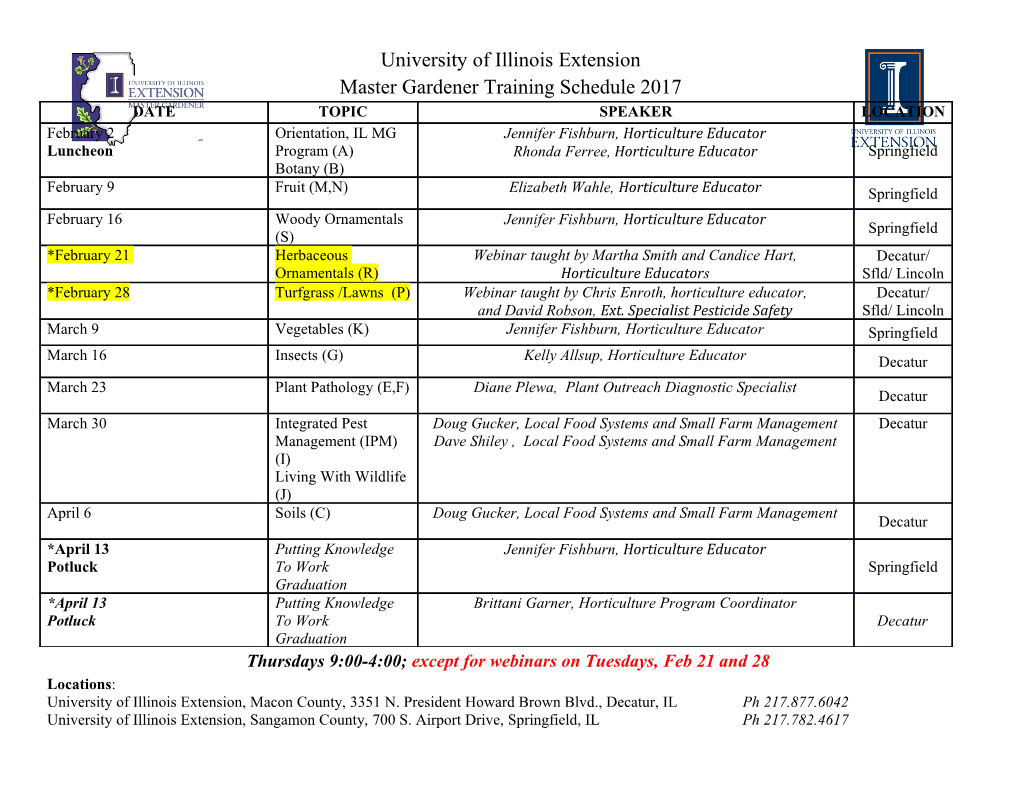
ABOUT WINMAX MILL HELP WinMax Mill v070.01.03 ©2007 www.hurco.com Hurco Companies, Inc. 30 August 2007 v07.01.03 Revision A WINMAX™ Welcome to WinMax On-screen Help System! The information in this on-screen Help is subject to change without notice and does not represent a commitment on the part of Hurco Companies, Inc. (Hurco). Hurco products and services are subject to Hurco’s current prices, terms, and conditions, and are subject to change without notice. The software described in this document is furnished under the License Agreement to customers. It is against the law to copy the software on any medium except as specifically allowed in the license agreement. The purchaser may make copies of the software for backup purposes. No part of this document may be reproduced or transmitted in any form or by any means, electronic or mechanical, including photocopying, for any purpose without the express written permission of Hurco. © 2007 Hurco Companies, Inc. All rights reserved. Patents: U.S. Patents B14,477,754; 5,453,933; Canadian Patent 1,102,434; Japanese Patents 1,649,006 and 1,375,124; other Patents pending. Hurco and Ultimax are Registered Trademarks of Hurco Companies, Inc. UltiPocket and WinMax are trademarks of Hurco Companies, Inc. AutoCAD, Autodesk, and DXF are registered trademarks of Autodesk, Inc. Fanuc is a registered trademark of Fanuc LTD. IBM and PC/AT are registered trademarks of International Business Machines Corporation. Microsoft and Windows are registered trademarks of Microsoft Corporation. Many of the designations used by manufacturers and sellers to distinguish their products are claimed as trademarks. Hurco has listed here all trademarks of which it is aware. 2 - WinMax™ v07.01.03 WinMax Mill Help SAFETY INFORMATION The information provided here is not an exhaustive description of all of the possible misuses of the machine, nor is it a substitute for operator training, skill, and good judgment. Hurco does not accept any liability for operator error. Owner's Responsibility Operator's Responsibility Machine Modifications Safety Hardware and Software Installation Maintenance Part Cutting Part Dimensions & Fixturing Travel Limits Subsystem Failure WinMax Mill Help v07.01.03 Safety Information — 3 MACHINE AND CONSOLE BASICS Machine Tool Components Because of CE requirements, Hurco machining centers sold in Europe differ somewhat from those sold elsewhere. The figures below identify some of the easily recognizable components of a machining center. The console is in front of the machine, facing the operator’s area. Communications Panel Each machining center may be connected to peripheral devices, using a connector plate located on the machine’s electrical cabinet. This section describes the connectors and other options available for each machine type. The connector plate may contain an optional servo-use counter, which records machine usage in hours. An optional cabinet light is positioned above the remaining connectors. Communication connectors may include two serial ports and two network connectors (refer to the illustration below). The BNC network connector is used for 10Base2, thin coaxial network cabling. The RJ45 connector is used for 10BaseT, unshielded twisted pair network cabling. The circular plug in the center of the plate connects to optional indexer equipment. 4 - Machine and Console Basics v07.01.03 WinMax Mill Help Spindles Tools must first be manually loaded into the spindle, then the Automatic Tool Changer (ATC) takes the tool from the spindle and loads it into the magazine. Refer to the Automatic Tool Changers and Tools for information about ATC operation. Loading a Tool into the Spindle Use this procedure to load a tool into the spindle: 1. Press the Manual Machine Mode button to prevent the ATC from moving while you insert a tool. 2. Press the Orient Spindle softkey to position the spindle for tool insertion or removal. If there is a tool in the spindle, refer to Removing a Tool from the Spindle. 3. While pressing the In button, insert the tool holder into the spindle. Make sure the tool holder slots align with the spindle head guides. (Refer to Tool Holder) 4. Release the Spindle Unclamp button to secure the tool in the spindle. Be certain that the tool is firmly seated. 5. Press the Tool In Spindle softkey on the Manual screen. 6. Make sure the tool number in the Tool In Spindle field matches the number of the tool in the spindle. (If the numbers do not match, enter the correct tool number.) 7. Calibrate the tool in the spindle as described in Tool Setup. A Manual tool is any tool that is not currently in the ATC Map. A Manual tool must be manual inserted into, and removed from the spindle – it is not placed in the ATC magazine. If you want a Manual tool loaded into the ATC magazine (and tracked by the ATC Map), you must convert it to an Auto tool in Tool Setup. An Auto tool is any tool currently listed in the ATC Map. Unloading a Tool from the Spindle To manually remove a tool from the spindle, follow these steps: 1. Hold the tool to prevent it from dropping. 2. Press the Spindle Unclamp button. The tool will disengage. 3. Pull the tool out of the spindle. 4. Release the Spindle Unclamp button when the tool is free. WinMax Mill Help v07.01.03 Machine and Console Basics — 5 Types of ATC Changers Many Hurco machining centers are equipped with an automatic tool changer (ATC). Tool changers stations are numbered, the control uses these stations to identify and keep track of the tools. Swing-Arm Tool Changer Horizontal Chain Type Loading Tools into the Tool Changer Tools should be loaded into the magazine from the spindle, whether using manual or automatic mode. Do not manually load tools into a magazine without using the spindle. A significant amount of force is required to manually insert or remove a tool from the tool pot and could result in injury to the operator or damage to the machine. The Tool In Spindle (displayed in the Input and Tool Setup screens) should always match the tool being calibrated. Removing Tools from the Tool Changer Remove all tools from the magazine before loading new tools by following these steps: 1. Press the Manual Machine Mode button. 2. Select the Tool In Spindle softkey to access the Tool In Spindle screen. If there is no tool in the spindle, set the Tool In Spindle field to zero (0). 3. Enter a tool number into the Next Tool field for the tool currently in the magazine that you want to remove. 4. Press the Auto Tool Change key on the console. This will place the next tool into the spindle. Clear the tool changer area and shut the enclosure door before pressing the Start Cycle. 5. Press the Start Cycle button to initiate the tool change. 6. Remove the tool using the Spindle Unclamp button. 7. Set the Tool In Spindle field to zero. 8. Enter a tool ID number in the Next Tool field. The ATC Map field will indicate if the tool selected is in the ATC magazine and its location. 6 - Machine and Console Basics v07.01.03 WinMax Mill Help CONSOLE The console and the electrical components required to operate it are called the "control" or the "CNC" (Computer Numeric Control). Some of the electrical components are built into a separate enclosure, which is kept in the machine tool’s electrical cabinet. Some of the control’s internal components, such as disk drives and memory, are like those in a PC. Disk operations, such as copying, deleting and storing files, are also similar. There is a floppy drive on the right-hand side panel of the control. Control Panel Functions Control Panel Function Programming Keyboard with Graphics Trackball Axis, Spindle, and Machine Control Machine Operations Remote Jog Unit WinMax Mill Help v07.01.03 Console — 7 The Power On button, Emergency Stop buttons, and brightness control thumbwheels for the Text and Graphics screens are located on the machine console. Some consoles are also equipped with contrast control thumbwheels. Programming Input WinMax allows you to program a job at the machine while reading directly from a blueprint or a program worksheet. The prompts on the text screen lead you through each element of the part program, allowing you to enter machine operations, part dimensions, and other parameters into the control’s memory. Respond to the various selections and prompts by pressing the appropriate screen softkeys and console buttons. Data entry keys allow you to set up and run part programs, and manage part program files. There are different types of data entry keys used for programming: Text Screen Data Entry Softkeys Numeric Keypad Virtual Keyboard Optional Computer Keyboard Graphics Screen Data Entry 8 - Console v07.01.03 WinMax Mill Help Virtual Keyboard The Virtual Keyboard is a graphical keyboard that looks and acts like a real keyboard. To access the Virtual Keyboard, touch the keyboard icon at the bottom of the screen. Axis, Spindle and Machine Control The following console keys and knobs are used to control movement and adjust the spindle and axes. Override Knobs Machine Control Keys Remote Jog Unit Emergency Stop Buttons There is an Emergency Stop button located on the console and a second one on the Remote Jog Unit. Press the Emergency Stop button to stop all spindle and table motion. A message appears on the screen indicating the Emergency Stop button was pressed. Using this shutdown method is not good for the machining center, especially if the table is long and has heavy equipment attached to one end. The table should be centered using the parking shut down method to equally distribute the weight of the table and any equipment.
Details
-
File Typepdf
-
Upload Time-
-
Content LanguagesEnglish
-
Upload UserAnonymous/Not logged-in
-
File Pages482 Page
-
File Size-