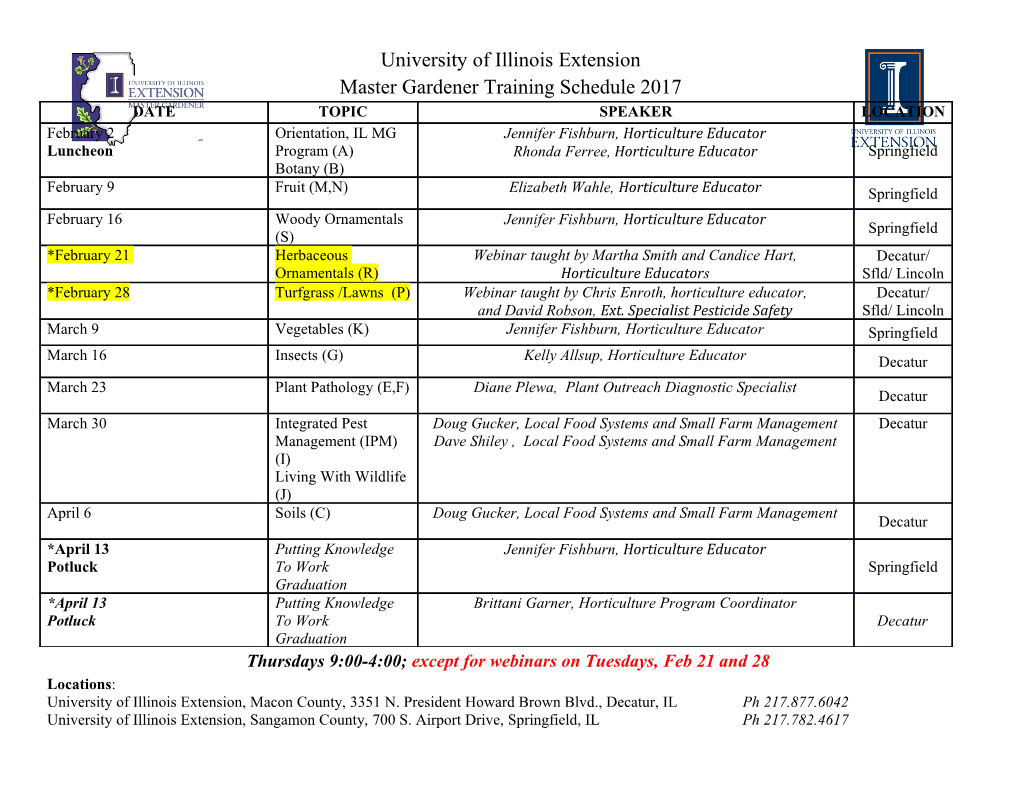
DESIGN OF A DATA ACQUISITION SYSTEM TO CONTROL AND MONITOR A VELOCITY PROBE IN A FLUID FLOW FIELD by ~lancy Lou Hen4ig Thesis submitted to the faculty of the Virginia Polytechnic Institute and State University in partial fulfillment of the requirements fo: the degree of MASTER OF SCIENCE r n Mechanical Engineering Approved: Dr. R.T. Stone, Chairman Dr. F ..J. Pierce Dr. S.8. Thomason December, 1982 Blacksburg, Virginia Acknowledgements There is no one beside thee, and no one above thee Thou standest alone as the nightingale sings! Yet my words that would praise thee are impotent things For none can express thee, though al I should approve thee EI i zabeth Barrett Browning I would I ike to thank Dr. R.T. Stone for the wealth of knowledge that he made avai I able to me, and for the trust and confidence that he bestowed upon me during the course of this project. I am very grateful to Dr. F.J. Pierce for his editorial efforts on this work, for his emotional support, and for his philosophical contributions to my perceptions of I ife. I am indebted to Mr. M.D. Harsh I I I for the technical support and the time that he has invested to Improve the quality of this project. His aid and encouragement wi I I never be forgotten. I wish to acknowledge Mr. J.R. Lucas for his excellent work on the fabrication of the Probe Control and Support Stand. I express my sincere appreciation to Mr. R.W. Wood,Jr. for the i I lustrations in this work, and for the pati~nce and love that carry me through difficult times. I am grateful to my parents for their unqualified support for me in my endeavors. They provide strength, security, and continuity in a chang(ng world. I thank all who have loved me in their hearts With thanks and love from mine. i i Table of Contents ~ Ac know I ed geme nts ••.•••. , ••• , ••• , • • . • • . • • • 1 1 Table of Contents ......................... iii Li st of Figures , .••.•.•.•.•.•••.•••••••••• v List of Tables •.••••••••••••••••••••••••.• vii I. Introduction .•.•.••....•..••.•••.•.•.•. , .•• I I. System Description ••.••....••..•..•••••••• 3 I I I. Extern a I Interfaces ....................... 9 External Input/Output Bus ••••••.•.••• 9 Computer Cable ....................... 15 STD Interface System •.•.••••••.•.•.•• 15 DE-80 Interface Box .•..••••••••..•••. 17 I nte rf ace Stations . • • • . • • • . • • • . • . • 2.0 Digital Inputs ....................... 38 S t e p p e r Mot o rs . • • . • • • • . • • . • . • • . • • • 4 5 Stepper Motor Interface Box •.•..••••• 48 IV. Program Description ....................... 53 MAIN Program ......................... 53 Primary Loop •...••....••...•.•. 55 Secondary Loop ................. 57 Tertiary Loop •.••...•..••••••.. 58 INITIAL Subprogram ................... 58 STEPPER Subprogram ................... 58 STEP/CMD Subprogram .................. 61 MEASURE Subprogram ................... 63 INPUT Subprogram ..................... 64 Nu I Ii ng Procedure .....................65 STORAGE Subprogram •.....•••••...•.... 74 RETRIEVE Subprogram .................. 74 V. Concluding Remarks ........................ 76 i i i Table of Contents (continued) References . • • 78 Appendices Appendix A - System Operating Procedures ............. 79 Appendix Al - STEP/CMD Program Description ........... 84 Appendix A2 - Terminal Program Procedure ............. 92 Appendix B - Program Descrip~ion 99 Appendix C - Troubleshooting and Warnings ............... 134 Appendix D - Glossary ............... 140 Vita 143 Abstract i v List of Figures Figure No. Title The Data Acquisition System 4 2 Block Diagram of the Data Acquisition System.................. 5 3 Velocity Probe Control and Support Stand . 7 ·4 Detailed Block Diagram of the External Interfaces .. .... .. .. ... .. 10 5 External Input/Output Signals on the Card Edge . 12 6 Conceptual Diagrams of 1/0 Operations . .. • . 14 7 The 1/0 Select Circuit ............. 16 8 Signals Available on the STD Bus in the DE-80 Interface Box 18 9 Connections Between the Computer Cable and STD Card Two ........;······ 19 10 Station Layout for STD Card One 21 I I Station Layout for STD Card Two 22 12 Si gna I Map in the Interface Station . • . 23 13 Sample Wiring Diagram for an Interface Station .................. 24 14 PPI Port Configuration for S tat i o n Z e ro . 2 6 15 PPI Port Configuration for Stations One Through Five • . 27 16 ·Signals Available at Station Zero .. 28 v List of Figures (continued) Figure No. Title Page 17 Signals Aval I able at Stations One th rough Five . • . 28 18 Address Select Circuit for Station Five . 29 19 Address Select Circuits for Stations Zero and One .•............ 30 20 Address Select Circuits for Stations Two and Three ....•......•.. 31 21 Address Select Circuits for Stations Four and Five ............. 32 22 Signal Assignments for the Digital Interfaces .................. 37 23 Location of Digital Signals in the DB-25 Connector on the DISA Voltmeter ..................... 42 24 Location of the Digital Signals on the Card Edge in the DANA Voltmeter ..•....................... 43 25 Location of Digital Signals on the DB-25 connector on the DATAMETRICS manometer ............. 44 26 Conceptua I Diagram of a Stepper Motor ..................... 46 27 Stepper Motor Excitation Sequence .• 47 28 Stepper Motor Pow~r Supply 49 29 Interface Circuit for One Stepper Motor Phase ................ ~I 30 Stepper Motor Interface Cable 52 31 Relationship between the MAIN Program and the Subprograms . 54 vi List of Figures (continued) Figure No. Title 32 General Flow.chart of the MAIN Program .•.•..•••.•.•...•.•..•• 56 33 Typical Voltage Data Distribution for an Odd Probe Response Function ..•.......•...•......•..... 66 34 Typical Voltage Data Distribution for an Even Probe Response Function •.•••..•..••••..•....•..... 67 35 Digital Filter - Spatial Domain 70 36 Digital filter - Frequency Domain ..................•......... 72 37 Probe Nul I Procedures .••........•.• 75 38 Deta i I ed Program FI owcha rt .•.•..... 100 39 STEPPER Subprogram •...........•.••.. 104 40 STEP/CMD Subprogram ..•••........•... 105 41 MEASURE Subprogram ..•..•..••....••.• 106 42 INPUT Subprogram ......•......•...•. 107 43 Signal Description of STD Control Signals ................••.. 139 44 Stepper Motor Cab I e Connector .•••... 137 vii I . INTRODUCTION A data acquisition system was designed to control the I inear and angular position of a velocity probe, and to record up to five voltage readings from thfs probe. This system replaces a similar manually operated system. The manual acquisition system includes hand control of the translational and rotational movement of a probe, and the visual estimation of fluctuating voltage signals using digital meters. The operation of this traverse system requires a period of from four to six hours for one traverse. Typically, multiple traverses are desired ' in a flow field so that manual operation can extend into several days of data acquisition. There is a potential for relative inconsistencies in the manual probe posi- tioning and acquisition process since operator techniques can conceivably change during the extensive hours of data ·acquisition. The automated data acquisition system uses two stepper motors to translate computer commands into translational or rotational probe movement. The heart of the system is the TRS-80, Model 111 microcomputer. The sys- tem in its current configuration is designed to acquire fluid velocity information during the vertical traverse of a velocity probe. The number of translational points to be used, and their positions are variables that are defined by the user. The velocity information provided by the probe is translated to digital voltages and re- corded by the computer. The direction of the fluid vel- ocity in the flow field at each point of translation is determined through a series of rotational .measurements. The vertical position, the angular position, and up to five voltage values are recorded at each data position. This computerized data acquisition system wi I I 2 relieve the experimenter from the tedious exercise of con- tinuously positioning ~he probe and recording data. ·Al- though it is recommended that the system be checked peri- odically, it wi 11 operate automatically, and require no user input after the initial start-up for each traverse. This automatic system also creates a more consistent ap- proach to al I aspects of the data acquisition process, and, hence, more consistency in the recorded data is ex- pected. The array of data resulting from one vertical tra- verse is stored on a floppy disk in a data file. This f i I e can be referenced by ana I ys is programs deve I oped on the TRS-80. The computer may a I so send the data f i I e to other larger systems, such as the IBM 370, using the ter- minal package discussed in Appendix A2. Existing data reduction software on the IBM 370 may then be used to process the recorded data. 11. SYSTEM DESCRIPTION ~ photograph of the automated data acquisition system is included in Fig. I A block diagram of the system elements is given in Fig. 2 The TRS-80, Model 111 computer, based upon the Z-80 microprocessor, is used. It contains forty-eight thousand bytes of programmable memory. In addition, there are two floppy disk drives that accom- modate five inch floppy disks, each with a storage ca- pacity of 184,000 bytes. The computer uses TRSDOS, the Radio Shack disk op- erating system. The traversing control program is written in the BASIC language [i]. The TRS-80 may also be programmed in Z-80 machine language, the language of the microprocessor.
Details
-
File Typepdf
-
Upload Time-
-
Content LanguagesEnglish
-
Upload UserAnonymous/Not logged-in
-
File Pages151 Page
-
File Size-