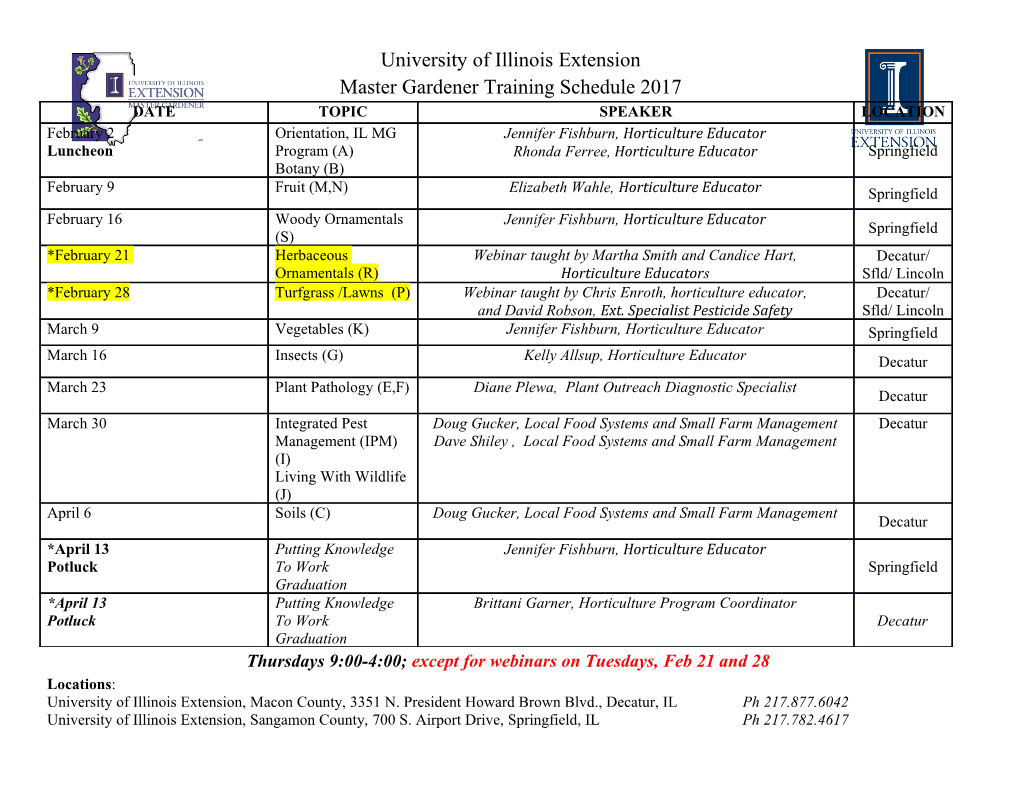
Communications in Information and Systems Volume 16, Number 3, 127–146, 2016 Solid deformation by material point method Yuntao Jiang, Tao Yang, and Jian Chang Solid materials are responsible for many interesting phenomena. There are various types of them, such as deformable objects and granular materials. In this paper, we present an MPM based frame- work to simulate the wide range of solid materials. In this frame- work, solid mechanics is based on the elastoplastic model follow- ing small deformation theory. We use von Mises criterion for de- formable objects, and the Drucker-Prager model with non- associated plastic flow rules for granular materials. As a result, we can simulate different kinds of deformation of deformable objects and sloping failure for granular materials. 1. Introduction Solid materials exist everywhere in our daily life, and are responsible for many interesting phenomena. Deformable objects, such as chewing gum, toothpaste, and bread dough, undergo elastic and plastic deformation when pressed or stretched. Another kind of solid materials are granular materials, including many kinds of geomaterials such as sand, soil and rubbles, consist of numerous grains colliding and sliding against each other. The numerical simulation of these different materials has been a problem of long standing interest and challenge. There have been many research on the simulation of deformation objects, either mesh-based methods like Finite Element Method (FEM) or meshless methods like Smoothed Hydrodynamic Particle (SPH) and Material Point Method (MPM). As for granular materials, given the extremely large number of grains in realistic scenes, it’s not practical to simulate individual grain as a Lagrangian particle. Thus the continuum based approaches like SPH or MPM are better choices. Since we want to build a unified framework to simulate different kinds of materials, SPH and MPM approach seems to be the best choice. Here we choose the MPM approach, because the hybrid of Lagrangian particles and Eulerian grids brings us a more stable performance. 127 128 Y. Jiang, T. Yang, and J. Chang In engineering field, deformable objects and granular materials can both be described as elastoplastic materials, and they share the same elastic model when the deformation remains in the elastic range. Their behavior under plastic deformation, however, correspond with different constitutive models. We use the linear model for elastic deformation for all solid materials, and use different yield criterion for the plastic deformation of different materials, Von Mises criterion for deformable objects[17], and Drucker-Prager model with non-associated flow rule for granular materials[1]. In this work, we follow the small deformation theory to compute the strain in the materials. This approach has been applied widely in SPH based simulations in engineering field, due to its simple mathematical form while remaining as a good approximation to the real physical process. We also show the constitutive models which have been applied in SPH framework can be easily adapted to MPM framework and still work well. Besides, we adopt the APIC method [7] to transfer physical quantities between grid and particles, which preserves the linear and angular momentum and results in an ignorable dissipation rate. 2. Related work Both SPH and MPM use a Lagrangian particle representation of materials, and they share very similar discretizations of physical equations. So here we first briefly introduce some SPH based works, and then some MPM based works. Mesh-based methods such as FEM, mass-string method, and Eulerian grid based method are beyond the scope, so are not discussed here. 2.1. SPH simulation In engineering field, SPH was first applied to simulate elastic solid materials by Libersky and Petschek [9]. Gray et al. [6] extended this early work with a method for overcoming the tensile instability, which could otherwise lead to numerical fracture. These works are based on the small deformation theory, and the strain in solid materials is updated additively with velocity gradient. To simulate different plastic materials, different yield criterions are used. Cleary et al. [4] used Von Mises plasticity and linear isotropic hardening to simulate elastoplastic deformation of deformable objects. Bui et al. [3] implemented the Drucker-Prager model with associated and non-associated plastic flow rules to simulate large deformation and post-failure of granular materials, and An et al. [1] extended this work to 3D cases. Solid deformation by material point method 129 In computer graphics, SPH has been widely used to simulate fluids([10], [12]), while it has also been recognized as a very potential method to sim- ulate solid materials. A common choice is to directly compute the strain of solid materials by comparing the current shape of the solid materials with a reference shape, which is the original shape of the object without any force exerted on it. M¨uller et al. [11] proposed a particle-based method for elastic, plastic and melting solid materials. They use the SPH method to compute the mass, density and volume of phyxels, and use Green-Saint-Venant strain to determine the stress tensor. To approximate the Jacobian of the deforma- tion vector field, a Moving Least Squares approach is employed. Solenthaler et al. [13] replaced the MLS approach with an SPH method, which can han- dle coarsely sampled and coplanar particle configurations. Becker et al. [2] extended their work with a corotational approach to correctly handle ro- tations. The methods using the reference shape can maintain the original shape well, but face additional difficulties when handling extremely large deformations and topological changes. Yan et al. [18] presented an SPH approach to uniformly handle the inter- action between elastoplastic solid and multiple fluids. Their approach follows the works in engineering field, and updates the strain with velocity gradi- ent. Here we also follow this idea, and adapt the solid part to our MPM framework. 2.2. MPM simulation MPM [16] has been used to simulate a wide range of solid materials in the past two decades, but is only applied in computer graphics in recent years. Stomakin et al. [14] first introduced MPM into graphics for simulating snow, using an elastoplastic constitutive model. Their framework is based on the finite deformation theory, and an energy related with deformation gradient tensor is used to derive the shear force. Following this work, they introduced a novel MPM method for heat transport, melting and solidifying materials[15]. Jiang et al. [7] tuned the model in [14] to simulate granular materials. Later Kl´ar et al. [8] introduced the Drucker-Prager plastic flow model into MPM to simulate sand dynamics, and Daviet et al. [5] presented a semi- implicit scheme for granular materials. Our MPM method is similar to the works mentioned above, but here we follow the small deformation theory, and adopt the constitutive model which has been used in the engineering field, especially in SPH based works. 130 Y. Jiang, T. Yang, and J. Chang Figure 1: The elastic and the elastoplastic bunny. We show that MPM based method is equally flexible and more stable than SPH for these applications. The grid/particle tranfer in MPM typically follows the method used in PIC or FLIP, or a weighted combination of both. While the tranfer in PIC suffers from the loss in angular momentum, the transfer in FLIP brings more noise into the system and makes it unstable. Jiang et al. [7] resolved this problem by coming up with the APIC method, which greatly increases the stability while still keeps a very low dissipation rate. This has been widely applied in the following MPM based works([8],[5], etc), and we also follow this method in our work. 3. Solid mechanics 3.1. Deformable objects The motion of solid materials obeys conservation of mass and conservation of momentum. Since the conservation of mass is naturally preserved by the particle representation, we here only focus on conservation of momentum Dv 1 (1) = ∇·σ + g Dt ρ where v is the velocity, ρ is the density, g is the gravity, and σ is the Cauchy stress tensor determined by the constitutive model of solid materials. 3.2. Linear elastic model In this section we briefly introduce the elastic constitutive model used by all the solid materials in our framework, and leave the plasticity to Section 3.1. Solid deformation by material point method 131 The stress tensor σ can be divided into two parts (2) σ = −P I + s where −P I is called the volumetric stress tensor, and s is the deviatoric stress tensor. P is in fact the hydrostatic pressure. These two parts have the following relations 1 (3) P = − Tr(σ) 3 (4) s = σ + P I where Tr(·)isthetraceoperator.Thevolumetricstresstensordescribesthe volume change of the deformed body, while the deviatoric part describes pure shear deformation. To calculate the stress tensor σ, we need a pair of tensors related with the velocity gradient 1 ˙ = (∇v + ∇vT ) 2 1 (5) ω = (∇v −∇vT ) 2 where ˙ is the strain rate tensor and ω is the Jaumannn rotation tensor. The first describes the rate of change of the strain tensor, while the second is used to correct the stress tensor when rotation happens. According to the Hookie’s law, s is updated with the strain rate tensor 1 (6) s˙ =2G ˙ − Tr(˙)I 3 where G is the shear modulus. The pressure P can be computed either with the equation of state (EOS), or with the volumetric change according to the strain rate tensor. Here we choose the later approach, (7) P˙ = −KTr(˙) where K is the bulk modulus. 132 Y. Jiang, T. Yang, and J. Chang Considering the effect of the rotation, the final equation for updating the stress tensor σ is 1 (8) σ˙ =2G ˙ − Tr(˙)I + KTr(˙)I + ωσ − σω.
Details
-
File Typepdf
-
Upload Time-
-
Content LanguagesEnglish
-
Upload UserAnonymous/Not logged-in
-
File Pages20 Page
-
File Size-