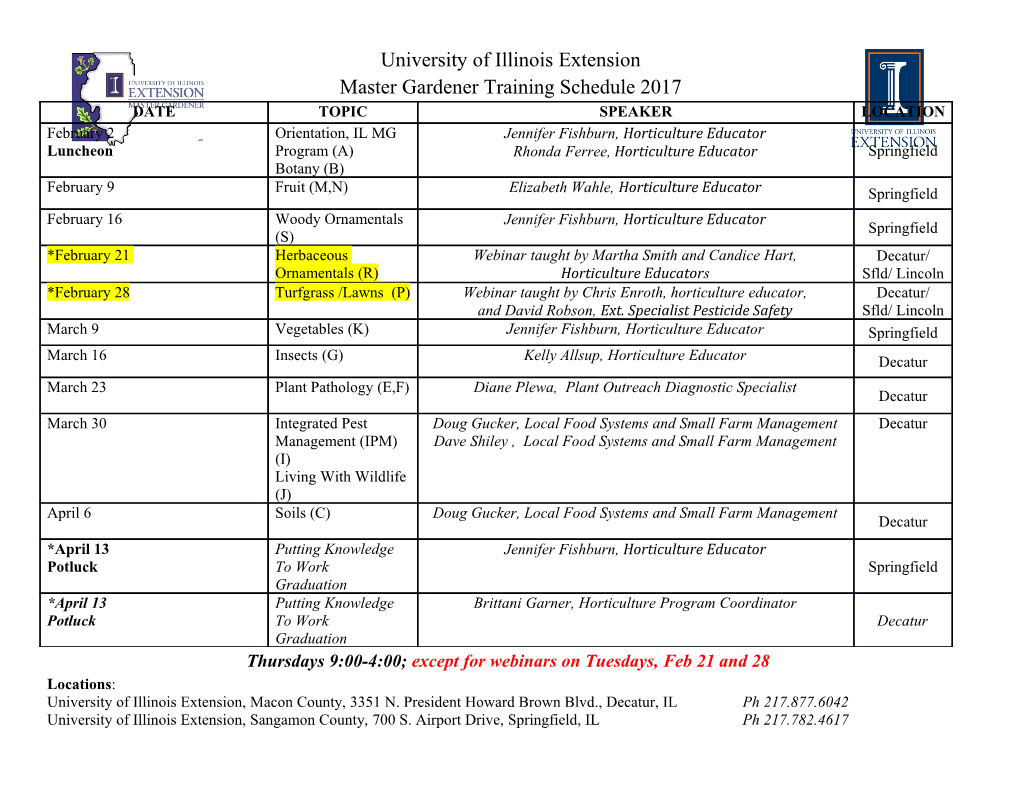
1999:185 MASTER'S THESIS Design and construction of a permeation measurement equipment Fredrik Jareman Civilingenjörsprogrammet Institutionen för Kemi och metallurgi Avdelningen för Kemisk teknologi 1999:185 • ISSN: 1402-1617 • ISRN: LTU-EX--99/185--SE Design and construction of a permeation measurement equipment Fredrik Jareman DEPARTMENT OF CHEMISTRY AND METALLURGICAL ENGINEERING DIVISION OF CHEMICAL TECHNOLOGY July 1999 Acknowledgements First of all I would sincerely thank my two supervisors PhD Derek Creaser and PhD Jonas Hedlund for their support when I was in need for help and inspiring discussions during the project. I also thank my examiner and future supervisor professor Johan Sterte for his acceptance of my total failure in keeping my budget. I am also grateful to PhD Derek Creaser for his help with the noble art of English writing, Tekn. lic. Peter Sedin for letting me borrow his private drilling machine during such a long time, M.Sc. Martin Kwasniewski for his cheerful words “Hey you got nothing left, this is done in fifteen minutes” when I was in a bad mood and for his friendship. Finally, my deepest thanks to my family for encouraging me to move up here to Luleå and start studying chemical engineering and their support during the years, to my love Pernilla for your support during this project. Summary This project started due to the need for a permeation test facility at the division of chemical technology at Luleå University of technology. The project covers design, equipment selection and construction of the test facility. A permeation measurement testing system was constructed consisting of several components, which is capable of making advanced measurements of the permeation characteristics on different gases and liquids. The system will be automated by a computer system once routine tests are started. The system contains three main components; one gas chromatograph one tubular split type furnace and a heated zone. The heated zone contains evaporating units and pressure regulating equipment. Quantitative gas analysis of the retentate and permeate will be performed with the gas chromatograph, in order to evaluate separation characteristics of the membrane. Several limitations had to be made regarding temperature, pressure and other operating parameters in order to find appropriate equipment and keep costs manageable. Within these limitations, all equipment was ordered and mounted together into the permeation test facility. Contents 1 Introduction...................................................................................................1 1.1 Purpose...................................................................................................1 1.2 Background.............................................................................................1 1.2.1 General description of zeolites, their structure and applications .........1 1.2.2 Thin zeolite films as membranes .......................................................2 1.2.3 Previous work at the division ...........................................................3 1.2.4 Permeation measurement experiments..............................................3 2. System description.........................................................................................5 2.1 Introduction............................................................................................5 2.2 Detailed descriptions of some of the components.....................................7 2.2.1 Furnace ............................................................................................7 2.2.2 Oven, heated zone ...........................................................................7 2.2.3 Gas chromatograph...........................................................................8 2.2.4 Back pressure regulators..................................................................11 2.2.5 Permeation cell...............................................................................12 2.2.6 Computer system ...........................................................................12 3 Design and construction ...............................................................................14 3.1 General considerations...........................................................................14 3.2 Explanation regarding choices of equipment ..........................................15 3.2.1 Mass flow controllers......................................................................15 3.2.2 Magnetic valves..............................................................................16 3.2.3 Gas Chromatograph .......................................................................16 3.2.4 Furnace ..........................................................................................17 3.2.5 Heated zone...................................................................................18 3.2.6 Pressure regulators..........................................................................18 3.2.7 Fluid pump ....................................................................................19 3.3 Calculations of necessary tubing lengths.................................................20 3.3.1 Equations and approximations ........................................................20 3.3.2 Results of calculated lengths ...........................................................23 4 Recommendations for future development and expansion ............................27 5 Conclusions..................................................................................................28 References ......................................................................................................29 1 Introduction 1.1 Purpose The purpose of this master thesis was to design and construct an automated laboratory system for permeation evaluation of zeolite membranes. I will share my experiences from this work and hopefully explain some of the pitfalls that occurred during the different stages in the design and construction of the laboratory system. 1.2 Background 1.2.1 General description of zeolites, their structure and applications Zeolites are a highly crystalline microporous material, with pore sizes of about 0.3 to 1.0 nm [1]. They consist of a network of connected SiO4 and AlO4 tetrahedra [2] with the silicon or aluminia atom in the centre. The connection between different tetrahedra is by shared oxygen atoms. This leads to the following general structural formula [1]: []()()⋅ M x'/ n AlO2 x' SiO2 y' wH 2O where the bracketed term is the crystallographic unit cell of the zeolite. The n denotes the valence of the cation present in order to make the unit cell electrically neutral, since the aluminia tetrahedron has a net charge of –1. The connected tetrahedra results in rings of oxygen atoms. These rings form the apertures to the channels inside the zeolite. Due to the fact that there may be 4, 5, 6, 8, 10 or 12 [1] oxygen atoms in the rings, there is a large range in possible aperture sizes. The ratio of Si/Al content present in a zeolite varies between different types of zeolites. The more Al present in the structure increases the acidic and hydrophilic properties of the zeolite. A zeolite with acidic sites is capable of interchanging protons and therefore it is suitable for catalytic applications. Due to this property zeolites have been used as catalyst in different process applications. 1 One of the mostly widely spread is the ZSM-5 cracking catalyst in the oil refining industry [1]. Zeolites have other different interesting properties. One of them is their molecular sieve property. A molecular sieve is a porous material capable of sorting different compounds by size and shape. 1.2.2 Thin zeolite films as membranes Due to their small pores, molecular sieve property and temperature stability, zeolites are of interest in several industrial applications where gas separation at an elevated temperature is desired. A practical example is production of styrene from ethyl-benzene, by catalytic dehydrogenation. With existing technology the process stream must be cooled down in order to separate the styrene from the unreacted ethylbenzene and hydrogen. With a thin zeolite film this would be done in one step by combining the membrane and the reactor i.e., hydrogen would be removed in situ from the reaction zone [3]. This combination would not only reduce the separation costs of the process, but it should also be possible to drive the reaction beyond its thermodynamic equilibrium and thus improve productivity. To obtain a high flux through the membrane, which increases its potential for use in industry, it is important that the film is ultra thin, i.e. less that 100 nm [4]. These ultra thin films have to be supported by another porous material such as alumina oxide, having pore sizes of 50 to 100 nm, to improve their mechanical strength. With these types of supported films a broad range of applications are possible. One was mentioned earlier, another is pure gas separation. Due to the broad range of crystal structures of zeolites there is a broad range of separation possibilities between molecules. This characteristic makes zeolite membranes interesting from an industrial point of view. The biggest challenge is to find a synthesis method, which is capable of producing membranes of sufficiently high quality. A high quality membrane would have a very thin zeolite film for high fluxes and be free of defects such as pinholes and cracks. 2 1.2.3 Previous work at the division The research group at
Details
-
File Typepdf
-
Upload Time-
-
Content LanguagesEnglish
-
Upload UserAnonymous/Not logged-in
-
File Pages34 Page
-
File Size-