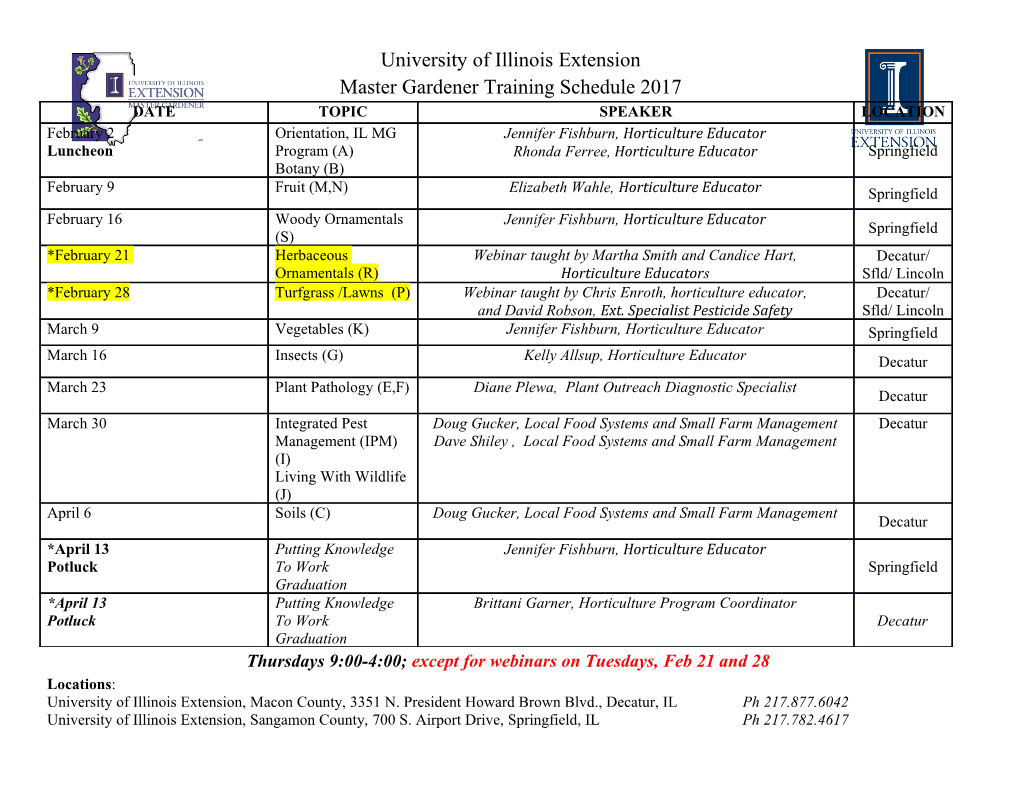
CHANGES TO PCC STRUCTURE IN PAPERMAKING Thad C. Maloney*, José Ataide, Juha Kekkonen, Henrik Fordsmand, Henrik Hoeg-Petersen *JM Huber, Telakkatie 5A, 49460 Hamina, Finland; [email protected] Abstract For precipitated calcium carbonate (PCC), it is well known that the degree of structuring has a strong influence on the performance of the pigment as a paper filler. “Structuring” refers to the aggregation of small primary particles into a larger secondary structure. A high degree of pigment structure results in high bulk and good optical performance. A long-standing question of papermakers concerns the possible break-down of PCC from an aggregated structure into primary particles. This could conceivably arise either from high shear forces in the wet end or from high structural pressure during web consolidation. This study attempts to determine if such a break-down occurs for S-PCC in fine paper production and to find out the implications for paper quality. In the study, we demonstrate with lab sheets that when PCC structure breaks down there is a high negative impact on paper properties. For example, two-sidedness increases and bulk decreases. In order to examine the PCC particle properties on a paper machine, a new analytical technique was developed. The technique is based on the oxidation of chemical pulp fibers under controlled conditions and the subsequent analysis of the ash residues with particle size techniques. Our studies indicate that this is an acceptable method to characterize fillers in pulp suspensions and paper handsheets. We go on to study the filler properties from the PCC plant, through the approach flow system, to the couch of a modern fine paper machine. Our analysis indicates that the S-PCC studied here did not break down to a significant extent on full scale paper machines, though we did find evidence of breakdown on a pilot machine. It was also found that the new test can give an indication of the amount of PCC flocs formed in the wet end and in web consolidation. Introduction For uncoated woodfree copy paper, bulk is one of the most important quality parameters. Generally speaking, the optical properties that can be reached with today’s pulp bleaching methods, optical brighteners and fillers are adequate. Likewise, strength of fine paper is less of an issue than in the 1980’s and 1990’s. There are several reasons why bulk (at a specified smoothness) is so important to fine paper manufacturers. One reason is related to the manufacturing economies because high bulk allows one to decrease grammages or to increase filler contents while maintaining adequate stiffness. Precipitated calcium carbonate (PCC) has emerged as the filler of choice for today’s fine paper. This is because PCC gives excellent optics and bulk compared to its leading competing filler, ground calcium carbonate (GCC). Also, the on-site solution allows one to synthesize several different morphologies with different characteristics that can be used to help optimize a mill’s grade mix. Two of the important morphologies for uncoated copy paper are rhombohedral PCC (R-PCC) and scalenohedral PCC (S- PCC). R-PCC is not highly aggregated and has a low surface area-to-particle size ratio and thus gives excellent drainage and high paper machine speed. However, even more important in fine paper manufacture is S-PCC which is useful for manufacturing paper with high bulk. Paper bulk at a given smoothness depends on several factors including the paper machine design and pulp quality variables. The filler type and amount also has an important role. A large particle size and narrow particle size distribution (PSD) increases paper bulk by decreasing the particle packing. Today, both these variables have been optimized with PCC and there is very little room left for further improvement by either of these appraoches. Another important variable for bulk is the amount of structure or aggregation. The success that S-PCC enjoys is largely due to its high amount of structure. The structure of S-PCC is shown in Figure 1. It it’s a useful view to consider the arrangement of PCC in paper in terms of structural hierarchy. The arrangement of the crystal lattice in the primary level of structural hierarchy determines certain material properties such as index or refraction and melting point. For PCC used in paper manufacture the important crystalline types are aragonite and calcite. S- PCC is the latter. The shape and size of the individual crystals influences the specific surface area, which has a direct consequence on the consumption of wet end additives in papermaking. However, it is the higher levels of structural hierarchy which are most important for paper bulk. 1 2 3 4 Crystal Structure Crystal Morphology Primary aggregation Secondary aggregation Figure 1. The levels of structural hierarchy in S-PCC: 1) molecular organization, 2) crystal morphology, 3) primary aggregation and 4) secondary aggregation (PCC flocs). In the synthesis of S-PCC, the cigar shaped crystals grow out of a calcium hydroxide core during the carbonization reaction. After carbonization is complete, the single crystals are arranged in a 3- dimensional star-shaped pattern attached at the original core through ionic bonding forces. In some places on the S-PCC aggregate secondary nucleation may lead to further growth of cigar shaped crystals. This third level of structural hierarchy is what is normally associate with the PCC particle size. The size and structure of this aggregate has an important consequence for paper bulk. We can also consider a fourth level of structure. In the paper machine wet end, colloidal and hydrodynamic forces may cause the PCC aggregates to flocculate together. Thus, in paper, there is a certain distribution of filler in the x, y an z directions that may be more or less homogenous (Karrila, S. et al. 2002). The bonding of these larger filler aggregates is much weaker than the primary aggregates, consisting mostly of electrostatic forces. It has been established through filler flocculation experiments (Holm M. and Manner, H. 2003) that this highest level of filler structure can influence paper properties e.g. optics, strength and bulk. From the point that it is manufactured in the on-site plant to the finished paper PCC experience some rather severe forces (Pelton, R. H. 1984) that may break down the aggregates into individual crystals. In the wet end, the high shear in the pumps, cleaning units and in the formation zone (the highest shear is normal at the fan pump and headbox screen) may be adequate to break apart the primary aggregates. In press dewatering, the paper is subjected to high pressure, in the range of 10 MPa for a roll press, which could “crush” the aggregated PCC structure causing a loss of bulk. Severe pressures in the calender stack could also break apart the PCC structure causing a loss of bulk. The objective of this study was to determine how deaggregation of S-PCC affects paper properties and to determine if, in fact, S-PCC breaks down during fine paper manufacture. Materials and Methods In the first part of this study, S-PCC with a deliberately broken down structure was compared to conventional in-tact S-PCC. The S-PCC used in the study is FS-240 and also a similar grade FS-270. These are commercial grades of S-PCC produced by JM Huber with an average particle size of 2.4 µm and 2.7 µm, respectively, as measured with a Sedigraph. A 70/30 hardwood/softwood mixture of industrially prepared refined kraft pulp was used in handsheet making. A sample of the FS-240 was broken down by exposing a 20% slurry to 12 hours in an Ultra-Turrax T50 mixer exposed to a shear of 1.83x10 4 s -1. Our experiments showed that this was adequate conditions to detach a significant fraction of primary crystals from the aggregates. 80 g/m 2 handsheets were prepared at different filler content in the range of 22-28% filler content on a Fibertech dynamic sheet former. A cationic polymer – micro particle retention system was used: 200 g/ton Kemira Fennopol K3400 R + 2500 g/ton bentonite. The pH was not adjusted and no other additives were used. Sheets were calendered in a Gradek calender with 2+2 nips at 11 kN/m pressure at room temperature. Sheets were tested with standard ISO methods. Two different methods for particle size analysis were used. A Sedigraph 5100 measures particle size distributions by sedimentation rate. The particle size by this method is especially effected by the particle specific volume. Some measurements were also performed with a Horiba LA-920. This method is also adequate to quantify PCC particle size distributions. However, because it is based on laser diffraction the resulting PSD does not necessarily equal that from Sedigraph. The PCC or the ash residues was first treated in a sonic bath for 30 minutes, followed by addition of a cationic dispersant, Fennofix 40, before particle size measurements. We have found that for a conventional PCC particle size distribution these are adequate dispersion conditions to break up flocs, but not to break down the primary aggregates to individual PCC crystals. The PSD of the PCC in either the pulp furnish or paper was determined as follows: A sample of the dried furnish or paper was treated in a Leco TGA-601 thermo gravimetric analyzer under conditions sufficient to oxidize the cellulosic fibers. An 8 gram sample of the dried furnish or paper was heated first to 300 oC and then held constant for 2 hours. The oven gas was air. These are sufficient conditions to oxidize most of the organic material but not to cause the pulp to burst into flames.
Details
-
File Typepdf
-
Upload Time-
-
Content LanguagesEnglish
-
Upload UserAnonymous/Not logged-in
-
File Pages7 Page
-
File Size-