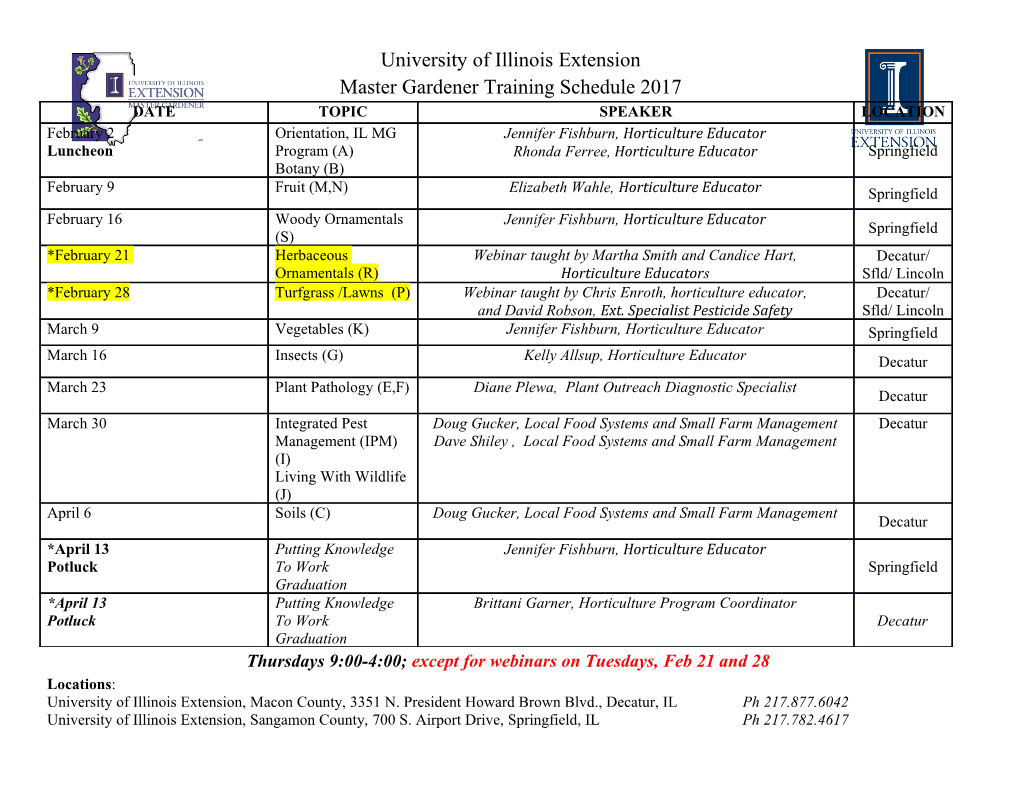
United States Patent (19) 11) 4,140,747 Sadan 45) Feb. 20, 1979 (54) PROCESS FOR THE PRODUCTION OF 3,498,744 3/1970 Frint et al. ....................... 423/206 T POTASSUM CHLORIDE AND 3,498,745 3/1970 Nylander .. ... 423/184 MAGNESUM CHILORDE FROM 3,644,102 2/1972 Svanoe ..... ... 23/302 CARNALL TE 3,852,044 12/1974 Neitzel et al. .......................... 23/302 3,967,930 7/1976 Sadan ........ 23/302 R (75) Inventor: Abraham Sadan, Herzelia Pituach, 4,039,617 8/1977 Kuo ...................................... 423/186 Israel Primary Examiner-O. R. Vertiz 73) Assignee: Israel Chemicals Ltd., Tel-Aviv, Assistant Examiner-Wayne A. Langel Israel Attorney, Agent, or Firm-Robert J. Koch (21) Appl. No.: 844,136 (57) ABSTRACT (22 Filed: Oct. 20, 1977 The present invention relates to a process for the pro duction of potassium chloride and of magnesium chlo (30) Foreign Application Priority Data ride hexahydrate (bischofite) from carnallite or from Nov. 9, 1976 (IL) Israel ........................................ 50873 carnallite containing sodium chloride. 51) Int. C.’........................... C01D 3/08; C01F 5/30 The process comprises heating carnallite at a tempera 52 U.S. C. .................................... 423/163; 423/179; ture of between above 70' C. and above 167.5' C., in the 423/2O3 presence of added water at the above former tempera 58 Field of Search ............... 423/158, 184, 163, 197, ture or without added water (but preventing evapora 423/179, 203; 23/297, 298,302 R, 304 tion of water) at the above latter temperature. Solid potassium chloride is then separated. In the residual 56 References Cited brine, carnallite is precipitated by evaporation or by U.S. PATENT DOCUMENTS lowering the temperature, and it is recycled to the start 1,304,097 5/1919 Reeve.........m 423/197 ing stage. The residual solution consists essentially of 1,757,592 6/1930 Schleicher .... ... 423/304 magnesium chloride which is recovered as bischofite, 2,479,001 8/1949 Burke et al. ........................... 23/304 2,758,912 8/1956 Dancy .................................. 423/163 11 Claims, 2 Drawing Figures aaaawaaz M72 / WS777A/6 VaSSEL ALZ/76/47 fow VASSEL seaaean/WG MASSAL M% 4. a/ Miyaza-64(6/sca/74774) U.S. Patent Feb. 20, 1979 Sheet 1 of 2 4,140,747 €/V/7CO2 7376933771 U.S. Patent Feb. 20, 1979 Sheet 2 of 2 4,140,747 /YO//tx/2///7737 7379957/1 4,140,747 2 than 1 percent of potassium chloride and about 46.1% PROCESS FOR THE PRODUCTION OF magnesium chloride and consists substantially of bis POTASSUM CHILORDE AND MAGNESUM chofite, i.e. MgCl2.6H2O. This may be processed by CHLORIDE FROM CARNALL TE conventional means to yield prilled magnesium chloride hexahydrate, magnesia or magnesium metal. It is clear The present invention relates to a novel process for that the process of the invention results in two main the production of potassium chloride and of magnesium valuable products: potassium chloride and magnesium chloride hexahydrate (bischoffite) from carnallite chloride which are marketable products. (KC.MgCl2.GH2O), and from mixtures of carnallite When the starting carnallite material contains sodium with some halite (sodium chloride). More particularly O chloride, as is the case with material obtained from the the present invention relates to a novel process charac Dead Sea, the sodium chloride precipitates with the terized in that the need to evaporate large quantities of potassium chloride and it can be separated by conven water is eliminated, and thus energy expenditure and tional processes such as flotation or hot leaching. When overall expenses are substantially reduced. coarse carnallite is used as starting material, it is possible Conventional processes are summarized in the article: 15 to elutriate the fine potassium chloride from the coarser Carnallite: The Other Potash Ore, Phosphorus & Potas sodium chloride. A further possibility is the separation sium, 84, July/August 1976, published by the British of the halite from the carnallite prior to processing by Sulphur Corporation Ltd. gravity separation as the specific gravity of halite and Hitherto carnallite is used in some parts of the world carnallite are 2.16 and 1.6 respectively, and that of the for the production of potassium chloride. The conven 20 brine is about 1.34. tional process comprises decomposing carnallite with According to another embodiment the process can water at substantially ambient temperature so as to crys also be effected with carnallite, possibly containing tallize potassium chloride, while the magnesium chlo some halite, at temperatures of above 70 C., in the ride is obtained as solution of about 25 to 26% concen presence of some additional water. The higher the tem tration by weight, which is separated. This solution 25 perature, the lower is the quantity of water which is contains generally about 3.3% potassium chloride and required to be added. For example, it is possible to some sodium chloride, which is generally present in the decompose the carnallite at a temperature of 105 C., starting material. The solution, which contains about adding per 1156 kg. carnallite, containing also 116 kg. 17% of the initial content of potassium chloride of the sodium chloride, an amount of 463 kg. water. At 70 C., carnallite, is subsequently evaporated to recover such 30 the amount of water to be added should be 585 kg. for potassium chloride and magnesium chloride solution. a complete decomposition of the same carnallite. The The evaporation is quite expensive and requires either amounts of water required to be added are compiled the use of fuel or the application of solar energy, where according to the solublities data of the system: magne suitable conditions exist. sium chloride - potassium chloride - sodium chlo It is an object of the present invention to provide a 35 ride. Above 167.5 C., no water has to be added at all, simple process for the production of potassium chloride as the water of crystallization of the carnalite are suffi and of magnesium chloride hexahydrate (bischoffite) cient to obtain the adequate melt. There is thus obtained from carnallite. It is another object of the present inven a slurry of sylvinite in a solution of carnallite. The solids tion to provide a process for the production of potas are separated and the resulting solution is evaporated at sium chloride and of magnesium chloride which greatly about 120° C. to give a slurry of carnallite and a melt of reduces or eliminates the quantity of water to be evapo bischoffite. The carnallite is recirculated to the decom rated, and thus requires less fuel than in the conven position vessel, and the bischoffite is processed to result tional process. in any desired magnesium product. The sylvinite is In its general aspect the process comprises dissolution separated by conventional means to give potassium of the carnallite components (possibly together with 45 chloride and sodium chloride. halite, if such is present in the starting material) in its A person skilled in the art will select the proper em water of crystallization or preferably together with a bodiment, according to the available facilities and com small amount of additional water, so that at a tempera modities. ture of at least 70 C., the carnallite will be decomposed. FIG. 1 of the enclosed drawings is a block diagram According to a preferred embodiment the carnallite 50 illustrating one embodiment of the process according to is used as such, and in this case it is heated to a tempera the present invention. Carnallite is fed via conduits 1 ture of above 167.5 C. in a closed vessel - which and 2 to the melting vessel A where it is heated to above avoids evaporation of water - thus resulting in a de 167.5° C. The carnallite contains some halite (NaCl), composition of said mineral in its water of crystalliza and in the vessel, there is obtained a slurry of sylvinite tion, producing a solid potassium chloride possibly to 55 and a solution of carnallite. The slurry and solution are gether with sodium chloride, (sylvinite) and a hot brine. passed via conduit 3 to the elutriation vessel B where It is possible to separate the solid potassium chloride the fine potassium chloride is elutriated from the from the solid sodium chloride by elutriation due to the coarser sodium chloride, the sodium chloride is passed difference in particle size. The hot brine contains about via conduit 4 to vessel C, from where it is removed via 8.2% potassium chloride and about 42.3% magnesium 6 to the outside. Part of the mixture is recycled through chloride. This hot brine is cooled, for example, by flash stream 7 to the elutriation vessel B. The potassium chlo evaporation, to about 115° C. so as to crystallize out the ride resulting from the vessel B is conveyed through potassium chloride in the form of carnallite which is conduit 5 to the centrifuge D and removed via conduit separated and returned to the carnallite feed. The cool 8. The hot solution is passed via conduit 9 to the cooling ing of the hot brine can also be carried out by direct 65 vessel E where the temperature is reduced to about contact with the cold carnallite feed, thus obtaining also 115.7 C. The solution is further conveyed via conduct a preheating of the entering carnallite. The solution 10 to the vessel F from where the separated carnallite is from which the carnallite was removed contains less recirculated to the vessel A via conduit 2 while the 4,140,747 3 4. bischoffite is removed via conduit 11 to provide a melt 24.41; MgCl2: 31.12, H2O: 35.38 was heated to 170° C. of bischoffite.
Details
-
File Typepdf
-
Upload Time-
-
Content LanguagesEnglish
-
Upload UserAnonymous/Not logged-in
-
File Pages6 Page
-
File Size-