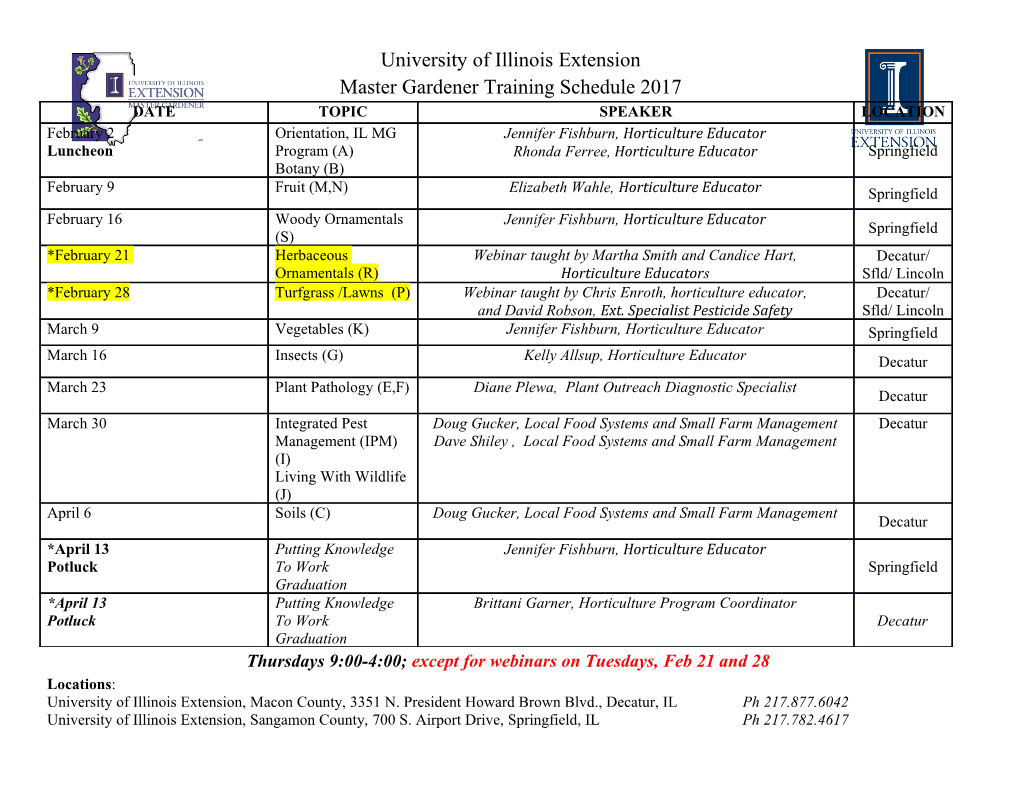
International Pipeline Conference — Volume 1 ASME 1996 IPC1996-1845 ASSESSMENT OF LONG CORROSION GROOVES IN LINE PIPE Duane S. Cronin K. Andrew Roberts Roy J. Pick Downloaded from http://asmedigitalcollection.asme.org/IPC/proceedings-pdf/IPC1996/40207/401/2506643/401_1.pdf by guest on 25 September 2021 Department of Mechanical Engineering University of Waterloo Waterloo, Ontario Canada ABSTRACT method and compared the results to reported experiments. Due to coating disbondment long corrosion grooves can develop in line pipe. For simple corrosion geometries current methods of EXPERIMENTAL DATA assessing the residual strength of the pipe are adequate but conservative, particularly if only the nominal material strength is Measured burst pressures of pipe with various corrosion geometries considered. In the case of long corrosion grooves which contain pits have been tabulated from a number of sources by Vieth and Kiefher the application of current assessment procedures can lead to a [4], Table 1 presents data from Vieth and Kiefher [4] for corrosion variation in the degree of conservatism, depending on the importance geometries that can be approximated by longitudinal grooves. These applied to the pitting. This paper reviews existing methods of results are labeled with the prefix KV and include the corrosion assessing long corrosion and describes the result of a finite element depth, length and a brief description. study of pits within long corrosion grooves. The authors have also completed tests on 3 sections of 24 inch pipe that suffered corrosion damage due to disbonded polyolefin tape. INTRODUCTION The results are shown in Table 1 and labeled with the prefix RL. For these tests, material properties were determined from tensile tests on Various pipelines, coated with polyolefin tapes, have experienced straightened circumferentially oriented coupons removed from the corrosion damage due to disbondment of the tape. Disbondment and pipe. sagging or wrinkling of the tape can lead to the trapping of water between the pipe and tape. The resulting corrosion often has a \ EFFECT OF THE CIRCUMFERENTIAL EXTENT OF longitudinal orientation due to the orientation of the wrinkles in the CORROSION tape. There have been various methods developed to evaluate the significance of this corrosion: the general approaches of ASME Most assessment procedures neglect the circumferential extent of B31G [1], CSA Z662 Clause 10.10.6 and RSTRENG [2] and the the corrosion, assuming burst to be controlled by the area of metal specific approach of Mok, Pick, Glover and Hoff [3], With the loss in the longitudinal and radial directions. To confirm this exception of RSTRENG these assessment procedures approximate assumption for long defects the finite element method was used to long corrosion as flat bottomed grooves. If the depth of the corrosion model pipe with infinite length longitudinal grooves of various varies or there is pitting, the depth of the groove is normally assumed depths and circumferential widths. The finite element model (shown to be the depth of the deepest pit. This leads to a conservative in Figure 1) was a circumferential section subject to plain strain estimation of the burst pressure of the corroded pipe. boundary conditions in the longitudinal direction. A description of RSTRENG will allow the geometry of the groove to be considered. the finite element code and failure criterion is presented later. However as will be shown, RSTRENG tends to minimize the effect Longitudinal defects in X52, 864 mm diameter, 7.1 mm wall pipe of individual pits whereas experiments show that burst normally were modeled using the finite element method. Burst pressures of originates in the deepest pit. Thus RSTRENG produces an long flat bottomed defects ranging in depth from 20% to 80% of the inconsistent factor of conservatism with different geometries. wall thickness and 23 mm to ISO mm in circumferential width were The authors have investigated the various assessment procedures, calculated. The results, shown in Table 2, indicate that the calculated considered a number of specific geometries using the finite element burst pressure decreased as the defect depth increased, but remained Copyright © 1996 by ASME constant with varying defect widths. flat bottom groove as the maximum depth of the pits in the groove. In summary, the circumferential width of longitudinal grooves does This will be a very conservative assumption if there are regions of not have a significant influence on the burst pressure of the pipe and local deep corrosion within long shallow defects. can be neglected for flat bottomed defects. The exceptions will be Table 3 compares the B31G predicted safe pressure with the actual when the groove is very narrow and the behavior is crack like and burst pressure. Predictions vary from 20% to 68% of the actual when the groove width is small compared to pits within the groove. burst pressure (average 49%) using the B31G procedure to evaluate Based on the assumption that the circumferential dimension has no longitudinal corrosion. If this B31G prediction of burst pressure is effect on the failure pressure, the pipe can be considered to be of below the operating pressure no further assessment is required. reduced thickness equal to the corrosion ligament thickness as in However due to the conservatism of the B31G assessment procedure B31G. it is possible that some safe pipe may fail this assessment procedure. In this case other assessment procedures developed specifically for ASSESSMENT PROCEDURES longitudinal grooves may be used. In most jurisdictions the B31G assessment procedure with Downloaded from http://asmedigitalcollection.asme.org/IPC/proceedings-pdf/IPC1996/40207/401/2506643/401_1.pdf by guest on 25 September 2021 variations is regulated as the assessment procedure. In Canada CSA Mok. Pick. Glover and Hoff [3] Z662, Clause 10.10.6 also allows an Engineering Critical Assessment Mok et al developed a model to predict the behavior of line pipe using other established procedures or analysis techniques. Therefore with long defects in various orientations (spiral corrosion). This it is assumed that the initial assessment of corroded pipe with long model was developed from burst tests on pipe with long flat bottomed corrosion grooves will be undertaken using the B31G or CSA Z662 machined defects in spiral and longitudinal orientations. Vieth and procedure. If this assessment procedure indicates an acceptable burst Kiefiier [4] have included the results for longitudinal defects in their pressure no further assessment is required. If the predicted burst database as KV97 ,KV98 , KV119 and KV120 as listed in Table 1. pressure is not acceptable it may indicate the pipe is unsafe or that the The equation developed by Mok et al to describe the strength of assessment procedure is overly conservative and an Engineering longitudinally oriented defects is shown in equation 4. Critical Assessment is more applicable. P = 1.5 P * |l - i (4) B31G Assessment B31-G was developed from a database of full size tests of corroded pipe. A semi-empirical formula was developed from this data which relates the failure pressure to the flow stress of the pipe material and where: to the size of the defect for different pipe geometries. These P = predicted burst pressure of pipe with defect equations have since been supported by additional full scale testing. “ = predicted burst pressure of plain pipe B31G models short defects as parabolas, but for long defects with P a length greater than a minimum Length given by: , . 4 'J e t t ... with P* being approximated by: Limn = — *------- (1) 0.893 P ' = SMYS — (5) D The defects are considered to be flat bottomed. The maximum safe pressure is described by: This is similar to the B31G formula except a factor of 1.5 is used (compared to a factor of 1.1 in B31G), based on consideration of the d P' = 1.1 P * 1 (2) strain hardening behavior of a series of typical pipeline steels. t Table 3 shows the ratio of the Mok et al predictions of burst pressure to the actual pressure. The Mok et al equation predicts burst and P* is given by: pressures between 27% and 92%'(with an average of 67%) of the actual burst pressure. In summary this assessment procedure is, on average, more P ’ = SMYS — (3) accurate than B31G, but like B31G makes use of the deepest point D in the corrosion as the depth of the flat bottomed corrosion groove. This leads to a conservative prediction of the burst pressure of the pipe. If this is not acceptable a more accurate assessment procedure In this case the length is not considered and can be infinite. For this should be attempted. study lengths exceeding Lmin will be considered infinite The assumption that the flow stress is 1.1 times the SMYS leads to RSTRENG a high degree of conservatism. Flow stress approximations based on The RSTRENG assessment procedure developed by Kiefner and the actual yield stress such as the yield stress plus 69 MPa are more Vieth [2] allows the use of a more complete description of the appropriate. longitudinal geometry of the corrosion compared to B31G and Mok For defects longer than Lmin B31-G approximates the depth of the etal.. Kiefner and Vieth recognized that the main sources of conservatism confirmed by the stress distribution through the pipe wall in the pipe in B31G were the assumed value of the flow stress and the away from the defect which approached that of plain pipe. The simplification of the corrosion geometry. RSTRENG redefines the model was not allowed to contract or expand longitudinally to create flow stress as the yield stress + 69 MPa and uses the actual corrosion a condition of plane strain in this direction. This simulates a buried geometry to describe the defect. An “effective area” technique is pipe in which longitudinal expansion and contraction is restricted by contained within the RSTRENG code that makes use of the variation the soil.
Details
-
File Typepdf
-
Upload Time-
-
Content LanguagesEnglish
-
Upload UserAnonymous/Not logged-in
-
File Pages8 Page
-
File Size-