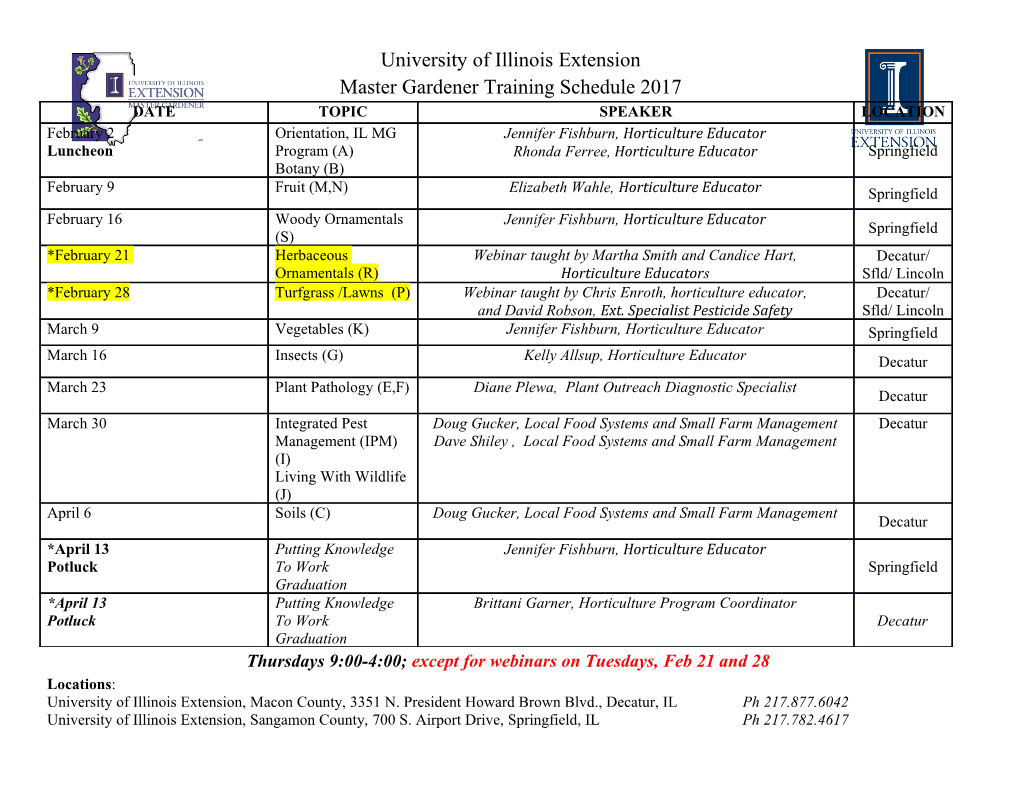
SCHRIFTEN DES INSTITUTS FÜR MIKROSTRUKTURTECHNIK AM KARLSRUHER INSTITUT FÜR TECHNOLOGIE (KIT) Band 25 25 TOBIAS MEIER Magnetoresisti ve and Thermoresisti ve Scanning Probe Microscopy with Applicati ons in Micro- and Nanotechnology Magnetoresisti ve and Thermoresisti ve Probe Scanning Microscopy and ve Thermoresisti Magnetoresisti T. MEIER T. Tobias Meier Magnetoresistive and Thermoresistive Scanning Probe Microscopy with Applications in Micro- and Nanotechnology Schriften des Instituts für Mikrostrukturtechnik am Karlsruher Institut für Technologie (KIT) Band 25 Hrsg. Institut für Mikrostrukturtechnik Eine Übersicht aller bisher in dieser Schriftenreihe erschienenen Bände finden Sie am Ende des Buchs. Magnetoresistive and Thermoresistive Scanning Probe Microscopy with Applications in Micro- and Nanotechnology von Tobias Meier Dissertation, Karlsruher Institut für Technologie (KIT) Fakultät für Maschinenbau Tag der mündlichen Prüfung: 22. Mai 2014 Hauptreferent: Prof. Dr. Volker Saile Korreferenten: PD Dr. Hendrik Hölscher, Junior-Prof. Dr. Fabian Pauly Impressum Karlsruher Institut für Technologie (KIT) KIT Scientific Publishing Straße am Forum 2 D-76131 Karlsruhe KIT Scientific Publishing is a registered trademark of Karlsruhe Institute of Technology. Reprint using the book cover is not allowed. www.ksp.kit.edu This document – excluding the cover – is licensed under the Creative Commons Attribution-Share Alike 3.0 DE License (CC BY-SA 3.0 DE): http://creativecommons.org/licenses/by-sa/3.0/de/ The cover page is licensed under the Creative Commons Attribution-No Derivatives 3.0 DE License (CC BY-ND 3.0 DE): http://creativecommons.org/licenses/by-nd/3.0/de/ Print on Demand 2014 ISSN 1869-5183 ISBN 978-3-7315-0253-1 DOI 10.5445/KSP/1000042497 Preface I would like to express my gratitude to the numerous friends, colleagues and institutions for the support and the inspiring discussions during the last years. Without their help, it would have been impossible to finish this thesis. Therefore, it is a pleasure for me to thank them for their contributions and I would like to point out a few for special recognition. First of all, I want to thank Prof. Dr. Volker Saile for the chance to write this thesis at the Institute of Microstructure Technology (IMT) at the Karlsruhe Institute of Technology (KIT) and his scientific and personal support for my work during this time. Furthermore, I like to acknowledge the great support of Prof. Dr. Juerg Leuthold and Prof. Dr. Uli Lemmer. Specifically, I wish to highlight the excellent support during this work by my supervisor PD Dr. Hendrik Hölscher. Due to both, his interpersonal and professional regard, it was a pleasure to discuss and tackle the exciting challenges on which this work is based. Furthermore, I’d like to thank the colleagues at Christian Albrechts Uni- versity Kiel, Ali Tavassolizadeh, Dr. Dirk Meyners and Prof. Dr. Eckhard Quandt, and at Bielefeld University, Dr. Karsten Rott and Prof. Dr. Gün- ter Reiss, who fabricated the magnetoresistive tunneling structures and incorporated them into AFM cantilevers. Without their continuously hard work, on fabricating AFM cantilevers, the results presented on magnetore- sistive self-sensing cantilevers would not have been possible. At this point, I acknowledge the financial support for this project from the Deutsche Forschungsgemeinschaft (DFG). Additionally, I want to thank Dr. Roland Gröger, Dr. Alexander Förste and Dr. Stefan Walheim from the Institute of Nanotechnology (INT) at the Karlsruhe Institute of Technology (KIT) i Preface for the fruitful discussions during the design and set up of the specialized instrument for the implementation of the magnetoresistive AFM cantilevers. I am very much indebted to Dr. Bernd Gotsmann of IBM Research - Zurich for inviting me to his laboratory and introducing me to the concept of scanning thermal microscopy. It was a great pleasure to work with him and exciting to be part of this highly innovative group. I further want to express special gratitude to Fabian Menges, who did an amazing job on setting up the scanning thermal microscope at the IBM labs. For funding my research period at IBM Research - Zurich, I would like to thank the Karlsruhe House of Young Scientists (KHYS). It is also a pleasure to thank my colleagues of the Nano- and Micoreplica- tion Group at the Institute of Microstructure Technology (IMT) for the good cooperation and working atmosphere during the processing of shape mem- ory polymers. I wish to express my gratitude to PD Dr. Matthias Worgull, Marc Schneider and Dr. Alexander Kolew for advice, technical help and most of all inspiring discussions and a helping hand whenever needed. In this regard, I would like to acknowledge the support of the Karlsruhe Nano Micro Facility (KNMF), a Helmholtz Research Infrastructure at Karlsruhe Institute of Technology (KIT). Additionally, I want to thank Paul Abaffy for the numerous hours at the scanning electron microscope. In addition, I wish to thank the entire workshop team at IMT and Andreas Deck from the workshop at the Institute of Applied Physics. At this point, I also want to thank my office mates Taleieh Rajabi, Christian Lay, Radwanul Siddique and Michael Röhrig - it was a pleasure working with you. It is also a pleasure to acknowledge fruitful discussions with Dr. Sven Schüle, Dr. Markus Simon, Dr. Zhenhao Zhang, Dr. Maryna Kavalenka, Dr. Julia Syurik, Senta Schauer, Richard Thelen, Kira Köhnle, Dr. Klaus Feit, Markus Heilig, Norbert Schneider, Oliver Krömer and Benjamin Leyrer at KIT. Outside KIT, I would like to thank Dr. Heike Riel, Dr. Peter Nirmalraj and Dr. Heiko Wolf at IBM Research - Zurich; Klaus Pross, Johannes ii Preface Kindt and Steve Minne of Bruker Nano Surfaces Division; Friedhelm Freiss, Stephan Vinzelberg, Amir Moshar and Ted DuPar of Asylum Research for inspiring discussions and their friendly welcome at their laboratories. Finally, I would like to thank my family, especially my parents and Nicole, for their understanding and loving support during the last years. Karlsruhe, April 2014 Tobias Meier iii Abstract In modern micro- and nanotechnology, knowledge from the macroscopic world has to be questioned whether it still applies at the micro- and nanoscale. Aiming for smaller structural feature sizes and smart usage of these new ma- terial properties can improve current devices and pioneer the technological platform for new applications. The key to this technology can be found in the ability to image samples on the nanoscale. This work presents approaches to extend limits of scanning probe microscopy techniques towards more versatile instruments. Integrated sensor concepts by magnetoresistive and thermoresistive sensing are presented. Furthermore, a fabrication method to design application-inspired micro- and nanostructures is introduced. To combine the advantages of high resolution scanning probe microscopy with a large field of view, a new atomic force microscope with a nested scanner design was developed. This unique microscope benefits from two independent scanners, one with a large range of 800×800µm2 and one with a scan range of 5×5µm2 for high spatial resolution. Additionally, the instrument is designed to be operated with both, a conventional beam deflection setup and self-sensing cantilevers based on magnetic tunneling junctions with magnetostrictive electrodes. This concept showed sufficient sensitivity to be used in atomic force microscopy and even outperformed specifically optimized piezoresistive and piezoelectric cantilevers. Utilizing thermoresistive cantilevers in scanning thermal microscopy, the heat flux between the tip of the cantilever and the sample was measured with high precision. This sensor concept enabled quantitative thermal con- ductance measurements of linear molecular chains as a function of their v Abstract chain length. Self-assembled monolayers of various linear alkanes were studied as a model system and showed signatures of phonon localization and interference. The switching properties of thermally triggered shape memory polymers were analyzed in micro- and nanoscale systems. These materials were introduced to the fabrication of molds for the replication of micro- and nanoscale components. Utilizing the shape memory effect for replication of micro- and nanostructures, allowed the fabrication of self-healing and demolding molds for the replication of micro- and nanostructures on curved surfaces. vi Kurzfassung In der modernen Mikro- und Nanotechnologie hängen Materialeigenschaf- ten nicht nur von deren Zusammensetzung ab, sondern auch stark von deren Größe und Form. Das Ziel mit immer kleineren Strukturelementen neue Materialeigenschaften intelligent zu nutzen, führt dabei nicht nur zur Verbes- serung gängiger Produkte, sondern kann den Weg zu neuen Anwendungen und Technologieplattformen bereiten. Die Fähigkeit, Proben auf dieser Grö- ßenskala abzubilden, öffnet dabei die Tür zu dieser Technologie. Diese Arbeit zeigt daher Wege auf, um die bereits große Familie der Rasterson- denmikroskope noch vielseitiger zu gestalten. Dabei wurde zunächst die Abtastfläche von typischerweise 100 × 100µm2 auf 800 × 800µm2 mit ei- nem Dual-Scanner System vergrößert. Das Dual-Scanner System verfügt zudem über einen unabhängigen 5 × 5µm2 Scanner für eine hohe lokale Auflösung. Zusätzlich wurde das Mikroskop für die gleichzeitige Nutzung eines konventionellen Lichtzeiger Detektors und dem Einsatz neuartiger selbst- detektierender Mikrofederbalken mit integrierten magnetischen Tunnelsen- soren ausgelegt. Diese
Details
-
File Typepdf
-
Upload Time-
-
Content LanguagesEnglish
-
Upload UserAnonymous/Not logged-in
-
File Pages192 Page
-
File Size-