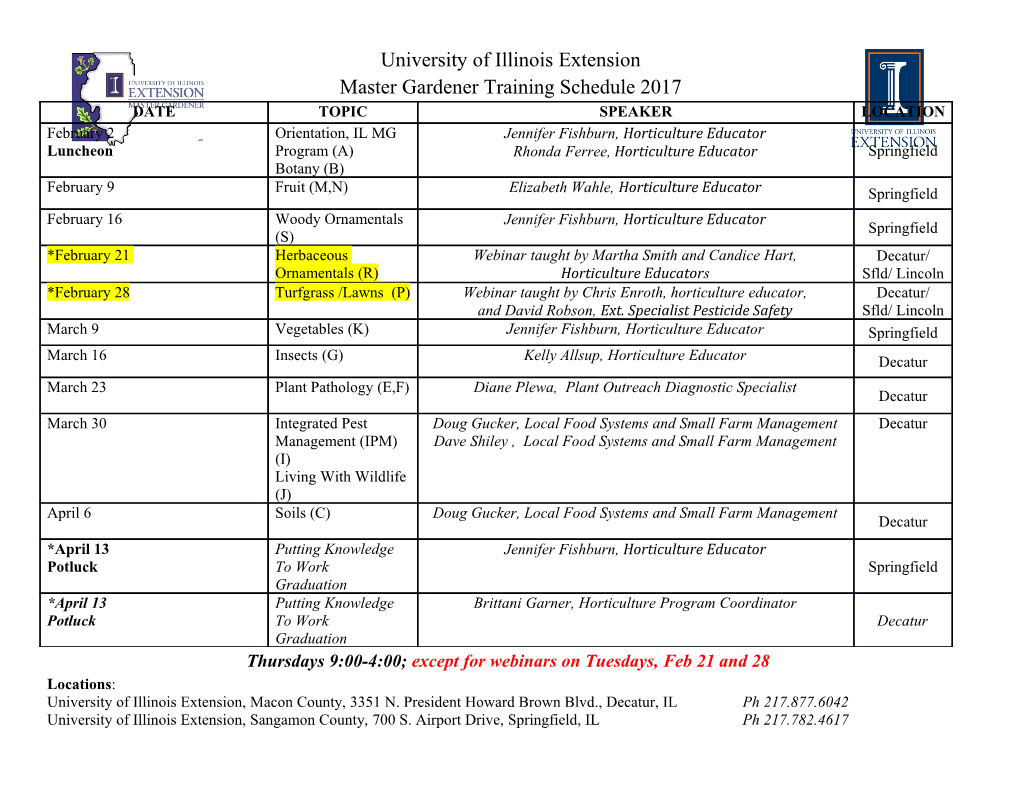
View metadata, citation and similar papers at core.ac.uk brought to you by CORE provided by Siberian Federal University Digital Repository ISSN 0020-1685, Inorganic Materials, 2016, Vol. 52, No. 11, pp. 1091–1095. © Pleiades Publishing, Ltd., 2016. Original Russian Text © O.I. Podkopaev, A.F. Shimanskii, T.V. Kulakovskaya, A.N. Gorodishcheva, N.O. Golubovskaya, 2016, published in Neorganicheskie Materialy, 2016, Vol. 52, No. 11, pp. 1163–1167. Amorphous Silica Containers for Germanium Ultrapurification by Zone Refining O. I. Podkopaeva, *, A. F. Shimanskiib, **, T. V. Kulakovskayaa, A. N. Gorodishchevac, ***, and N. O. Golubovskayab aOJSC Germanium, Transportnyi proezd 1, Krasnoyarsk, 660027 Russia bSiberian Federal University, Svobodnyi pr. 79, Krasnoyarsk, 660047 Russia cReshetnev Siberian State Aerospace University, pr. im. gazety Krasnoyarskii rabochii 31, Krasnoyarsk, 660014 Russia *e-mail: [email protected] **e-mail: [email protected] ***e-mail: [email protected] Received March 2, 2016 Abstract—We have studied the wetting behavior of molten germanium on silica ceramics and amorphous sil- ica coatings in vacuum at a pressure of 1 Pa and a temperature of 1273 K. The results demonstrate that the wetting of rough surfaces of ceramic samples and coatings by liquid Ge is significantly poorer than that of the smooth surface of quartz glass. The contact angle of polished glass is ~100°, and that of the ceramics and coatings increases from 112° to 137° as the total impurity content of the material decreases from 0.120 to 1 × 10–3 wt %. Using experimental contact angle data, we calculated the work of adhesion of molten Ge to the materials studied. Its value for the surface of the ceramics and coatings decreases from 0.45 to 0.20 J/m2 with decreasing impurity content, whereas the work of adhesion to a smooth glass surface is 0.55 J/m2. We have fabricated fused silica test containers coated with high-purity amorphous silica. Using horizontal zone refining, we obtained germanium samples with a carrier concentration difference on the order of 1011 cm–3. Keywords: melt, container materials, amorphous silica, fused silica, ceramic, contact angle, work of adhesion DOI: 10.1134/S0020168516100125 INTRODUCTION mobility in dislocation-free germanium, up to The use of germanium single crystals containing as ~3000 cm2/(V s), which is twice that in Si, allows it to low impurity concentrations and defect densities as be used with great success in the fabrication of space- possible holds much promise for the development of grade high-speed digital devices [6]. semiconductor nanotechnologies. They are needed in photovoltaics as substrates for epitaxial III–V opto- Extrapure-grade germanium is used to fabricate electronic structures, which are required for the fabri- radiation-resistant gamma-ray detectors, which cation of solar cells based on GaInP–GaInAs–Ge require crystals with a concentration of electrically systems—high-performance photoconverters offering active impurities in the range from 109 to 1011 cm–3 efficiencies above 39% [1–4]. [4, 5]. In the technology of the preparation of extra- To fabricate such solar cells, high-purity, disloca- pure germanium and low-dislocation germanium tion-free crystals are necessary, because dislocations crystals, the melt container material plays an import- and unintentional impurities lead to lattice mismatch ant part. A standard material for this purpose is ultra- between Ge and III–V compounds, making it difficult pure-grade graphite. However, when graphite melt to grow high-quality epitaxial layers on germanium containers are used, the germanium melt becomes substrates [4, 5]. contaminated with B, Ga, and P. At low concentra- Dislocation-free high-purity germanium helps to tions of these impurities, their effective distribution resolve issues pertaining to the use of silicon in the fab- coefficients approach unity and, accordingly, they rication of radiation-resistant power MOSFET tran- cannot be removed [7]. One way to resolve this issue is sistors, which are employed in power supply units, to employ new container materials. These include voltage converters, drive control units and other elec- boron nitride, silica-based materials, sapphire, glassy tronic devices in space equipment. The high carrier carbon, and aluminum nitride. According to a large 1091 1092 PODKOPAEV et al. amount of data, amorphous SiO2 in the form of fused Impurity concentrations in our samples were deter- silica or ceramics is the best choice [4, 5, 8, 9]. mined by atomic absorption on a Solaar M spectro- During germanium purification by crystallization, meter (Thermo Electron Corp.). To examine the impurities present in the container material may enter microstructure of the samples and assess their surface the melt and contaminate it, so the wettability of the roughness (surface height distribution), we used an container by the melt is an important factor, because it Axio Observer A1 optical microscope. determines the dissolution kinetics of the container Germanium was zone-refined using a Kristall-808 material. Moreover, the contact angle influences the unit (Freal and Co.) and test containers with a high- shape of the melt meniscus and, accordingly, the purity silica coating on their working surface. As a feed adhesion of the coating material to germanium, which stock, we used GPZ zone-refined germanium with a in turn influences its ability to separate from the con- resistivity of at least 47 Ω cm. The process was run in a tainer in the unloading step [9]. Available data on the hydrogen atmosphere. The molten zone length was wettability of SiO2-based materials by molten germa- 5cm. nium are limited to results for polished surfaces of The room-temperature resistivity of GPZ poly- fused silica [10, 11]. crystalline ingots was measured by the two-probe The purpose of this work was to study the wetting method. The resistivity of the zone-refined germa- properties of molten germanium on rough surfaces of nium was also measured by the two-probe method at silica ceramics differing in purity and on amorphous room temperature, using monocrystalline blocks cut silica coatings on the surface of fused silica. We pro- from the ingots. In addition, we performed resistivity duced test silica containers with high-purity silica measurements at 213 K by a microwave method. The coatings and used them in germanium purification by microwave measurements were performed with an zone refining. Angara 2 system. The carrier concentration difference was determined by capacitance–voltage (C–V) mea- surements with a QuadTech QT7600B LCR meter. EXPERIMENTAL Ceramic articles were produced by slip casting. To RESULTS AND DISCUSSION this end, we prepared an aqueous slip containing 70 wt In our experiments concerned with the wetting % amorphous SiO2 powder, which was sintered at a temperature of 1450 K for 2 h [12]. behavior of molten germanium, we used ceramic sam- ples prepared under identical conditions from amor- Silica powders ranging in total impurity content phous silica powders with identical particle size com- from 0.120 to 0.020 wt % were prepared by grinding positions, similar in physical properties and micro- quartz glass in a planetary mill using agate vials, fol- structure (Fig. 1). lowed by purification in a 3 : 1 mixture of the HF and The grain size in the ceramics ranged from 1 to HNO acids. High-purity amorphous SiO containing 3 2 20 μm. The surface roughness value was 5–10 μm, the 0.010 to 0.001 wt % impurities was prepared by a sol– density of the ceramics was 1.95 g/cm3, and their gel process using extrapure-grade silicon tetrachloride porosity was ~12.0%. The ceramic samples differed in (SiCl ) [13]. 4 impurity content, which ranged from 0.001 to 0.120 wt %. The synthetic SiO2 powders were used to prepare In all of the samples, the dominant impurities were ceramics and produce ceramic coatings up to 100 μm Na, K, Al, and Fe. The reference sample (polished thick on quartz glass substrates by slip casting [12]. In quartz glass) had a similar range of impurities, and addition, ~20-μm-thick SiO2 coatings were produced their content was 0.050 wt %. on fused silica by repeatedly wetting its surface with Figure 2 is a photograph of a molten germanium silicon tetrachloride, followed by hydrolysis in humid air, drop on the surface of a ceramic sample containing drying, and annealing at a temperature of 1253 K [14]. 0.01 wt % impurities. At this impurity content, the ° The contact angle of molten germanium on SiO2- contact angle is 133 . based ceramics and coatings was determined on a The contact angle of molten germanium on the Kaplya apparatus (State Research and Design Insti- surface of polished quartz glass was determined to be tute for the Rare-Metals Industry) using substrates in ~100°, which is comparable to the corresponding the form of rectangular plates 2 × 2 cm2 in area. The equilibrium contact angle reported by Cröll et al. [10] measurements were performed in vacuum at a residual and Kaiser et sl. [11]. Figure 3 demonstrates that the pressure of 1 Pa and a temperature of 1273 K. The ref- contact angle of the ceramic samples increases from erence sample used in our wetting experiments was a 112° to 137° as the total impurity content decreases polished fused silica plate. from ~0.120 to 0.001 wt %. INORGANIC MATERIALS Vol. 52 No. 11 2016 AMORPHOUS SILICA CONTAINERS 1093 133° Fig. 2. Photograph of a molten germanium drop on the sur- Fig. 1. Typical microstructure of the ceramic samples, face of a ceramic sample containing 0.01 wt % impurities. 700×. 140 135 10.84 μm 130 125 120 Contact angle, deg Contact 115 110 0 0.02 0.04 0.06 0.08 0.10 0.12 wt % impurities Fig. 3. Contact angle as a function of the percentage of Fig. 4. High-purity silica coating on the surface of fused impurities in the ceramic samples.
Details
-
File Typepdf
-
Upload Time-
-
Content LanguagesEnglish
-
Upload UserAnonymous/Not logged-in
-
File Pages5 Page
-
File Size-