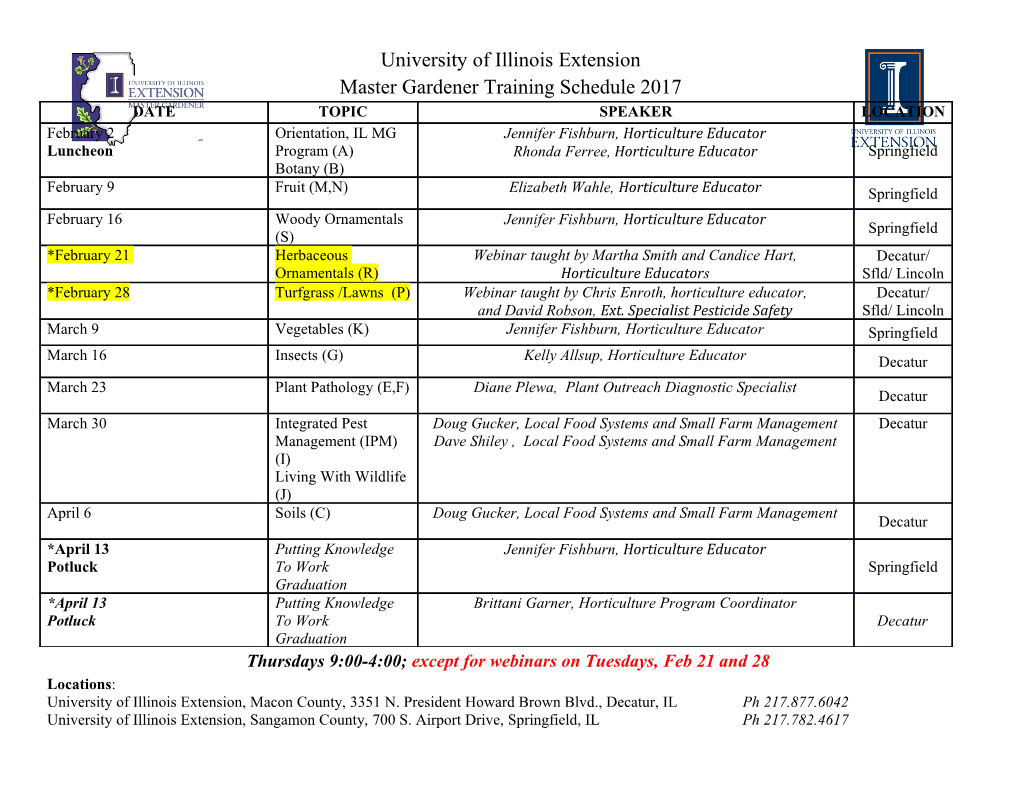
Low adhesion and sanders AUTHORS INTRODUCTION WHY IS LOW ADHESION IMPORTANT TO THE RAILWAY? Andrew Lightoller is a This paper will introduce the concept of low Chartered Mechanical adhesion between train wheel and rail, including Low adhesion can cause safety incidents (such Engineer, working for why it is so important to the railway, and will as Signals Passed At Danger, or SPADs) and DB ESG, a rolling stock show how sand is used to improve low adhesion significant performance issues (such as station consultancy. Andrew braking performance. Using sand is not a new overruns or delays). In low adhesion, train drivers started his career in concept, indeed steam trains were using sand for will naturally drive more cautiously; perhaps the rail industry as a traction purposes over 100 years ago. However, resulting in a lower maximum speed between graduate engineer at by increasing sand delivery it is possible to deliver stations and braking early and gently. There are Bombardier where consistent train braking performance regardless also issues with traction, particularly affecting he took over as Brakes engineer on the of the underlying adhesion conditions. Solving freight trains with limited motored axles. Classic project. After various experience the braking issue builds driver confidence in poor Each year, approximately 350,000 delay minutes including a six month placement at Chiltern adhesion conditions and opens the door to using are attributed to low adhesion. The direct impact depot commissioning 168s and EU testing sand in traction to achieve higher performance. of low adhesion is estimated to cost the GB of aluminium foam, Andrew moved to Atkins railway industry and wider society £345m per as a Brakes & Pneumatics Engineer in 2001. This paper describes how the braking year. The cost is made up of delay compensation, In 2014, Andrew moved to DB ESG after performance of different sanding configurations as well as the costs to mitigate low adhesion their acquisition of WSPER and works as a was quantified in a real railway environment, and (including rail head cleaning) and the operational Principal Mechanical Engineer involved with how an innovative new analysis methodology and reputational damage which occurs when WSPER, brake testing and other general was developed (since wheel/rail adhesion cannot train reliability and punctuality are degraded. Low consultancy work. be measured directly, the ‘Reference Adhesion’ adhesion issues are also a significant barrier to provides a method of inferring effective adhesion maximising future network capacity increases, Liam Purcell, CEng during a brake event). since predictable and reliable braking is a key FICE FPWI requirement for running trains closer together. INTRODUCING LOW ADHESION Liam is currently AVAILABLE MITIGATIONS working as a Principal In order to accelerate or decelerate normally, Consultant at Ricardo railway vehicles rely on adhesion between steel Although low adhesion exists mainly on the Rail, and leads the wheels and rail. A typical ‘step 2’ service brake rail (the permanent way engineer’s domain), it Intelligent Infrastructure demand (representing a requested deceleration of primarily affects the rolling stock (the rolling stock team. Liam is a 0.6m/s2 or 6%g) requires a coefficient of adhesion engineer’s domain). There are several types of Chartered Civil Engineer and Fellow of the between wheel and rail of µ ≥ 0.06. Table 1 shows available mitigations against low adhesion: ICE and PWI, with sixteen years’ experience a range of typical braking demands, however in the railway industry. please note that some trains have different brake • infrastructure-based mitigations include rates and/or more granular control. vegetation management (to reduce After initially joining AEA Technology contaminant getting on to the rails in the first Rail /DeltaRail as a graduate in 2003, he For the majority of the year, this level of wheel/ place) and rail head treatments (to clean the worked as a track consultant focussing on rail adhesion is readily available. However, each contaminant off the rails). vehicle-track interaction and derailment autumn, deciduous trees shed their leaves with investigation. Liam joined Lloyd’s Register some being crushed under the pressure of train • rolling stock mitigations include sanders (the Rail (now Ricardo Rail) in 2012 to specialise wheels, bonding to the rail to produce a very hard subject of this paper), as well as braking in wheel-rail adhesion, asset management and smooth layer. When combined with moisture, systems independent of wheel/rail adhesion and independent assurance of infrastructure the resulting coefficient of adhesion between (magnetic or eddy-current track brakes). projects. wheel and rail can be as low as µ = 0.01; six times There are also potential future technologies lower than that required to sustain normal braking. being evaluated, including using high- During braking, if the demanded adhesion powered lasers or plasma arcs to burn exceeds the available adhesion, the train wheels contaminant off the rails, or using frozen start to rotate more slowly than the actual train’s carbon dioxide to freeze the leaf film and speed; the wheels are starting to slide. With a blow it clear of the track. pneumatically actuated friction braking system, the Wheel Slide Protection (WSP) system will This paper focusses on enhancing the use of intervene to control the slide before any wheel sanders. Since sanders already have a history of damage occurs. in service use on the railway, the technology is available now and the benefits are proven. Sand This is generally done on an axle-by-axle basis is also relatively inexpensive. by rapidly venting pneumatic pressure in the brake cylinders, thus removing the braking force INTRODUCING SAND (AND and allowing the wheel speed to increase back SANDERS) to true train speed. Some slide is beneficial as it can create heat, drying and scrubbing the track, Sand, as shown in image 1, has been used on improving adhesion for the following axles. This the railway for almost as long as railways have effect, known as wheelset conditioning, tends to existed; historically steam locomotive drivers work best at improving medium levels of adhesion could open a valve to activate steam-powered - however it is less beneficial at very low adhesion sanders to aid traction. On a modern train, the levels. WSP system controls the sander (automatic sanding) - although the driver often has a manual override button to obtain sand on-demand. 28 Sanders deliver sand to both wheels of an are equipped with fixed rate sanding ahead axle either by having a pair of sanders (one of the third axle, delivering a nominal 2 kg of for the left wheel and one for the right wheel) sand per minute (to each wheel). The sander or by having two delivery hoses from a single is often inhibited at speeds below 10mph, to sander. Since sanders are directional, Multiple avoid laying a high density of sand which could Units are typically equipped with sanders at cause interference with track circuits. (2 kg / axle three in each direction. min of sand, deposited at 10 mph, is equivalent to a sand density on the track of 7.5 g/m. At When the WSP system detects wheel slide, this density, sand is unlikely to interfere with it calls on the sander to eject sand. A typical track circuits.) The above configuration, herein sander configuration is shown in image 2; referred to as Single Fixed Rate Sanding the sand is delivered from a hopper and (SFRS) undoubtedly has low adhesion braking compressed air carries it along a flexible sand performance benefits. However, by using Image 1: Railway sand (note coarse grains). delivery hose, ejecting the sand just ahead more sand, there is potential to deliver greater of the wheel. The sand is aimed at the wheel/ benefits. rail contact point, as shown in image 3. As the sand passes through the wheel/rail interface, DELIVERING MORE SAND the abrasive nature of the sand helps transmit the braking shear forces from the wheel into A greater quantity of sand could be delivered the rail, and the contamination layer is also through: damaged by the abrasive sand particles. The sand is crushed and turns to dust (see • Distributed sanding (multiple sanders image 4); the dust probably helping to absorb distributed along the train), and moisture. Sanders are considered to have a • Variable rate sanding (speed-dependant two-fold benefit by: sand discharge rate, with higher sand Image 2: Typical sander configuration (note rates at higher speed). sand hopper and flexible delivery hose). • Providing a temporary boost to the level of adhesion experienced by the sanded The key benefit of the variable rate sander axle (and subsequent axles to a lesser is that it can deliver a higher rate of sand at extent), and higher speeds (4 kg / min at speeds above • Abrading or breaking down the leaf film, 20 mph), yet it is able to vary its flow rate at assisting in its removal. lower speeds to respect the 7.5 g/m guidance. A comparison of sand flow rates for fixed and It should be noted that automatic sanders do variable rate sanders is given in image 5. A not predict where to lay sand: they need wheel train equipped with variable rate sanders at slide to occur first to trigger the sand delivery. axle 3 is referred to as Single Variable Rate Automatic sanders were initially introduced on Sanding (SVRS), and when two axles are Image 3: Sand being ejected from the sand multiple units by British Rail Research, starting equipped (typically axles 3 & 7) it is known as delivery hose, directed at the wheel/rail around 1996. Most modern multiple units Double Variable Rate Sanding (DVRS). interface (train is stationary; test button used to eject sand for photograph). Image 4: Sand being delivered at speed (≈ 40 mph) during wheel slide.
Details
-
File Typepdf
-
Upload Time-
-
Content LanguagesEnglish
-
Upload UserAnonymous/Not logged-in
-
File Pages6 Page
-
File Size-