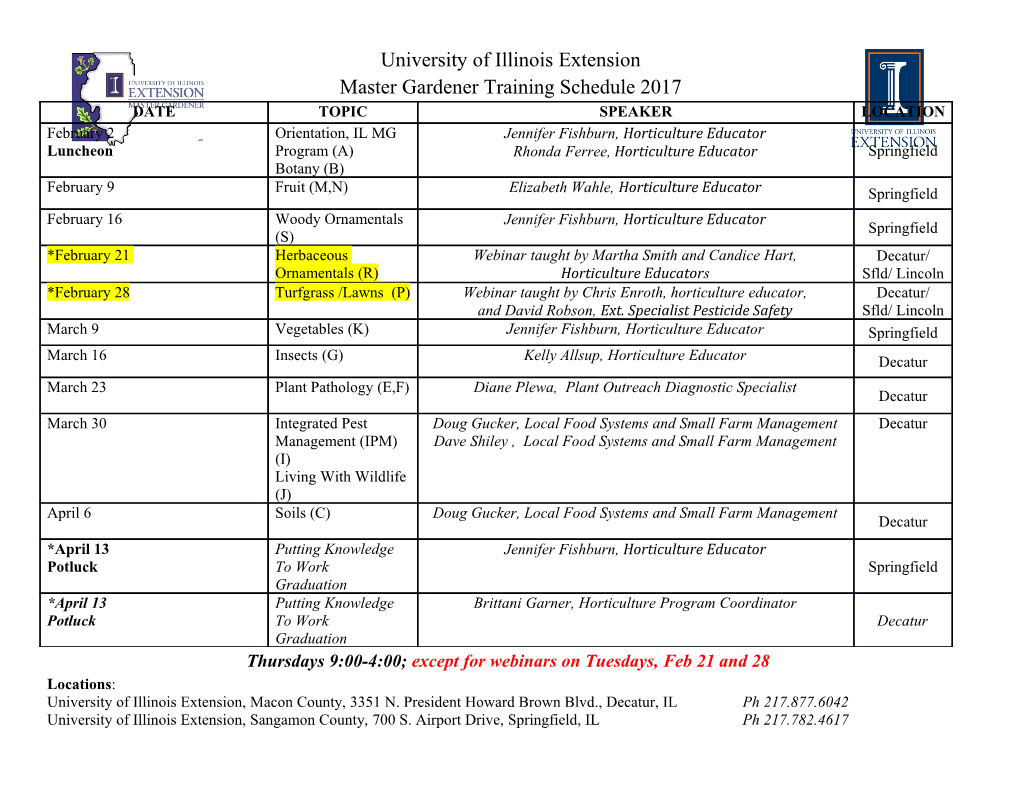
ARTICLE IN PRESS INTERNATIONALJOURNALOFHYDROGENENERGY33 (2008) 3847– 3855 Available at www.sciencedirect.com journal homepage: www.elsevier.com/locate/he Backfire prediction in a manifold injection hydrogen internal combustion engine Xing-hua Liua, Fu-shui Liua, Lei Zhoua,Ã, Bai-gang Suna, Harold. J. Schockb aSchool of Mechanical and Vehicular Engineering, Beijing Institute of Technology, Beijing 100081, China bEngine Research Laboratory, Michigan State University, East Lansing, MI, USA article info abstract Article history: Hydrogen internal combustion engine (H2ICE) easily occur inlet manifold backfire and Received 27 July 2007 other abnormal combustion phenomena because of the low ignition energy, wide Received in revised form flammability range and rapid combustion speed of hydrogen. In this paper, the effect of 26 April 2008 injection timing on mixture formation in a manifold injection H2ICE was studied in various Accepted 28 April 2008 engine speed and equivalence ratio by CFD simulation. It was concluded that H2ICE of Available online 16 June 2008 manifold injection have an limited injection end timing in order to prevent backfire in the inlet manifold. Finally, the limit of injection end timing of the H2ICE was proposed and Keywords: validated by engine experiment. Hydrogen internal combustion & 2008 International Association for Hydrogen Energy. Published by Elsevier Ltd. All rights engine (H2ICE) reserved. Backfire Injection timing CFD Simulation 1. Introduction 1.2. Literature review 1.1. Background 1.2.1. Experiment study on backfire in H2ICE In the experiments of the hydrogen engine, the problem of As a new type of internal combustion engine, the difference backfire and rapid rate of pressure rise were frequently between H2ICE and gasoline was chiefly induced by the experienced. A close study on hydrogen–oxygen combustion difference of physical features between these two types of mechanism is very important, primarily with an objective to fuels. Compared with gasoline, the advantages of hydrogen, assess how different it is from petroleum-based liquid fuels such as high flammability, low ignition energy, good homo- as to combustion. genous combustion, high octane number and high thermo- From the literature, the single greatest issue regarding dynamic efficiency, had been analyzed in most papers [1–3]. spark-ignited H2ICE combustion is backfire and/or pre-igni- However, because the ignition energy of hydrogen–air tion occurring as a lean fuel/air ratio approaches stoichio- mixtures is very small, the first obstacle regarding spark- metric, which limits the torque output of the engine [4]. ignited (SI) H2ICE combustion are backfire, pre-ignition and Backfire is the condition when the fresh charge of hydrogen is knocking; especially for a manifold injection H2ICE, the back ignited in intake ports. Pre-ignition is the condition when the fire is the first obstacle which should be overcome by a hydrogen charge is ignited after the intake valve closes and designer. before the spark plug fires in cylinder. ÃCorresponding author. Tel.: +86 10 68912516. E-mail address: [email protected] (L. Zhou). 0360-3199/$ - see front matter & 2008 International Association for Hydrogen Energy. Published by Elsevier Ltd. All rights reserved. doi:10.1016/j.ijhydene.2008.04.051 ARTICLE IN PRESS 3848 INTERNATIONAL JOURNAL OF HYDROGEN ENERGY 33 (2008) 3847– 3855 Nomenclature EVO exhaust valve open Phi equivalence ratio IVC intake valve close TDC top dead center (3601 CA in this paper) IVO intake valve open BDC bottom dead center EVC exhaust valve close The intake process is complicated considering the gas and in-cylinder with respect to different engine speeds and dynamics of the intake and exhaust, and so it is possible that equivalence ratios. We can obtain an optimal injection timing a rich pocket of hydrogen could also exist that would locally for avoiding backfire based on the analysis of CFD simulation. be the first to ignite especially in a manifold injection hydrogen engine. 1.2.2. Simulation study on backfire in H2ICE It has been suggested in the literature [5] that backfire can Johnson [8] uses the Kiva-3 V engine simulation code devel- be controlled by injecting the hydrogen only during the oped at Los Alamos National Laboratory with the standard forward flow of air into the cylinder during the intake stroke, eddy-turnover model to simulate a hydrogen engine at a fixed thus minimizing the fuel’s exposure to being heated or equivalence ratio and volumetric efficiency. The standard coming into contact with hot spots or hot oil ash/residual in model contains one free parameter that is adapted for the combustion chamber. hydrogen and held constant for varying ignition timing and Isadore and Frank [6] haddetailedanalysisoftheflamm- engine speed. The model is validated against the experiments ability limits of hydrogen–air mixture. They concluded that the reported in Ref. [9]. Fontana et al. [10] modified the Kiva-3 V lean limit occurs at lower concentration as the mixture code to simulate an SI engine fuelled with a hydrogen/ temperature increase with a linear relationship, while the gasoline mixture. They used a hybrid model where the global pressure effect appears to be small. They gave the lean limit up reaction rate is either given by the standard eddy-turnover to 400 1C (673.15 K) mixture temperature. Since this tempera- model or a weighed reaction rate based on two global reaction ture range is not enough to cover the ignition temperature in rate expressions, one for hydrogen combustion and one for engine condition, the lean limit line is extended up to 700 1C gasoline. They validated the model for gasoline operation and (973.15 K) and plotted in Fig. 1. Thus, concentration is the most calculated the effects of adding various hydrogen concentra- sensitive parameter for controlling hydrogen self-ignition and, tions to gasoline. GM company optimized the mixture of course, backfire. formation of the H2ICE [11] using CFD-simulation method It is necessary for developers to put up a close study for the and found the conclusion that injection timing should be hydrogen mixture formation both in the inlet and in-cylinder advanced with engine speed increasing, and the injection to avoid the backfire with respect to injection timing. Keck [7] duration should be completed before intake valves closed. reports measurements in an optically accessible engine, However, the objective of their study are the improvement of operated on propane as well as hydrogen, and uses a the output of the H2ICE. turbulent entrainment model to compare predicted trends In order to optimize the intake charge and mixture with experimentally observed trends. In fact, by means of the formation in H2ICE, a CFD simulation of injector locations 3D-CFD-simulation (full analysis of the fluid motion), it is and timing in different engine operation was conducted nowadays possible to gain a deep insight of the processes that by BWM [12], and two important conclusions were proposed: govern engine performance and emissions, and the 3D-CFD- (1) in order to avoid backfire, it is greatly important to select simulation represents the most sophisticated approach injector location and injection timing; (2) if the injection for the detailed numerical investigation on any fluid-dyna- timing is too early, it will let mixture flow back to manifold mical problem. Consequently, the CFD simulation is the best while intake valves nearly closing. As a result, delay the tools to demonstrate the mixture formation both of intake injection timing as much as possible, it can make part of air enter the cylinder to cool the hot pots first, and lower the possibility of backfire. Their studies may be more valuable if they had gave a recommendation or a range of hydrogen injection timing, and which is the focus of this paper. 1.3. Motivation and objective Frankly, the most recent efforts into H2ICE simulation focus on CFD calculation of DI engines which have nothing to do with the backfire. A team from TU Graz and BMW has reported CFD simulations of the mixing process in DI engines [13] and is now working on the CFD simulation of the combustion process [14]. Nevertheless, the DI H2ICE has a very complex structure of cylinder head and a huge cost for Fig. 1 – Influence of temperature on hydrogen lean production; so it is impractical to develop DI H2ICEs for flammability limit. automobiles in the near future. Actually, the hydrogen ARTICLE IN PRESS INTERNATIONAL JOURNAL OF HYDROGEN ENERGY 33 (2008) 3847– 3855 3849 powered cars produced by BMW and FORD were equipped with manifold injection H2ICE rather than DI H2ICE. Thus, it 2. Materials and methods is very important to discover the methods of avoiding the backfire in the manifolds for this type of H2ICE. 2.1. Approach Although we can get an in-cylinder image of mixture formation by experiment of optical-H2ICE, little information After an exhaustive study to identify the various causes of of intake ducts and ports can be obtained. In addition, it is backfire, it was clearly observed that the injection configura- difficult to make experiments of optical-H2ICE on high speed tion of the gasoline engine is not appropriate for a fuel such and load which is the operation of frequently backfire. as hydrogen which has combustion characteristics widely Furthermore, the bench experiments indicate that correct different from conventional petroleum fuels. The reason and injection timing is one of the key factors to avoid backfire. possible solve methods for backfire in manifold injection Consequently, it is necessary to explore an injection timing H2ICE is demonstrated in Table 1. range to avoid the backfire in H2ICE by CFD simulation, and As shown in Table 1, minimizing the hydrogen residual in we will discuss it in the following text. the manifold after the intake valve closure is the way to lower the backfire possibility.
Details
-
File Typepdf
-
Upload Time-
-
Content LanguagesEnglish
-
Upload UserAnonymous/Not logged-in
-
File Pages9 Page
-
File Size-