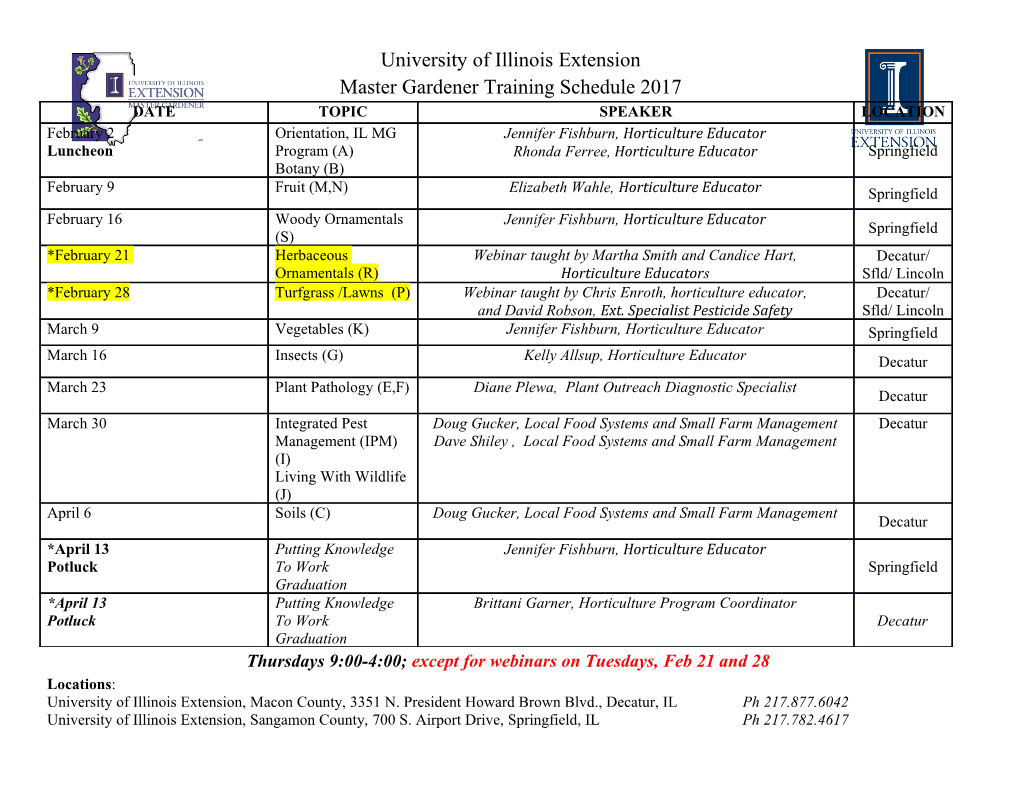
e-Polymers 2021; 21: 108–130 Review Article Debaditya Bera#, Rimpa Chatterjee#, and Susanta Banerjee* Aromatic polyamide nonporous membranes for gas separation application https://doi.org/10.1515/epoly-2021-0016 received November 12, 2020; accepted January 10, 2021 1 Introduction Abstract: Polymer membrane-based gas separation is a High-performance polymeric materials exhibit several superior economical and energy-efficient separation tech- exciting properties, such as high thermal stability, che- nique over other conventional separation methods. Over mical resistance, low flammability, and excellent mechani- the years, different classes of polymers are investigated for cal properties, that make them useful for advanced tech- their membrane-basedapplications.Theneedtosearchfor nologies. Wholly aromatic polyamides (PAs) are a class of - new polymers for membrane based applications has been high-performance polymers that find applications in dif- a continuous research challenge. Aromatic polyamides ferent cutting-edge technologies, particularly in aerospace ( ) - PAs , a type of high performance materials, are known and military applications. Nevertheless, very high glass - for their high thermal and mechanical stability and excel transition temperatures of PAs, mostly above their thermal fi - lent lm forming ability. However, their insolubility and decomposition temperatures, and their low solubility in ffi - processing di culty impede their growth in membrane organic solvents resulted in processing difficulties and based applications. In this review, we will focus on the restricted many of their applications. Consequently, basic - - PAs that are investigated for membrane based gas separa and applied research is directed to enhance their proces- tions applications. We will also address the polymer sability and solubility and widen the possibility of their design principal and its effects on the polymer solubility industrial applications (1–5). and its gas separation properties. Accordingly, some of Separation and purification of gas mixtures are neces- the aromatic PAs developed in the authors’ laboratory sary industrial processes in different demanding applica- that showed significant improvement in the gas separa- tions, such as removing carbon dioxide for natural gas tion efficiency and placed them in the 2008 Robeson “sweetening,” carbon dioxide from greenhouse gas-pro- upper bound are also included in this review. This review ducing sources, oxygen enrichment from air, (6) etc. Com- will serve as a guide to the future design of PA mem- pared to the different traditional separation processes like branes for gas separations. pressure swing adsorption, cryogenic distillation, etc., gas Keywords: aromatic polyamide, synthesis, solubility, gas separation using polymer membranes offers many advan- permeability, gas selectivity tages. The ease of fabrication of polymer membranes, mechanical simplicity, energy efficiency, relatively low cost for small-scale operation, and the overall environ- ment-friendly techniques made them a better choice (6–8). The limited thermal and chemical stability, consid- erable material cost for high output applications, and the inherent trade-off between gas permeability and selectivity of these polymer membranes are the significant issues that ( – ) - need attention 7 9 . The critical paradigm for the suc # These authors contributed equally. cessful application of polymer membrane for cost-effective large-scale industrial applications is to develop polymers with high permeability and good selectivity (6,7).Gas * Corresponding author: Susanta Banerjee, Materials Science molecules permeate through the dense polymer mem- Centre, Indian Institute of Technology Kharagpur, Kharagpur brane according to the solution diffusion mechanism. 721302, India, e-mail: [email protected] Debaditya Bera, Rimpa Chatterjee: Materials Science Centre, Indian According to the model, the permeation of the gas mole- Institute of Technology Kharagpur, Kharagpur 721302, India cules depends on the interaction (solubility) between the Open Access. © 2021 Debaditya Bera et al., published by De Gruyter. This work is licensed under the Creative Commons Attribution 4.0 International License. Aromatic polyamide nonporous membranes for gas separation application 109 polymer and the individual gas molecules and on the movement (diffusion) of the gas molecule through the transient opening of the leap channels (linking between the free volume elements in the membranes) of adequate size caused by the segmental mobility of the polymer Figure 1: Structures of the aromatic PAs, Nomex, and Kevlar. chains (10). In short, the permeability and selectivity of the gas This review is intended to address in detail the PA molecules through the polymer membrane depends on membranes used for gas separation applications. We will the interaction between gas molecules and the functional focus on their structural modifications, i.e., strategies groups (polar groups) present in the polymer chain and employed to overcome their processability issue and also on the polymer chain packing density, which con- improve their gas separation properties. trols the fractional-free volume (FFV) in the dense polymer membrane. However, there is no strict design rule to con- trol these parameters for obtaining an optimal gas separa- tion (11). But, generally, it has been observed that poly- mers with rigid backbone induce size-based selectivity for 2 PA synthesis small molecules like CO2 and O2 (kinetic diameter of the gas molecules, CO2 (3.3 Å),O2 (3.46 Å),N2 (3.64 Å),CH4 PAs are generally synthesized by condensation polymeri- (3.8 Å)), and the incorporation of the bulky groups in the zation of an aromatic diamine and an aromatic dicar- polymer chain, which improve the FFV by limiting the boxylic acid/acid chloride. The synthesis of PAs by dif- polymer chain packing, helps to enhanced superior per- ferent pathways is discussed below. meability and selectivity (12).Different classes of polymers, such as poly(arylene ether)s (13–16), modified cellulose (17),andpolyimides(PIs)(18–21), have been investigated for membrane-based gas separation applications. Because 2.1 Low-temperature polymerization of their certain outstanding qualities like excellent thermal, mechanical and dimensional stabilities, and low dielectric It is the most common method of preparation of PAs. In constant values, aromatic PIs are known as promising can- this method, diacid chlorides react with diamines at low didate for membrane-based gas separation applications temperatures (from −10°C to 0°C). This method is gener- (22). However, the gas separation based on PA membranes ally preferred when acid chloride of the corresponding has not gotten proper attention. aromatic diacid monomer is easily obtained (Scheme 1). Aromatic PAs are considered high-performance mate- The solvents used are polar aprotic solvents like N,N- rials because of their versatile chemistry, superior thermal dimethylacetamide (DMAc), N,N-dimethylformamide (DMF), and mechanical properties, solvent and chemical resis- and N-methyl-2-pyrrolidone (NMP). Salts, such as CaCl2 tance, high friction resistance, and good film-forming and LiCl, are often used as solubility promoters because ability, leading to increased importance in advanced tech- the cations interact with the amide groups, diminishing nologies (1,21,23).AromaticPAswerefirst introduced com- the interchain hydrogen bonding. During this process, mercially in the early 1960s, in the form of meta-aramid the main difficulty faces the moisture sensitivity of the (Nomex®) produced by DuPont and later para-aramid with diacidchlorides,whichisrequiredinhighpurityto much higher elastic modulus called Kevlar® (Figure 1). obtain the high-molecular-weight polymers (25,26). Both the polymers are commercial aromatic PAs of great economic relevance. PAs draw attention due to their superior thermal and mechanical properties. PAs are used for several applications, like protective apparel, air filtration, thermal and electrical insulation, as advanced composites in the aerospace and armament industry. However, difficulties in their processability and solubility due to strong interchain hydrogen bonding that result in dense polymer chain packing restricted their use for the Scheme 1: Low-temperature solution polycondensation of diamine industrial membrane-based gas separations (24). and diacid chloride. 110 Debaditya Bera et al. 2.2 High-temperature polymerization nH2NR1 NH2 + nClOCR2 COCl Yamazaki and Higashi developed this high-temperature polymerization method (27). The condensation reaction H2O+Base Organic solvent occurs directly between diacids and diamines at higher temperatures (from 80°C to 100°C) in the presence of O O polar aprotic solvents like DMAc, DMF, and NMP. Pyri- H H N R N C R C dine and triphenyl phosphite were used as a condensing 1 2 agent. Also, salts such as CaCl2 and LiCl are used as solu- n bility promoters. Yamazaki and Higashi proposed that the Scheme 3: Interfacial polycondensation of diamine and diacid polymerization proceeds via the formation of an inter- chloride. mediate acyloxy N-phosphonium salt of pyridine, as shown in Scheme 2 (27). Recent efforts have been directed to reduce the poly- vigorously to obtain a high-molecular-weight product. Low merization time by applying microwave heating (2 min) temperature is required to control the side reactions, and instead of the conventional one (4h)(28). Also, investi- the polymers that are unstable at a high temperature can be gations
Details
-
File Typepdf
-
Upload Time-
-
Content LanguagesEnglish
-
Upload UserAnonymous/Not logged-in
-
File Pages23 Page
-
File Size-