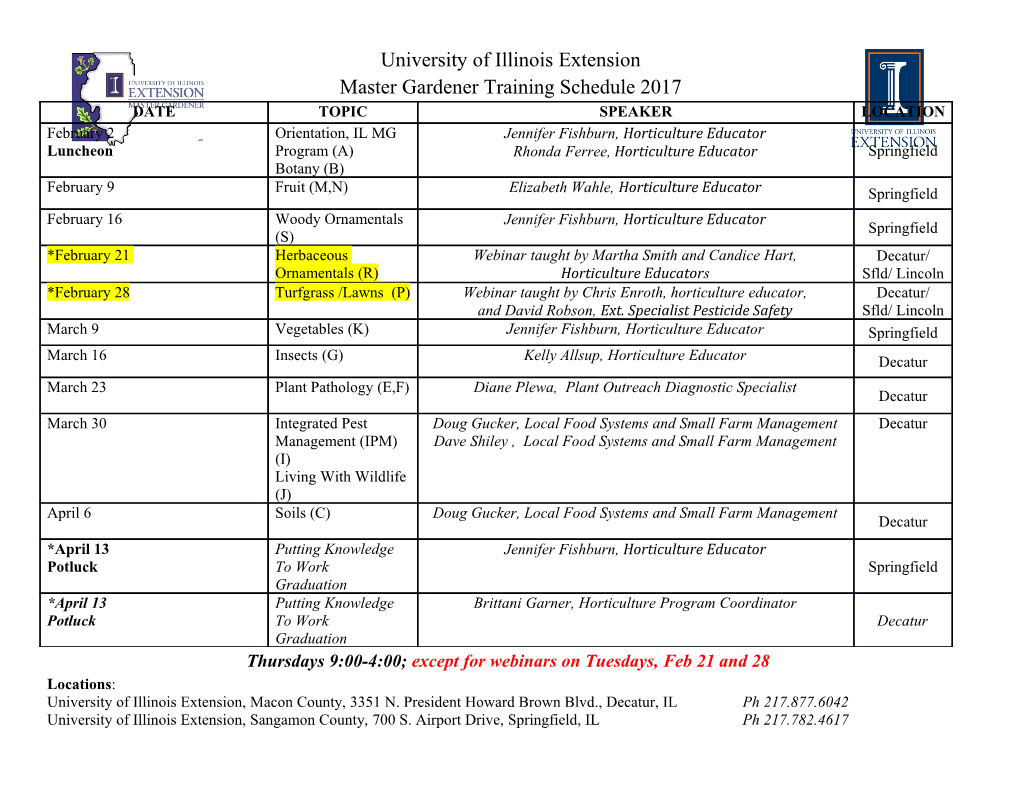
materials Article Effect of Zinc Phosphate on the Corrosion Behavior of Waterborne Acrylic Coating/Metal Interface Hongxia Wan 1, Dongdong Song 1,2,*, Xiaogang Li 1,3,*, Dawei Zhang 1, Jin Gao 1 and Cuiwei Du 1 1 Institute for Advanced Materials and Technology, University of Science and Technology Beijing, Beijing 100083, China; [email protected] (H.W.); [email protected] (D.Z.); [email protected] (J.G.); [email protected] (C.D.) 2 Aerospace Research Institute of Materials and Processing Technology, Beijing 100076, China 3 Ningbo Institute of Material Technology and Engineering, Chinese Academy of Sciences, Ningbo 315201, China * Correspondence: [email protected] (D.S.); [email protected] (X.L.); Tel.: +86-010-68383576 (D.S.); +86-010-62333931 (X.L.) Academic Editor: Yong-Cheng Lin Received: 22 April 2017; Accepted: 30 May 2017; Published: 14 June 2017 Abstract: Waterborne coating has recently been paid much attention. However, it cannot be used widely due to its performance limitations. Under the specified conditions of the selected resin, selecting the function pigment is key to improving the anticorrosive properties of the coating. Zinc phosphate is an environmentally protective and efficient anticorrosion pigment. In this work, zinc phosphate was used in modifying waterborne acrylic coatings. Moreover, the disbonding resistance of the coating was studied. Results showed that adding zinc phosphate can effectively inhibit the anode process of metal corrosion and enhance the wet adhesion of the coating, and consequently prevent the horizontal diffusion of the corrosive medium into the coating/metal interface and slow down the disbonding of the coating. Keywords: waterborne acrylic coating; zinc phosphate; LEIS 1. Introduction Serious environment problems have directed attention toward water-based coatings because of their low volatile organic compounds VOC advantages [1–3]. However, waterborne coatings have performance limitations; moreover, they have been extensively used indoors, where the corrosion environment is below the C3 level [4]. Thus, waterborne coatings need to have improved performance for long-term applications [5–8]. Acrylic coatings have good barrier properties and ageing resistance, which has attracted much attention [9,10]. Disbonding is the first sign of coating/metal interface corrosion [11–14], which is the most common form of failure that limits coatings, especially for long-term applications of waterborne coatings [15]. Hence, the ability to resist disbonding characterizes the coating service life, which is the main purpose for developing long-lasting water-based coatings suited for harsh environments [16]. Traditional coatings would exhibit significant cathodic disbonding under different environments that would affect the coating service life. Adding an electrochemically active antirust pigment is a common method for improving the antirust capacity of the coating [17,18]. Therefore, the effect of an electrochemically active antirust pigment on the cathodic disbonding process when added into a waterborne acrylic coating is significant. Much attention has been given to phosphate antirust pigments for their relative environmental protection [19–23]. Phosphate pigments mainly contain aluminum tripolyphosphate [24] and zinc phosphate [25]. The antirust function and mechanism of zinc phosphate have been previously studied. Bethencourt et al. [26] studied the failure process of a waterborne acrylic zinc phosphate coating using Materials 2017, 10, 654; doi:10.3390/ma10060654 www.mdpi.com/journal/materials Materials 2017, 10, 654 2 of 13 electrochemical impedance spectroscopy (EIS). The corrosive failure of composite coatings in 3.5% NaCl solution were divided into three stages: the first stage is the water diffusion stage, wherein Materials 2017, 10, 654 2 of 13 the coating impedance decreases; the second stage involves the zinc phosphate coming in contact withcoatings water, whereinin 3.5% NaCl a passivation solution were rust divided resistance into effectthree stages: reaches the a first certain stage concentration is the water diffusion after water absorption;stage, wherein and the the third coating stage isimpedance the start ofdecreases; the shielding the second decline stage after involves the zinc the phosphate zinc phosphate is exhausted. Yaweicoming ShaoMaterials etin al. contact2017 [,27 10, ,65428 with ] studied water, the wherein corrosion a passivation inhibition rust of zincresistance phosphate effect inreaches an oil-based 2 aof 13certain epoxy coatingconcentration using EIS after and water electrochemical absorption; and noise, the andthird showedstage is the that start zinc of the phosphate shielding providesdecline after a recovery the zinc phosphatecoatings in 3.5%is exhausted. NaCl solution Yawei were Shaodivided et intoal. three[27,28] stages: studied the first the stage corrosion is the water inhibition diffusion of zinc effect for coatingstage, wherein defects. the Currently, coating impedance researchers decreases; [29] foundthe second that stage when involves the corrosive the zinc mediumphosphate permeates phosphate in an oil-based epoxy coating using EIS and electrochemical noise, and showed that zinc the oil-basedcoming epoxy in coating/metalcontact with water, interface, wherein zinc a passivation phosphate rust partly resistance dissolves effect andreaches forms a certain metal substrate phosphate provides a recovery effect for coating defects. Currently, researchers [29] found that when concentration after water absorption; and the third stage is the start of the shielding decline after the phosphate and stabilizes the protective film, which contains γ-Fe2O3, α-FeOOH, γ-FeOOH, and iron the corrosivezinc phosphate medium is permeatesexhausted. Yaweithe oil-based Shao et epoxyal. [27,28] coating/metal studied the interface,corrosion zincinhibition phosphate of zinc partly phosphate.dissolvesphosphate Moreover, and forms in an theoil-based metal protective substrate epoxy coating film phosphate containsusing EIS and and carboxyl st electrochemicalabilizes and the hydroxylprotective noise, and groups film,showed which that that zinc contains enhance the combinationγ-Fe2Ophosphate3, α of-FeOOH, coating provides γ-FeOOH, and a recovery metal. and effect Someiron for phosphate. coating researchers defects. Moreover, [Currently,30] have the researchers proposedprotective [29] film that found contains zinc that phosphatewhen carboxyl can formand stable hydroxylthe iron corrosive phosphates groups medium that permeates andenhance block thethe medium combinationoil-based diffusionepoxy of coating/metal coating into and the interface,metal. channels Some zinc and researchersphosphate slow down partly [30] corrosion.have However,proposeddissolves the that effects andzinc offorms phosphate zinc metal phosphate substratecan form activephosphate stable fillersiron and phosphates onstabilizes the waterborne the and protective block medium acrylic film, which cathodicdiffusion contains into disbonding the channelsγ-Fe 2andO3, α slow-FeOOH, down γ-FeOOH, corrosion. and ironHowever, phosphate. the Moreover, effects of the zinc protective phosphate film contains active carboxylfillers on the process, especiallyand hydroxyl involving groups that the enhance interface the combination corrosion mechanismof coating and ofmetal. cathodic Some researchers and anodic [30] processes, have have waterborne acrylic cathodic disbonding process, especially involving the interface corrosion not been comprehensivelyproposed that zinc phosphate studied. can form stable iron phosphates and block medium diffusion into the mechanism of cathodic and anodic processes, have not been comprehensively studied. In thischannels paper, and we slow studied down thecorrosion. coating/metal However, the interface effects of corrosionzinc phosphate process active of fillers waterborne on the acrylic In this paper, we studied the coating/metal interface corrosion process of waterborne acrylic coatings withwaterborne zinc phosphate acrylic cathodic using disbonding EIS and localizedprocess, especially EIS (LEIS). involving Furthermore, the interface we studiedcorrosion the effects coatingsmechanism with zinc of cathodicphosphate and using anodic EIS processes, and localize have notd EIS been (LEIS). comprehensively Furthermore, studied. we studied the effects of activeof active pigments Inpigments this paper, on on coating/metal wecoating/metal studied the coating/metal interfaceinterface co corrosion rrosioninterface andcorrosion and disbonding disbonding process ofprocesses waterborne processes in waterborneacrylic in waterborne acrylicacrylic coatings.coatings coatings. with zinc phosphate using EIS and localized EIS (LEIS). Furthermore, we studied the effects of active pigments on coating/metal interface corrosion and disbonding processes in waterborne 2. Results2. Resultsacrylic coatings. 2. Results 2.1. The2.1. CoatingThe Coating Adhesion Adhesion Test Test FigureFigure2.1.1 showsThe 1 Coating shows the Adhesion the adhesion adhesion Test values values of of 0% 0% and and 8%8% zinc phosphate phosphate coatings. coatings. The The adhesion adhesion values values werewere the samethe sameFigure in the in 1 showsthe 0% 0% and the and adhesion 8% 8% zinc zinc values phosphate phosphate of 0% and coatings.co 8%atings. zinc phosphateAdding Adding zinc coatings. zinc phosphate phosphate The adhesion did didnot values affect not affect the the initialinitial coatingwere coating mechanicalthe same mechanical in the performance. 0% performance.and
Details
-
File Typepdf
-
Upload Time-
-
Content LanguagesEnglish
-
Upload UserAnonymous/Not logged-in
-
File Pages13 Page
-
File Size-