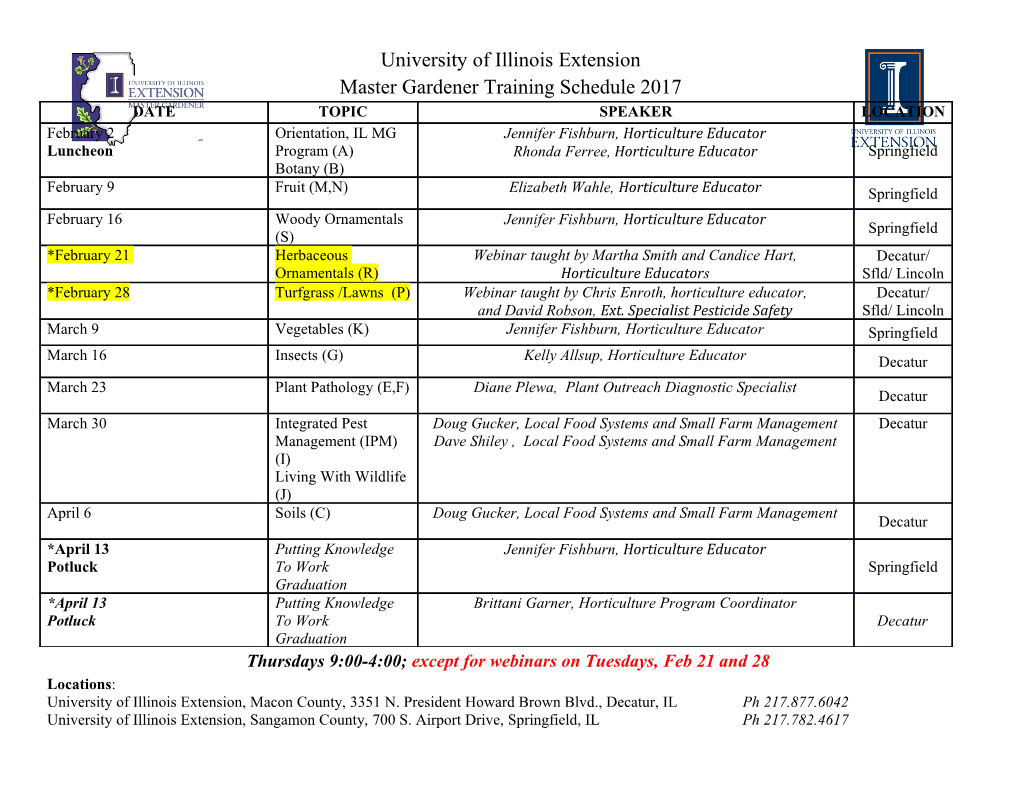
The Five Minute Guide to the Modern Power MOSFET Whitepaper The Five Minute Guide to the Modern Power MOSFET Introduction For most engineers the metal oxide semiconductor field effect transistor (MOSFET) is the foundation on which power system designs are built. This stalwart component proves invaluable in providing the necessary switching functionality to all manner of electronics hardware, and seems certain to stay that way - especially given that power densities continue to increase at pace and switching speeds are still accelerating. With so many different models now on the market, ensuring that the right one is specified can often be challenging. As a result, when implementing MOSFETs into any particular application there are a multitude of factors that should be carefully assessed. This brief but informative document is intended to help, by describing the various factors that should be considered when specifying a power MOSFET. It will show how to correctly consult product datasheets in order to derive the necessary information for judging a particular power MOSFET’s suitability and give engineers the information they need to make well-reasoned purchasing decisions. MOSFET Basics MOSFETs have a number of advantages over other transistors used to provide switching functionality to power circuits. They operate as majority carrier devices (i.e. using electrons to carry current in the case of N- channel devices and holes to carry current in the case of P-channel devices), whereas bipolar junction transistors (BJTs) are minority carrier devices. MOSFETs possess some substantial advantages over BJTs - importantly, BJTs are current controlled, while MOSFETs are voltage controlled. This means that the drive circuitry needed for a MOSFET is much simpler to implement, as well as enabling faster switching speeds and better frequency response. In addition, MOSFETs offer higher input impedance, greater current gain and lower susceptibility to external influences such as temperature variation. Modern power MOSFETs feature an integrated body diode. To minimise switching losses and increase system efficiency, this integrated diode can be optimized as a fast recovery body-diode (FRD). Such FRDs are usually characterised by reverse recovery times (trr). In addition, choosing devices with integrated FRD into the body of the MOSFET can help to reduce component count, save space, simplify design and streamline inventory. Copyright 2019 © TOSHIBA ELECTRONICS EUROPE GMBH, All Rights Reserved. Whitepaper Figure 1 – Circuit diagram of a MOSFET with integrated FRD On State Resistance When choosing a MOSFET, engineers must have a firm idea about the maximum on state resistance (RDS(ON)) that will be the acceptable. The power losses within a MOSFET can be either dynamic or static in nature. RDS(ON) is the principal static loss. It is intrinsic to the device and cannot under any circumstances be eliminated. When comparing RDS(ON) values for different MOSFET devices, it is vital that mistakes are not made because datasheets may quote the RDS(ON) at different VGS levels. The impact of RDS(ON) is fairly small when a MOSFET is incorporated into a high or medium voltage, low current application, but it can be more acute in low voltage applications where drain currents are higher and power consumption needs to be reined in. A MOSFET datasheet will normally quote the RDS(ON) value at a junction temperature (TJ) of 25°C and also at the device’s maximum TJ too. Current Rating For power MOSFETs the DC current that flows in the forward direction is denoted by ID and the pulse current by IDP (where relevant). Such currents are heavily influenced by the power losses caused by the RDS(on) and the relationship this has with the operating temperature. The maximum temperature that the device will support will therefore be instrumental in determining its ID and IDP figures. Threshold Voltage The threshold voltage (VTH) is another important parameter. This gives the minimum gate bias that can be utilised to create a conduction channel between the MOSFET’s source and drain. Once the gate-source voltage (VGS) exceeds this value, then the MOSFET channel will start to conduct an electrical current. The thickness of oxide layer on the gate and level of doping within the channel both affect the value of VTH. Copyright 2019 © TOSHIBA ELECTRONICS EUROPE GMBH, All Rights Reserved. Whitepaper Breakdown Voltage Capacity The maximum drain source-voltage (VDSmax) is otherwise referred to as the breakdown voltage. There is a difficult situation that engineers face when it comes to the VDSmax of the specified MOSFET, which is dictated by how the device has been fabricated. The thickness of the MOSFET’s N− epitaxial layer and its doping level have a direct influence of the VDSmax that can be supported. The thinner this layer is and the heavier its doping concentration, the lower the resultant RDS(ON) will be, but the MOSFET is thus potentially left more vulnerable. Conversely by having a thicker layer and lighter doping, the VDSmax that can be supported is raised, but this comes with the drawback of worse power losses - which may be unacceptable for application where the power budget is restricted. Engineers have to compromise on one of these factors in order to satisfy the other. It should also be noted that VDSmax is influenced by temperature. Gate Charge Capacity The gate charge (QG) determines the charge energy that must be supplied so as to switch the MOSFET device. It is through the MOSFET’s QG that its switching performance will effectively be defined. The lower the QG is, then the higher the switching frequency that can be utilised. In turn the higher the switching frequency, the smaller the board space that needs to be allocated and the lower the overall system cost will be. The total value of QG is made up of a number of distinct parts, including: • QGD (gate-drain charge) • Qgs (gate-source charge) As QGD is inversely proportional to RDS(on), choosing an appropriate balance between RDS(on) and QGD is crucial for optimal circuit performance and the speeds that can be supported. The compounding together of a MOSFET’s RDS(on) and its QG value (RDS(on) x QG) gives the figure of merit (FoM), which is a key performance indicator for specifying these devices. Copyright 2019 © TOSHIBA ELECTRONICS EUROPE GMBH, All Rights Reserved. Whitepaper Component Packaging The MOSFET package size that can be accommodated by the system is another critical factor. If the board space pressures are not too great then a MOSFET can be sourced that is housed in a relatively large package format. This means that key characteristics such as RDS(on) (by tolerable maximum chipsize) and power dissipation will be better. System performance will thus be improved and power consumption lowered. However, in space-constrained designs it may not be possible to have this luxury. As a result taking time to find a MOSFET device that can deliver strong figures for certain key parameters while still being enclosed within a compact package type is advised. Key trend in power electronics leads to higher power density at less PCB space, as well as lowest possible connection resistance. Figure 2 – SOP-Advance (5x6mm), TSON-Advance (3.3x3.3mm) and PS-8 (2.8x2.9mm) packages Supported Temperature Range The TJ that the application is likely to subject the device to will have impact upon not only the performance of the system, but also its operational longevity. The degradation of a power MOSFET will normally be accelerated by a heightening of the working temperature it has to deal with. The mean service life (LM) of a MOSFET can be calculated using the following simple equation: Log LM = X + Y/TJ Where both X and Y are constants, inherent to power MOSFETs. For any parameter on a MOSFET datasheet it important to ascertain at what temperature the stated figure applies and ensure that any calculations made that are based on such figures relate to the operating temperature you plan to run your device at - otherwise these calculations will be incorrect and judgements made using them will be misguided. Copyright 2019 © TOSHIBA ELECTRONICS EUROPE GMBH, All Rights Reserved. Whitepaper Thermal Management Range The power losses that stem from the semiconductor material and the topology employed, combined with the MOSFET package size, package type and its contact area with the PCB, all impact upon the heat generated by the MOSFET. Heat sinks are typically employed to dissipate thermal energy and help ensure system reliability. As ever, a balance must be struck between ensuring sufficient heat dissipation and the space and cost of installing thermal management systems. Certain package types, such as the DSOP Advance, provide enhanced thermal dissipation by providing surfaces on both sides of the MOSFET. Beside cooling to the bottom by PCB also top side can be fitted with heat sinks. Figure 3 – DSOP-Advance package (5x6mm) MOSFET Topology MOSFET devices will either have a planar or some sort of trench-based construction. Trench MOSFETs constitute an ever increasing percentage of the power market, as engineers strive to lower the power consumption of modern systems designs. The industry is increasingly being defined by two major drivers - the need to curb power consumption and the need to enable further miniaturization. In portable consumer electronic devices (such as smartphones and tablet computers), OEMs are looking to introduce sleeker more compact designs that will give them a competitive edge. They also need to be able to offer customers longer battery lives. Among the topologies now representing a large proportion of power MOSFET unit sales are: • UMOS : Vds 20- 250V (which is generally suited to low voltage deployment) • DTMOS: Vds 500-800V (which is better suited to high voltage deployment) UMOS - The U-shaped MOS (UMOS) MOSFET structure is becoming one of the most commonly used in the power electronics sphere.
Details
-
File Typepdf
-
Upload Time-
-
Content LanguagesEnglish
-
Upload UserAnonymous/Not logged-in
-
File Pages10 Page
-
File Size-