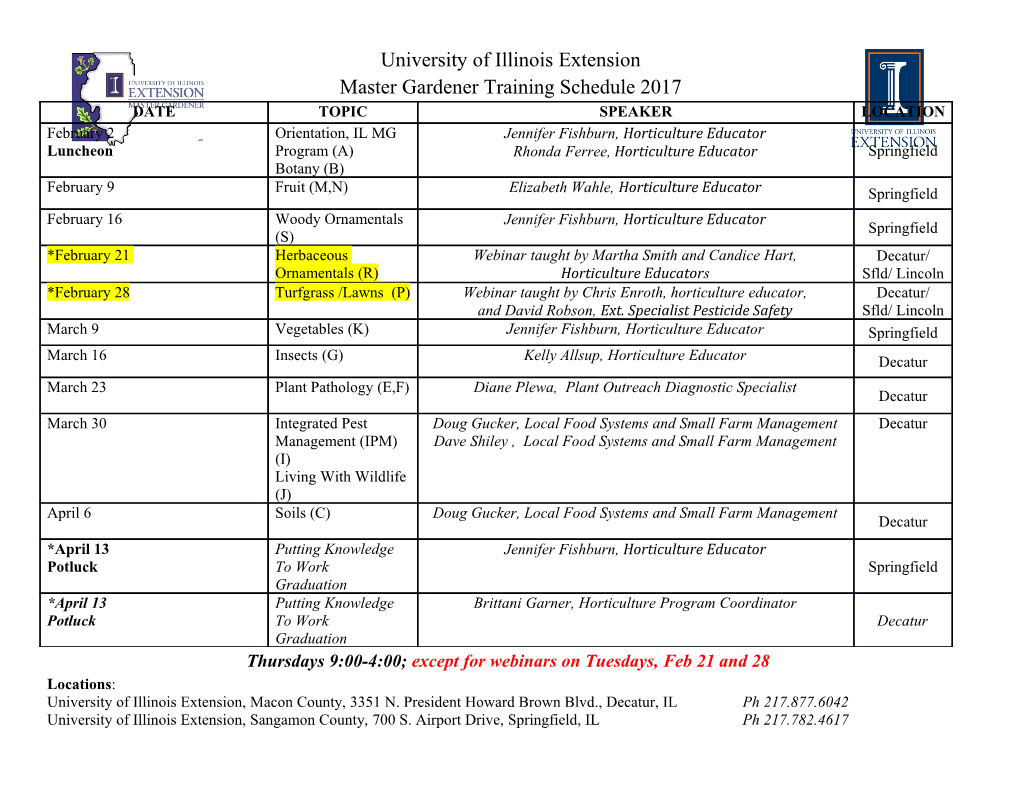
Paper accepted for 2015 6th International Conference on Automation, Robotics and Applications (ICARA) © 2015 IEEE. Personal use of this material is permitted. Permission from IEEE must be obtained for all other uses, in any current or future media, including reprinting/republishing this material for advertising or promotional purposes, creating new collective works, for resale or redistribution to servers or lists, or reuse of any copyrighted component of this work in other works. DOI: 10.1109/ICARA.2015.7081135 A backward-oriented approach for offline programming of complex manufacturing tasks Ludwig Nagele¨ ∗, Miroslav Macho∗, Dr. Andreas Angerer∗,AlwinHoffmann∗, Michael Vistein∗, Manfred Schonheits¨ † and Prof. Dr. Wolfgang Reif∗ ∗Institute for Software & Systems Engineering, University of Augsburg, Universitatsstrae¨ 6a, 86159 Augsburg, Germany Email: [email protected], [email protected], [email protected], [email protected], [email protected], [email protected] †German Aerospace Center, Institute of Structures and Design, Center for Lightweight Production Technology (ZLP), Am Technologiezentrum 4, 86159 Augsburg, Germany, Email: [email protected] Abstract—The automation of production processes with large cesses this can be very time consuming. This required time in process variability and a low batch size can be very difficult particular is another major drawback of online programming. and non-economic. Using the example of manufacturing carbon- While the programming is in process, the robot (and possibly fibre-reinforced polymers (CFRP) which represents a complex, the whole production line where the robot is stationed) cannot currently hardly automated process, we present a backward- be used for production and thus no revenue is generated. oriented approach for offline programming of complex manufac- turing tasks. We focus on an automatic process definition which A possible solution to these problems is the use of offline is supported by expert knowledge where required. Due to domain programming, where all major development steps take place specific software modules, user interaction is intuitive and tailored using a simulated environment which resembles the real fact- to CFRP experts. This leads to significant time-savings compared ory floor as close as possible. The simulation environment is to currently used teach-in approaches. Moreover, we introduce usually based on CAD data of the robot cell. Offline program- an extensible offline programming platform which is able to meet ming allows the developer to test all programs without the the high requirements of CFRP manufacturing. dangers of collisions and without blocking the real hardware for an extended period of time. Testing on the real hardware I. INTRODUCTION is necessary nevertheless, because the simulated environment Automating production processes has become a major trend almost always differs slightly from the real-world e.g. due in many industries. Key benefits of automated processes are to production tolerances. In contrast to online programming, highly precise and repeatable results as well as a high through- this step takes considerably less time as only small positional put. Because industrial robot arms can be flexibly adjusted to a modifications should be required. broad variety of tasks by simply using different programs, they This work is focused on an approach for offline pro- are a common sight in an automated production line. Creating gramming of industrial robot systems for the production of robot programs for complex manufacturing tasks however is carbon-fibre-reinforced polymers (CFRP). Amongst the differ- not always that easy, sometimes requiring several months of ent methods for the manufacturing of CFRP components [1]– development time. Even before the programming of robots [3], the investigated process uses dry textile preforms and VAP can be started, it is necessary to design a production process resin infusion [4]. This means that a CFRP part consists of that can be employed for creating the desired work-pieces many planar cut-pieces from dry textile weave or non-crimp with the available hardware. Due to different capabilities, but fabric. A CFRP part is designed using a CAD tool and its cut- also to different limitations, processes previously performed pieces are stored in a plybook. Moreover, the cut-pieces are by human workers cannot necessarily be directly transformed usually of different shapes and dimensions: in our example into automated processes. This paper introduces an approach of CFRP, the size ranged between 0.3m × 0.2m up to which concentrates on the results of a production process to 2.0m× 2.0m. For the preforming process, each planar cut- deduct the steps necessary to reach this result, instead of trying piece has to be laid onto a 3D tooling surface. This draping to find the steps beginning from the raw materials. process is challenging because it has to precisely transform a planar textile into a 3D form with double curvature in order Once the production process has been designed, programs to guarantee the overall material properties. In particular the controlling all automation hardware including robots and tools requirements to the position of the resulting contour and the must be created. Traditionally, industrial robots are equipped local fibre angle must be met according to the plybook [4]. with a programming environment which allows writing and Although the offline programming platform has been evaluated testing programs directly on the robot hardware (so-called using the preform process, it is – due to its extensibility – also online programming). Although this programming method has applicable to other methods. the advantage of immediate feedback of whether the program is working properly, it also has several drawbacks. Testing new CFRP parts are currently manufactured with a low automa- robot programs always comes with the risk of collisions due to tion level and many manual steps [4]. However, many different programming errors. Depending on the mounted tools and the shapes and delicate handling of the cut-pieces pose challenges selected robot systems, such collisions can be extremely costly. to human workers. The automation of such a process is difficult This risk can be reduced by testing programs carefully and as well and often non-economic with traditional approaches slowly after each change, however for large production pro- due to small batch sizes. Current research projects for automat- Figure 1. Supported research end-effectors: Foam Gripper, Grid Gripper and Modular Surface Gripper ing CFPR production often concentrate on developing novel The remainder of this paper is organized as follows. The gripping end-effectors (c. f. Fig. 1). To put these end-effectors requirements for both the production process as well as the into operation, usually a teach-in process as illustrated in Fig. 2 offline programming platform are identified in Sect. II. The is utilised. Each cut-piece defined in the plybook is picked backward-oriented approach for interactive programming is ex- up with the gripper which is attached to a robot’s flange plained in Sect. III, its integration into an offline programming and is positioned within the moulding form. A laser projector platform in Sect. IV. The approach has been evaluated in real- programmed with the dimensions and position of the cut-piece world scenarios, the results can be found in Sect. V. Sect. VI is used to draw the boundaries onto the form. After the cut- gives a short overview of related work for both process design piece has been placed by the robot, a teaching-expert compares and offline programming environments. This paper is finally the real position to the laser projection and, if necessary, the concluded with Sect. VII. positioning process is repeated until the cut-piece perfectly fits the projected position. For large CFRP parts consisting of many layers, this process is very time-consuming. II. REQUIREMENTS ANALYSIS To facilitate the automation of CFRP manufacturing, we For the development of the offline programming environ- developed a novel backward-oriented approach for interact- ment, several general requirements in the domain of CFRP ively programming tasks for complex gripping end-effectors. manufacturing have been identified. Those requirements cover In this paper, we show that offline programming combined both the general design of an offline programming environment with a (partially) automated generation of preforming tasks as well as an expert-driven process definition required in this significantly reduces the time required for automation with res- specific domain. The identified general requirements are as ults comparable to manual teach-in. The proposed backward- follows: oriented approach has been developed as part of the AZI- ∙ automatic process definition: The production process MUT project [5] and was integrated into an extensible offline should be generated automatically as far as possible, and programming research environment which was particularly user input should only be requested if domain-expert designed for CFRP manufacturing. It currently supports three knowledge is required. In particular, the user should different end-effectors which are mounted on different KUKA not need to have in-deep knowledge about automation industrial robots (KR-210 and KR-270). The end-effector technology or software development. Available data such systems – Foam Gripper, Grid Gripper and Modular Surface as CAD models or the plybook should be used. Gripper (c. f. Fig. 1) – have different gripping
Details
-
File Typepdf
-
Upload Time-
-
Content LanguagesEnglish
-
Upload UserAnonymous/Not logged-in
-
File Pages7 Page
-
File Size-