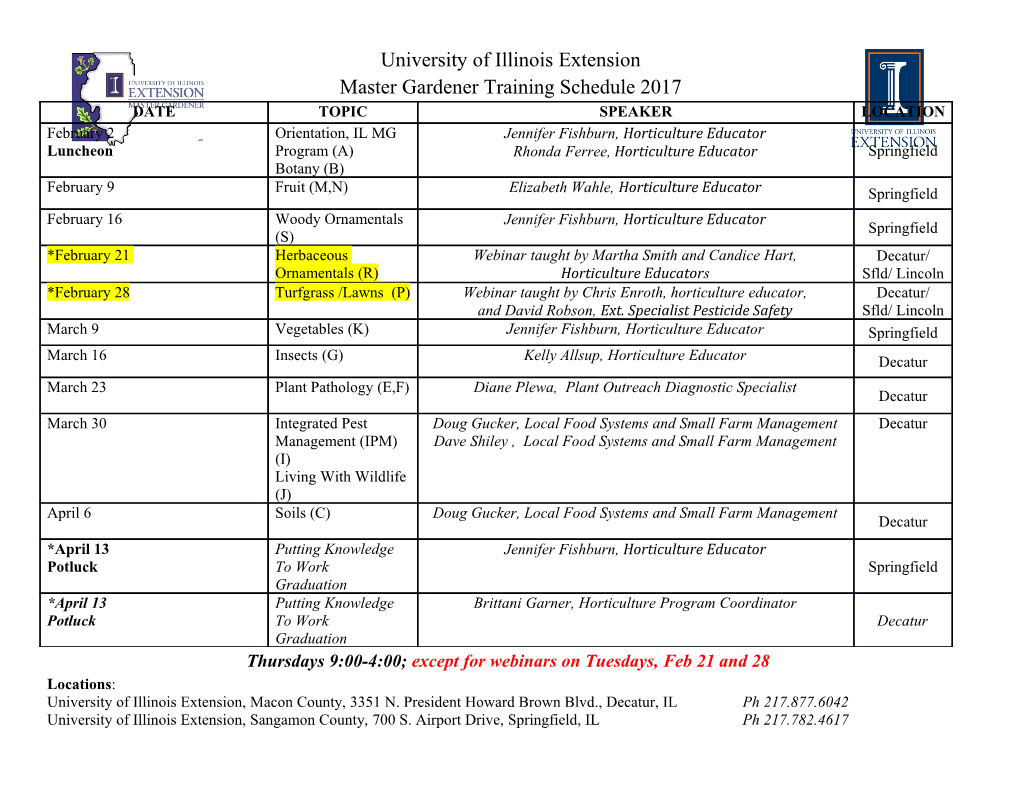
Final manuscript after referees Click here to download Manuscript: Lopez-Arce&Zornoza-Indart_JAppPhysA_2015_FINAL_AfterReferees.docx Click here to view linked References 1 Carbonation acceleration of calcium hydroxide nanoparticles 1 2 2 Induced by yeast fermentation 3 4 5 3 Paula Lopez-Arce*1,2 Ainara Zornoza-Indart2 6 7 4 1Géosciences et Environnement department, Université de Cergy-Pontoise, Neuville-sur-Oise, 8 9 5 Cergy-Pontoise cedex, France 10 11 6 2Instituto de Geociencias IGEO (CSIC,UCM), C/José Antonio Nováis 2, 28040 Madrid, Spain 12 13 14 7 *Corresponding author: [email protected] / [email protected] 15 16 8 Abstract 17 18 19 9 Carbonation of Ca(OH)2 nanoparticles and consolidation of limestone are accelerated 20 10 by high humidity and a yeast fermentation system that supplies a saturated 21 22 11 atmosphere on CO2, H2O vapor and ethanol during 28 days. Nanoparticles were 23 24 12 analyzed by X-ray diffraction and differential thermal analyses with thermogravimetry. 25 Spectrophotometry, scanning electron microscopy analyses, hydric and mechanical 26 13 27 14 tests were also performed in stones specimens. Samples exposed to the yeast 28 29 15 environment achieve 100% relative CaCO3 yield, whereas at high humidity but without 30 the yeast and under laboratory environment, relative yields of 95% CaCO and 15% 31 16 3 32 17 CaCO3 are respectively reached, with white crusts and glazing left on the stone 33 34 18 surfaces when the nanoparticles are applied at a concentration of 25g/l. 35 36 19 The largest increase in the drilling resistance and surface hardness values with slight 37 38 20 increase in the capillarity absorption and desorption coefficients and with lesser stone 39 40 21 color changes are produced at a concentration of 5g/l, in the yeast system 41 22 environment, in stone specimens initially with bimodal pore size distributions, more 42 43 23 amounts of pores with diameters between 0.1 and 1µm, higher open porosity values 44 45 24 and faster capillary coefficients. 46 47 25 An inexpensive and reliable method based on water and yeast-sugar solution is 48 49 26 presented to speed up carbonation of nanoparticles used as a consolidating product to 50 51 27 improve the mechanical properties of decayed limestone from archaeological and 52 28 architectural heritage. 53 54 55 29 Keywords: carbonation; yeast fermentation; Ca(OH)2 nanoparticles; environmental 56 57 30 conditions; humidity; CO2; limestone; consolidation 58 59 31 60 61 62 63 1 64 65 32 1 Introduction 1 2 33 When calcium hydroxide (Ca(OH)2) is exposed to atmospheric carbon dioxide (CO2) 3 4 34 under moist conditions, it reacts and converts into calcium carbonate (CaCO3) 5 6 35 releasing water as a result of carbonation. This reaction takes place in 7 36 biomineralization, medical and pharmacological processes [1,2], in concrete and 8 9 37 mortars [3-5] or as a product binder to improve the cohesion of highly porous materials 10 11 38 [6,7]. Achieving its stability is very important in architecture and decorative arts [8,9]. 12 13 39 An approach to improve conservative treatments based on the use of inorganic 14 15 40 compounds was to enhance and stimulate the growth of new calcite crystals inside the 16 17 41 porous system using biomineralization mechanisms [10]. Bacteria have been used to 18 42 create microbial deposited carbonate layers on ornamental stones. After the first 19 20 43 patent using microbial induced carbonate precipitation for the protection of ornamental 21 22 44 stone in the 90s, called Calcite Bioconcept technique, different approaches, bacterial 23 45 strains and methods, have been studied to solve the limitations of the technique . Even 24 25 46 though bacteria induced carbonate mineralization is considered a promising 26 27 47 consolidation treatment, compatible with carbonate stones and lime-based mortars and 28 48 cements, is not frequently used on-site by restorers. This is because it is a more 29 30 49 complex application process than traditional products, the incompatibility with previous 31 32 50 or subsequent treatments, their expensive price, need of knowledge on the bacteria 33 51 carbonation process and the interaction with the substrate with possible appearance of 34 35 52 secondary effects together with the lack of awareness on the long-term behavior [11- 36 37 53 13]. 38 54 Nanoscience deals with a large diversity of research fields and applications considering 39 40 55 that most of the properties are modified or improved by effect of the reduction in size of 41 42 56 nanomaterials. The use of nanoparticles is funded by the fact that the specific surface 43 57 area of a solid increases exponentially with the decrease of its volume, having a much 44 45 58 superior surface area available to react [14]. Colloidal nanoparticles are used for 46 47 59 cleaning, consolidation, and deacidification of materials from cultural heritage [15]. 48 60 Calcium hydroxide (Ca(OH)2) nanoparticles have been applied to improve the 49 50 61 petrophysical properties of lime mortars and carbonate stones, acting as a cementing 51 52 62 product to avoid decohesion of construction and building materials [16,17] or to 53 63 consolidate archaeological wall paintings [18]. 54 55 56 64 There are known factors and conditions that control the precipitation of CaCO3 57 58 65 polymorphs, such as pH, temperature, saturation, conductivity or impurities and 59 66 additives that determine the mineral precipitation and phase transformations together 60 61 62 63 2 64 65 67 with morphological and structural variations. The variables that play a role in the 1 68 carbonation of Ca(OH)2 nanoparticles, and the resulting mineral phases, are essential 2 3 69 for the final physical properties in a short- and longer- term [16]. It has been found that 4 5 70 these colloidal nano-dispersions are highly conditioned by the relative humidity (RH) 6 71 and exposure times [7,19] in the environment. These conditions directly influence the 7 8 72 speed of carbonation and the precipitation of CaCO3 polymorphs, as vaterite and 9 10 73 aragonite, which are less stable than calcite [20,21]. The alcohol present in the 11 74 environment also influences the stabilization of metastable CaCO3 polymorphic 12 13 75 phases, especially at high RH, where the rate of alcohol evaporation is slower, giving 14 15 76 rise to higher content of metastable phases, such as vaterite and aragonite [20]. 16 77 Moisture content and relative humidity during carbonation is a major factor in 17 18 78 determining the final mineral phases and pore structure of the resulting matrix in stone, 19 20 79 mortars or cement materials [16, 17], where the formation of nano-droplets of water is 21 80 necessary for the gaseous CO2 to react with Ca(OH)2 [22]. Due to the adsorption of 22 23 81 multilayers of water onto the solid Ca(OH)2 [23], high RH values (>75%) speed up the 24 25 82 carbonation process and the consolidation of lime mortars and carbonate stones [7,16, 26 17, 20, 21]. 27 83 28 29 84 Besides, even though CO2 is another key factor involved in the carbonation reaction, its 30 31 85 concentration and registration is not often considered in the studies of carbonation of 32 86 Ca(OH)2 nanoparticles. The influence of CO2 concentration on the acceleration of 33 34 87 carbonation process of Ca(OH)2 has been extensively debated. Even though, Van 35 36 88 Balen and Van Gemert [24] concluded that lime mortar carbonation depends on the 37 89 presence of water and occurs very quickly especially in a saturated CO2 atmosphere, 38 39 90 Van Balen [25] later shows that the reaction speed is not dependent upon the CO2 40 41 91 concentration, within the limits he tested. Dheilly et al. [26] demonstrate the importance 42 92 of CO2 concentration and RH during carbonation process. These authors observed 43 44 93 how a lime paste displays a rapid and complete reaction in a carbonic atmosphere, 45 46 94 while in a low CO2 environment carbonation takes twice as long. Cultrone et al. [5], 47 also demonstrate that high CO concentrations favor a faster and more complete 48 95 2 49 96 carbonation process, with 8 days being enough to convert portlandite (Ca(OH)2) into 50 51 97 90wt.% calcite (CaCO3) of lime-based mortars. They showed that under natural 52 conditions, carbonation is much slower and similar levels were not reached for 6 53 98 54 99 months, suggesting that the carbonation process is influenced by the amount of CO2. 55 56 100 Recently, Visser [27] showed that a change in CO2 concentration does not change the 57 58 101 carbonation process and that the amount of material that can carbonate can be 59 102 determined on the basis of the amount of calcium in the unreacted material. 60 61 62 63 3 64 65 103 Nevertheless, Cizer et al. [28] show that carbonation process is kinetically favored 1 104 under high RH and high pCO2 where supersaturation plays a critical role on the 2 3 105 nucleation density and size of CaCO3 crystals. 4 5 6 106 The control the CO2 concentration during carbonation process of lime based products, 7 107 for structures and building materials in the construction field, on-site under natural 8 9 108 conditions is a difficult task. It is hard to obtain CO2 sources that are reliable, durable, 10 11 109 cheap and easy to manage [29]. Saitoh et al. [30] developed an easy and cheap 12 110 method to produce CO2 for diseases purposes by using a yeast-sugar solution in 13 14 111 plastic bottles.
Details
-
File Typepdf
-
Upload Time-
-
Content LanguagesEnglish
-
Upload UserAnonymous/Not logged-in
-
File Pages39 Page
-
File Size-