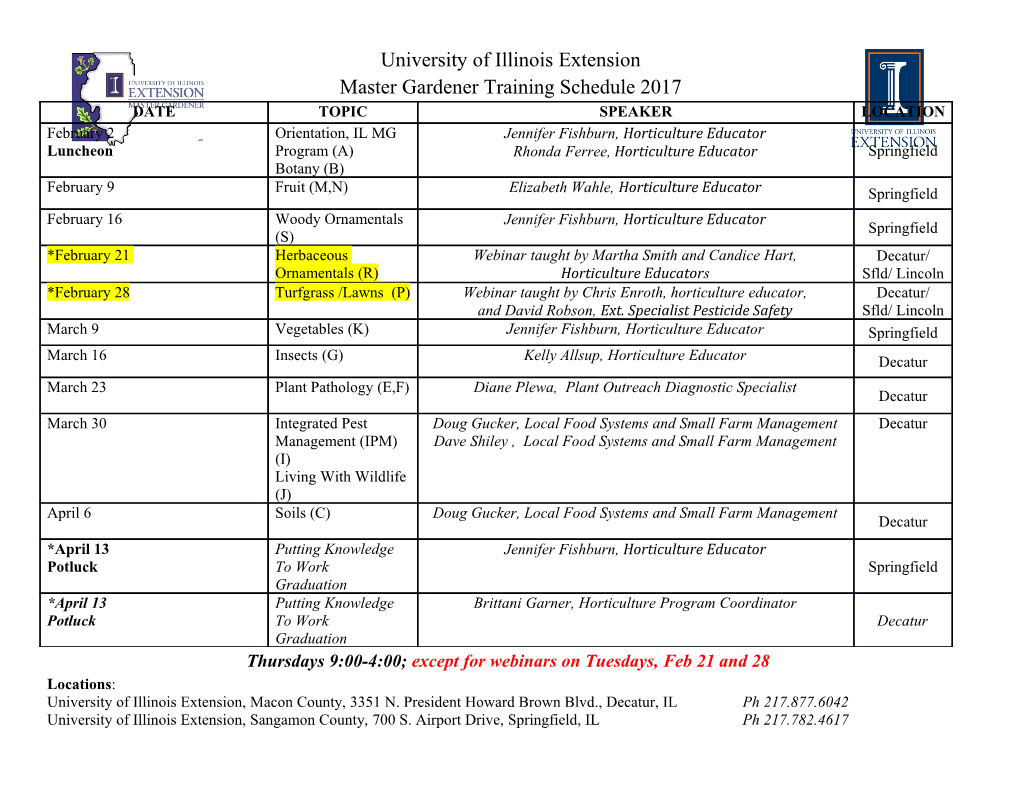
Operation and Maintenance Instructions /SOMETTM Low Speed Saw ©1992 BUEHLER LTD. Printed in U.S.A. r I I {})ecfaration of Conformity I ®A I Manufacturer: BUEHLER, Ltd. Of: 41 Waukegan Road Lake Bluff, Illinois 60044 I Declares the following product: /SOMET n.t LOW SPEED SAW I To be in accordance with EC Directive(s); Safety of Machinery: EMC Directive: I 89/392/EEC and 91/368/EEC and 93/44/EEC 89/336/EEC and 92/231/EEC according to the according to the following standards: following standards: EN 292 PART 1 1991 EN 50081-1: 1992 EN 292 PART 2 1991 EN 50082-1: 1992 I EN 60204 PART 1 1993 Position: Director of Engineering I Name: Chuck Motley I Signature: Date: 111197 Cliuc~9rtotfey I I I I I I This Manual is a custom generated document. It includes all revisions relative to this specific Buehler item as of the date shown below. I I MA111280-11 1113/99 I TABLE OF CONTENTS DESCRIPTION PAGE Warranty ....................................................................................................................................... 2 Unpacking ................................................... ................................................................................. 2 Assembly ......................................................................................................................................2 Installation .................................................................................................................................... 3 Location ...................... ................................................................ ..................................... 3 Electrical ......................................... ..... ............................................................................ 3 Blade Installation .............................................................................................................4 Lubrication .................................................................................................................................... 5 Operation ...................................................................................................................................... 6 Loading the Saw .............................................................................................................. 6 Adjustment of Cut-Off Switch Mechanism ....................................................................... 6 Micrometer Adjustment and Weight Selection ................................................................ 7 Cutting the Specimen ...................................................................................................... 7 Maintenance ..... ............ .......................... ....................................................................................... 9 Motor or Drive Belt Replacement ............................. ....................................................... 9 Micrometer Screw Adjustment .................................................................. ~ ..................... 11 Replacement or Exchange of Micrometers ..................................................................... 11 General Specifications ....................................................... .. ......... .................................. 12 Hot Cell or Glove Box Use ........................................................................................................... 12 Exploded Assembly Drawings ...................................................................................................... 13 Electrical Connection Drawing ........................................ ............................................................. 20 Packaging Drawing .................................................... ......................... .. ....................................... 21 Parts List .......................................................................... ............................................................ 22 Accessories and Supplies .....................................................................................· ....................... 24 ISOCUT ®Wafering Blades .............................................. .............................. .. ................ 26 Notes: ...................................................... .. ...................... ............................................................. 28 MA111280-11 1113199 ----- -- - ------ ---------------------------------------- OPERATION AND MAINTENANCE INSTRUCTIONS BUEHLER® ISOMET™ LOW SPEED SAW Warranty This unit is guaranteed against defective material and workmanship for a period of two (2) years from the date of receipt by customer. Warranty is void if inspection shows evidence of abuse, misuse or unauthorized repair. Warranty covers only replacement of defective materials. If, for any reason, this unit must be returned to our plant for warranty service, please apply for prior authorization with shipping instructions, and include the following information: Customer Purchase Order Number, Buehler Ltd. Invoice Number and Date, Serial Number, and reason for return. Unpacking Carefully unpack and check contents. If any components are missing or damaged, save the packing list and material and advise the carrier and Buehler®, Ltd. of the discrepancy. Assembly The ISOMErrM Low Speed Saw is shipped fully assembled except for a Diamond Wafering Blade and Dressing Stick which are packed separately in the same box. Three Chucks, Weights, Weight Shaft, Counter-Balance Weight, Balance Weight Shaft, two (2) Allen Wrenches, a Spanner Wrench, and an optional Chuck mounting screw are packed separately in the Lubricant Pan which is accessible via the door on the right panel. (See Accessories) 2 MA111280-11 1113/99 I Figure 1 Installation Location The ISOME"fTM is intended for bench-top placement. Select a convenient location with access to a grounded type electrical receptacle rated for voltage, hertz and phase indicated on the Specification Plate located at the base of the rear panel. Electrical Consult Specification Plate for proper voltage for the unit. All units are equipped with an IEC cord connector . Appropriate cord for country of use is supplied. 3 MA111280-11 1113/99 Blade Installation To install the Blade on the ISOMETTM perform the following steps: 1 Remove Thumb Screw, End Cap Bushing and Outer Flange from Drive Shaft. 2. Install blade on Drive Shaft against Inner Flange relieved surface. 3. Slip on Outer Flange and End Cap Bushing, then hand tighten Thumb Screw to complete installation. Waf ering Bl ade Drive Shaft Outer Flange Thumb Screw Figure 2 Note: Smaller flanges must be employed when the 11-1188 Chuck is used for thin sections, or the 11-1189 Chuck for 1" and 1 114" dia. specimens. If gang-sawing is desired, several Blades may be installed, with appropriate spacers, followed by installation of the Outer Flange, End Cap Bushing and Thumb Screw as previously described. Flanges provide support for the wafering blades. Failure to provide adequate flange support may result in curved cuts and damaged blades. Always select the maximum flange diameter commensurate with the size of the specimen to be cut. Note: Before reinstallation of a Wafering Blade, the End Cap Bushing, Screw and Flanges should be cleaned in a mild detergent solution to remove adherent particles from previous sawing. This will help prevent misalignment of Blade and resultant poor-quality cuts. New Wafering Blades, including the original equipment Blade, must be dressed before making sample cuts. Dressing removes normal smeared matrix metal and exposes the abrasive grain to assure free cutting. New Wafering Blades should be dressed several times and older Blades dressed as required by the properties of the sample material. When cutting metal samples it may be necessary to dress after each cut. 4 MA111280-11 11/3/99 To dress, position the Dressing Stick in the 11-1187 Saddle Chuck and make thin transverse cuts through the Dressing Stick, or use a 11-1196 ISOMETTM Dressing Chuck. (See Accessories) Use of this device permits dressing to be performed without removing a previously fixtured sample. CAUTION - Feeding the Dressing Stick or any sample materials manually into the Blade could result in damage to the Blade. Lubrication The ISOMETTM employs the "drag" principle of lubrication with the lubricant carried to the sample on the periphery of the Blade. ISOCUT® Fluid reduces cutting time and produces superior quality cuts. Its use promotes effective lubrication which allows the diamond particles to cut cleanly. It minimizes Blade loading by the formation of discrete chips and effects their clean release from the Blade and work surface. Fill the Lubricant Pan with 11-1193-032 ISOCUT® Fluid to a level that will immerse Blade approximately 1/4". ISOCUT® Fluid is best for most metals and many non-metals. When the lubricant becomes contaminated with sludge it should be discarded and replaced. To remove Lubricant Pan, lift off Door on right side of Saw, grasp Knob on Slide Lock, pull Slide Lock outward until lock disengages, lower the Lubricant Pan Tray and then swing it outward. This will swing the tray outside the case and permit removal and emptying of Lubricant Pan. Clean Pan and Specimen Basket thoroughly and replace in Tray. With Slide Lock still pulled out, swing Tray inward to stop. Press Slide Lock inward to stop and then, while maintaining light pressure on Slide Lock lift Tray upward until Slide Lock engages. Press Slide Lock tully in to secure Tray. Refill with fresh
Details
-
File Typepdf
-
Upload Time-
-
Content LanguagesEnglish
-
Upload UserAnonymous/Not logged-in
-
File Pages29 Page
-
File Size-