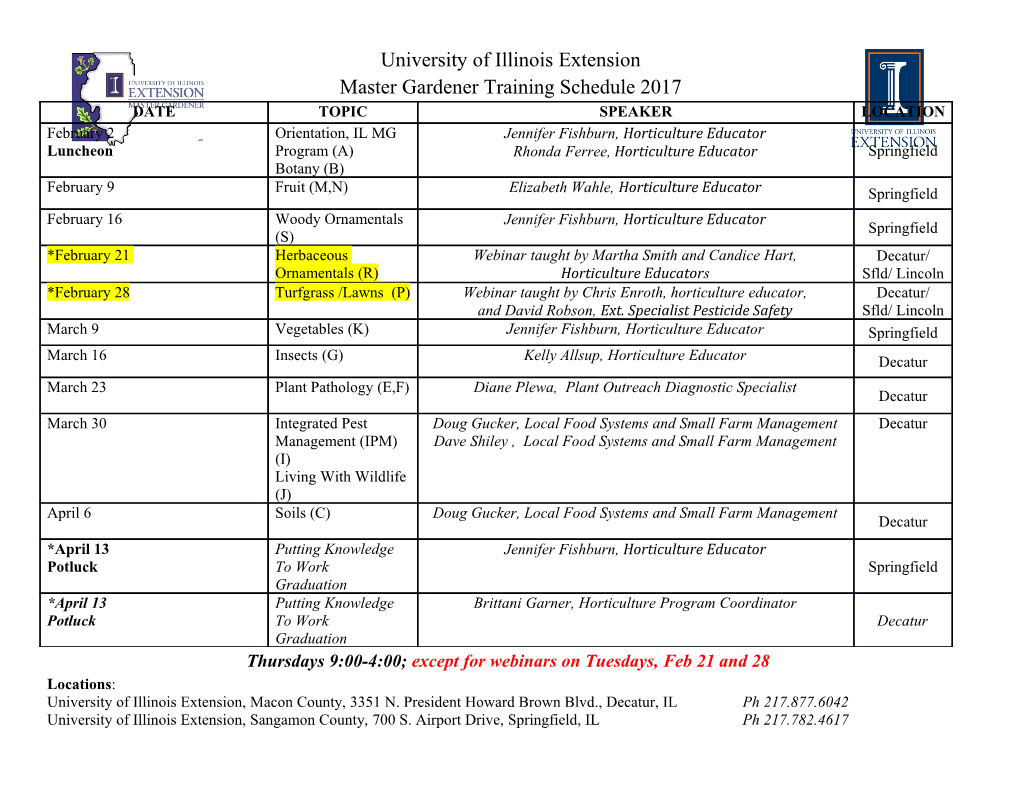
2015 IEEE International Conference on Robotics and Automation (ICRA) Washington State Convention Center Seattle, Washington, May 26-30, 2015 A Multi-level Motion Controller for Low-Cost Underwater Gliders Guilherme Aramizo Ribeiro, Anthony Pinar, Eric Wilkening, Saeedeh Ziaeefard, and Nina Mahmoudian Abstract— An underwater glider named ROUGHIE (Research deploying UGs [23] for submarine tracking. With a valida- Oriented Underwater Glider for Hands-on Investigative Engineer- tion platform, researchers will be able to better understand ing) is designed and manufactured to provide a test platform and glider dynamics [24] and improve UG effectiveness in littoral framework for experimental underwater automation. This paper presents an efficient multi-level motion controller that can be used zones. Additionally, underwater localization and positioning to enhance underwater glider control systems or easily modified and path planning in high risk areas will be improved. for additional sensing, computing, or other requirements for ROUGHIE is 1 m long and weighs 12 kg (payload 1 kg) advanced automation design testing.The ultimate goal is to have with minimum operating endurance of 8 hours and maximum a fleet of modular and inexpensive test platforms for addressing depth of 40 m. At 10% of the cost of commercial underwater the issues that currently limit the use of autonomous underwater vehicles (AUVs). Producing a low-cost vehicle with maneuvering gliders, a ROUGHIE fleet is affordable without compromis- capabilities and a straightforward expansion path will permit easy ing the sophisticated control systems and maneuverability experimentation and testing of different approaches to improve (See the detailed characteristics in Table I). underwater automation. In this paper, the mechanical and electrical components of the ROUGHIE are introduced in Section I as a plant for the INTRODUCTION controller design. Section II outlines the multi-level control Recent developments in underwater glider (UG) control system, appropriate sensor integration, and preliminary test- systems portend greater predictive modeling and path plan- ing results. Section III concludes with the summary of the ning efficiency [1]–[10], more accurate localization [11], im- work and plans for future developments. proved autonomous cooperation [12]–[14], improved glider navigation [15] and a broader field of applications for UGs [16]. Unfortunately, progress is delayed by the lack of a robust, affordable test platform. The size, weight, and cost of legacy gliders [17]–[19] prevent them from being a viable option for testing purposes. This is evident as universities spend resources developing their own test platforms [20], [21]. To provide a universal UG testing platform for control system validation, Michigan Tech’s Nonlinear Autonomous Systems Laboratory has designed and fabricated ROUGHIE, the Research-Oriented Underwater Glider for Hands-on In- vestigative Engineering (Figure 1). ROUGHIE was designed at a low cost to increase avail- ability across universities, providing a platform on which most control systems can be evaluated. The basic design was Fig. 1. Final ROUGHIE Design and Prototype detailed in [22], under the concept design name GALUR. The price allows researchers to explore hazardous environ- ments such as high traffic harbors or under-ice waters without I. ROUGHIE DESIGN significant expense in case of glider loss. Furthermore, coop- A. Mechanical System erative control systems can also be inexpensively validated, The ROUGHIE was designed to have clean, simple hydro- as a fleet of ROUGHIEs costs less than a single legacy glider. dynamic surfaces minimizing drag and assembly time. The Expanding access of validation tools to more researchers front nose cone is a standard ogive that mates directly with will unlock new applications for UGs. Already NATO is the 0.13 m outer diameter hull. This hull is a single, o.83 This material is based upon work supported by the Office of Naval m long aluminum cylinder with no protrusions or gaps. The Research under Grant No. N00014-14-1-0032. intent is to keep the boundary layer completely intact along G. Aramizo Ribeiro ([email protected]) and S. Ziaeefard the entire hull. Figure 1 shows the glider with an acrylic hull ([email protected]) are graduate research assistants, E. Wilkening ([email protected]) is an undergraduate research assistant, and used for testing purposes. The Reynolds number remains in N. Mahmoudian ([email protected]) is an assistant professor in the the laminar region due to the short length of ROUGHIE, Department of Mechanical Engineering-Engineering Mechanics, A. Pinar allowing the design to forgo complicated geometry as seen ([email protected]) is a graduate research assistant in the De- partment of Electrical & Computer Engineering, Michigan Technological on Seaglider [18]. To reduce separation, the back end cap is University, Houghton, MI 49931, USA shaped as a revolved NACA 0051 airfoil, post max thickness. 978-1-4799-6923-4/15/$31.00 ©2015 IEEE 1131 Metric Value piston in the water reservoir is found by reading the analog Dimensions (m) 1.3 (d) x 1 (l) output of a draw-wire sensor, which provides feedback to Wingspan (m) 0.6 the Arduino so it can determine when to turn the water Total Mass (kg) 12 pump on and off. The draw-wire sensor, shown in Figure Payload Mass (kg) 1 2, is a retractable cable that actuates a potentiometer inside Endurance (hr) 8 the sensor housing. The linear mass is moved using a non- Maximum Depth (m) 40 continuous servo whose shaft is coupled to a large gear that Optimal Glide Angle (degrees) 35 meshes with a linear rack. The servo has built-in electronics Displacement (mL) 400 that communicate with the Arduino using RS-485, providing Battery Chemistry LiPO the Arduino with a means to both command the servo shaft to a particular angle and positional feedback of the shaft. TABLE I An inertial measurement unit (IMU) is also installed that ROUGHIE DESIGN CHARACTERISTICS communicates (UART) with the Arduino providing pitch angle feedback. Finally, the glider has a pressure sensor whose analog output is read by the Arduino so that the external water pressure can be monitored. The ROUGHIE final design placed the NACA 0012 wing on the tail cap; this imposed a 3-5% penalty in lift-to- drag ratio in laminar simulation but prevents premature turbulent transition on the hull. The tail cap is also a flooded compartment, which obviates the need for sealing the wing mounts. The internal components of the ROUGHIE fit into four major modular subassemblies: the pumping and ballast as- sembly, control masses (batteries), electronic components (including the power distribution system), and framework. The framework is modular and allows these subassemblies to be swapped out if researchers prefer different components. This is accomplished using a single rail that runs the length of the glider to which each self-contained subassembly mounts. ROUGHIE controls displacement by pumping water to an internal ballast tank. A TCS MG1000 micropump takes in water through the front cap into a 450mL cylinder ballast tank with piston. Position of the piston head is read with a draw-wire sensor that correlates to total displacement. A solenoid valve is in series with the pump to prevent free flow. Pitch, roll, and yaw are controlled with linear and rotary control masses. A plate constrained to linear longitudinal movement holds the batteries and rotary control mass. This Fig. 2. Draw-Wire Sensor is driven +/- 2.5 inches from center by a Dynamixel servo using a gear and rack system. For rotary control, a brass A 14.1V battery is used as the linear mass in the glider, weight cantilever hangs from another servo and can swing from which the entire electrical system derives its energy. as a pendulum to roll the glider. The rotary mass is partially Since the pump and solenoid are the only components that coupled with the linear mass since it rides along the same can use 14.1V, a DC-DC converter is used to regulate the plate as the linear control mass. voltage to 5V. This regulated voltage supplies all other on- board electronics. All voltage rails are protected with fuses B. Electrical System and distributed from a custom circuit board. This custom All electromechanical components of the glider are con- circuit board also includes the relay-driving BJTs and relays trolled by an Arduino Mega. The water pump has its own mentioned above. dedicated off-the-shelf controller that is oscillated via a relay Other electronic assemblies include an RS-485 shield that controlled by a digital pin on the Arduino. Similarly, the allows the Arduino to communicate with the servo and on solenoid is also manipulated with a relay driven by the XBee shield allowing wireless communication (above water Arduino. Note that bipolar junction transistors (BJTs) are communication only) between the glider and a base computer used to drive the relay coils, alleviating the current demand so that gliding parameters can be changed without disassem- on the Arduino digital output pins. The position of the bling the glider. When possible, electrical connections are 1132 control when the valve is open and closed. Higher efficiency solid state switching solutions will be explored in future upgrades to the glider’s circuitry. II. ROUGHIE CONTROLS A closed loop control system is designed to provide attitude and depth control, and guarantee desired gliding per- formance underwater and robust behavior in the presence of system and environmental uncertainties. The system depicted in Figure 5 receives two inputs: pump flow rate and moveable mass position, and three outputs: depth, pitch angle, and ballast weight. Specifically, the design goals were: • Control the pitch angle to maximize the forward ve- locity (gliding velocity) or the horizontal to vertical Fig. 3. Power Distribution Circuit Board velocity ratio (gliding efficiency). • Bound the saw-tooth motion into a limited depth inter- val, removing drifts on the vertical trajectory by using made using detachable connectors so that the system can the depth sensor.
Details
-
File Typepdf
-
Upload Time-
-
Content LanguagesEnglish
-
Upload UserAnonymous/Not logged-in
-
File Pages6 Page
-
File Size-