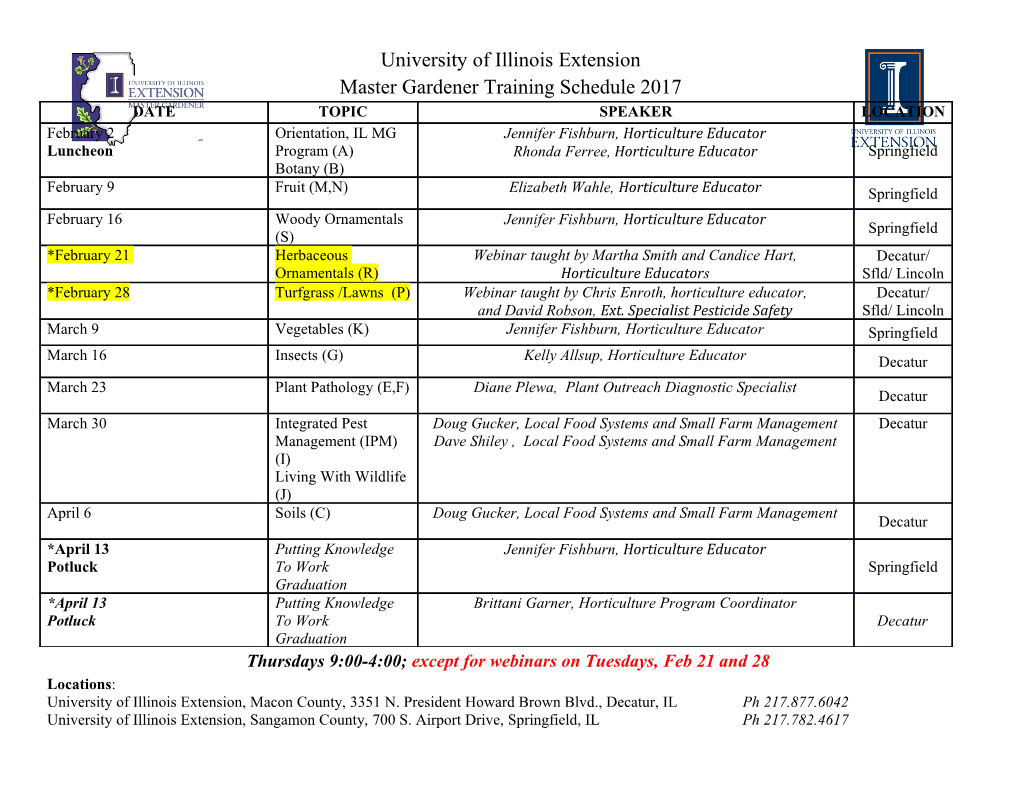
NATIONAL TECHNICAL UNIVERSITY OF ATHENS SCHOOL OF NAVAL ARCHITECTURE AND MARINE ENGINEERING LABORATORY OF MARINE ENGINEERING Diploma’s Thesis Smoke Emission Reduction of Marine Diesel Engines by Leading Part of the Exhaust Gas into Diesel Particulate Filter During Transient Loading Papoulias Fotis Professor Supervisor: N.P. Kyrtatos Athens, October 2014 Abstract Potential reduction of smoke emission of marine diesel engines is investigated through the installation of an exhaust bypass system featuring two diesel particulate filters in the Laboratory of Marine Engineering of the National Technical University of Athens. This system differs from the ones already in use in the automotive industry because it charges only during engine transient loading in order to avoid early filter contamination. The exhaust flow is controlled by the operation of two butterfly valves. When the engine is idle or operating in steady state the first valve is fully open and the exhaust gas flows through the main duct unfiltered. In case of engine transient loading, during which there is high smoke emission, the second valve gradually opens leading part of the exhaust gas into the filters. When it is almost fully open, the first one closes and the exhaust gas is being fully filtered until the engine operates in steadier conditions. Then, the valves are moved to their initial positions. The efficiency of the method, in terms of smoke emission reduction, is assessed by measuring the exhaust gas opacity after the filters. Furthermore, the differential pressure across the filters is measured, as well as the system back pressure, in order to estimate the soot load in the filters and its impact on the engine operation. The project includes the supervision of the construction and proper installation of the exhaust bypass system in the exhaust processing unit of the laboratory, the acquisition and mounting of all sensors, the installation of the necessary subsystems and the conduction of the experiments. In the context of this project, opacity measurements on a high speed passenger vessel are also carried out in order to evaluate the opacity sensor performance, as well as to observe the smoke emission from an engine operating in real conditions. In addition, a brief description of the radio – frequency soot sensing technology is performed in order to decide whether to use this or the state of the art differential pressure in order to estimate the soot load in the filters. The main objective is to develop a system that will reduce efficiently and in a safe way the smoke emission of diesel engines without interfering in their overall operation. Furthermore, additional issues must be considered so that the system will be suitable for retrofit in marine engines. i Acknowledgements First of all, I would like to express my gratitude to every person involved in this great project, beginning from the director of the laboratory and also my supervisor professor Mr. N. Kyrtatos, for the opportunity that he gave me to undertake this project and for all the necessary information and feedback, that he offered me, regarding my thesis subject. Moreover, I would like to give special thanks to Dr. G. Papalambrou and to the doctoral student S. Topaloglou, who were involved in this project from the early beginning providing me valuable help and support for the completion of this project. Without their daily presence this project would have never been fulfilled. Also special thanks to the technical staff of the laboratory, Mr. C. Sarris and Mr. G. Daliapes for their invaluable assistance regarding my familiarisation to the laboratory equipment and for providing me the necessary means to carry out my thesis. Finally, I would like to thank the doctoral students S. Glaros and N. Vrettakos as well as the undergraduate student L. Rizos for their advice and support that proved very helpful for the accomplishment of the project and the elaboration of this thesis. ii Contents Introduction ..................................................................................................................................... 1 Chapter 1: Project Overview ........................................................................................................... 2 1.1 General Background ........................................................................................................ 2 1.2 Problem Description ........................................................................................................ 4 1.3 Smoke Emission Abatement Methods ............................................................................ 7 1.4 Exhaust Bypass System .................................................................................................. 12 Chapter 2: Diesel Particulate Filter Technology ............................................................................ 14 2.1 The Particulate Filter ..................................................................................................... 14 2.2 DPF Regeneration Strategies ......................................................................................... 18 2.3 DPF System Design for Marine Applications ................................................................. 22 2.4 DPF Selection for the Exhaust Bypass System ............................................................... 25 Chapter 3: Exhaust Bypass System Overview ................................................................................ 28 3.1 System Description ........................................................................................................ 28 3.2 System Efficiency Evaluation ......................................................................................... 32 3.2.1 Smoke Emission Measurement ............................................................................. 32 3.2.2 The G1000 Smoke Density Monitor ...................................................................... 34 3.2.3 System Backpressure Measurement ..................................................................... 37 3.2.4 DPF Soot Load Estimation...................................................................................... 39 3.3 Exhaust Gas Flow Control .............................................................................................. 41 3.3.1 The SOMAS Butterfly Valves .................................................................................. 41 3.3.2 Exhaust Gas Flow Measurement ........................................................................... 46 3.4 Additional Measurements and Devices ......................................................................... 48 3.4.1 Temperature Measurements ................................................................................ 48 3.4.2 Isolating Amplifiers and Data Acquisition System ................................................. 50 Chapter 4: Exhaust Bypass System Installation ............................................................................. 52 4.1 Exhaust Bypass System Construction – Delivery - Assembly......................................... 52 4.2 Exhaust Bypass System Modifications ........................................................................... 58 4.3 Sensors Process Connection .......................................................................................... 60 4.4 Electrical Connections ................................................................................................... 65 4.5 Additional Tasks ............................................................................................................. 71 4.5.1 Air Supply Subsystem Installation ......................................................................... 71 4.5.2 Pipe Duct Insulation Installation ............................................................................ 72 iii Chapter 5: Opacity Measurements Onboard ................................................................................ 74 5.1 Introduction ................................................................................................................... 74 5.2 Ship Specifications ......................................................................................................... 74 5.3 Equipment Installation .................................................................................................. 77 5.4 Measurements Analysis................................................................................................. 79 5.5 Conclusion ..................................................................................................................... 83 Chapter 6: Experiments with Exhaust Bypass System ................................................................... 84 6.1 Preparation for the Experiments ................................................................................... 84 6.2 Results Analysis ............................................................................................................. 91 6.2.1 Caterpillar 3176B, Valves: Manual Handling ......................................................... 91 6.2.2 Caterpillar 3176B, Valves: Stateflow Control ........................................................ 96 6.2.3 MAN B&W Holeby L16/24, Valves: Manual Handling ......................................... 101 6.3 Conclusion ................................................................................................................... 105 Chapter 7: Conclusions - Recommendations .............................................................................
Details
-
File Typepdf
-
Upload Time-
-
Content LanguagesEnglish
-
Upload UserAnonymous/Not logged-in
-
File Pages181 Page
-
File Size-