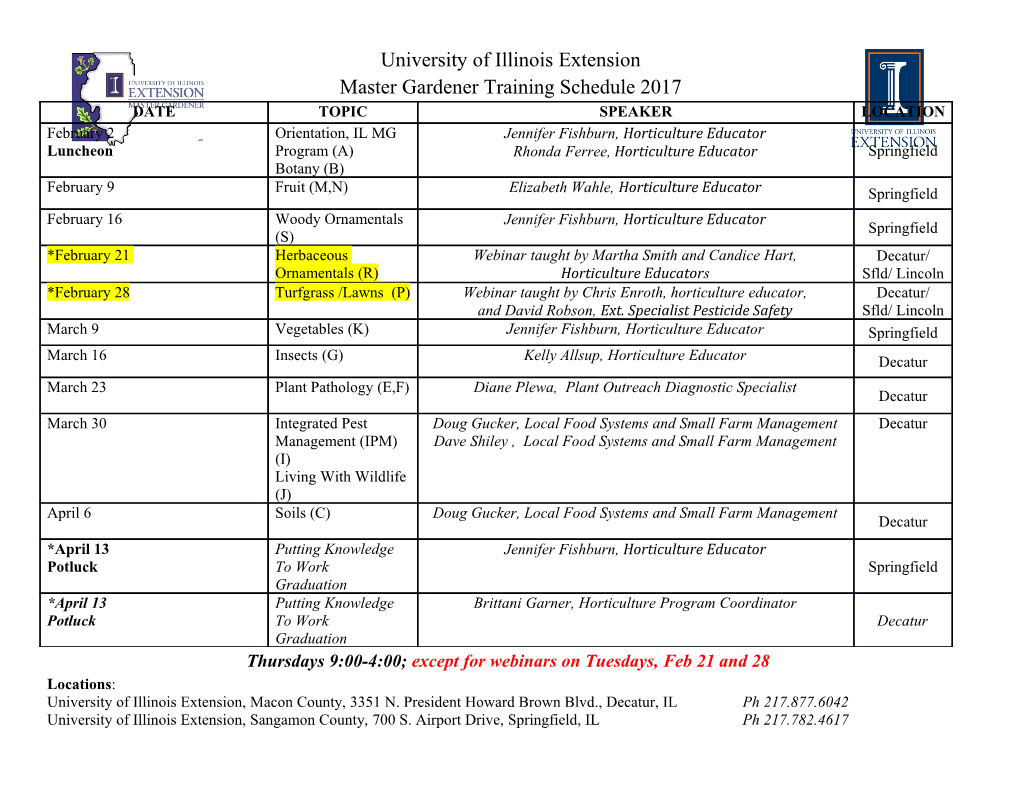
P.Chellapandi, P.Puthiyavinayagam, T.Jeyakumar S.Chetal and Baldev Raj Indira Gandhi Centre for Atomic Research Kalpakkam - 603102 IAEA-Technical Meeting on ‘Design, Manufacturing and Irradiation Behavior of Fast Reactor Fuels’ 30 May-3 June 2011, IPPE, Russia Scope of Presentation Nuclear Power & FBR Programme in India Economic advantages of high burnups Int. experience on achieving high burnup Roadmap of enhancing the burnup Experience with carbide & oxide fuels Highlights of R&D Future Plans India’s Nuclear Roadmap 70000 • PHWRs from indigenous Uranium Nuclear Power Capacity • PHWRs from imported Uranium 60000 Projection (in MWe) • Imported LWR to the max. extent of 40 GW(e) 50000 • PHWRs from spent enriched U from LWRs 40000 (undersafeguard) 30000 • FBRs from reprocessed Pu and U from PHWR 20000 • FBRs from reprocessed Pu and U from LWR (undersafeguard) 10000 • U-233-Thorium Thermal / Fast Reactors 0 2010 2012 2017 2022 2032 • India has indigenous nuclear power program (4780 MW out of 20 reactors) and expects to have 20,000 MWe nuclear capacity on line by 2020 and 63,000 MWe by 2032. • Now, foreign technology and fuel are expected to boost India's nuclear power plans considerably. All plants will have high indigenous engineering content. • India has a vision of becoming a world leader in nuclear technology due to its expertise in fast reactors and thorium fuel cycle. FBR Programme in India • Indigenous Design & Construction Future FBR • Comprehensiveness in development of • 1000 MWe • Pool Type Design, R&D and Construction • Metallic fuel • High Emphasis on Scientific Breakthroughs • Serial constr. • Indegenous • Synthesis of Operating Experiences • Beyond 2025 • Synthesis of Emerging Concepts (Ex.GENIV) • Focus on National & International Weight in t No. Component PFBR CFBR CFBR 07 08 01 Main vessel 134 116 Collaborations 09 10 02 Core support 44.8 36 structure •500 MWe 03 Grid Plate 76 34 • Emphasis on high quality human resources 04 Core -- -- 06 •Pool Type 05 Inner vessel 61 55 •UO2-PuO2 Ø11950 06 Transfer Arm -- -- 07 Large Rotatable -- -- • Creation of environment for enabling 13725 Plug •3 twin units 08 SRP/Control Plug -- -- 04 05 11 innovations 09 IHX -- -- 10 Primary Pump -- -- •Indigenous 03 01 11 Anchor safety 110 95 •From 2023… 02 12 vessel • Marching towards world leadership by 2025 12 Thermal -- -- Insulation PFBR FBTR •1250 MWt • 40 MWt •500 MWe • 13.5 MWe •Pool Type • Loop type •UO2-PuO2 • PuC – UC •Indigenous • Design: CEA •From 2013.. • Since 1985 Economic Befefits of High Burnup High Burnup is desired to FR Burn-up (MWd/Kg) • Reduce Fuel Cycle Cost - to lower unit energy cost • Minimise Waste Generation - less minor actinides and fission products • Reduce Man Rem Exposure Cost Projection (%) EFR EPR Capital 71 55 O & M 19 17 cost cycle fuel Relative Fuel Cycle 10 20 For PFBR with 100 GWd/t (peak) Unit Energy Cost Rs. 3.22 Fuel Cycle Cost Rs. 0.73 Target - 200 GWd/t gradually Fuel Cycle Cost Variation enhanced to 250 GWd/ti Worldwide Experience on Burnup Standard MOX fuel Experimental fuel Country or Burn-up Maximum group of No. of pins Type of fuel reached burn-up Main reactors countries irradiated pellets MWd/t MWd/t Oxide Western Phenix, PFR, Solid & 265 000 135 000 200 000 Europe KNK-II annular Unites States 64 000 130 000 200 000 FFTF Leading pins Japan 50 000 100 000 120 000 Joyo Solid CIS 13 000 135 000 240 000 BOR-60 Vibro-pac 1 800 100 000 - BN-350 Solid &annular Solid & 1 500 100 000 - BN-600 annular Country Reactor Burnup (% h.A) BR-10 5 Russia BOR-60 10 Carbide Germany KNK-II - USA EBR-II 20.7 India FBTR 17 200 GWd/t is realisable. Burnup on whole core basis is important Issues Related to High Burnup Limitation to achieve high burnup comes from the current generation core structural materials owing to its excessive deformation and degradation due to irradiation rather than from the fuel. Thus, the capability to achieve high burn up is limited by the capability to accommodate higher neutron doses. Governing Parameters Multi Disciplinary Expertise In-Pile Behaviour of Fuel • Reactor physics Element & Subassembly • Fuel Properties - FCMI • Material Development - FCCI • Core engineering Degradation in PIE Mechanical Properties Modelling Fuel Cycle Aspects • Reprocessing and Waste Management Integrated and Synergistic Approach is Essential Experience with Carbide Fuel FBTR and Its Fuel Cycle • FBTR is in operation since 1985: completed more than 25 years of operation • It uses a unique U,Pu mixed carbide fuel with high Pu content (Mk-I:70%, Mk-II: 55 %) • Over 1000 fuel pins have reached an international record in burn-up (165 GWd/t) without any failure in the core • PFBR test fuel SA attained allowable burnup of 112 GWd/t. The performance of FBTR has been excellent in recent years, with plant availability during each campaign exceeding 80 %. • Since no direct data was available, physical, chemical and irradiation behaviour of fuel were obtained through extensive out-of-pile tests and with the gradual increase of burnup in the reactor. FBTR would operate further around 10 EFPY for irradiation tests on metallic fuel, sol-gel fuel and advanced clad materials FBTR: Mk-I Carbide Fuel Subassembly SALIENT DATA Fuel : (70%Pu-30%U)C Pellet dia : 4.18 mm Pin OD/ID : 5.1 / 4.36 mm Peak Linear Power : 400 W/cm Active Core Height : 320 mm Clad Material : 20%CW 316 Wrapper Material : 20%CW316L No. of Pins : 61 Width Across Flats : 49.8 mm Height : 1661.5 mm Mark-I SA Performance Active core Active core Parameters Active Core top bottom Middle Coolant Temp (Av.) 340 405 515 º C Coolant Pressure 0.34 0.25 0.17 MPa Neutron Flux 1.25X 1015 1.71X 1015 0.98X 1015 n/cm2/sec Temp & DPA variation over SA length Burnup Peak Fluence 600 80 DPA 2 70 (GWd/t) (n/cm ) 500 60 400 100 46.8 0.783E+23 50 150 70.2 1.17E+23 300 40 30 200 Fluence. (DPA) 154 72.5 1.21E+23 20 Temperature ( C ) . Temperature ( ) C 100 160 74.9 1.25E+23 10 0 0 0 50 100 150 200 250 300 350 165 77.2 1.28E+23 Axial length of SA (mm) Micrographs of Fuel Pin Cross Section 25GWd/t 50GWd/t 100GWd/t 155GWd/t Micrographs of fuel pin cross section at the centre of fuel column Radial cracking at low burn-ups in free swelling regime 155GWd/t Progressive reduction in fuel clad gap with burn-up Cracking pattern changes from radial to circumferential cracking with closure of fuel clad gap Complete closure of fuel-clad gap along the entire fuel column at 155 GWd/t burnup Porosity free dense zone at the outer rim of the fuel Swelling of fuel accommodated by porosities & clad swelling End of fuel column X –radiography & Neutron radiography Plenum Fuel column Fuel column Plenum X-radiographs N-radiographs 12 10 Max. FG release ~ 16 % FG Pressure ~ 20 bars 8 6 (155 GWd/t) 4 2 Average increase in increase stackAverage length(mm) Burn-up in GWd/t 0 0 50 100 150 200 Av. increase in stack length stack in increase Av. Burn-up(GWd/t) 5 Fuel column elongation (X-ray) Higher axial swelling in the restrained swelling phase & low fission gas release and plenum pressure Performance of Fuel Clad and Wrapper 20 % CW SS316 Burnup Max Fluence Peakdpa 155 GWd/t 1.2 x 1023 n/cm2 83 . • 155 GWd/t Burnup Fuel assembly and Fuel Pins 11.5% (485 C) Progressive increase in ∆d ∆d /d %) dimensions of clad & V / V % 3.5% wrapper with ∆ (430 C) dpa Diametral strain ( strain Diametral Dimensional Changes in Wrapper & Clad Void Swelling of FBTR Clad & Wrapper Structural Material Properties: PIE Data Cladding Wrapper 81 dpa TEM studies 40 dpa 30 dpa Virgin 100 nm 100 100 nm V / V % nm 500 ∆ nm Salient PIE Results of 100 GWd/t Fuel EXCELLENT PERFORMANCE OF FUEL / CLAD / HEXCAN NO FUEL/CLAD GAP SEEN AT THE CENTRE OF FUEL COLUMN AVERAGE INCREASE IN STACK LENGTH ~ 1.73% FISSION GAS RELEASE ESTIMATED TO BE BETWEEN 3-14% INTERNAL CLAD CARBURISATION NOT OBSERVED MAXIMUM INCREASE IN CLAD DIAMETER- 1.6% RESIDUAL DUCTILITY OF 3% OBSERVED ON THE CLAD TUBE CLAD VOLUMETRIC SWELLING ESTIMATED TO BE 4.4% FUEL HAS REACHED 150 GWd/t BURN-UP WITHOUT FAILURE Swelling and Creep Strains in Clad Burnup Total Clad Strain Clad Diametrical Increase (GWd/t) Predicted PIE Predicted PIE 50 0.2% 0.3% 0.01 mm 0.018 mm 100 1.9% 1.6% 0.09 mm 0.08 mm 150 5.7 % - 0.27 mm - 154 6.2% 5% 0.274 mm 0.27 160 6.7% - 0.32 mm - 165 7.2% - 0.34 mm - Burnup Limited to 165 GMd/t based on residual ductility consideration (<10 %) Dilation Width Across Flat SA Active Core Theoretical Normalised At Max. B.U Limit Length (mm) 154GWd/t 154 GWd/t 164.2 GWd/t 0 0.008 0.004 0.004 32 0.009 0.004 0.005 64 0.010 0.005 0.006 96 0.029 0.017 0.019 128 0.104 0.072 0.080 160 0.245 0.199 0.224 192 0.455 0.405 0.462 224 0.647 0.596 0.690 256 0.701 0.650 0.765 288 0.575 0.525 0.633 320 0.343 0.297 0.362 Burnup Limited to 165 GMd/t based Handling consideration (< 1 mm) Cladding Failure in 17th Campaign Campaign started in Dec ‘10 with 48 fuel SA 27 MK-I, 13 MK-II & 8 MOX In Feb 2011, at 18 MWt with TG feeding the grid, scram took place on DND signal provided for detection of fuel clad failure • From DND signals and the ratio of Kr85 / Kr87 in cover gas samples, failed fuel identified to be one with a burn-up of >100 GWd/t.
Details
-
File Typepdf
-
Upload Time-
-
Content LanguagesEnglish
-
Upload UserAnonymous/Not logged-in
-
File Pages48 Page
-
File Size-