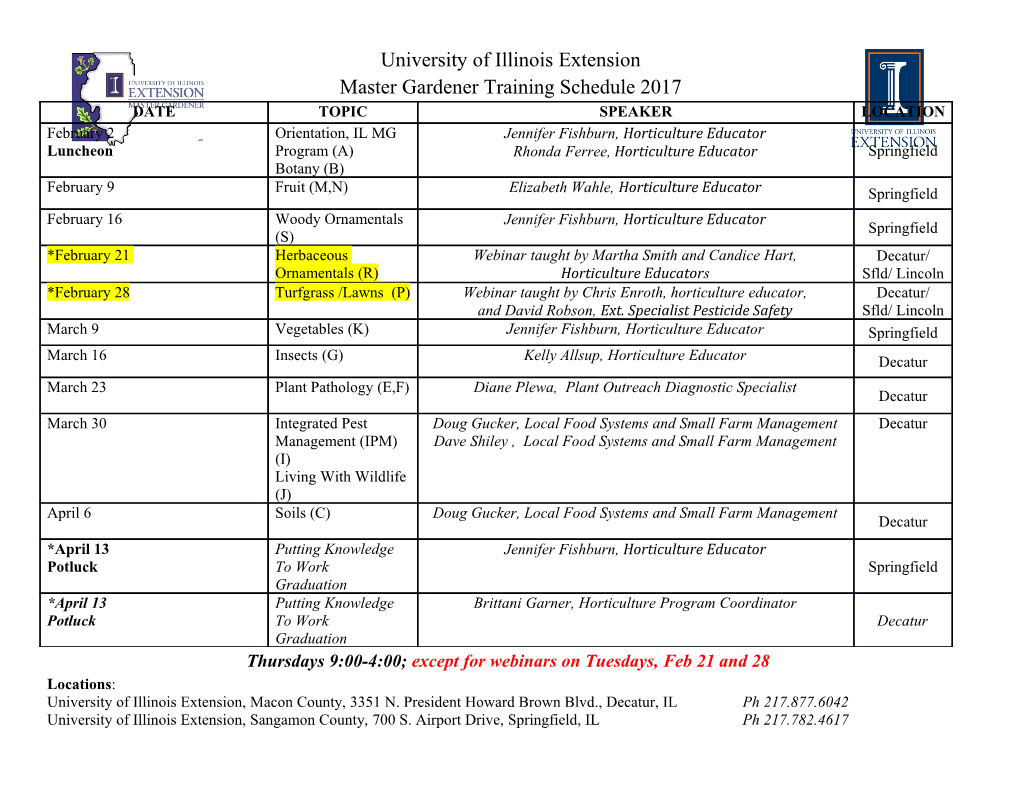
Available online at www.sciencedirect.com Journal of the European Ceramic Society 32 (2012) 203–210 ® Crystallisation of Foturan glass–ceramics ∗ Anna Evans , Jennifer L.M. Rupp, Ludwig J. Gauckler ETH Zurich, Department of Materials, Nonmetallic Inorganic Materials, Wolfgang-Pauli-Strasse 10, CH-8093 Zurich, Switzerland Received 11 April 2011; received in revised form 3 August 2011; accepted 7 August 2011 Available online 30 August 2011 Abstract Photostructurable glass–ceramics are suitable for 3-dimensional microfabrication and, in some instances, can be used as an alternative material ® to silicon in the microfabrication of micro-electro-mechanical-system (MEMS) devices. Foturan is a photosensitive lithium–aluminium–silicate glass that can be structured by an exposure to UV light, followed by a thermal treatment and an etching step. In this work, the crystallisation ® kinetics and microstructure evolution of unexposed and UV-exposed Foturan are investigated by means of differential scanning calorimetry, X-ray diffraction and scanning electron microscopy. The glass transition temperature Tg, the apparent activation energy of crystallisation Ea and ® ® the colour of UV-exposed Foturan are discussed. It is shown that nucleation and crystallisation of UV-exposed Foturan can be steered either as ® a function of temperature (non-isothermal) or as a function of time (isothermal). This is essential for the photostructuring and etching of Foturan regarding the achievable feature sizes of 25 m for MEMS applications. © 2011 Elsevier Ltd. All rights reserved. ® Keywords: Foturan ; Photostructurable glass ceramic; Nucleation; Crystallisation; MEMS microfabrication −6 −1 ◦ 1. Introduction 8.6 × 10 K (at 20 C) close to the one of most ceramic oxide thin films and it is possible to achieve high aspect-ratio The miniaturisation of electronic devices requires suitable microstructures. ® substrates for micro-electro-mechanical-system (MEMS) fabri- Foturan is used in different micro-system compo- 4–6 cation. Currently, mostly silicon is used as in the semi-conductor nents such as micro-reactors and micro-fluidic devices, 7–9 industry. There are, however, several limitations regarding the micromechanics, gas channels systems made of bonded 10 11–15 processing and applications of silicon, e.g. it is a stiff, brittle wafers and substrates for micro-solid oxide fuel cells. and semi-conducting material, and a photoresist and a lithogra- An overview of the chemical, thermal, mechanical, and elec- ® 10 phy step are required for the surface structuring. Furthermore, trical properties of Foturan is given by Dietrich et al. The −6 −1 ® × silicon has a thermal expansion coefficient of 2.6 10 K state-of-the-art photostructuring of Foturan glass is always ◦ 10 (at 20 C) and is mainly used in low-temperature applications in based on: (i) a UV-radiation step by mask photolithography or order to prevent silicon diffusion. laser-induced exposure to predefine the selective areas where 16 Photosensitive glass is an alternative material used in nuclei are formed in the glass, (ii) followed by a thermal microfabrication. Such glasses allow for a direct etching annealing step in which the nuclei a crystallised, and (iii) finally 10 and structuring through photo-radiation and thermal annealing a selective etching step by a wet-chemical agent or by focussed 1–3 17 steps. One example of a commercially available photostruc- ion beam whereby the crystalline parts are etched faster than ® ® turable glass is Foturan . The properties and the processing of the glassy areas to obtain channels through the Foturan wafers. ® ® Foturan glass offer several advantages compared to the sil- Foturan (Mikroglas Chemtech GmbH, Mainz, Germany) ® icon technology: Foturan is a good electrical insulator, it is is a photosensitive lithium–aluminium–silicate glass consisting thermally stable, and has a thermal expansion coefficient of primarily of silica (SiO2, 75–85 wt.%) and stabilizing oxides, such as Li2O (7–11 wt.%), K2O (3–6 wt.%), Al2O3 (3–6 wt.%), 10 Na O (1–2 wt.%), ZnO (<2 wt.%) and Sb O (0.2–0.4 wt.%). ∗ 2 2 3 Corresponding author. It can be microstructured by ultraviolet (UV) lithography fol- E-mail address: [email protected] (A. Evans). 0955-2219/$ – see front matter © 2011 Elsevier Ltd. All rights reserved. doi:10.1016/j.jeurceramsoc.2011.08.009 204 A. Evans et al. / Journal of the European Ceramic Society 32 (2012) 203–210 lowed by a thermal treatment and chemical wet etching with annealing programs with respect to total processing time, max- 10 hydrofluoric acid. The photosensitivity is achieved by the pres- imum temperatures, heating rates and dwell times to allow for ® ence of dopants such as Sb2O3, Ag2O and CeO2 within the small feature sizes in microfabrication with Foturan substrates. 3+ glass matrix. During the exposure to UV light, Ce absorbs 4+ a photon and is converted to Ce and releases an electron. 2. Experimental procedures ◦ ◦ In the subsequent thermal treatment at 500 C and 600 C, + ® the Ag ions absorb the electrons and agglomerate to Ag Foturan wafers (Mikroglas Chemtech GmbH, Germany, Ø: nuclei. The glass crystallises around these Ag nuclei forming 4 in., 300 m thickness) with polished surfaces were cut into a lithium-metasilicate, and proceeds actively to grain formation smaller pieces with a wafer saw (Disco Dad 321) or by diamond ® and growth. It is important to note that crystalline Foturan carving. Two types of samples – untreated and UV-exposed ® grains show a 20 times higher etch rate of around 10 m/min in Foturan wafer pieces – were used for the crystallisation and 10 10% hydrofluoric acid compared to the amorphous glass. The grain growth studies. The UV-exposed samples were radiated for ® microstructuring of Foturan wafers is based on the selective 4 min with a 310 nm UV light (LOT-Oriel 500W Hg UV-Source) etching rates of the UV-exposed and thermally treated crystalline operating at 450 W. ® areas and of the unexposed glassy ones. Nucleation and crystallisation of the Foturan samples ® The Foturan crystal size defines the actual feature size of the were studied by a combined differential scanning calorime- to-be-structured patterns and the final microfabrication resolu- ter and thermogravimetric device (DSC/TG, STA 449C Jupiter tion, e.g. the achievable aspect ratio of the geometric structures calorimeter, Netzsch, Germany). In these DSC measurements, and the roughness of the etched side walls. This crystal size the degree of crystallinity can be obtained from integration 20 depends on the UV-exposure time and wavelength, and also of the exothermic heat loss signal. In order to quantify the on the thermal annealing time and temperature. The annealing DSC results, the instrument was calibrated with calibration ® program of Foturan suggested by the Mikroglas company is standards (Netzsch 6.223.5-91.2) with known melting points ® performed in a two-step tempering consisting of a slow heating and heat losses, or phase changes. The pieces of Foturan ◦ ◦ ∼ × (1 C/min) up to 500 C with an 1 h isothermal hold to provoke ( 4 mm 4 mm) were put into an aluminium oxide crucible ◦ nucleation and a further 1 h dwell at 600 C to induce crystalli- (0.085 mL, outer diameter Ø 6.8 mm, Netzsch, Germany) and 10,18 sation and grain growth. It is reported that this two-step measured against an empty reference crucible. All crucibles annealing results in actual mean crystal sizes of 1–10 m suit- were covered with a platinum lid to increase the heat conductiv- ® able for microstructuring Foturan with feature sizes down to ity. The cooling curve was used for the correction measurement, 10 ® 25 m. It is important to note that the actual grain growth as the fully crystalline Foturan did not show any reversible temperature signifies the maximum temperature the material changes. Non-isothermal DSC experiments were measured ◦ may be exposed to in further thermal treatments and in MEMS from RT to 1100 C at different heating rates with 60 mg of ® applications. For applications at higher temperatures, Mikroglas Foturan , whereas in the isothermal DSC measurements 45 mg ® ◦ ® suggests an additional annealing of Foturan at 800 C, but the of Foturan were sufficient. A synthetic air atmosphere of 43.7% authors do not specify the exact temperature and resulting mean argon and 12.3% oxygen was set during the measurement with 10 grain sizes. an air flow of 60 sccm. The DSC characteristics were evalu- Summarising the literature, there are many reports on the ated using the Netzsch evaluation software (Proteus Thermal crystallisation and grain growth kinetics of Li2O–Al2O3–SiO2 Analysis, Version 4.7.0), whereby the peak temperatures were 19–23 in general, but so far, there are only a few publications on taken for the glass transition and crystallisation, and the onset ® 24–26 the crystallisation of UV-exposed Foturan , and detailed temperature was used for describing the melting of the glass. investigations of the nucleation and crystallisation kinetics of A detailed microstructural analysis at the different states ® ® Foturan are sparse. However, microfabrication would strongly of crystallisation of Foturan was performed. For this, the ® × benefit from a higher flexibility in the feature size through 1 cm 1 cm Foturan samples were annealed in an oven ® variation of the mean grain size which is achievable by vari- (Logotherm Controller S17, Nabertherm, Switzerland) with ◦ ◦ able crystallisation and grain growth conditions, and thermal a heating rate of 3 C/min and a cooling rate of 15
Details
-
File Typepdf
-
Upload Time-
-
Content LanguagesEnglish
-
Upload UserAnonymous/Not logged-in
-
File Pages8 Page
-
File Size-