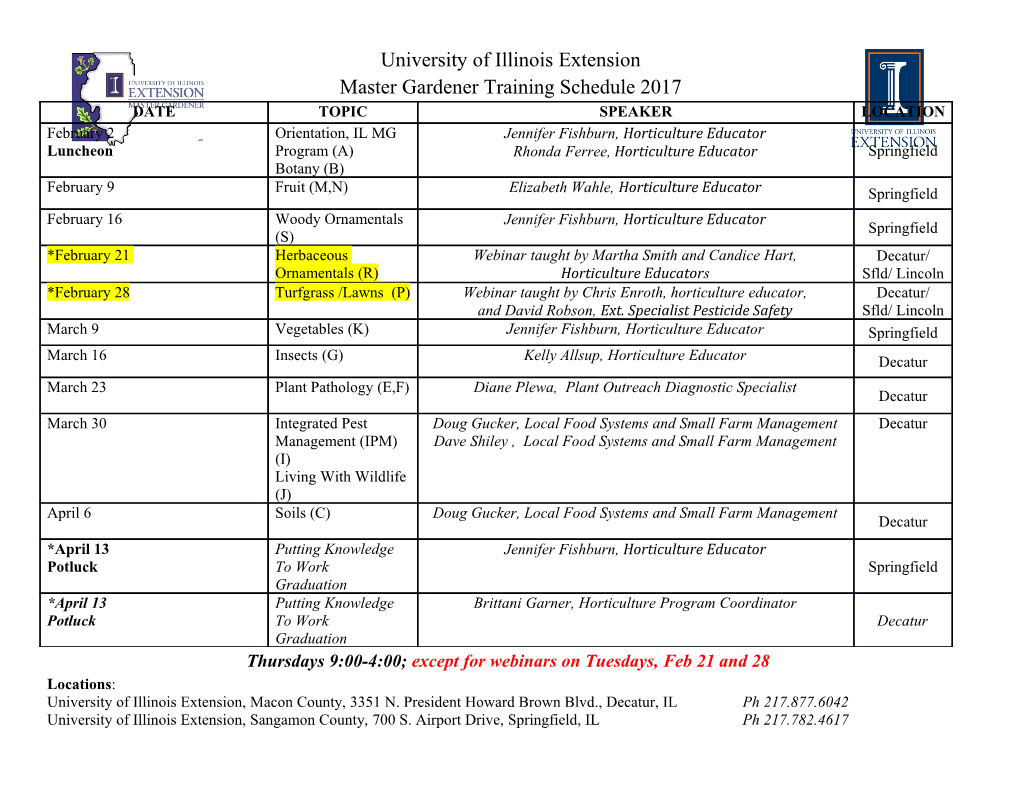
nanomaterials Review The Fabrication of Micro/Nano Structures by Laser Machining Liangliang Yang 1,2, Jiangtao Wei 1,3, Zhe Ma 1,2 , Peishuai Song 1,3, Jing Ma 1,2 , Yongqiang Zhao 1,2, Zhen Huang 1,2, Mingliang Zhang 1,2, Fuhua Yang 1,2,4,6 and Xiaodong Wang 1,2,4,5,6,* 1 Engineering Research Center for Semiconductor Integrated Technology, Institute of Semiconductors, Chinese Academy of Sciences, Beijing 100083, China; [email protected] (L.Y.); [email protected] (J.W.); [email protected] (Z.M.); [email protected] (P.S.); [email protected] (J.M.); [email protected] (Y.Z.); [email protected] (Z.H.); [email protected] (M.Z.); [email protected] (F.Y.) 2 College of Materials Science and Opto-Electronic Technology, University of Chinese Academy of Sciences, Beijing 100049, China 3 School of Electronic, Electrical and Communication Engineering, University of Chinese Academy of Sciences, Beijing 100190, China 4 Beijing Academy of Quantum Information Science, Beijing 100193, China 5 School of Microelectronics, University of Chinese Academy of Sciences, Beijing 100190, China 6 Beijing Engineering Research Center of Semiconductor Micro-Nano Integrated Technology, Beijing 100083, China * Correspondence: [email protected] Received: 11 November 2019; Accepted: 12 December 2019; Published: 16 December 2019 Abstract: Micro/nano structures have unique optical, electrical, magnetic, and thermal properties. Studies on the preparation of micro/nano structures are of considerable research value and broad development prospects. Several micro/nano structure preparation techniques have already been developed, such as photolithography, electron beam lithography, focused ion beam techniques, nanoimprint techniques. However, the available geometries directly implemented by those means are limited to the 2D mode. Laser machining, a new technology for micro/nano structural preparation, has received great attention in recent years for its wide application to almost all types of materials through a scalable, one-step method, and its unique 3D processing capabilities, high manufacturing resolution and high designability. In addition, micro/nano structures prepared by laser machining have a wide range of applications in photonics, Surface plasma resonance, optoelectronics, biochemical sensing, micro/nanofluidics, photofluidics, biomedical, and associated fields. In this paper, updated achievements of laser-assisted fabrication of micro/nano structures are reviewed and summarized. It focuses on the researchers’ findings, and analyzes materials, morphology, possible applications and laser machining of micro/nano structures in detail. Seven kinds of materials are generalized, including metal, organics or polymers, semiconductors, glass, oxides, carbon materials, and piezoelectric materials. In the end, further prospects to the future of laser machining are proposed. Keywords: micro/nano structures; micro/nano fabrication; femtosecond laser; laser machining; mental; semiconductor; material; application 1. Introduction Richard Feynman (Nobel Laureate in Physics) gave a famous lecture called “There’s Plenty of Room at the Bottom” which stimulated numerous research projects about the fabrication of micro/nano structures in 1959 [1]. The micro/nano structures are an artificial structure with special features, dimensions, levels, and physical properties on the micro-nano scale [2]. Compared with bulk materials, Nanomaterials 2019, 9, 1789; doi:10.3390/nano9121789 www.mdpi.com/journal/nanomaterials Nanomaterials 2019, 9, 1789 2 of 69 micro/nano structured materials have different properties. For example, the nanocrystal hardness of copper is 5 times that of bulk materials, and ceramic materials become materials that are easily deformed after reaching nanometer size [3]. In the past 20 years, micro/nano structural materials have had several application fields. In bionics, it is possible to mimic nanomaterials, nanodevices that provide the desired properties in biology or nature. For example, according to the “Lotus Effect”, a natural biomimetic artificial surface having superhydrophobicity, self-cleaning property, low adhesion, and drag reducing property is prepared [4–8]. In the field of biomedicine, micro/nano functional scaffolds for in vitro cell culture are used to mimic a physiological/pathophysiological environment. The artificially controllable micro/nano 3D environment provides a platform for cell biology research and clinical transplantation research which has great research prospects [5,8–10]. In the field of materials science, 3D micro/nano structured metamaterials have been designed and manufactured with reasonable mechanical properties [11]. Manipulating fluids in tens of micron-sized channels (microfluidic) has become a unique new field. Microfluidic technology has the potential to influence disciplines ranging from chemical synthesis and biological analysis to optical and information technology [12–18]. Therefore, the development of microfluidic technology is the product of the development of micro/nano technology. In microelectronics, micro electro mechanical systems (MEMS) and nano electro mechanical systems (NEMS) implement many different microsensors, microactuators, and microsystems. Its mature commercial products include silicon pressure sensors, micro accelerometers, micro gyroscopes, etc., which are widely used in automobiles, mobile phones, and video games [1,19,20]. In addition, micro/nano structured materials are also widely used in photonics, plasma, optoelectronics, photofluidics, and other fields [21]. The preparation of micro/nano structural materials is inseparable from the advanced micro/nano processing technology. For example, photolithography, X-rays, electron beams, ion beams, particle beams, and mechanical methods. Lithography has achieved unique success in creating the ability to create 2D patterns in the range of 10 nanometers to a few microns [22–31], and is a key technology that has enabled Moore’s Law to expand and revolutionize computing power [32]. Nanoimprinting or injection printing produces a pattern by mechanical deformation of the imprinted resist or by pushing droplets of variable size liquid material (ink) or powder onto the substrate [33]. Despite having nanoscale resolution, the available geometries directly achieved by these means are typically limited to 2D mode. Manufacturing a three-dimensional structure on this length scale has a more challenging prospect [16,34–37]. In recent years, laser machining has received extensive attention as a new technology for the fabrication of micro/nano structures. The term laser was first proposed in 1957 and represents light amplification by stimulated radiation emission [38]. In 1960, Maiman built the first functional laser at the Hughes Research Laboratory [39]. Laser interaction with matter results in material removal and ultimately formation of micro/nano structures. Since then, lasers have been widely used in a range of scientific and technical fields, and laser-assisted preparation of micro/nano structured functional materials is one of the most important applications. In 1987, Srinivasan et al. first reported the use of ultrafast lasers (lights emitted with pulses shorter than tens of picoseconds) for material processing. Femtosecond (fs) laser micromachining was first demonstrated in 1994 when femtosecond lasers were used to ablate the micron-scale features of silica and silver surfaces. Since 1996, Davis et al. published, for the first time, reports of fs laser writing waveguides in glass. Femtosecond lasers have certain advantages over other longer pulsed lasers, such as nanosecond or picosecond lasers. A key feature of the fs laser is the ability to emit high-intensity pulses in a very short period of time, allowing precise ablation of the material and formation of small heat affected zones. Therefore, nano resolution and accuracy are possible. Compared to other micro/nano structured material preparation methods, laser micromachining has several advantages [16,38,40–42]: (1) simpler equipment; no vacuum or clean room facilities required; (2) capable of handling almost all types of materials, including metals, semiconductors, glass, and polymer; (3) Many parameters can be easily adjusted to produce a variety of possible structures. (4) This procedure applies to the surface of any 3D object. Understanding Nanomaterials 2019, 9, 1789 3 of 69 the physical mechanisms of laser machining provides guidance for the preparation of structures with controlled morphology and good quality. The first step in the interaction of the laser with matter is electron absorption of photons. Linear absorption is the primary absorption mechanism of metals, while for semiconductors, dielectrics, and insulators, nonlinear absorption is dominant. The corrugations formed by long laser pulses and continuous wave (CW) illumination are similar to Wood’s anomalies (1902): diffraction of metal gratings at oblique incidence, which can be interpreted according to the surface interpretation proposed by Lord Rayleigh [43,44]. For the ripple generated by short laser pulses, people are still arguing. The details of the process depend on the laser intensity, pulse duration, laser wavelength, and material properties. The physical mechanism is not fully understood. The main ablation mechanisms of fs laser machining are phase explosion, critical phase separation, fragmentation, spallation, melting, vaporization, and Coulomb explosion. The short pulse laser ablation mechanism needs further understanding [38,45]. A more detailed
Details
-
File Typepdf
-
Upload Time-
-
Content LanguagesEnglish
-
Upload UserAnonymous/Not logged-in
-
File Pages69 Page
-
File Size-