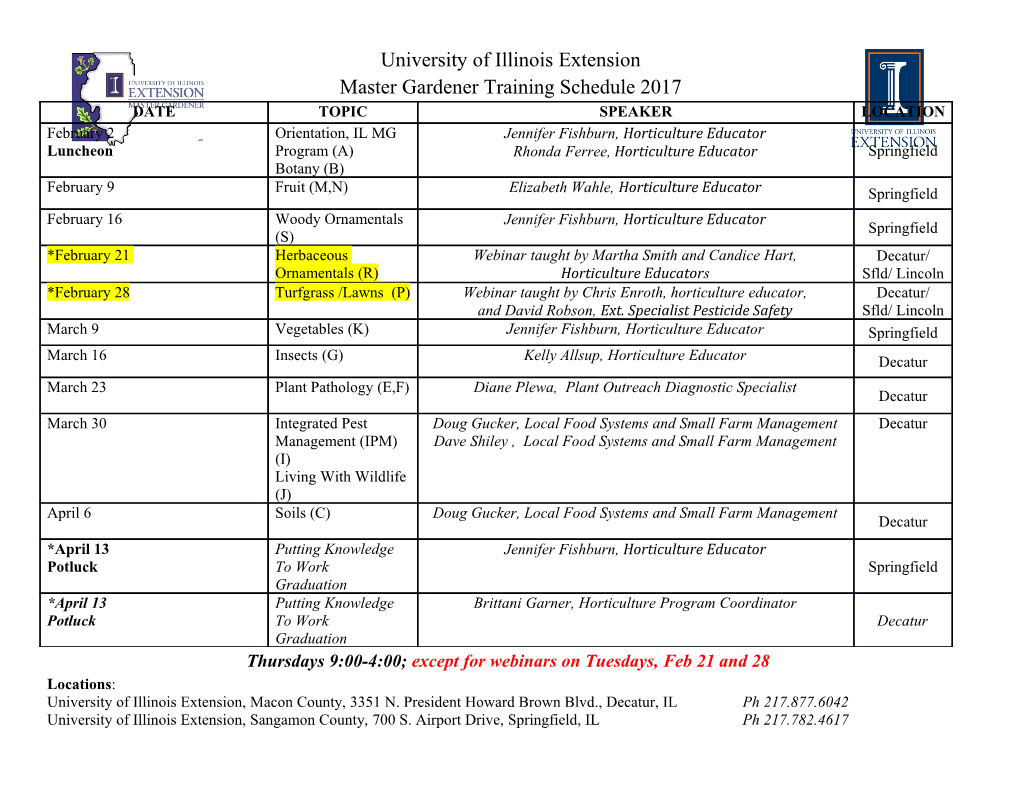
Coal to Liquids (CTL): An Overview Rio de Janeiro March 2007 Dr. Dan Driscoll Project Manager Gasification and Fuels Division National Energy Technology Laboratory Interest Drivers for CTL “Addicted to oil” – State of the Union address 2006 US petroleum imports in 2005 exceeded $250 billion 35% of energy consumption is from Oil 1 Daily world consumption is 84 million bbl/d – 20% higher than 1995 – expect 120 M by 2030 World vehicle ownership at 700 M; – double by 2030 to 1.5 billion; – developing countries to triple 96% of all energy used for transportation – largest demand for oil World oil supplies could peak between 2016 and 2037 2 Oil resources not equitably distributed globally; coal more wide spread Concerns in: Energy security and Economic Development Oil availability supply issues Infrastructure difficulties Coal remains the most abundant fossil fuel in the world. Products produced from oil can be made from coal. Outside Activities: National Coal Council Report (March 2006) identified capacity to support production of 2.6 million bpd of liquid fuels from coal by 2025. See www.NationalCoalCouncil.org Southern States Energy Board Report (July 2006) called for aggressive federal investment in CTL incentives “to encourage the private sector to step forward on a massive scale.” See www.AmericanEnergySecurity.org DOD Air Force Request for Interest in Military Alternative Fuels 1Ref: World Coal Institute Report “Coal-to-Liquids” November 2006 2Ref: Hirsch, Robert, et, al., “Peaking of World Oil Production: Impacts, Mitigation, & Risk Management”, NETL, February 2005 U.S. Dependence on Foreign Oil Oil Reserves Saudi Arabia 21% Canada 14% Iran 10% Iraq 9% Kuwait 8% U.A.E. 8% Venezuela 6% Russia 5% Libya 3% Nigeria 2% U.S. 2% Rate of Use U.S. 25% Japan 7% China 7% Germany 3% Russia 3% The United States uses India 3% more oil than the next Canada 3% Brazil 3% five highest-consuming S. Korea 3% nations combined. France 3% Mexico 3% 0% 5% 10% 15% 20% 25% Updated July 2005. Source: International Energy Annual 2003 (EIA), Tables 1.2 and 8.1-O&GJ. Canada’s reserves include tar sands. U.S. Energy Sources % of U.S. % of Total Electricity U.S. Energy Energy Source Supply Supply Oil 3 39 Natural Gas 15 23 Coal 51 22 Nuclear 20 8 Hydroelectric 8 4 Biomass 1 3 Other Renewables 1 1 Why Coal? Coal Reserves are Abundant Years Supply at Current Production Rates Provides over half 300 Nation’s electricity Abundant domestic 200 Western reserves 100 Eastern Low, relatively stable prices 0 Coal Oil Gas U. S. Coal Resources Are Widely Distributed Delineation of U.S. Coal Resources and Reserves Sufficient reserve to meet projected demand for electricity and up to 4MMBPD CTL industry for over 100 years 1 ton of coal produces 2 barrels of liquid Source: EIA Coal Reserves Data 1997 http://www.eia.doe.gov/cneaf/coal/reserves/chapter1.html#chapter1a.html Coal-to-Liquids – Rationale U.S. economy requires a reliable supply of liquid fuels for national security and economic stability. Oil refineries operating at > 90% capacity, refining capacity highly concentrated in Gulf Coast Rising oil prices and imports, moratoriums for off-shore drilling Increasing concern about terrorism/natural disasters on petroleum supply chain. Coal-derived liquid fuels can supplement oil-based fuels and moderate fuel price increases. Coal to Liquids Technologies Conversion Technologies: Direct Liquefaction (Bergius Hydrocracking) Indirect (Gasification + Fischer-Tropsch) Liquefaction. Direct Liquefaction - Dormant in the U.S. but being actively pursued in China. The Shenhua project in Inner Mongolia will bring a full scale single train, 20,000 BPD commercial unit into production in 2008 using Headwaters technology. Inner Mongolia Coal Liquefaction Plant Schematic, China 2006 Direct Coal Conversion Projects Originally developed in Germany in 1917 Used to produce aviation fuel in WWII US spent $3.6 billion on DCC from 1975-2000 Headwaters Technology licensed to China in 2002 Lawrenceville, NJ Catlettsburg, KY Inner Mongolia, China 3 TPD (30 bpd) 250 – 600 TPD 4,200 TPD (1,800 bpd) (17,000 bpd) Direct Coal Conversion to Liquid Fuels H2S, NH3, COx Methane Make-up Recycled H 2 Gas Recovery & Ethane H2 Treatment LPG Hydro- Coal + Coal Gasoline treating Refining Catalyst conversion Diesel Fuel Unit H-Donor Slurry Slurry Fractionation Heavy Vacuum Gas Oil Solvent Ash Reject Deashed Oil Deashing Gasifier Unconverted Coal Direct Conversion Advantages Disadvantages Conceptually simple process High aromatic content Produces high-octane gasoline Low-cetane number diesel More energy efficient than indirect conversion Potential water and air (i.e. more fuel / BTUs emissions issues produced per ton of coal) Fuels produced are not a Products have higher good environmental fit energy density for the U.S. market (BTU/gallon) than May have higher indirect conversion operating expenses than indirect conversion Indirect Coal Conversion Originally developed in Germany in 1923 (Franz Fischer and Hans Tropsch) Used to produce diesel fuel during WW-II Currently used to produce liquid fuels and chemicals in South Africa Example of Prior Large Scale US-based Facilities World Large Scale Facilities Brownsville, TX 7,000 bpd GTL Plant • Designed by HRI (Headwaters predecessor) • First commercial use of High Temp. FT • Operated 1950-55 • Shut down when oil price dropped due to Secunda, South Africa Middle East oil discoveries. 150,000 bpd Indirect Coal Conversion Coal Petcoke Biomass Oxygen/ etc Steam Catalyst C H FT Product Gasification & H2 + CO Fischer-Tropsch x y Liquids Gas Cleaning Syngas Synthesis Separation & & Wax Upgrading Steam Tail Gas Sulfur, Water Ultra-Clean CO2 & Liquid Fuels and Ash Oxygenates & Chemical Feedstocks Steam Electric Power Generation Electricity Gasification- A Versatile Source of Fuels Oxygen Extreme Conditions: .1,000 psig or more .2,600 Deg F .Corrosive slag and H2S gas Coal, Products (syngas) biomass, CO (Carbon Monoxide) Gas pet. coke H2 (Hydrogen) Clean-Up [CO/H2 ratio can be adjusted] Before By-products Product H2S (Hydrogen Sulfide) Use CO2 (Carbon Dioxide) Slag (Minerals from Coal) Water Coal Gasification Chemistry 2C (coal) + ½O2 + H2O = 2CO + H2 Simultaneous Three Body Collisions are Unlikely Multiple Bi-Molecular Interaction Mechanism in Effect C + O2 = CO2 C + CO2 = 2CO C + ½O2 = CO C + H2O = CO + H2 C + 2H2 = CH4 Gasifiers GE Energy ConocoPhillips KBR Shell Siemens (Chevron-Texaco) E-Gas Transport SCGP (GSP/Noell) Reactor Slurry-feed Dry-feed Comparison of Gasifier Characteristics Moving Bed Fluidized Bed Entrained Transport (Lurgi & BGL) (U-Gas & HTW) Flow Flow (GE, Shell, (KBR) E-Gas, Siemens) Ash Cond. Dry Slagging Dry Agglomerate Slagging Dry Coal Feed ~2in ~2in ~1/4 in ~1/4 in ~ 100 Mesh ~1/16in Fines Limited Better Good Better Unlimited Better than dry ash Coal Rank Low High Low Any Any Any Gas Temp. (°F) 800-1,200 800-1,200 1,700-1,900 1,700-1,900 >2,300 1,500-1,900 Oxidant Req. Low Low Moderate Moderate High Moderate Steam Req. High Low Moderate Moderate Low Moderate Issues Fines and Carbon Conversion Raw gas Control Hydrocarbon liquids cooling carbon & inventory carryover Products from Syngas Clean Electricity Gasification Clean Syngas and Gas Gas H2, CO, CO2 Cleaning Turbine Stationary Fuel Cells H2 Separation Building Shift Reaction of H CO2 for Blocks Methanation 2 for CO + H2OH2 + CO2 from CO Sequest CO + 3H CH + H O 2 Chemical 2 4 2 ration Industry Fischer- Tropsch or Methanol Synthesis H2 2nH2 + nCO (- CH2-)n + nH2O Methane CO + 2H2 CH3OH (SNG) Transportation Fuels Fuel Cell Vehicle Fischer-Tropsch (F-T) Technology 0 CO(g) + 2H2(g) (CH2)n(l) + H2O(g) ΔH = -165kJ/mol The water produced combines with CO in the water-gas shift reaction to form H2 and CO2 0 CO(g) + H2O(g) (CO2)(g) + H2(g) ΔH = - 41.2kJ/mol The overall F-T reaction is therefore described as follows: 0 2CO(g) + H2(g)(-CH2-)n(l) + CO2(g) ΔH = -206 kJ/mol Another approach to liquid fuels via synthesis gas is methanol production. CO(g) + 2H2(g) CH3OH(l) Methanol can be used directly or converted into gasoline through a process such as the Mobil process using zeolite catalysts. *With Fe-based Catalysis Anderson Schultz Flory Distribution Indirect Conversion The liquid products from indirect conversion process are zero sulfur, near zero aromatic hydrocarbons. Minimal refining needed to produce ultra-clean diesel or jet fuel. Carbon dioxide produced during indirect conversion can be captured for subsequent storage. Indirect conversion plants can co-produce electric power to improve process economics. If hydrogen is the preferred fuel in the future, these plants may be easily reconfigured to produce fuel cell grade hydrogen SASOL in South Africa has two large, indirect coal conversion facilities (SASOL II and III) that currently produce about 150,000 BPD of liquid fuels. Indirect Conversion Advantages Disadvantages Ultra-clean products Conceptually more Well suited for CO2 capture complex than direct conversion Well suited for electric power co-production Less efficient fuel production than direct May have lower operating expenses than Produces low-octane direct conversion gasoline Fewer BTUs per gallon than direct conversion products Comparison of Typical Direct and Indirect Liquefaction Final Product Slate Direct Indirect Distillable product mix 65% diesel 80% diesel 35% naphtha 20% naphtha Diesel cetane 42-47 70-75 Diesel sulfur <5 ppm <1 ppm Diesel aromatics 4.8% <4% Diesel specific gravity 0.865 0.780 Naphtha octane (RON) >100 45-75 Naphtha sulfur <0.5 ppm Nil Naphtha aromatics 5% 2% Naphtha specific gravity 0.764 0.673 Hybrid Conversion A hybrid conversion facility is basically a direct and indirect conversion facility built next to one another. The products of the direct and indirect conversion trains complement each other and can be blended to produce high quality diesel and gasoline.
Details
-
File Typepdf
-
Upload Time-
-
Content LanguagesEnglish
-
Upload UserAnonymous/Not logged-in
-
File Pages57 Page
-
File Size-