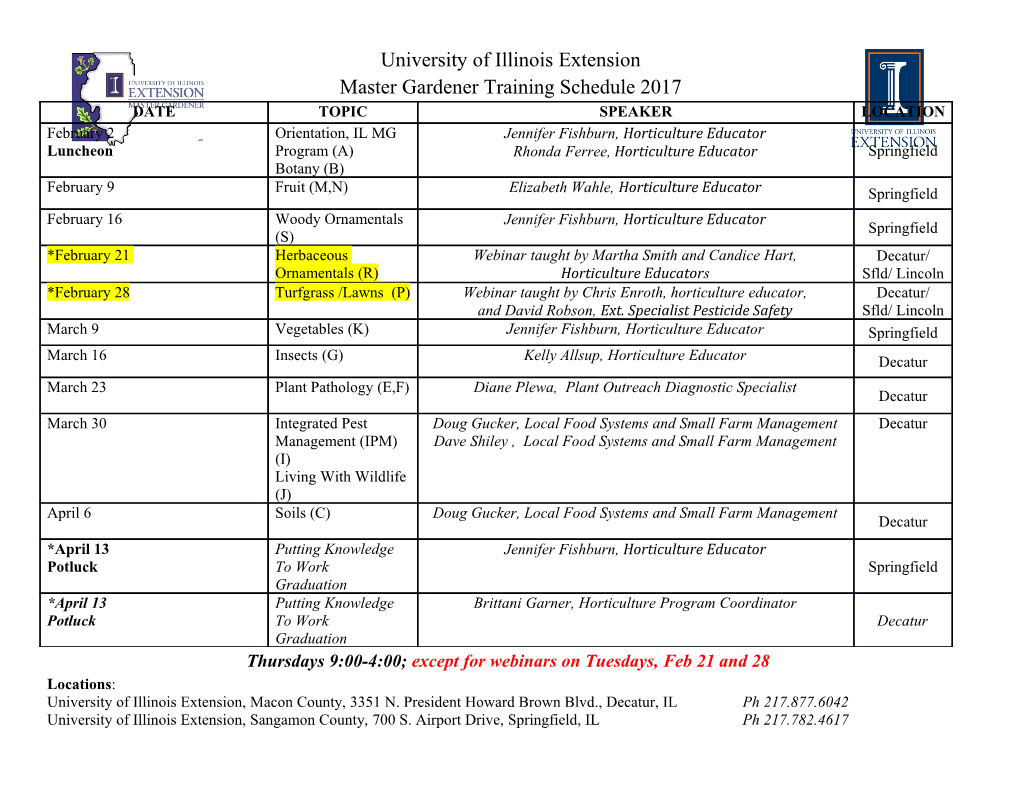
SUPERALLOY METALLURGY A GLEEBLE STUDY OF ENVIRONMENTAL FRACTURE IN INCONEL 601 A Thesis presented to the Faculty of California Polytechnic State University, San Luis Obispo In Partial Fulfillment of the Requirements for the Degree Master of Science in Materials Engineering by Alan C Demmons June 2016 © 2016 Alan C Demmons ALL RIGHTS RESERVED ii COMMITTEE MEMBERSHIP TITLE: Superalloy Metallurgy A Gleeble Study Of Environmental Fracture In Inconel 601 AUTHOR: Alan C Demmons DATE SUBMITTED: June 2016 COMMITTEE CHAIR: Dan Walsh, Ph.D. Professor of Materials Engineering COMMITTEE MEMBER: Robert Crockett, Ph.D. Professor of Biomedical Engineering COMMITTEE MEMBER: Lanny Griffin, Ph.D. Professor of Biomedical Engineering iii ABSTRACT Superalloy Metallurgy a Gleeble Study of Environmental Fracture in Inconel 601 Alan Demmons At temperatures above 0.5 Tm and in aggressive atmospheres predicting alloy performance is particularly challenging. Nickel alloys used in regimes where microstructure and properties are altered dynamically present unique requirements. Exposure may alter properties with unexpected early failure. The Gleeble is a valuable tool for investigation and simulation of thermo-mechanical properties of an alloy in various regimes up to the threshold of melting. In this study, four regimes of temperature and strain rate were simulated in an argon atmosphere to both investigate and document normal and abnormal failure modes. Commercial Inconel 601 was tested in selected regimes and in two treatments (as received and strain aged). Next two exposed conditions (TEOS and Hydride) were tested. Slow strain-rate and high temperature produced brittle intergranular fracture. Exposure at elevated temperature to process gases reduced both strength and ductility in both TEOS and Hydride. TEOS exposure reduced reduction in area in the alloy significantly more than the Hydride exposure. Key Words: Superalloy, Inconel 601, Gleeble, Fracture, Environmental iv ACKNOWLEDGMENTS The author wishes to acknowledge Dr. Dan Walsh for his support and encouragement. He is not only a stellar mentor and minor deity in welding, but also a true humanitarian and friend. Dan took me in when others would drop the bar and pull the curtains. Dan’s wife Jane must be recognized for her generosity of spirit and patience for without the sustenance of home and family, which she shared graciously on many memorable occasions this work would not be complete. Peg Peterson my dear friend and muse who nurtured and healed my wounds of struggle with the less gentile practitioners of the writing art. My sincere appreciation is also offered to Dr. Heidersbach whose support of students in their pursuit of dreams fueled with a thirst for new knowledge goes beyond the occasional mending of damaged self-esteem with a little Holy Water. In our society education has come to represent opportunity. For me, obtaining a Master’s degree acknowledges personal growth and a nurturing of a soul living in a community of souls. It is one small step in pursuit of my passion. At this juncture, a time of closure, it is satisfying to acknowledge that I was never alone. In addition to Dan, Jane, Peg, and Bob, I do very much appreciate and thank these other very special people. Special recognition must be extended to Becky Powel and those persons in the Graduate Office, where they support scholarship with more than thesis editing. Their genteel encouragement, sanguine support, and gracious style are all to be emulated and admired. Further I must give my very special thank-you to Martin Koch and Dr. Paul Rainey for the complement with FEF recognition of my abilities, wants and needs. Both Martin and Paul know the lessons of history and life. Adding to this group of supporters is Dr. Lanny Griffin who is a valued member of my review committee. These educators are passing on knowledge through thoughts and deeds to fortunate students in their classes. Thank-you is also offered to David Gibbs, and Alan Shi. These are two, fellow graduate students who share an on-going passion and passionate desire to know. To know, not just cram enough to pass a test but to master the inclusive subjects supporting and incorporated within metallurgy and materials. Together we pursued multifaceted ideas of the engineering science in ways that nurtured mutual intellectual growth. Finally, I would like to acknowledge the support of my son Patrick, my Mother, my adopted brother Donald Okano, my brother John Sutton, Karen (horses, donkey dogs, cats, et al) and others in my extended family for their sympathetic v forbearance. They all picked up the slack levied by my ambition to pursue a passion for metallurgy. The loss of my presence and income during an important time of their lives brought elements of student life with want or indigence to them all. Their collective sacrifices made in my behalf can only be repaid in-kind, with love. I also dedicate a loving thank-you to my Grandfathers, Lester and Bion and my Father Wesley for their combined support, sacrifice, and love are the rock solid foundation of the Demmons family upon which I could rely to guide me. From these men I learned the meaning of to be a man and the values of Duty, Honor, and Country. In conclusion, I have too many associates to thank individually. So if unnamed please know that your fellowship and scholarship is treasured. vi TABLE OF CONTENTS Page LIST OF TABLES ............................................................................... xi LIST OF FIGURES ............................................................................ xii CHAPTER 1. SUPERALLOYS ............................................................................. 1 1.1 Introduction ........................................................................ 1 1.2 Preview .............................................................................. 6 2. OBJECTIVE .................................................................................... 8 3. ALLOY DEVELOPMENT ................................................................ 9 3.1 Alloy Processing .............................................................. 12 3.2 Alloy Evolution ................................................................. 15 3.3 Metallurgical Alloy Theory ................................................ 18 3.4 The Solid State ................................................................ 20 3.5 Gamma Matrix (γ) ............................................................ 23 3.6 Gamma Prime (γ’) ............................................................ 25 3.7 Carbides .......................................................................... 31 3.8 Borides ............................................................................. 32 vii 3.9 Topologically-Close Packed (TCP) Phases .................... 33 3.10 Mechanical Metallurgy ................................................... 33 3.11 Dislocations ................................................................... 34 3.12 Burgers’ Vector .............................................................. 37 3.13 Edge Dislocation ............................................................ 37 3.14 Screw Dislocations ......................................................... 38 3.15 Grain Boundaries ........................................................... 40 3.16 Twin Boundaries ............................................................ 40 3.17 Deformation ................................................................... 42 3.18 Stage I. Easy–Glide ....................................................... 43 3.19 Stage II. Linear–Hardening ............................................ 44 3.20 Stage III. Cross–Slip ...................................................... 45 3.21 Mechanical Tests ........................................................... 47 3.22 Creep ............................................................................. 49 3.23 Larson–Miller ................................................................. 54 4. GLEEBLE TESTING ..................................................................... 59 4.1 Procedure ........................................................................ 59 4.2 Gleeble General ............................................................... 60 viii 4.3 Computer Interface .......................................................... 61 4.4 Mechanical Control .......................................................... 62 4.5 Heating ............................................................................ 64 4.6 Chemistry ......................................................................... 65 4.7 Gleeble Test Samples ...................................................... 67 4.8 Fracture and Microstructure ............................................. 68 4.9 Imaging ............................................................................ 69 4.10 Electronic Characterization ............................................ 69 5. RESULTS AND DISCUSSION ..................................................... 72 5.1 Introduction ...................................................................... 72 5.2 Rod and Plate Test Results ............................................. 74 5.3 Plane Stress Test Results ................................................ 79 5.4 Service Conditioned Specimen Test Results ................... 83 5.5 OLM Microstructure and Grain Size ................................. 86 5.6 Flow and Fracture Discussion .......................................... 90 5.7 SEM Fractography
Details
-
File Typepdf
-
Upload Time-
-
Content LanguagesEnglish
-
Upload UserAnonymous/Not logged-in
-
File Pages169 Page
-
File Size-