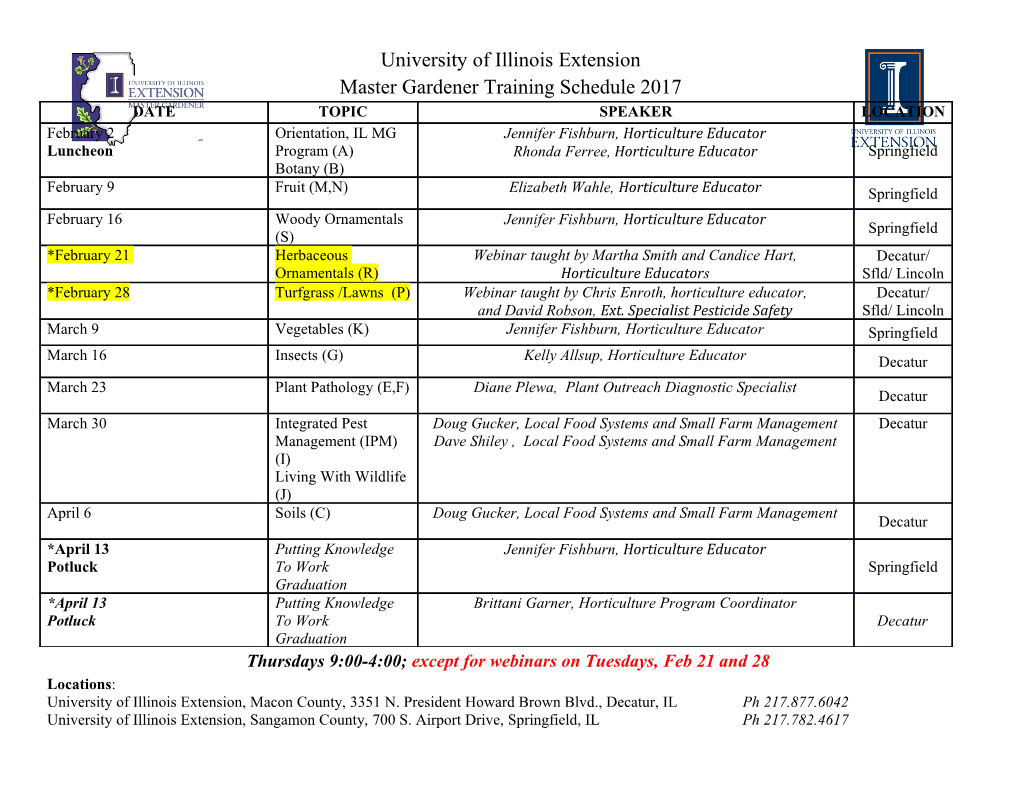
MIT 2.810 Fall 2015 Homework 4 Solutions MIT 2.810 Manufacturing Processes and Systems Homework 4 Solutions Sheet Metal Forming October 7, 2015 Problem 1. Springback Rank the metals in Table 2.2 (Kalpakjian, all editions) in terms of springback, listing those with the largest springback first. Answer: Springback is larger for materials with larger values of Y/E. Materials ranked in terms of their springback behavior E [GPa] Y [MPa] Y/E Ti 105 862 8.2 x 10-3 Mg 43 218 5.1 x 10-3 Steel 195 965 5.0 x 10-3 Cu 128 588 4.6 x 10-3 Al 74 293 4.0 x 10-3 Ni 197 653 3.3 x 10-3 Mo 345 1075 3.1 x 10-3 W 375 620 1.7 x 10-3 Pb 14 14 1.0 x 10-3 Note: The values in this Table are averaged and therefore can deviate considerably. Example: Mild steel can have a yield strength of approximately 350 MPa, which leads to a Y/E ratio of 1.53 x 10-3, a value even smaller than the one for Tungsten (W). 1 MIT 2.810 Fall 2015 Homework 4 Solutions Problem 2. Consider the manufacture of the bracket shown in Figure 1 from sheet steel (available in 4 in. wide strips) using a manual brake press or presses. Assume UTS = 70,710 psi. We are interested in estimating the unit cost to make these brackets. Please use information from Boothroyd’s “Design for Sheet Metalworking” and the following assumptions: 1. The sheet material costs $0.25/lb. 2. The cost of a press is: Press cost [$] = 2 [$/lb] × force capacity [lb]. 3. All operations take the same length of time, with no breakdowns or unusual delays between steps. 4. Labor costs $30/hr. 5. Equipment has a life of 10 years, tools—of 1 year. (a) Describe the sequence operations needed to make this bracket, including materials, tools, machines and operators. (b) Estimate the size and cost of the equipment needed to make this part. (c) Estimate the time required to make one of these (ignore waiting time). (d) Estimate the cost per bracket (materials, labor, and equipment) assuming 106 parts are produced. State any assumptions, beyond those given, explicitly. (e) Estimate the minimum bend radius for the part. (f) If the part is formed to 90±, make a rough estimate of the resulting angle due to the spring back. Use 1.5x(your minimum bend radius). How would this change if the bracket material was aluminum or titanium (rough answer is OK)? How would you compensate for spring back (list at least 3 ways)? Figure 1: Sheet steel bracket. 2 MIT 2.810 Fall 2015 Homework 4 Solutions Answer: (a) Sequence of operations: 1. Cutting and hole punching: Material: sheet metal strip, 4” wide Machine: stamping press Tool: compound die set (with cutting and punching dies) (as in Fig 16.11, Kalpakjian, 7th ed) Operator: 1 2. Bending: Material: sheet metal strip for each bracket Machine: press brake Tool: V-die Operator: 1 Note: An alternative for Step 1 can be a progressive die with 2 stations, punching and cut- off. In this case, the sheet metal strip would need to be supplied continuously as a coil.) (b) Machine force capacities: L = perimeter of cut or bend (varies) T = thickness = 0.1 in UTS = ultimate tensile strength = 70,710 psi W = V-die opening ≈ 2 in 1. Cutting: maximum shearing force (equation 16.1 in Kalpakjian, 7th ed.) �! = 0.7 ��(���) = 0.7 0.1 �� 4 �� 70,710 ��� = � = 19799 ��� 4.448 = 88 �� �� 2. Hole punching: maximum shearing force �!,!!"# = 0.7 �(��)(���) = 0.7 0.1 �� � 0.25 �� 70,710 ��� = 3887 ��� = 17.3 �� �!,!"!#$ = 17.3 �� × 4 = 15548 ��� = 69 �� 3. Bending: maximum bending force (equation 16.8 in Kalpakjian, 7th ed.) ��� ��! 70,710 ��� (1 ��) (0.1 ��)! � = = = 354 ��� = 1573 � ! � (2 ��) Press costs: 1. Stamping press: $2 � ≈ ��� ����� �������� = $2 19799 + 15548 lbs ≈ $70,700 !"#"$%& �� 2. Press brake: �!"#$%& ≈ $2 354 lbs ≈ $708 3 MIT 2.810 Fall 2015 Homework 4 Solutions Die costs: 1. Cutting and 4-hole punch die set: !" !" Usable area: � = 4 �� 2.5 1 �� 2.5 = 25 ��! ! !" !" Die set material cost: �!" = $120 + 0.36�! ≈ $130 Time for die making: !" !" Base time: � = 23 + 0.03�� = 23 + 0.03 4 �� 2.5 1 �� 2.5 ≈ 24 ℎ� !" !" !" Standard punch shape time: �!" = ��! + 0.4�! = 2 4 + 0.4(1) = 8.4 ℎ� $# Total cost for blanking and punching die set: � = $130 + 24 + 8.4 ℎ� = $1102 !"#$ !! 2. Bending V-die: Die set material cost: �!" = $120 + 0.36�! ≈ $130 (as above) Time for die making: Base time: �!" = 18 + 0.023�� 0.9 + 0.02� = �� �� �� = 18 + 0.023 4 �� 2.5 1 �� 2.5 0.9 + 0.02 2 �� 2.5 ≈ 19 ℎ� �� �� �� !" Bend length time: � = 0.68� + 5.8 � = 0.68 1 �� 2.5 + 5.8(1) = 7.5 ℎ� !" ! ! !" $# Total cost for V-die: � = $130 + 19 + 7.5 ℎ� = $925 !"#$ !! (c) Time estimate per part: Using the cycle time from Boothroyd (equation 9.22), t = 3.8 + 0.11(L+W) seconds for loading and removing a part manually from a brake press. The time for the stamping press step will be less since it has automated part ejection. Assuming 2 operators are operating the 2 machines simultaneously, the time for one part will be limited by the longer step time (bending): � = 3.8 + 0.11 � + � = 3.8 + 0.11 4 + 1 �� = 4.35 � = 1.21×10!!ℎ� per part (d) Cost per bracket: Material costs: �!"#$ = $0.25/�� 0.15 ��� = $0.038/���� Labor costs: �!"#$% = $30/ℎ� �!"#$% �!"#"$%& + �!"#$%& + �!"#$ + �!"#$ � = + � = + (� + � ) = !"#$ � !"# � !"#$% !"#$ $70,700 + $708 + $1,102 + $925 $30 = + 1.21×10!! ℎ� + $0.038 = � ℎ� $73,435 = + $0.074 � 4 MIT 2.810 Fall 2015 Homework 4 Solutions If 10! parts are produced, the cost per bracket is: $73,435 � = + $0.074 ≈ $0.15 !"#$ 10! (e) The minimum bend radius is the radius at which a crack first appears at the outer fibers of a sheet being bent (Sec. 16.5, Kalpakjian, 7th ed). Engineering strain during bending: 1 � � = = 2� + 1 2� + � � � 2� = − � � � �!"# = 0.5 − � �!"# !!!!! Here, T = 0.1 in and emax = maximum strain at fracture = ductility of the material = = !! 0.22 for low-carbon steel (Boothroyd, p. 403). Thus, !.! !" � = 0.5 − 0.1 �� = 0.18 in. !"# !.!! (f) From slide 64 of the sheet metal forming lecture, the equation for springback radius is: ! 1 1 � ! � − = 3 − 4�! �! �! �� �� where Ri = 1.5(0.18 in) = 0.27 in, T=0.1 in From the diagram on the same slide, Y/Esteel = 1/909 Y/EAl = 1/212 Y/ETi = 1/188 ! ! ! ! ! ! Then the final radii would be: = − − 3 + 4�! !! !! !" !" !! ! ! ! ! Steel: � = − 3 + 4 0.27 ! = 0.2724 in ! 0.27 !".! !".! !! ! ! ! ! Aluminum: � = − 3 + 4 0.27 ! = 0.2807 in ! 0.27 !".! !".! !! ! ! ! ! Titanium: � = − 3 + 4 0.27 ! = 0.2822 in ! 0.27 !".! !".! Estimate the final angle after springback, assuming it is initially bent to �! = 90°: If the radii are measured to the centerline of the metal sheet, then the length of the centerline arc is � = �!�! = �!�! (Figure 2). 5 MIT 2.810 Fall 2015 Homework 4 Solutions Figure 2. Diagram of springback angles. !! !.!" Steel: �! = �! = 90° = 89.2°, �! = 180° − �! = 90.8° !! !.!"!# !.!" Aluminum: � = 90° = 86.6°, � = 180° − � = 93.4° ! !.!"#$ ! ! !.!" Titanium: � = 90° = 86.1°, � = 180° − � = 93.9° ! !.!"!! ! ! Springback is largest for Titanium. Compensation methods: 1. Over-bending 2. Bottoming 3. Stretch bending 6 .
Details
-
File Typepdf
-
Upload Time-
-
Content LanguagesEnglish
-
Upload UserAnonymous/Not logged-in
-
File Pages6 Page
-
File Size-