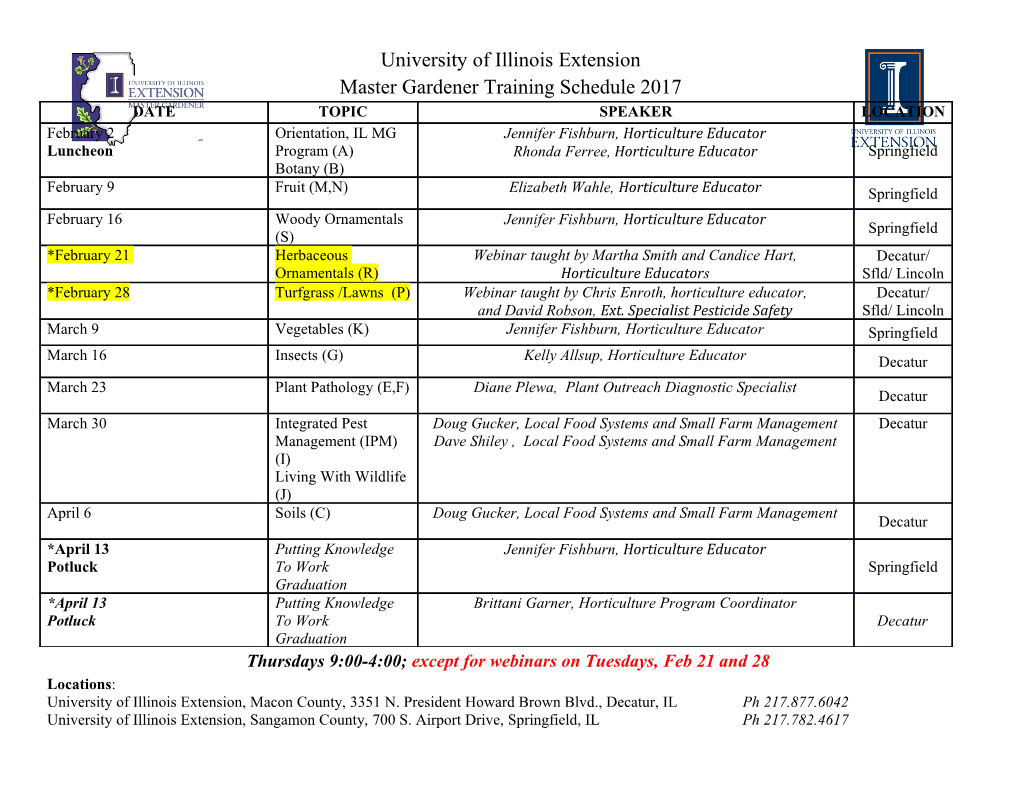
TODAY’S HIGH-RISE CO NCR ETE The Challenge: • To create a new architectural icon in a city filled with distinctive structures – one that relates to its neighbors while making its own mark on the Chicago skyline. • To build an elegant mixed use hotel/condo tower that will soar to new heights yet withstand lake - front winds, all within the narrow footprint of its downtown site. • To erect a thoroughly modern structure in record time, using advanced methods for all-season construction to assure speed and safety on the job. P L L l l i r r e M & s g n i w O , e SpotLight r o Trump International m d i Series k S f o Hotel and Tower y s e t r Chicago, Illinois u o c o t o h P The Solution: Steel reinforced concrete construction answers the challenges of footprint, strength and speed. After developing many landmark buildings in New York, The Over a two-year period, SOM presented three major designs, Trump Organization identified a new opportunity in the heart building more than 50 models of the proposed tower. The of Chicago. The site overlooks the Chicago River, where for final concept revealed the perfect marriage of elegance and decades the Chicago Sun-Times headquarters stood. When stability. SOM’s design for the 92-story structure features plans to raze the 1950s structure became known, Trump uniquely shaped setbacks with curved edges that allow lake - executives instantly saw the possibilities. The site was “im - front winds to flow easily around the building. The setbacks possible to turn down due to its location in the center of the artfully relate the tower to its neighbors – the historic city and the inherent development potential,” says Jill Cremer, William Wrigley Building, the twin towers of Marina City and Vice President with The Trump Organization. the sleek, modern 330 North Wabash Avenue, designed by Ludwig Mies van der Rohe. The reflective glass façade The Trump Organization engaged Skidmore, Owings and makes an elegant transition from the stark white Wrigley Merrill LLC (SOM) to design a distinctive residential tower Building to the jet-black 330 North Wabash tower. that would stand tall on the Chicago skyline, yet remain stable against constant winds coming off Lake Michigan. The tower would be the tallest reinforced concrete structure Final in the Western hemisphere. The site’s restrictive size inten - Building sified the challenges faced by SOM architects as design work Program Condominiums began in 2000. Hotel Health Club Reinforced concrete fits narrow footprint Retail SOM engineers identified steel reinforced concrete as Building Lobby the material that would enable them to create a soaring Parking Space residential tower that would stand strong on its chosen site. The Trump organization typically develops projects using re - inforced concrete structural frames. The same building, if rendered in steel, would have required a larger footprint than 51st 2oor the site would allow. addresses roo2ine of 330 North Wabash 29th 2oor matches height of Marina City towers 16th 2oor aligns with cornice on the Wrigley Building Irregularly stacked setbacks of Trump Tower Chicago place it in relationship with tall neighbors. Footprint of Trump Tower Chicago during foundation mat pour. “What has really made the difference for concrete construction [is] the development of high-strength concrete mixes, the greatly increased efficiency of concrete pumps and placing booms and the development of forming systems that can be erected safely and quickly, then moved to the next location.” -- Stan Korista, Structural Engineering Director (ret.) Skidmore, Owings and Merrill Reinforced concrete provides strength The complex design of Trump International Hotel and Tower pushed the capabilities of steel reinforced concrete construction. Because of the setbacks, there isn’t a single column line with a centerline running the length of the build - ing. As a result, the setback locations – which begin at the 15th, 28th and 50th floors – must bear tremendous stress. The bold design presented engineering issues that call for extraordinary strength at the three transition levels. A system of shear walls, outriggers and belt walls at transi - tion floors serves to transfer the load from columns above each setback to those below. Heavily reinforced concrete strengthens each transition floor. Together, the transition floors contain 6,850 tons of steel reinforcing bar, fabricated to exacting standards by Ambas - sador Steel of Bourbonnais and Rochelle, Illinois. The three- story 29th floor alone required 3,000 tons of reinforcement. Beams in these locations measure 36 feet square and 10 feet tall, each containing 120 rods of high-strength, recycled steel. With this degree of congestion, SOM specified high-strength, self-consolidating concrete for the transition floors: 12,000 psi compressive strength for the 16th floor and 16,000 psi for the upper two locations. Modulus of elasticity (E), a measure of stiffness, also came into play at the setback floors. In fact, Trump International Hotel and Tower marks the first time stiffness was specified for a building project. The unique stiffness of high-modulus concrete is essential to control drift and motion in tall build - ings. The stiffness has been monitored throughout con - struction, targeting for average numbers of 6,200 ksi for the 12,000-psi concrete and 7,200 ksi for the 16,000-psi mix. Reinforcing bar in outrigger and belt walls at transition 2oors. Reinforced concrete delivers speed All-season construction methods helped crews deal with the weather up high. Working on the tallest concrete structure in the Western Hemisphere was no easy task, says Dave Alexander Senior Vice President at McHugh Construction. “Conditions up high were punishing,” Alexander says. “Temperatures varied as much as 20 to 30 degrees from ground level, and winds were about 15–30 miles per hour greater.” Innovative concrete forms helped assure speed and safety of construction, regardless of what the Chicago weather scene dished out. Core walls were cast using self-jacking forms while floors, columns and outrigger wall work used a system specifically created for the project. The climbing protection panel windscreen system extended 10 feet above the top deck, protecting workers and materials on the top three floors of construction. McHugh Construction was the first U.S. company to employ this innovative system. This approach shields workers from wind and weather at upper levels while keeping debris from blowing off the structure, offering added protection for workers and observers below. While high winter winds and icing led to occasional problems with the tower’s construction crane, only a few days were lost to weather, Alexander reports. Crews maintained a fast-track schedule, constructing one floor per week at lower levels and a floor every three days above the tower’s 50th floor. >>> Trump International “Speed is everything. Hotel and Tower Without the speed Project Partners… it just doesn’t 401 North Wabash Venture LLC, Chicago, Illinois happen, and it building owner can’t be successful… Skidmore, Owings and Merrill, Chicago, Illinois I want real quality, architect and engineer but I want speed.” Bovis Lend Lease, Chicago, Illinois project manager/ general contractor -- DonaldTrump James McHugh Construction, Chicago, Illinois concrete contractor Ambassador Steel Corporation, Rochelle, Illinois reinforcing steel fabricators Hard Facts… $750 million estimated cost of construction 1,362 feet total building height 2.6 million square feet of occupied space on 92 levels 26,000 tons of steel reinforcement 194,000 total cubic yards of concrete 10,000 psi to 16,000 psi strengths of self-consolidating concrete at critical levels including the building’s mat and setbacks Foundation pour Crews needed continuous access to multiple lengths of Grade Preparing the tower’s foundation took months – culminating in 60 and 75 rebar with matching terminators nearby. “We a 24-hour marathon crews called “The Big Pour.” Construction scheduled five deliveries per day during construction of the first of Trump Tower began in March 2005 with James McHugh setback,” Helminski says. “Coordinating lists and loads – Construction of Chicago serving as concrete contractor. especially when the sequence changed in the middle of the day McHugh crews drilled holes 10 feet in diameter and 130 feet for the next day’s deliveries – took incredible care on our part.” deep, socketed six feet into the bedrock. The piles were lined with steel and filled with 10,000 psi concrete. In October, Concrete pumping system workers placed a 10-foot-thick, 4,700-cubic-yard mat of high- An innovative pumping system lifts tons of concrete to new strength, self-consolidating concrete. The mat, measuring 65 heights. An aggressive schedule, combined with ever-changing feet by 200 feet, required 500 truckloads of concrete delivered weather conditions in Chicago, called for advanced methods of continuously over nearly 24 hours. concrete handling. A specialized concrete pump located un - derground answered the challenge – enabling rapid pouring of “The Big Pour” is believed to be the largest single placement floors and walls. of self-consolidating concrete in North America. The ready-mix contractor met the stringent requirements for consistent loads Connected to the construction boom at upper levels by a system of concrete that would achieve spreads of 28 inches, allowing of tubes, the pump used a 640-horsepower engine to the self-consolidating concrete (SCC) to move approximately 50 deliver specially mixed concrete to the levels above. The pump’s feet from the point of placement. The use of SCC resulted in power enabled it to lift more than 6,000 pounds of concrete – both a time and labor reduction. Further, each load had to meet roughly the weight of two Mini Coopers – up the tower in a strict temperature controls at the time of placement and during single minute.
Details
-
File Typepdf
-
Upload Time-
-
Content LanguagesEnglish
-
Upload UserAnonymous/Not logged-in
-
File Pages6 Page
-
File Size-