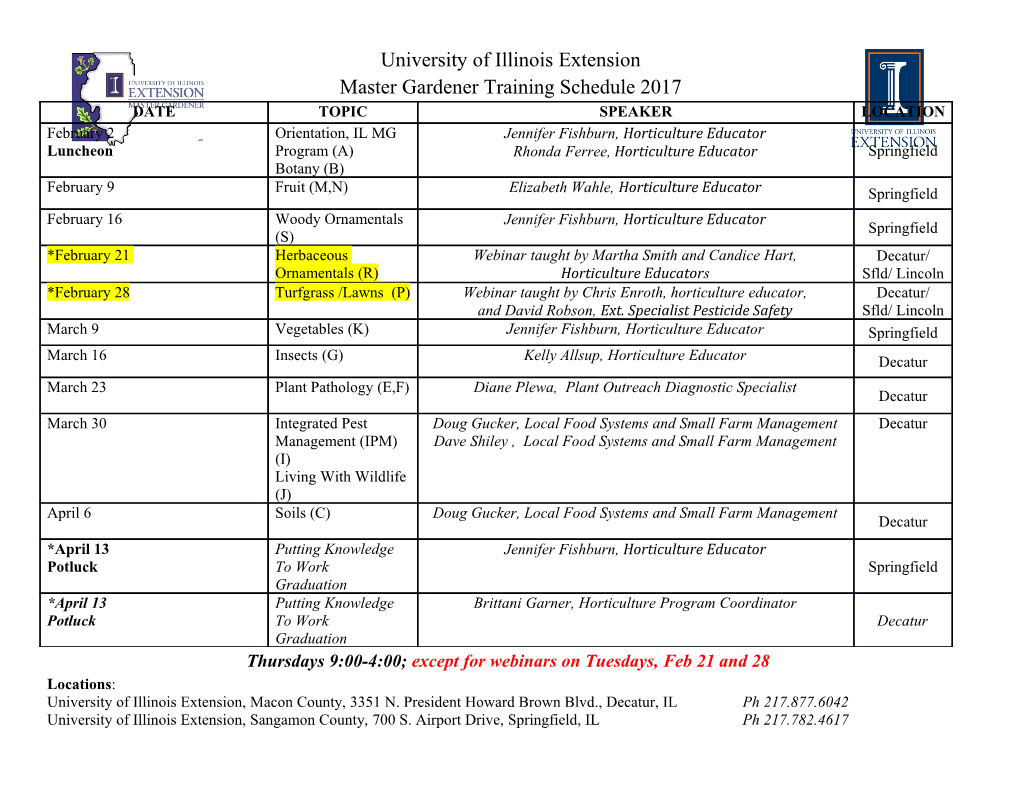
Conference Paper FORMATION OF CORROSION PRODUCTS OF CARBON STEEL UNDER CONDENSER OPERATING CONDITIONS COMPANY WIDE CW-127420-CONF-001 Revision 0 Prepared by Rédigé par Turner Carl - Senior Scientist Reviewed by Vérifié par Burton Gordon R. - Senior Chemist Approved by Approuvé par Angell Peter - Manager - Component Life Technology Branch 2013/01/15 2013/01/15 UNRESTRICTED ILLIMITÉ Atomic Energy of Énergie Atomique du Canada Limited Canada Limitée Chalk River, Ontario Chalk River (Ontario) Canada K0J 1J0 Canada K0J 1J0 UNRESTRICTED CW-127420-CONF-001 - 1 - Rev. 0 FORMATION OF CORROSION PRODUCTS OF CARBON STEEL UNDER CONDENSER OPERATING CONDITIONS Carl W. Turner, Atomic Energy of Canada Ltd., Canada, [email protected] Lisheng Chi, Atomic Energy of Canada Ltd., Canada, [email protected] ABSTRACT Corrosion product transport studies conducted more than a decade ago showed that lepidocrocite, hematite and magnetite are the major components of suspended corrosion products filtered from water collected at the outlet of the Condensate Extraction Pump (CEP), Boiler Feed Pump (BFP), and High-Pressure Heater (HPH) in the steam cycles of pressurized water reactors. The presence of lepidocrocite and hematite in these samples was taken as evidence that the low-pressure section of the feed water system is oxidizing during power operation. It follows that a reduction in the concentration of dissolved oxygen in the condenser and an increase in hydrazine concentration in the feed water would be effective steps to reduce the concentration of fully oxidized corrosion products being transported with the feed water to the steam generators. A review of the literature on the formation of iron oxides under oxidizing conditions, however, has revealed that pH is a more important parameter than dissolved oxygen concentration for determining the phase of iron oxide that forms in the secondary heat-transport system at low temperature, i.e., temperature less than about 100C. Thus, magnetite has been shown to be the dominant phase of iron oxide under oxidizing, alkaline conditions, i.e., pH in the range 9.0 to 11.0, whereas the formation of lepidocrocite and goethite are favoured under mildly acidic to neutral conditions. Goethite also forms under strongly acidic and caustic conditions, but these conditions are not found in the feed water system. Hematite forms under strongly acidic and neutral conditions. It is well known that lepidocrocite and goethite will transform to hematite at elevated temperatures. The only conditions that prevail in the steam cycle during power operation are those that favour the formation of magnetite, yet corrosion product transport studies have consistently shown the presence of hematite and lepidocrocite in samples filtered during power operation. It is proposed that lepidocrocite is formed primarily during maintenance outages when air ingress can lead to the low pH conditions that favour formation of this phase. Once formed, lepidocrocite will transform to hematite at elevated temperatures, thus accounting for the presence of hematite in the corrosion product samples as well. Thus, the evidence from the literature survey of the formation of iron oxides does not support the contention that reducing the concentration of dissolved oxygen in the condenser will reduce the amount of fully oxidized corrosion product that is being transported to the steam generators during power operation. The implications of these findings on outage chemistry control in the secondary system are discussed in this paper. Presented at the Nuclear Plant Chemistry Conference (NPC) 2012 in Paris, France on 2012 September 23 to 27. UNRESTRICTED CW-127420-CONF-001 - 2 - Rev. 0 INTRODUCTION Corrosion product transport studies conducted more than a decade ago showed that lepidocrocite, hematite, magnetite and sometimes goethite are the major constituents of suspended corrosion products filtered from water sampled at the discharge of the Condensate Extraction Pump (CEP), Boiler Feed water Pump (BFP), High-Pressure Feed water Heater (FW) and Boiler Blowdown (BD) in the steam cycles of Pressurized (Heavy) Water Reactors, PWRs and PHWRs [1],[2],[3],[4],[5],[6],7],[8]. The concentration of magnetite in the corrosion product samples varied widely from one plant to another and from one sampling location to another in the steam cycle, as shown by the data listed in Table 1 [6]. Note that the fraction of magnetite in the FW and BD at PWR plants tends to be higher than at PHWR plants. The lower fraction of magnetite at PHWRs compared to PWRs is likely a consequence of two main factors: 1) all PHWRs but one1 have a steam-heated direct-contact deaerator between the low-pressure FW heaters and the boiler feed pump that appears to act as a source of fully oxidized corrosion products to the FW, and 2) high-temperature drains contribute a larger fraction of the total feed water iron, mostly in the form of magnetite, at PWRs than at PHWRs. Table 1: The percentage of magnetite in corrosion product samples collected from various sampling points in the steam cycle of PWR and PHWR plants during power operation Reactor Type CEP FW BD % magnetite % magnetite % magnetite PWRa 25-65 30-84 50-96 PHWRb 37-65 14-59 44-83 a: From a database of over 30 measurements b: From a database of over 90 measurements The presence of fully oxidized iron oxides and oxyhydroxides, such as lepidocrocite, goethite and hematite, in the corrosion product samples has generally been taken as evidence that some regions of the condensate/feed water system are oxidizing during power operation [2],[5],[6]. This hypothesis is challenged in this paper, as discussed below. The evidence from corrosion product transport studies shows that the range of composition of corrosion products and, especially, the fraction of magnetite versus fully oxidized corrosion product is not strongly correlated with the concentrations of either dissolved oxygen or hydrazine in the condensate/feed water system during power operation. For example, a comparison of the results from 8 different PWR plants, all of which had < 2.5 g/kg dissolved oxygen at the CEP and reported FW hydrazine concentrations between 110 and 185 g/kg, shows the percentage of magnetite in the FW corrosion product samples ranging from 18 to 100% [5]. Three other plants with CEP dissolved oxygen ranging between 4 and 10 g/kg reported magnetite fractions in the FW between 35 and 72%, which is within the same range reported for plants that operate with lower concentrations of dissolved oxygen in the condensate. The CANDU plant at Embalse, which operates with < 5 g/kg dissolved oxygen and 2 to 3 g/kg hydrazine at the CEP, has reported 41% magnetite in the FW sample (together with 56% hematite and 3% lepidocrocite) [7], similar to the results from the PWR plants cited above which operate with comparable dissolved oxygen and much higher concentrations of hydrazine in their condensate/feed water systems. In addition, CANDU plants operating in Ontario with > 100 g/kg hydrazine in the FW have reported similar fractions of magnetite in the CEP to the Gentilly-2 nuclear power plant [6] that operated from 1984 to 1998 with no hydrazine addition to the steam cycle during operation at power. It is proposed in this paper that the composition of iron-based corrosion products in the secondary system of a nuclear power plant is determined primarily by the pH, and not by the concentration of dissolved oxygen. Furthermore, it is proposed that the fully oxidized phases of iron corrosion products, such as lepidocrocite and goethite, are formed not during power operation but, instead, when the plant is shut down for a maintenance outage, during which time air ingress introduces carbon dioxide to the water that produces the low-pH conditions (i.e., pH 6 to 7) that are conducive to the formation of these phases. Upon return to full power operation, both lepidocrocite and goethite will transform to hematite in the higher-temperature regions of the system, thus introducing hematite to the system. In this paper, we first review the literature on the preparation of iron oxides as a function of pH and dissolved oxygen concentration to determine the chemistry conditions that favour formation of the various phases of iron oxide that have been observed from the corrosion product transport measurements for the secondary side of nuclear power plants. This review will clearly demonstrate that pH is the most important that determines the major phase of iron oxide that precipitates under a given set of conditions, and not the concentration of dissolved oxygen. 1 Nucleoelectrica Argentina Sociedad Anonima (NASA) operates a CANDU PHWR plant at Embalse that does not have a deaerator in the condensate/feed water system. Presented at the Nuclear Plant Chemistry Conference (NPC) 2012 in Paris, France on 2012 September 23 to 27. UNRESTRICTED CW-127420-CONF-001 - 3 - Rev. 0 The results of past corrosion product transport investigations will be discussed in light of this result, and an argument will be proposed to support the hypothesis that the fully oxidized forms of the iron-based corrosion products are formed only during maintenance outages as the result of air ingress causing pH depression, and therefore their presence on corrosion product filters is not a measure of oxidizing conditions in the condensate/feed water system during power operation. FORMATION OF IRON OXIDES AND OXYHYDROXIDES FROM SOLUTIONS OF IRON(II) AND IRON(III) Formation of Magnetite Magnetite is commonly prepared at low temperature (< 100ºC) by oxidizing an Fe(II) solution under alkaline conditions using, for example, air, pure oxygen or KNO3 for the oxidant. If the oxidant is left out of this preparation, the product will be a white suspension of Fe(OH)2. For example, magnetite has been prepared by the drop-wise addition of a solution of KNO3 and KOH to a solution of FeSO4 at room temperature, followed by aging for 2 hours - - - at temperature of 90ºC [9],[10],[11].
Details
-
File Typepdf
-
Upload Time-
-
Content LanguagesEnglish
-
Upload UserAnonymous/Not logged-in
-
File Pages10 Page
-
File Size-