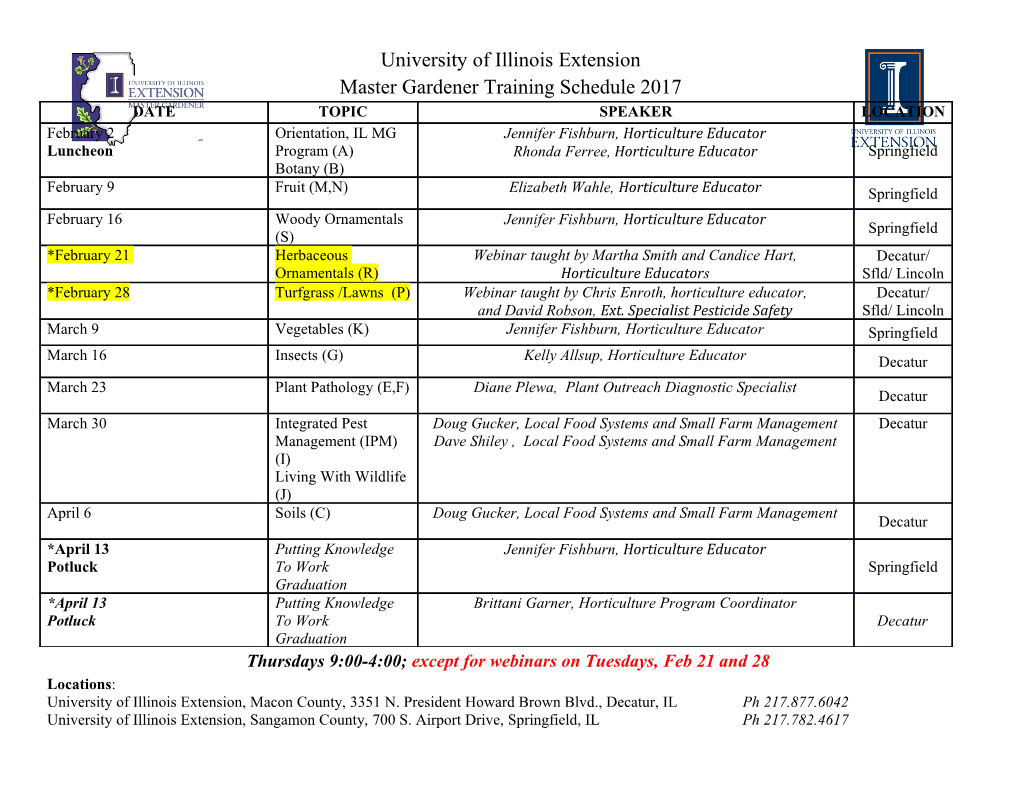
A Fresh Look at Lithium Complex Greases Part 1: How Did We Get Here? J. Andrew Waynick August 26, 2020 Overview of Presentation • Review of the lithium complex grease literature • Not exhaustive • But representative • Mountaintop flyover approach • Primarily taken from patent literature, published research papers, NLGI Lubricating Grease Guide, 6th Edition • Provides foundation for Part 2 presentation Beginnings • In 1942, five U.S. patents issued with Clarence E. Earle as inventor • Defined simple lithium soap thickened greases for subsequent decades • High temperature applicability limited, in part due to dropping point • Dropping point (D.P.) typically about 200 C • Shortly after the Earle patents issued, modifications to simple lithium soap greases began to be developed • The first ones did not increase D.P. , but did suggest directions in subsequent development that led to today’s lithium complex greases • A good discussion of these “pre-lithium complex” greases can be found in “A Brief History of Lubricating Greases” by Arthur T. Polishuk, Chapter 12C U.S. Patent No. 2,898,296 • Issued August 4, 1959; Pattendon, et. al., only months after the Earle patents expired • The first use of shorter chain dicarboxylic acids to produce higher dropping points • Used di-esters of sebacic acid (C10) or adipic acid (C6) • Longer chain monocarboxylic acid was stearic acid • Stearic acid and diester of dicarboxylic acid in base oil reacted with LiOH(aq), heated to about 204 C, then cooled and finished • Stearic/sebacic ratio = 2.1 (wt/wt) • D. P. ranged from 248 C to >260 C • When dicarboxylic acids used instead of esters: grainy product; D.P ~182 C • Likely reason was that the esters and/or transient alcohols acting as coupling agent • Enhanced “co-crystallization” of lithium stearate and di-lithium sebacate. • Higher melting points of the di-lithium salts impart higher D.P. to a sufficiently co-crystallized thickener structure • True Werner coordination complex NOT formed! Term “complex” originally used as a marketing tool, not as a chemically accurate term. Ehrlich, et.al., “The Development of Lithium Complex Greases”, NLGI Spokesman, 44, 3, pp 97 – 100, June, 1980 • Reported that lithium complex grease development began in late 1959 • Initially used low molecular weight mono-carboxylic acids (formic, acetic) as complexing acid candidates – without success • Eventually used azelaic and sebacic acids – still with problems • When di-esters of these acids were used, good results were obtained • No record of this work can be found in the open literature before this 1980 Spokesman, 4-page paper • Nonetheless, this paper continued to acknowledge the beneficial effect of using esters in facilitating sufficiently co-crystallized lithium complex thickener twenty years after the original documented work. U.S. Patent No. 2,940,930 • Issued June 14, 1960; Pattendon, et. al. • Mixture of long chain fatty acid, shorter chain dicarboxylic acid, and polyhydric alcohol heated to 148 C – 177 C for one to five hours to form complex acidic polyester mixture • Typically stearic acid; adipic, sebacic, or azelaic acid; and ethylene glycol used • Reaction mixture cooled, added to base oil, and reacted with LiOH(aq) • Mixture heated again to as high as 204 C to fully form grease and dehydrate • Alcoholic bi-products released if not remaining in final grease • Stearic/azelaic ratio = 1.5 (wt/wt) • D.P. ~ 260 C • Required two heating and cooling cycles • Once again, sufficiently co-crystallized lithium complex thickener likely facilitated by ester and/or transient alcoholic moieties acting as coupling agents U.S. Patent No. 3,681,242 • Issued August 1, 1972; Gillani, et. al. • Claimed presence of glycols in final grease deleterious to oxidation and water resistance • 2-HSA and dicarboxylic acid (azelaic) dissolved in base oil at 82 C – 93 C • LiOH(aq) slowly added and reacted • During reaction, mixture heated to 204 C – 221 C to complete reaction and dehydrate • Rapidly cool to about 104 C • Heat again to about 177 C – 190 C • Cool as rapidly as possible to at least 116 C and finish grease • 12-HSA/azelaic ranged from 1.6 to 2.95 (wt/wt) • D.P. as high as 282 C • Avoided use of esters or glycols • Required two heating and cooling cycles to achieve high D.P. U.S. Patent No. 3,791,973 • Issued February 12, 1974; Gillani, et. al. • Claimed presence of glycols in final grease deleterious to oxidation and water resistance • LiOH(aq) added to 12-HSA in base oil at 82 C – 93 C • Heated to 149 C to fully react and form Li 12-HSt and dehydrate • Cool to no lower than 96 C • Add dicarboxylic acid (azelaic), add more LiOH(aq) • Heat again to about 198 C to fully react • Cool and finish grease • 12-HSA/azelaic ranged from 2.0 to 3.2 (wt/wt) • D.P. as high as 329 C • Avoided use of esters or glycols • Required two heating and cooling cycles to achieve high D.P. U.S. Patent No. 4,435,299 • Issued March 6, 1984; Carley, et. al. • Avoided use of two heating/cooling cycles • 12-HSA and di-carboxylic acid (azelaic) dissolved in initial base oil • LiOH(aq) slowly metered into mixture at carefully controlled rate • Mixture held below 100 C until reaction complete • Heat to between 199 C and 204 C • Rapidly quench to 190 C by base oil addition • Cool and finish grease • 12-HSA/azelaic was 2.6 (wt/wt) or lower • D.P. >260 C Use of Stable LiOH Dispersion in Base Oil • Developed as a convenient alternative to the use of LiOH(aq) • Anhydrous • Can be used to make simple lithium and lithium complex greases • Reaction with acids proceeds rapidly allowing an earlier heating to top temperature • Heating to top temperature takes less time since no water from LiOH was added (no latent heat of vaporization required) • Only one heating/cooling cycle required • Shown to allow reduction in process kettle residence time and associated energy/manpower costs • Yields at least as good as traditional methods that use LiOH(aq) • Dropping points somewhat higher than when LiOH(aq) is used • Allows simple lithium or lithium complex greases to be made in hydrolytically unstable ester base oils, thus avoiding the use of pre-formed lithium soaps Borated Lithium Soap-Thickened Greases • Boric acid, B(OH)3,has been used as an alternative to di-carboxylic acids as a means to provide higher dropping point lithium soap-thickened greases • Boric acid itself has been reacted in-situ during the lithium 12-HSt formation reaction • Alternatively, addition of various borated organic compounds have been used • Representative examples of each are provided in the next slides U.S. Patent No. 3,758,407 • Issued September 11,1973; Harting • Used long chain hydroxy-carboxylic acid (12-HSA), B(OH)3, LiOH • Aqueous LiOH and B(OH)3 added to 12-HSA in base oil at about 82 C • Mixed and heated to 199 C • Additional base oil added; grease cooled and finished • Optional second hydroxy hydrocarbyl acid could be used (salicylic acid) • D.P. ranged from 251 C to >260 C U.S. Patent No. 4,376,060 • Issued March 8, 1983; Stadler • Used long chain hydroxy-carboxylic acid (12-HSA), B(OH)3, LiOH • Also used a poly-hydric alcohol to be present when LiOH was reacted with B(OH)3 • Poly-hydric alcohol preferably glycerol or cis-di-hydroxybenzene • Aqueous LiOH and B(OH)3 added to 12-HSA in base oil at about 82 C in presence of alcohol • Mixed and heated to 199 C • Additional base oil added; grease cooled and finished • D.P. ranged from 261 C to >315 C; without poly-hydric alcohol D.P. ranged from 218 C to 228 Doner/Horodysky/Keller U.S. Patents • At least 16 U.S. Patents issuing from April 15, 1986 to January 21, 1997 • Various families of organic compounds reacted with boric acid • Compounds borated included epoxides, alcohols, catechols, Mannich bases, alkoxylate alcohols, oxazolone, alkyoxylated amides, and amines • Borated compounds added to Li 12-HSt base grease at typical temperatures for grease additives • Optional organic S/P compounds sometimes optionally used to provide further increase in D.P. • S/P compounds include ZDDP and/or mixtures of organic phosphates, phosphites, and sulfurized olefins/sulfurized triacylglycerides • D.P. has high as 327 C Insights Into How Borated Additives Work • Doner, et. al. patents taught that overborating the organic substrate provided best improvement in D.P. • Likely due to formation of extended -(O-B-O)n- cross linkages between 12-hydroxystearate moieties – most likely the OH group • Linkages may be present in finished grease, or possibly formed when grease is sufficiently heated in actual use • Several major additive companies now market borated esters, amines, etc. for their ability to increase D.P. of lithium-based greases. • Significant number of papers presented over the last 10+ years discussing the use of such borated additives • Some borated additives shown to improve oxidation stability and/or rust protection • Allows reduction or elimination of azelaic/sebacic acid Additional Approaches to Increasing Dropping Point of Lithium 12-HSA Greases • The earliest of the Doner, et. al. patents taught that combinations of borated organic compounds with zinc dithiophosphates could synergistically increase D.P. • Numerous other subsequent patents and research papers provided examples of this • Other synergistic combinations comprising metal dithiophosphates and dithiocarbamates have been suggested • Diesters of terephthalic acid have been suggested Manufacturing Equipment Impact on Dropping Point • Pressurized kettles allow small amount of solvent water to remain while increasing reaction temperature,
Details
-
File Typepdf
-
Upload Time-
-
Content LanguagesEnglish
-
Upload UserAnonymous/Not logged-in
-
File Pages18 Page
-
File Size-