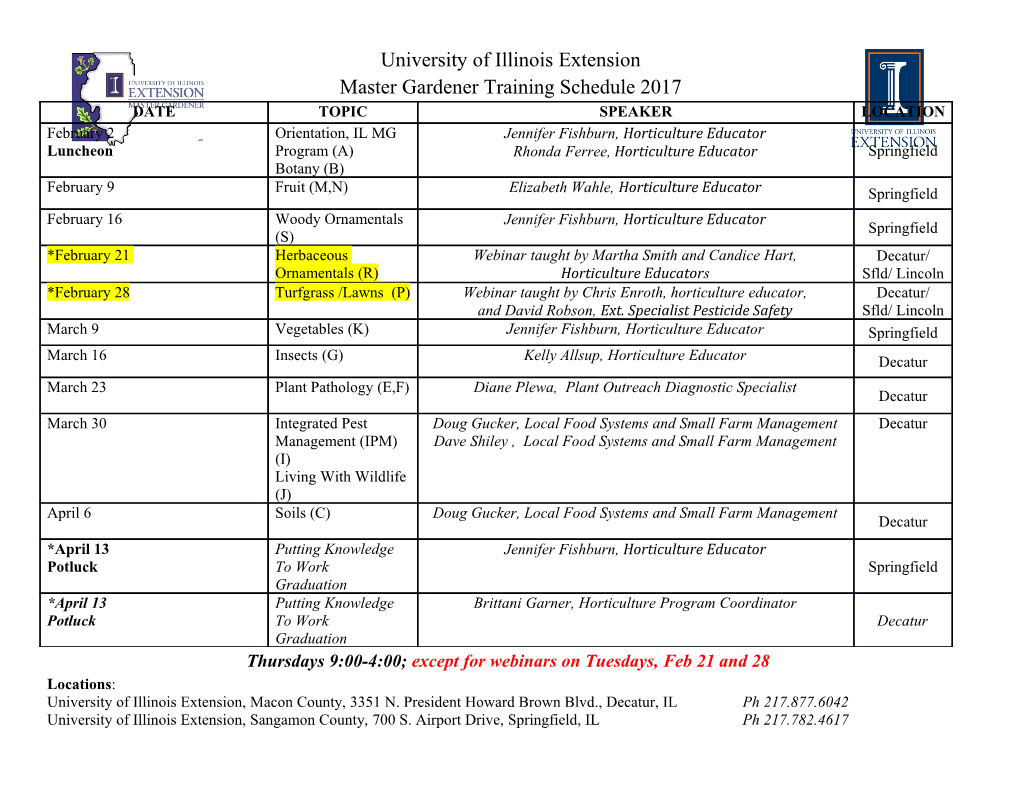
Europäisches Patentamt *EP001398493A1* (19) European Patent Office Office européen des brevets (11) EP 1 398 493 A1 (12) EUROPEAN PATENT APPLICATION (43) Date of publication: (51) Int Cl.7: F02K 1/15, F02K 1/76 17.03.2004 Bulletin 2004/12 (21) Application number: 03255630.0 (22) Date of filing: 09.09.2003 (84) Designated Contracting States: (72) Inventor: McKay, Richard John AT BE BG CH CY CZ DE DK EE ES FI FR GB GR Brewood Staffordshire ST19 8DX (GB) HU IE IT LI LU MC NL PT RO SE SI SK TR Designated Extension States: (74) Representative: Carpenter, David AL LT LV MK MARKS & CLERK, Alpha Tower, (30) Priority: 12.09.2002 GB 0221108 Suffolk Street Queensway Birmingham B1 1TT (GB) (71) Applicant: Goodrich Actuation Systems Ltd Luton, Bedfordshire LU1 3LU (GB) (54) Thrust reverser for a jet engine and hydraulic actuator (57) A thrust reverser assembly comprising at least device (16), said one side of the device being a high one thrust reverser element (12, 13) which, during nor- pressure side during operation of the device in a thrust mal use in association with a jet engine, is movable be- reverser element deploy mode to displace said element tween a stowed position and a deployed position and is from its stowed position, a second port (24) through so arranged as to experience an assisting load during which hydraulic fluid is displaced from a low pressure movement of the element from the stowed position to- side of the device (16) during operation in said deploy wards the deployed position, a source (28) of hydraulic mode, and a return line (25a, 25b, 25c) through which fluid under pressure, and, a double-acting hydraulic pis- hydraulic fluid displaced from said low pressure side of ton and cylinder device (16) for moving said element said device is returned to said high pressure side of said (12, 13) between said stowed and deployed positions, device in addition to said fluid supply from said pressure said hydraulic piston and cylinder device (16) having a source (28), and, a check valve (27) in said return line first port (23) through which hydraulic fluid under pres- preventing flow of hydraulic fluid from said high pressure sure from said source (28) is admitted to one side of said side to said low pressure side of said device (16). EP 1 398 493 A1 Printed by Jouve, 75001 PARIS (FR) 1 EP 1 398 493 A1 2 Description Disclosure of Invention Technical Field [0005] In accordance with the present invention there is provided a thrust reverser assembly comprising at [0001] This invention relates to a thrust reverser as- 5 least one thrust reverser element which, during normal sembly for an aircraft jet engine, particularly a gas tur- use in association with a jet engine, is movable between bine engine, and relates also to an hydraulic actuating a stowed position and a deployed position and is so ar- system for the thrust reverser The invention is con- ranged as to experience an assisting load during move- cerned with thrust reversers of the kind which are so ment of the element from the stowed position towards constructed as to experience an assisting force when 10 the deployed position, a source of hydraulic fluid under being moved from a stowed position to a deployed po- pressure, and, a double-acting hydraulic piston and cyl- sition, and relate particularly, but not exclusively, to inder device for moving said element between said thrust reversers of the so called "Bucket" type. stowed and deployed positions, said hydraulic piston and cylinder device having a first port through which hy- Background Art 15 draulic fluid under pressure from said source is admitted to one side of said device, said one side of the device [0002] United States patent 5392991 discloses a being a high pressure side during operation of the de- thrust reverser of the bucket-type and it can be seen, vice in a thrust reverser element deploy mode, to dis- from US patent 5392991 that as the thrust reverser is place said element from its stowed position, a second deployed from a fully stowed position a point is quickly 20 port through which hydraulic fluid is displaced from a low reached at which the forward edges of the thrust revers- pressure side of the device during operation in said de- er shells or elements project into the air stream passing ploy mode, a return line through which hydraulic fluid over the engine, and thus are urged by the air stream to displaced from said low pressure side of said device is move towards their fully deployed position. However, it returned to said high pressure side of said device in ad- can also be seen that as the shells approach their fully 25 dition to said fluid supply from said pressure source, deployed position they extend into the jet of exhaust and, a check valve in said return line preventing flow of gasses flowing from the exhaust nozzle of the engine hydraulic fluid from said high pressure side to said low and the load imposed by the engine exhaust flow op- pressure side of said device. poses the movement of the shells to their fully deployed [0006] Preferably said return line communicates with position. Generally the force applied by the jet exhaust 30 a low pressure line which receives excess displaced hy- flow will exceed the force applied by the air flow around draulic fluid not returned from said low pressure side to the engine as the deployed position is approached. said high pressure side of said device. Thus during deployment the shells will need to be driven [0007] Preferably a flow restrictor controls the rate of from their fully stowed position to the point at which the discharge of hydraulic fluid from said low pressure side air flow assists, and then at the end of the deploying 35 of said device so as to control the speed of movement movement the shells will also need to be driven against of said element at least during its assisting load phase the action of the exhaust flow to reach the fully deployed of deployment. position. [0008] Desirably said flow restrictor is positioned in [0003] While the invention is described herein in rela- said return line. tion to a bucket-type thrust reverser it is to be under- 40 [0009] Alternatively, where excess hydraulic fluid is stood that the invention can be applied to any thrust re- displaced from said low pressure side of said device verser configuration in which there is an assisting load then said flow restrictor controls the rate at which said on the thrust reverser element or elements during de- excess hydraulic fluid flows in said low pressure line. ployment of the thrust reverser from its fully stowed po- [0010] Advantageously a further flow restrictor is pro- sition to its fully deployed position. 45 vided to control the flow rate of hydraulic fluid from said [0004] Thrust reversers typically are deployed by hy- high pressure source to the high pressure side of said draulic piston/cylinder actuators which generally, be- device. cause of the loads involved, are of relatively high volume [0011] Preferably said device is operated in a retract- and thus require a large capacity high pressure supply. ing mode to cause deployment of said thrust reverser The high pressure supply is derived from one or more 50 element. hydraulic pumps, and naturally the size of the pump or [0012] The invention further resides in an hydraulic pumps is determined by the flow requirements of the hy- system for a thrust reverser assembly as defined above. draulic actuator of the thrust reverser. It is an object of the present invention to provide a thrust reverser as- Brief Description of the Drawings sembly, and an hydraulic actuator system, in which the 55 volume of high pressure fluid required by the actuators [0013] In the accompanying drawings Figures 1 and is reduced and thus the size of the hydraulic supply 2 are diagrammatic views illustrating the exhaust nozzle pump or pumps is minimised. of a gas turbine engine, or similar jet engine, and show- 2 3 EP 1 398 493 A1 4 ing the thrust reverser elements of the engine respec- flow around the exterior of the nozzle assembly 11 and tively in their stowed, and fully deployed positions, the effect of the airflow hitting the under surfaces of both [0014] Figure 3 is a diagrammatic representation of elements 12, 13 will be to generate an assisting load on part of an hydraulic system of a thrust reverser assembly the elements 12, 13 driving them towards their fully de- in accordance with a first example of the present inven- 5 ployed positions. There is however a forceful flow of gas tion, from the exhaust nozzle and thus as the elements 12, [0015] Figure 4 is a view similar to Figure 3 of a mod- 13 approach their fully deployed position they will start ification of the hydraulic system of the assembly. to intersect the high speed gas flow from the exhaust [0016] Figure 5 is a more detailed hydraulic circuit di- nozzle and there will be a progressively increasing force agram of the thrust reverser assembly of Figure 4, and 10 upon the elements 12, 13 derived from the exhaust gas illustrating the control valves of the hydraulic system of flow, tending to drive the elements 12, 13 back towards the assembly in the positions which they occupy during their stowed position. Before full deployment occurs a deployment of the thrust reverser elements of the en- position is reached at which the air flow and gas flow gine, and, forces acting on the elements 12, 13 are in balance, and [0017] Figure 6 is a view similar to Figure 5 but show- 15 hydraulic force from the hydraulic actuating system of ing the valves in the position which they occupy during the thrust reverser assembly is needed to drive the ele- stowing movement of the thrust reverser elements.
Details
-
File Typepdf
-
Upload Time-
-
Content LanguagesEnglish
-
Upload UserAnonymous/Not logged-in
-
File Pages12 Page
-
File Size-