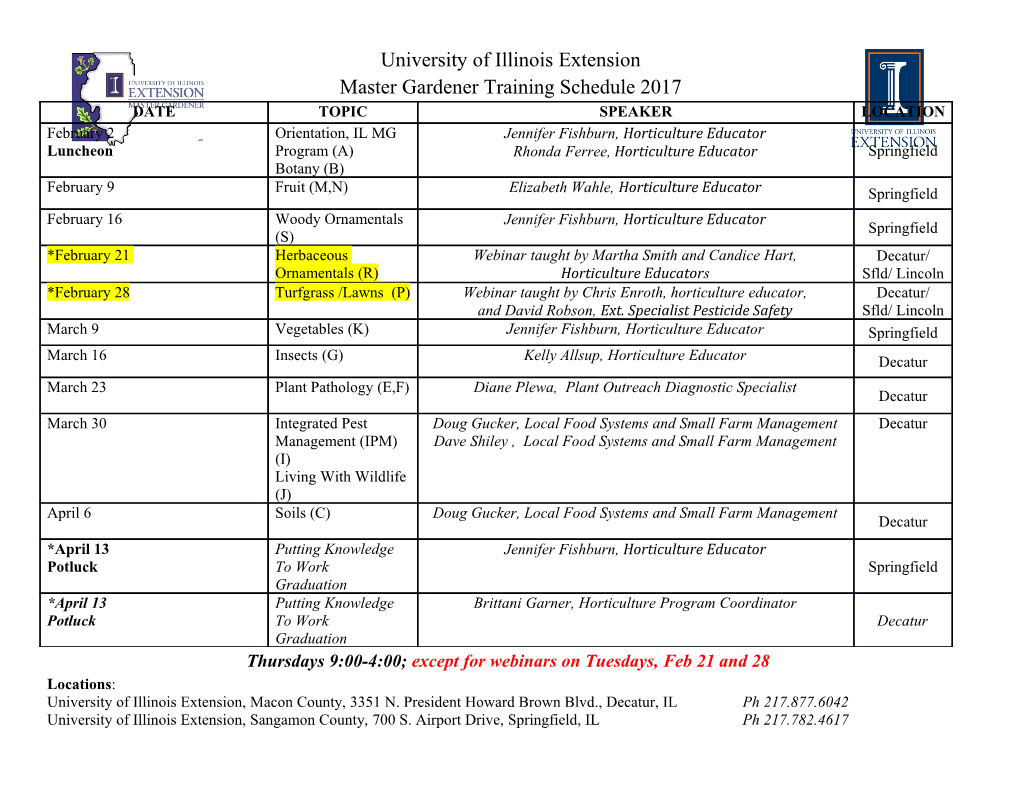
Proceedings of the 9th International Conference on Structural Dynamics, EURODYN 2014 Porto, Portugal, 30 June - 2 July 2014 A. Cunha, E. Caetano, P. Ribeiro, G. Müller (eds.) ISSN: 2311-9020; ISBN: 978-972-752-165-4 Automatic train type identification in railway bridge monitoring H. Bigelow1, B. Hoffmeister1, M. Feldmann1, F.Weil1 1RWTH Aachen University, Institute of Steel Construction, Mies-van-der-Rohe-Str. 1, 52074 Aachen, Germany email: [email protected], [email protected], [email protected], [email protected] ABSTRACT: When studying dynamic behaviour of railway bridges subjected to (high-speed) trains, monitoring of these bridges is a very useful tool. Reactions to different train types at different crossing velocities can be investigated as well as subsequent free decay processes. Nevertheless a certain amount of work is required to analyse the recorded data. Especially long term monitoring of frequently crossed bridges can lead to a large number of recorded reactions of train passages. In any case the respective train type and its crossing velocity have to be known to be associated with a certain reaction of the bridge, e.g. resonance phenomena. Using the example of a monitored German filler beam bridge, it is shown how this information can be derived directly from the measured data. At this bridge longitudinal strain and tri-directional acceleration measurements were performed at measuring points placed underneath the bridge. The strain measurements were used to identify the respective train type and its crossing velocity. Crucial for the identification of the train type and respective velocity is the knowledge of the carriage formation (number and order of engines, passenger coaches, etc.) and the length over buffers of each component. In the paper the methods used are presented and examples of the automatically identified train types are given by illustrations of measurements. KEY WORDS: Railway bridge, Long term monitoring, Train induced vibrations, Filler beam bridge. 1 INTRODUCTION Three options for the identification of a train type are Permanent or long term monitoring systems of railway provided. At least one of them has to be defined to enable the bridges are installed for various reasons, e.g. surveillance of automatic train identification. critical structural members or research of dynamic behaviour of bridges subjected to crossing train loads. Certain bridge 1. Determination of total number of local maxima. reactions, e.g. resonance phenomena are of special interest. 2. Definition of system reaction. These have to be associated with crossing train types and 3. Comparison of the measured train passage characteristic crossing velocities. If train type and velocity can be directly to a reference characteristic. derived from the measured bridge reaction, no additional measurements of the velocity and comparison of time tables to The first method was already part of [3]. As can be easily seen identify the train type are required. when comparing the characteristics of passenger trains to the As presented in [1] a long term monitoring system was characteristics of freight trains in the following sections, installed on German filler beam twin bridge Erfttalstraße as method 1 is only valid for freight trains. These trains consist part of a European research project [2]. The single span bridge of higher numbers of carriages and thus cause a higher consists of two decks separated by a longitudinal gap but with number of local maxima. Passenger train types usually have a continuous ballast layer. The monitoring system consists of lower numbers of carriages similar to each other. On the other four measuring rows with eleven measuring points each, hand comparison to a reference characteristic cannot be used placed underneath the two bridge decks. Each deck carries for the identification of freight trains as they differ very much one track. Longitudinal strain and tri-directional acceleration in their carriage configurations. measurements were carried out. An analysis routine [3] was The second method requires a definition of the train developed which included the algorithm given in [1] to configuration. Each train consists of a defined number of calculate bridge deformations from strain measurements. The carriages, each with specific carriage “length over buffers” routine was expanded [4] and now includes amongst other (Figure 1), which are arranged in a certain order. In [4] four functions an automated train type identification which is carriage types were defined: presented in this paper. r engine 2 METHODS b end vehicle c centre coach The routine [4] uses strain measurements obtained during v centre coach with speed determination train crossings (in the diagrams in section 3 depicted in red) for the train type identification. The subsequent free decay Several carriages of one type in a row can be combined in one process and ambient oscillations before and after the command. The definition of a centre coach with speed excitation are illustrated in blue. 2193 Proceedings of the 9th International Conference on Structural Dynamics, EURODYN 2014 determination is as follows, the definition of the other carriage high-speed trains passing over the bridge. Maximum speeds types can be carried out analogously. are limited to 250 km/h. Furthermore there is local traffic and freight transportation as well as individual engines. v[<number of wagons>](<length over buffers>) The diagrams given in this section show typical examples of {<normalised exciter amplitude average>} reactions to trains crossings. The numbered pink dots mark the local maxima which are used for the estimation of the crossing speed. As the carriage lengths are known (except for freight trains and single engines) the velocity can be easily calculated. Only centre coaches with the same “lengths over buffers” are considered for the estimation of the crossing speed. Figure 1. Illustration of “length over buffers” and position of axle loads 3.1 ICE 1 ICE 1 can drive with velocities up to 280 km/h, which The normalised exciter amplitude average has to be defined exceeds the speed limit of 250 km/h. Configurations with up as a train with n carriages always causes a minimum of n + 1 to 14 coaches are possible, the respective axis-centre distances local maxima. Figure 2 shows schematically the train type and design loads are given in [6], as well as the “length over definition. The exciter amplitudes are illustrated in light blue, buffers” of 26.4 m of the centre coaches. The ICE 1 used the normalised averages in red. The example in Figure 2 between Aachen and Cologne consists of six centre coaches, shows the reaction (nine local maxima) to a train consisting of one control car and one engine. Using the second method eight coaches. introduced in section 2 it can be defined as follows: Table 1. ICE 1 configuration r [1] (19.78) {0.9} c [1] (26.4) {0.85} v [5] (26.4) {0.75} b [1] (24.9) {0.7} Figure 2. Illustration of train type definition [4] Of the six centre coaches the latter five are suited for the The number of local maxima strongly depends on the speed estimation; the resulting six local maxima used by the crossing velocity. A higher velocity leads to a smaller number routine [4] are numbered in the diagrams. of local maxima (minimum n + 1). At a low speed the system can respond to single axle loads while at higher velocities one local maximum combines the reactions to several axle loads. This circumstance also affects method 3. There reference characteristics are defined. Measured reactions caused by known train types are stored at a database and new measurements can be compared with them. The reference reaction with the smallest difference defines the most probable train type. The routine [4] has a graphical user interface where the results obtained can be checked by the user. At this point the user can control and if necessary adjust automatically Figure 3. Measured strains due to an ICE 1 train crossing [4] determined indexes, e.g. the points defining beginning and end of the train crossing. In the strain diagrams in section 3 these are the red dots. Furthermore falsely determined train types can be revised before further analyses or eliminated from the overall assessment. Not all measured data are suited for further evaluation, e.g. sometimes both decks are crossed at the same time by trains with opposite direction of travel. Reactions cannot be assigned to one crossing train as both decks influence each other. 3 CONSIDERED TRAINS Figure 4. Measured strains due to an ICE 1 train crossing [4] The bridge Erfttalstraße is located between Cologne and Aachen and thus part of the European railway network Comparison of Figure 3 and Figure 4 shows that ICE 1 connecting Germany e.g. with Brussels, Paris or London. trains are used with the engine in front as well as at the end of Currently Inter-City-Express ICE and Thalys are the only the train (pull/push operation). The defined routines always 2194 Proceedings of the 9th International Conference on Structural Dynamics, EURODYN 2014 check both directions. The durations of the train crossings and thus the crossing velocities differ slightly (Figure 3: v = 46.65 m/s = 168k km/h; Figure 4: v = 41.8 m/s = 150.6 km/h; Figure 5: v =28.5 m/s = 103 km/h). All figures show the respective reaction on the loaded deck; in case of Figure 3 this is the south bridge deck, while the other two show reactions on the north deck. Figure 7. Measured strains due to an ICE 3 train crossing [4] Figure 5. Measured strains due to an ICE 1 train crossing [4] 3.2 ICE 3 ICE 3 trains basically can be put to many different coach configurations.
Details
-
File Typepdf
-
Upload Time-
-
Content LanguagesEnglish
-
Upload UserAnonymous/Not logged-in
-
File Pages6 Page
-
File Size-