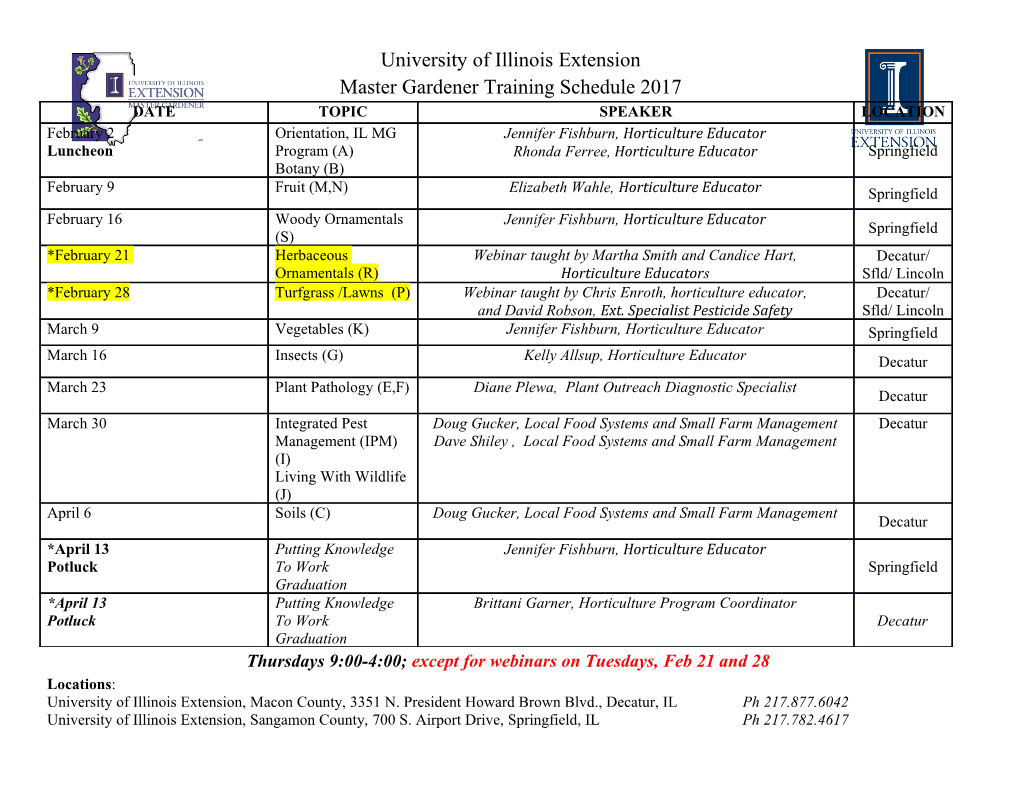
2 - Ashby Method 2.7 - Materials selection and shape Outline • Shape efficiency • The shape factor, and shape limits • Material indices that include shape • Graphical ways of dealing with shape Resources: • M. F. Ashby, “Materials Selection in Mechanical Design” Butterworth Heinemann, 1999 Chapter 7 • W. C. Young, R. G. Budynas, “Roark’s Formulas for Stress and Strain” 7th ed, McGraw-Hill, 2002 • The Cambridge Material Selector (CES) software -- Granta Design, Cambridge (www.grantadesign.com) Structural components Moments of area They depend on shapes Moment of area about axis x dA 2 Ixx = y dA ∫A Moment of area about axis y 2 Iyy = x dA ∫A Polar moment of area J = r 2 dA ∫A Modes of loading: Axial loading F σ = Stress A δ ε = Strain L • From Hooke’s Law (linearly elastic material): σ F σ = Eε ⇒ ε = = E AE F • From the definition of strain: δ FL ε = ⇒ δ = L AE σσσ F AE S = = Stiffness δ L Modes of loading: Bending Pure Bending : Prismatic members subjected to couples acting in the longitudinal plane crossing one of the principal inertia axes After deformation, the length of the neutral surface remains L. At other sections: L′ = (ρ − y)θ δ = L' − L = ()ρ − y θ − ρθ = −yθ δ yθ y ε = = − = − Strain (varies linearly) z L ρθ ρ z c ⇒ c εmax = ρ = ρ εmax y ε = − ε z c max x Modes of loading: Bending For a linearly elastic material: y σ = Eε = − Eε z z c max y = − σ Stress (varies linearly) c max M M (c = y ) σmax = = max Z Ixx /c I σz Z = xx Bending strength modulus c M I = moment of area σ z = XX Ixx /y about the bending axis Modes of loading: Bending d2y F F CEIxx E I = M()z S = = Stiffness xx 2 3 dz z δ L δ I XX = moment of area about the bending axis C = constant (depending on the loading conditions) Modes of loading: Torsion Torsion : Prismatic members subjected T to twisting couples or torques Consider an interior section of the shaft. As a torsional load is applied, the shear strain is equal to angle of twist. ) ) ρφ A 'A = Lγ = ρφ ⇒ γ = L cφ ρ γ = γ = γ max L c max Shear strain ( ∝ twist angle and radius) Modes of loading: Torsion For a linearly elastic material: T ρ τ = Gγ = Gγ c max ρ = τ Shear stress (varies linearly) c max T T τ = = (c = ρmax ) max Q K/c K Q = Twisting strength modulus c T τ = K = torsional moment of area K/ ρ Modes of loading: Torsion T KG Lγ L τ L Tρ Stiffness φ = = = ST = = ρ ρ G ρG K T φ L • Cross-sections of noncircular (non-axisymmetric) shafts are distorted when subjected to torsion. • Cross-sections for hollow and solid circular shafts remain plain and undistorted because a circular shaft is axisymmetric. K = J for circular sections only T T τ = = (c = ρmax ) max Q J/c T τ = J = polar moment of area J/ ρ T JG S = = Stiffness T φ L Modes of loading: Buckling F F Buckling : Prismatic members subjected to compression in unstable equilibrium • In the design of columns, cross-sectional area is selected such that - allowable stress is not exceeded F σ = ≤ σ A y - deformation falls within specifications FL δ = ≤ δ AE lim • After these design calculations, may discover that the column is unstable under loading and that it suddenly buckles. Modes of loading: Buckling F F • Consider ideal model with two rods and torsional spring. After a small perturbation k(2∆θ ) = restoring moment L L F sin ∆θ = F ∆θ = destabiliz ing moment 2 2 • Column is stable (tends to return to F’ aligned orientation) if L F ∆θ < k()2∆θ 2 4k F’ F < F = cr L Modes of loading: Buckling F The critical loading is calculated from Euler’s formula 2 π EI min Fcr = L2 Stress corresponding to critical loading L 2 π E ( r 2 = I /A inertia radius ) σcr = min ()L r 2 2 π E ( λ2 = L2/r 2 slendernes s ) σcr = λ2 Modes of loading: Buckling 2 π EI min Fcr = F F 2 F F Le Le = Equivalent length (length of free inflexion, distance between two subsequent inflexion points) Shape efficiency “Shape ” = cross section formed to a tubes I-sections hollow box-section sandwich panels “Efficient ” = use least material for given stiffness or strength Shapes to which a material can be formed are limited by the material itself (processability and mechanical behaviour) Goals: - quantify the efficiency of shape - understand the limits to shape - develop methods for co-selecting material and shape Certain materials can be made to certain shapes: what is the best combination? Shape and mode of loading When materials are loaded in bending, in torsion, or are used as columns, section shape becomes important Area A matters, not shape Area A and shape I ( XX ) matter Area A and shape (J, K) matter Area A and shape I ( min ) matter Shape and mode of loading Function Tie-rod F F Area A L Objective Minimise mass m: m = A L ρρρ m = mass A = area L = length Constraints Stiffness of the tie S: ρ = density S = stiffness E A E = Youngs Modulus S = L Area A matters, not shape Shape and mode of loading Function Tie-rod F F Area A L Objective Minimise mass m: m = A L ρρρ m = mass A = area L = length Constraints Must not fail under load F: ρ = density σy= yield strength F/A < σσσy Area A matters, not shape Shape and mode of loading F Function Beam (solid square section). b b Objective Minimise mass , m, where: m = ALρ = b2 Lρ L m = mass A = area Constraint Stiffness of the beam S: L = length ρ = density CEI S = b = edge length 3 S = stiffness L I = second moment of area E = Youngs Modulus Area A and shape matter b4 I is the second moment of area: I= 12 Shape and mode of loading F Function Beam (solid square section). b b Objective Minimise mass , m, where: m = ALρ = b2 Lρ L m = mass Constraint Must not fail under load F A = area L = length M M⋅b/2 ρ = density σ y > = b = edge length Z I I = second moment of area σy = yield strength Area A and shape matter b4 I is the second moment of area: I= 12 Shape and mode of loading Definition of Shape Factor Bending has its “best” shape: beams with hollow-box or I-sections are better than solid sections of the same cross-sectional area Torsion too has its “best” shape: circular tubes are better than either solid sections or I-sections of the same cross-sectional area To characterize this we need a metric - the shape factor – a way of measuring the structural efficiency of a section shape - specific for each mode of loading - independent of the material of which the component is made - dimensionless (regardless of shape scale) We define shape factor the ratio of the stiffness (or strength) of the shaped section to the stiffness (or strength) of a ‘reference shape’, with the same cross-sectional area (and thus the same mass per unit length) Shape efficiency: Bending stiffness Take ratio of bending stiffness S of shaped section to that (S o) of a neutral reference section of the same cross-section area • Define a standard reference section: a solid square with area A = b 2 (alternatively: solid circular section) • Second moment of area is I; stiffness scales as E I (S = CE I/L 3) F b C IE b S = L3 L Shape efficiency: Bending stiffness Take ratio of bending stiffness S of shaped section to that (S o) of a neutral reference section of the same cross-section area • Define a standard reference section: a solid square with area A = b 2 (alternatively: solid circular section) • Second moment of area is I; stiffness scales as E I (S = CE I/L 3) Area A is b4 A2 I = = constant o 12 12 Area A = b 2 Area A and b modulus E b unchanged Define shape factor for elastic bending, measuring efficiency, as S IE I φ e = = = 12 B 2 So EIo A Shape efficiency: Bending stiffness Properties of Shape Factor The shape factor is dimensionless -- a pure number It characterizes shape Increasing size at constant shape Each of these is roughly 2-10-12 times stiffer in bending than a solid square section of the same cross-sectional area Tabulation of Shape Factors S EI I φ e = = = 12 B 2 So EIo A (standard reference section: solid square section) b4 A2 I = = o 12 12 Tabulation of Shape Factors S IE I φ e = = = 4π B 2 So EIo A (standard reference section: solid circular section) π r 4 A 2 I = = o 4 4π Shape efficiency: Bending strength • Take ratio of bending strength (failure moment) Mf of shaped section to that (Mf,o ) of a reference section ( solid square ) of the same cross-section area • Section modulus for bending is Z; strength (M f) scales as σ y Z (M f = σy Z) I Z = y Area A is max constant b4 2 b3 A3/2 Z = ⋅ = = o 12 b 6 6 Area A and yield Area A = b 2 strength σ y unchanged b b Define shape factor for failure in bending, measuring efficiency, as M σ Z Z φ f = f = y = 6 B 3/2 Mfo σ yZo A Shape efficiency: Bending strength Shape efficiency: Twisting stiffness Take ratio of twisting stiffness S T of shaped section to that (ST,o ) of a reference section ( solid square ) of the same cross-section area T KG S = = T θ L • Torsional moment of area is K (= J for circular sections) ; stiffness scales as KG b⋅h3 b K = ⋅1− 0,58 = 0,14 A 2 o 3 h b = h Area A = b 2 Area A and b modulus G b unchanged Define shape factor for elastic twisting, measuring efficiency, as S KG K φ e = T = = 7,14 T 2 ST, o KoG A Shape efficiency: Twisting stiffness Shape efficiency: Twisting strength • Take ratio of twisting strength (failure torque) Tf of shaped section to that (Tf,o ) of a reference section ( solid square ) of the same cross-section area • Section modulus for twisting is Q; strength (Tf) scales as τ Q (Tf = τ Q) J Q = (for circular rmax sections only) b2h2 b3 A3/2 Q = = = o 3h +1,8b 4,8 4,8 Area A and b = h strength τ Area A = b 2 unchanged b b Define shape factor for failure in twisting, measuring efficiency, as T τ Q Q φ f = f = = 4,8 T 3/2 Tf, o τ Qo A Shape
Details
-
File Typepdf
-
Upload Time-
-
Content LanguagesEnglish
-
Upload UserAnonymous/Not logged-in
-
File Pages33 Page
-
File Size-