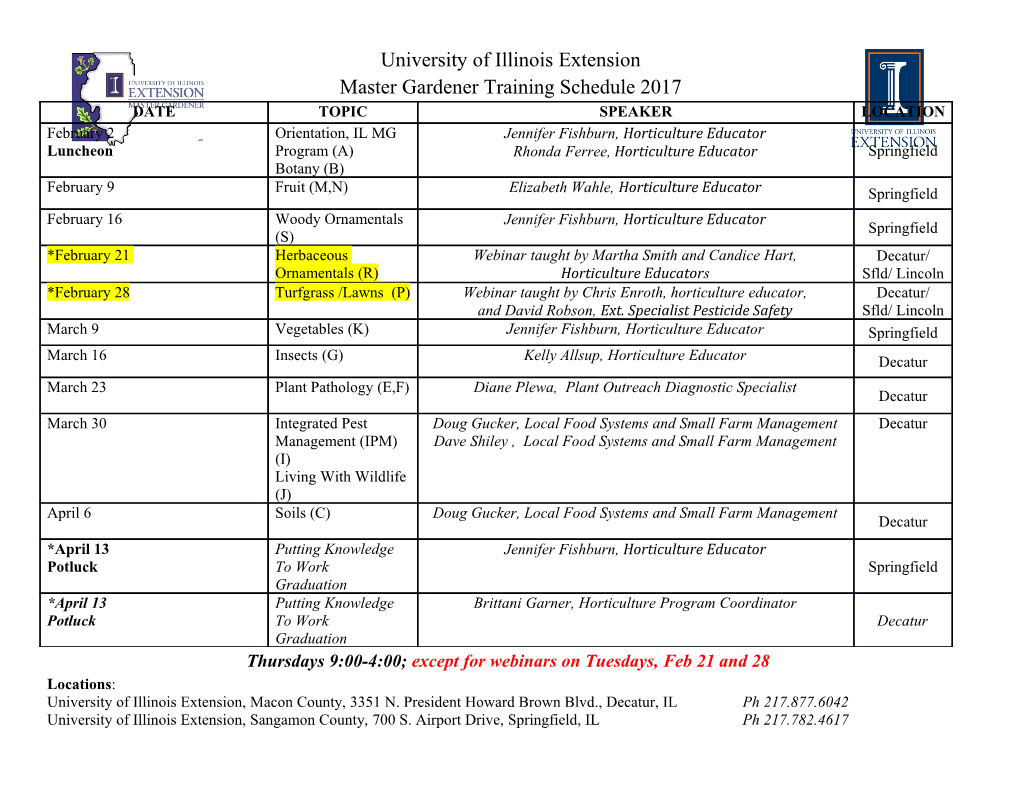
A Study of the Gas Phase Polymerization of Propylene: The impact of catalyst treatment, inject conditions and the presence of alkanes on polymerization and polymer properties. Ana R. Martins1,2, Aarón J. Cancelas1, Maria R. Ribeiro2, Timothy F. L. McKenna1 1 Laboratoire de Chimie, Catalyse, Polymères et Procédés (C2P2), LCPP Group, Villeurbanne, France 2Departament of Chemical Engineering, Instituto Superior Técnico, Lisbon, Portugal ABSTRACT: The effect of changing reaction It is also observed polymerization rate is higher conditions on propylene polymerization using a when the catalyst is pre-contacted with a liquid Ziegler-Natta catalyst is studied. It is observed that hydrocarbon instead of injecting it dry. the instantaneous rate of polymerization increases performing a prepolymerization. This is attributed The presence of an alkane increases the rate of to the effect of prepolymerization step in decreasing polymerization, by the absorption of the reaction local particle overheating in the initial instants of heat by its latent heat of vaporization but also by reaction, due to a lower catalyst activity. enhancing the local concentration of propylene inside the active sites. Hydrogen concentration affects the instantaneous rate of polymerization, once it reactivates dormant Keywords: propylene, prepolymerization, dry sites of the catalyst. A lower rate is observed in the injection, wet injection, hydrogen concentration, absence of hydrogen, since there are less active alkane, turbosphere reactor. sites where polymerization reaction can occur. INTRODUCTION: Polypropylene is one of the can have an effect on the heat removal and the most important polyolefins along with polyethylene deactivation of the catalyst. and is one of the most versatile thermoplastic polymers available. It is widely used thanks to its It has already been studied that performing a properties, which include low density, high prepolymerization step before the main stiffness, heat resistance, recyclability, easy to polymerization reaction can significantly help weld, etc, making it one of the most produced controlling the growth of the polymer particle and polymers in the world, with a production exceeding avoiding the overheating of the particles during the 50 Mton per year. initial reaction times, when catalyst is highly activated.[1],[2] The prepolymerization must occur at Despite the already massive market for polyolefins mild conditions, which allows the crystal fragments (estimated to be 125 million tons in 2011), its to be separated and covered by a thin layer of global consumption is expected to grow over the prepolymer. These mild conditions are responsible next years, continuing holding a major portion of for the production of the regular fragments’ size the market share of the commodity plastics and better replication of the catalyst shape. globally. Due to the expected growth of consumption, there is a need to increase the The injection of an alkane, to the best of our productivity and space-time yield in existing knowledge, it has not ever been made during processes; making them able to have a bigger propylene polymerization. An induced condensing production to satisfy its consumption. agent (ICA) is a saturated alkane normally between 4 and 6 carbon atoms in its structure, introduced in As it is known, olefin polymerization reactions are the beginning of olefin polymerization. Using this highly exothermic, what makes heat removal one of type of approach it is possible to increase the rate of the main limitations to achieve higher production heat removal in polyolefin processes. By the rates. Gas phase processes are even more affected vaporization of the liquid alkane, a high amount of by this, given the known limitations of heat transfer heat can be removed thanks to its latent heat of in gas state. In the current paper, will be studied the vaporization. impact of changing some reaction conditions that In ethylene polymerization, Alizadeh and In the current paper, kinetic profiles and powder Namkajorn observed that the instantaneous rate of characterization obtained from gas phase semibatch ethylene polymerization is promoted when a higher polymerization reactions have been compared using amount of ICA is introduced [3]. different reaction conditions such as prepolymerization step, hydrogen concentration, In other hand, the presence of a vaporized alkane catalyst injection and condensed mode cooling can modify the way the reaction proceeds. This is using a commercial Ziegler-Natta catalyst. caused by the co-solubility effect: the presence of an alkane will provoke an increase of the diffusivity Experimental Section of ethylene, boosting its concentration inside the active sites of the catalyst, increasing the reaction Chemicals rate. It is also true that more the alkane is soluble in the polymer, greater is the observed effect. The precatalyst was a commercial MgCl2 supported TiCl4 fourth generation Ziegler Natta, with titanium In propylene polymerization, propylene is fed content 2.8% and with di-isobutyl phtalate as partially liquid and by its vaporization it will internal donor. The catalyst had a wide particle size remove the reaction heat itself, not being necessary distribution and an average size of about 10,6 µm. a different induced condensing agent to remove heat. On the other hand, the presence of an alkane Tryethylaluminum (TEA) used as cocatalyst and will affect the activity, increasing it by the scavenger in 1M dilution in heptane was purchased enhancement of local concentration of propylene from Witco, Germany. Dicyclopentyl dimethoxy inside the active sites. silane (DCPDMS) was used as external electron donor, in 0,42M solution with heptane. The catalyst Another important aspect in olefin polymerization injection was made in two different ways: Sodium is the presence of hydrogen in the reaction medium Chloride (Acros Organics France) with purity of because it plays a decisive role in the way the 99,5% and mineral oil (OIL PRIMOL 352). TEA reaction proceeds. Mori et al.[4] studied the effect of (1M, heptane solution) was used in a ratio of 190 hydrogen in slurry polymerization and concluded Al/Ti and the external Lewis base used in a 10 Si/Ti that it acts as a chain transfer agent and increases ratio. activity, since it has the capacity of reactivating dormant sites. The salt was previously vacuum-dried during five hours at 200ºC and kept under argon atmosphere at As it is known Ziegler-Natta catalysts produce room temperature. The oil was degassed frozen polymers with high regioregularity[5], favoring 1-2 under vacuum and then kept under argon. The insertions and head-to-tail enchainment. If the experiments performed with dry injection were insertion of the polymer is from 2-1 or with other made with 30 mg of ZN catalyst, injected along enchainment, it will affect the melting point and the with 10 g of salt. The wet injection was made crystallinity of the polymer, as well as the activity, injecting 250 μL of oil, which cores 15 mg of ZN since these can also block active sites. Having this catalyst. type of regioregularity problem, the active site of the catalyst will stay dormant, which can be The propylene used was obtained from Scott reactivated by the hydrogen. Specialty Gases with a purity of 99,95% and passed through a three stage system of columns before use: Several patents show that adding a small amount of a first one filled with BASF R3-16 catalyst (CuO hydrocarbon to the catalyst prior to its injection in on alumina), a second one filled with molecular the reactor can help polymer production. As a way sieves (13X, 3 Å, Sigma-Aldrich) and a last one of testing the influence of catalyst injection, two filled with Selexsorb COS (Alcoa). Hydrogen with systems were studied: solid-solid with salt and minimum purity of 99,9% were purchased from Air solid-liquid with mineral oil. In both cases, the Liquide (France) and used as received. Argon suspension media can absorb some of the reaction provided by Air Liquide, France, with minimum heat, improving heat transfer between catalyst purity of 99,5%, was used in order to keep the particles and surrounding environment. In the case reaction environment free of oxygen. Heptane, pre- of wet injection, the oil can also fill the catalyst’s treated on 3 Å molecular sieves, was used for pores, slowing the diffusion of monomer to the preparation of cocatalyst and external donor active sites, acting like the prepolymerization step solutions. in each pore of the catalyst. After some moments of reaction, this liquid either evaporates or is displaced The alkane used in this work was iso-hexane from from the pores, which enables the monomer to enter Sigma-Aldrich with a minimum purity 99%, freely in the active sites. previously degassed frozen under vacuum and then kept under argon. Polymerization Methods to the reactor and agitation (300 rpm) was started. Subsequently, about 5 minutes after the first Gas phase homopolymerizations were done in a injection the donor/heptane mixture and the catalyst 2,5L semibatch reactor with injection valves for the suspension were injected under an argon stream. catalyst and monomer feeds. The system was kept Finally the reactor is pressurized with a mixture of under isothermal conditions and constant agitation monomer-hydrogen in the desired ratio. of 300 rpm Reactor system is schematically shown in Figure 1. Note that propylene polymerizations were performed using 15-30 mg of precatalyst. TEA and DCPDMS amounts were fixed to keep the Al/Ti ratio close to 190 and the Si/Ti ratio close to 10. Once the reaction is finished (normally one hour) the monomer inlet is closed and the reactor is rapidly cooled down and depressurized. Polymer is recovered either directly from the reactor in the mineral oil injection case, either after washing it with demineralized water, to dissolve NaCl. In this last case the final powder is then dried for at least one hour at 90 ºC to remove the remaining traces of solvent.
Details
-
File Typepdf
-
Upload Time-
-
Content LanguagesEnglish
-
Upload UserAnonymous/Not logged-in
-
File Pages10 Page
-
File Size-