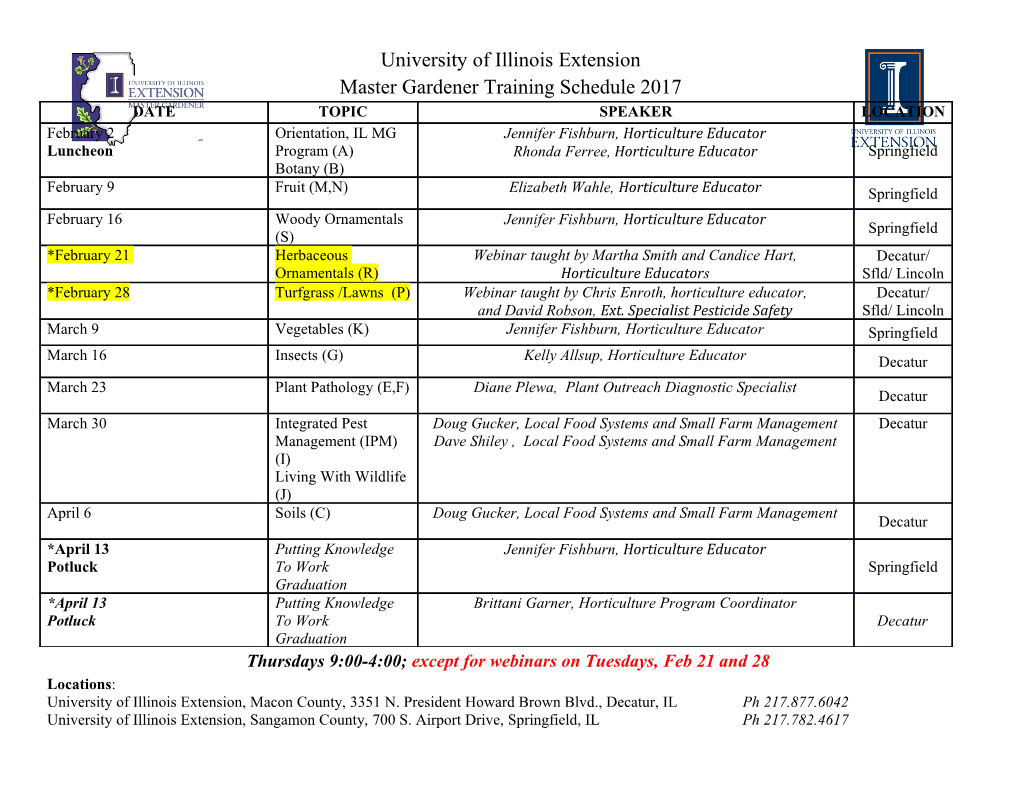
3,529,046 United States Patent Office Patented Sept. 15, 1970 2 of die materials utilized in the hot-pressing operation is 3,529,046 UTILIZENG LITHIUM oxide AND PRECURSORS somewhat limited because of the high temperature and ASSINTERING AID FOR HOT PRESSING BERYL pressures necessitated for the fabrication. LUMOXDE It is the aim of the present invention to obviate or sub Rudolph Hendricks, Jr., Oak Ridge, Tenn., assignor to 5 stantially minimize the above and other shortcomings or the United States of America as represented by the drawbacks suffered by practicing previously known tech United States Atomic Energy Commission niques for fabricating BeO structures by providing an im No Drawing. Filed June 20, 1968, Ser. No. 738,418 proved hot-pressing process wherein significant reductions Int, C. CO4b 35/08 in the cost of preparing theoretically dense or near theo U.S. C. 264-66 4. Claims 10 retically dense, high-purity BeO structures are realized. In accordance with the method of the present invention, lithium oxide (Li2O) is employed as a fugitive-type sinter ABSTRACT OF THE DISCLOSURE ing aid with BeO powders of either the so-called "pressa High-purity, theoretically dense beryllium oxide prod ble” or "non-pressable' variety so as to promote rapid ucts are produced at reduced temperatures and pressures 5 densification of the BeO at temperatures substantially low by utilizing a fugitive-type sintering aid and beryllium er than previously useable and to facilitate the fabrication oxide powder. A mixture of beryllium oxide powder and of BeO structures by utilizing relatively inexpensive hot about 0.5 weight percent lithium oxide, added either as pressing equipment such as a single-acting die. lithium oxide or a precursor of lithium oxide is hot-pressed An object of the present invention is to provide a new at a temperature of about 950° C. and a pressure of 1500 20 and improved method of fabricating structures of beryl 2000 p.s.i. to form theoretically dense products. The prod lium oxide in a substantially less expensive and more uct may be subsequently heat-treated at about 1000 readily reproducible manner than heretofore available. 1400° C. for removing virtually all the lithium oxide re Another object of the present invention is to provide maining in the product to provide a product of high purity. for the fabrication of beryllium oxide structures near or 25 at theoretical density at significantly lower temperatures and pressures than previously useable while maintaining desired product purity. The present invention relates generally to hot-pressing A still further object of the present invention is to beryllium oxide products or structures of theoretical fabricate beryllium oxide structures by hot-pressing a density or densities near theoretical, and more particular 30 mixture of beryllium oxide powder and a fluxing agent ly to a method of producing such structures at lower consisting of lithium oxide or a lithium compound which pressures and temperatures than previously employed. will decompose to lithium oxide when heated to a tempera This invention was made in the course of, or under, a ture less than about 950 C. contract with the U.S. Atomic Energy Commission. Other and further objects of the invention will be ob Beryllium oxide (beryllia or BeO) enjoys nuclear and 35 vious upon an understanding of the illustrative process physical properties which are highly advantageous in about to be described, or will be indicated in the appended nuclear power and space applications. However, because claims, and various advantages not referred to herein will of the difficulty of fabricating complicated structural com occur to one skilled in the art upon employment of the ponents from beryllium oxide with desirable density, puri invention in practice. ty, and strength characteristics, the employment of this 40 The mixture of beryllium oxide powder and lithium material in such applications has heretofore been some oxide found suitable for providing structures of theo what limited. retical density or, if desired, near theoretical density, e.g., Previous efforts utilized for the fabrication of beryllium 95 percent or greater, consists of 99.5 weight percent beryl oxide structures of desired densities and close dimensional lium oxide powder and 0.5 weight percent lithium oxide. tolerances for minimizing or obviating the high cost of 45 This mixture is hot-pressed at a temperature less than machining the structures with diamond tooling include 1000 C., preferably about 950 C., and a pressure less hot-pressing techniques as well as cold-pressing techniques than about 2000 p.s. i., preferably about 1500 p.s. i. for a followed by a sintering operation. These techniques result duration ranging from about 15 minutes for smaller struc in undesirable density gradients unless structures of near tures, e.g., wafers of about 2 inches in diameter by 1 inch theoretical density are obtained. It is also known that 50 thick, to about 30 minutes for larger structures. In other beryllium oxide structures produced by hot-pressing tech Words, the duration of the hot-pressing operation is de niques are somewhat more desirable and superior in many pendent upon the mass of the structure. respects to BeO structures made by practicing cold-press The high degree of densification of the BeO structure ing and sintering techniques. In some applications, the obtained by hot-pressing at these relatively low tempera only means of obtaining densities near or at theoretical 55 tures and pressures is believed to be due to the formation density, i.e., 3.0 grams per cubic centimeter, as well as of a Small amount of liquid phase resulting from the inter precise dimensions, is by employing a relatively expensive action of LiO and BeO to form a compound believed to hot-isostatic-pressing operation. be LibeC2 (an empirical formula for a compound not To fabricate beryllium oxide structures of near theo listed in the ASTM X-ray diffraction index and conse retical density by hot-pressing, the use of sintering aids, 60 quently identified as an unknown compound). The high high pressures, and temperatures in excess of 1500° C. degree of mobility promoted by this small amount of has heretofore been required. For example, the fabrica liquid phase causes the novel rapid densification of the tion of beryllium oxide components having a density of BeO. Also, since the thermal stability of LiBeO is ap 95 percent theoretical or greater required temperatures of parently very poor above its melting point of less than 1500 C. at 1500 p.s. i. while utilizing known sintering aids, 65 950 C., this compound acts as a fugitive-type flux or e.g., MgO. Without the use of sintering aids, an even high sintering aid for effecting and facilitating liquid phase er temperature of 1800° C. and a higher pressure of 4000 sintering. Approximately 50 percent of the LiO is lost p.s. i. are required for producing a product of about 95 during the hot-pressing operation and virtually all, if not percent thoretical density, with the temperature and pres all, of the remaining LiO may be removed by sublimation Sure requirements further increasing for fabricating struc 70 with a subsequent, or prolonged, heating of the product tures of theoretical density. In addition to the difficulties at a temperature of about 1000-1500 C, without de of producing these high-temperature products, the choice creasing the density of the beryllium oxide product. 3,529,046 3 4 While a specific quantity of LiO in the BeO-TiO mix the graphite flakes to the wetted surface. The hot-pressing ture does not appear to be critical for the formation of operation can be readily accomplished in a vacuum, inert the theoretically dense BeO products, it has been found atmosphere, or oxidizing atmosphere, depending on the that about 0.5 weight percent lithium oxide is satisfac particular die materials. tory and that a greater quantity of lithium oxide adds very In order to provide a more facile understanding of the little, if anything, to the effectiveness of the process. With present invention, an example of a typical hot-pressing op less than about 0.3 weight percent lithium oxide, the quan eration utilizing the novel lithium oxide sintering aid is tity of liquid phase present in the mixture may be insuf set forth below. This example is merely illustrative and ficient to provide a product of theoretical density. The is not intended to limit the scope of the present invention, lithium oxide employe as the fugitive-type sintering aid which is limited only by the scope of the appended claims. may be provided by lithium oxide or by any other lithium O compound capable of decomposing to lithium oxide when EXAMPLE heated to a temperature less than 950 C. For example, A beryllium oxide product of 3.00 gms./cc. was pre lithium hydroxide (LiOH) or lithium carbonate (Li2CO3) pared by admixing 1000 grams of a commercially avail have provided satisfactory results when mixed with the 5 able and “pressable' beryllium oxide powder of the de beryllium oxide in an amount or quantity equivalent to sired purity with 8.13 grams lithium hydroxide in a twin about 0.5 weight percent lithium oxide upon decomposi shell-type blender; loading the beryllium oxide-lithium hy tion of the lithium compound. When using lithium hy droxide mixture in a graphite die assembly which had been droxide as a sintering aid, it may be desirable to employ coated with approximately 0.005 mill of natural-flake a water vehicle for facilitating the admixture of the lithi graphite bonded with a suitable plastic binder; placing the um hydroxide with the beryllium oxide. A quantity of loaded graphite die assembly in an induction furnace; water corresponding to 6-8 weight percent of the reaction pressing the assembly at 100 p.s.i.
Details
-
File Typepdf
-
Upload Time-
-
Content LanguagesEnglish
-
Upload UserAnonymous/Not logged-in
-
File Pages3 Page
-
File Size-