittings the wall thickness. The outer pipe Improper use of a tool can cause washout and other system components. However, diameter stays the same for a given pipe and/or splitting of the flare connection. the air supply must be filtered and dry to size, while the inside opening becomes prevent contamination of the parts. smaller as schedule number increases. Bend tubing instead of cutting and using a fitting. This reduces pressure drop and Examine pipe fittings and hose A comparison of early classifications minimizes system losses. The minimum assemblies prior to use to be certain that versus the ANSI classification follows: radius of a tubing bend should be at burrs, dirt and/or scale are not present. least three times the inside diameter of Standard – Schedule 40 the tube. Larger bends are preferred. All pipe and tubing ends should be Extra Heavy – Schedule 80 reamed to prevent restriction and Sketch the optimum tubing route before turbulent flow. The double extra heavy classification beginning the bending process. Be sure does not compare with a schedule to use tubing with the proper temper to Do not use Teflon tape on straight number. However, the inside diameter of prevent wrinkles and flattened bends. thread connections. a double extra heavy pipe is approximately one half that of a schedule Most flares are made by hand or power When installing pumps or motors, 160 pipe. tools that swage the tube end over a always align coupling halves as closely split die. The standard flare angle is 37 as possible, within 0.007 inch. In many cases, flanges are welded to degrees from the centerline. For best the pipe ends and gaskets or “O” rings results, heavy wall tubing should be cut, When using flexible couplings, follow the are used to seal the connections. deburred, and flared and bent using manufacturer’s recommendations or Various pipe fittings are used to route power equipment. allow 1/32 to 1/16 inch clearance the piping to and from each system between the coupling halves. component. These fittings can be For information on sealing technology, or threaded or welded in place as the need how to prevent leakage of hydraulic fluid, Do not drive couplings on pump or arises. Threaded connections are used refer to “Leakage Control” in this catalog. motor shafts. They should be a slip fit, in low pressure applications and welded or shrunk on using hot oil. connections are used if high pressure, Always use a dry spray-on lubricant on high temperature, or a severe splines when installing. This prevents mechanical load exists. wear and adds to the life of the splines. All piping should be secured with When using double universal joint clamps to prevent vibration and couplings, the shafts must be parallel excessive stress due to the weight of and the yokes must be in line. the fluid. Do not weld the clamps to the pipe as it may weaken the pipe and When installing V-belt pulleys on pumps cause a stress crack. or motors, line up both pulleys as closely as possible. Always install the pulleys with a minimum amount of overhang as close to the pump or motor face as possible. This increases bearing service life. 3 Troubleshooting Guide & Maintenance Hints 1. Know the capabilities of the system. 1. Excessive heat means trouble. A General Each component in the system has a misaligned coupling places an The troubleshooting charts and maximum rated speed, torque or excessive load on bearings and can maintenance hints that follow are of a pressure. Loading the system beyond be readily identified by the heat general system nature but should the specifications simply increases generated. A warmer than normal provide an intuitive feeling for a specific the possibility of failure. tank return line on a relief valve system. More general information is indicates operation at relief valve covered in the following paragraphs. 2. Know the correct operating pressures. setting. Hydraulic fluids which have a Effect and probable cause charts Always set and check pressures with a low viscosity will increase the internal appear on the following pages. gauge. How else can you know if the leakage of components resulting in a operating pressure is above the heat rise. Cavitation and slippage in a maximum rating of the components? pump will also generate heat. System Design The question may arise as to what the correct operating pressure is. If it isn’t 2. Excessive noise means wear, There is, of course, little point in correctly specified on the hydraulic misalignment, cavitation or air in the discussing the design of a system which schematic, the following rule should be fluid. Contaminated fluid can cause a has been operating satisfactorily for a applied: relief valve to stick and chatter. These period of time. However, a seemingly noises may be the result of dirty filters, uncomplicated procedure such as The correct operating pressure is the or fluid, high fluid viscosity, excessive relocating a system or changing a lowest pressure which will allow drive speed, low reservoir level, loose component part can cause problems. adequate performance of the system intake lines or worn couplings. Because of this, the following points function and still remain below the should be considered: maximum rating of the components and machine. 1. Each component in the system must Maintenance be compatible with and form an Once the correct pressures have been Three simple maintenance procedures integral part of the system. For established, note them on the hydraulic have the greatest effect on hydraulic example, an inadequate size filter on schematic for future reference. system performance, efficiency and life. the inlet of a pump can cause cavitation and subsequent damage to 3. Know the proper signal levels, 1. Maintaining a clean sufficient quantity the pump. feedback levels, and dither and gain of hydraulic fluid of the proper type settings in servo control systems. If and viscosity. 2. All lines must be of proper size and they aren’t specified, check them free of restrictive bends. An when the system is functioning 2. Changing filters and cleaning undersized or restricted line results in correctly and mark them on the strainers. a pressure drop in the line itself. schematic for future reference. 3. Keeping all connections tight, but not 3. Some components must be mounted to the point of distortion, so that air is in a specific position with respect to excluded from the system. other components or the lines. The Developing Systematic housing of an in-line pump, for Procedures example, must remain filled with fluid to provide lubrication. Analyze the system and develop a Guidelines logical sequence for setting valves, The following charts are arranged in five 4. The inclusion of adequate test points mechanical stops, interlocks and main categories. The heading of each for pressure readings, although not electrical controls. Tracing of flow paths one is an effect which indicates a essential for operation, will expedite can often be accomplished by listening malfunction in the system. For example, troubleshooting. for flow in the lines or feeling them for if a pump is exceptionally noisy, refer to warmth. Develop a cause and effect Chart 1 titled Excessive Noise.
Details
-
File Typepdf
-
Upload Time-
-
Content LanguagesEnglish
-
Upload UserAnonymous/Not logged-in
-
File Pages29 Page
-
File Size-