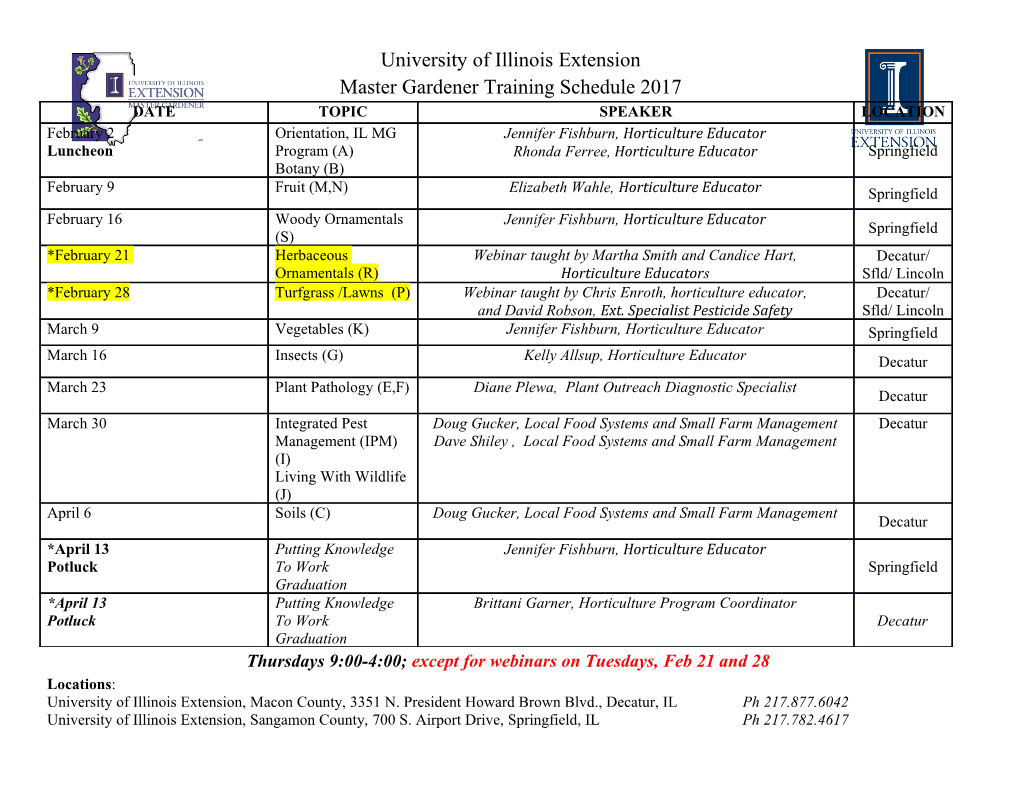
*Manuscript Click here to download Manuscript: manuscript_26Feb.tex Click here to view linked References 1 2 3 4 5 Ultrasonic bandgaps in 3D-printed periodic ceramic 6 microlattices 7 8 a a a, a b 9 Alena Kruisova´ , Martin Sevˇ cˇ´ık , Hanusˇ Seiner ∗, Petr Sedlak´ , Benito Roman-Manso´ , 10 Pilar Miranzoc, Manuel Belmontec, Michal Landaa 11 12 aInstitute of Thermomechanics, Czech Academy of Sciences, Dolejskovaˇ 5, 18200 Prague, Czech Republic. 13 bSchool of Engineering and Applied Sciences, Harvard University, 14 52 Oxford St, 02318 Cambridge MA, USA 15 c 16 Institute of Ceramics and Glass (ICV-CSIC), Campus de Cantoblanco, Kelsen 5, 28049 Madrid, Spain 17 18 19 20 21 Abstract 22 23 The transmission of longitudinal ultrasonic waves through periodic ceramic microlattices 24 25 fabricated by Robocasting was measured in the 2 12 MHz frequency range. It was ob- 26 − 27 served that these structures (scaffolds of tetragonal and hexagonal spatial arrangements 28 29 with periodicity at length-scales of 100µm) exhibit well-detectable acoustic band struc- 30 ∼ 31 tures with bandgaps. The locations of these gaps were shown to be in close agreement 32 33 with the predictions of numerical models, especially for the tetragonal scaffolds. For the 34 35 hexagonal scaffolds, a mixing between longitudinal and shear polarizations of the prop- 36 37 agation modes was observed in the model, which blurred the matching of the calculated 38 39 band structures with the experimentally measured bandgaps. 40 Keywords: 41 Phononic crystals; Ceramics; Additive manufacturing; Bandgaps; Wave 42 propagation; Finite elements method. 43 44 45 Robocasting [1, 2, 3] is an additive manufacturing technique that enables fabrication 46 47 of micro-architectured three-dimensional (3D) scaffolds consisting of ceramic micro-rods 48 49 in periodic spatial arrangements. These scaffolds are typically developed for particular 50 51 applications such as bone tissue engineering [4, 5] or advanced liquidfiltering [6]; how- 52 53 ever, the high acoustic performance of dense ceramic materials in combination with the 54 periodicity of the micro-architecture of the scaffold predetermines the robocast structures 55 56 also for applications in acoustics. 57 58 59 Corresponding author, [email protected] 60 ∗ 61 62 63 Preprint submitted to Ultrasonics March 2, 2017 64 65 1 2 3 4 As previously shown by the current authors [7], tetragonal robocast scaffolds ex- 5 6 hibit extremely strong elastic anisotropy, accompanied by equivalently anisotropic ef- 7 8 fects in the acoustic wave propagation. In addition, due to the periodicity, a pronounced 9 10 frequency-dependence of the acoustic wave propagation can be expected, as some spe- 11 12 cific frequencies of the propagating waves may induce internal resonances of the struc- 13 14 ture, which prevents the acoustic energy from being transmitted through the scaffold. 15 16 Hence, the existence of the so-called frequency bandgaps (BGs) typical for acoustic meta- 17 18 materials [8, 9, 10] or phononic crystals [11, 12, 13, 14] can be theoretically expected for 19 20 the scaffolds. Indeed, the appearance of these gaps in tetragonal robocast structures was 21 22 recently predicted byfinite elements calculations [7, 15]. 23 24 In this paper, we give experimental evidence of the existence of acoustic BGs for sil- 25 26 icon carbide (SiC) scaffolds of various micro-architectures and symmetry classes. We 27 28 show that the BG structure can be reliably predicted byfinite elements calculations, es- 29 30 pecially for scaffolds with highly symmetric (tetragonal) spatial arrangements. The main 31 aim of this paper is, however, to show experimentally that the acoustic energy transmis- 32 33 sion through a robocast scaffold is strongly dependent on the micro-architecture, which 34 35 opens the possibility of tuning this architecture in order to achieve the desired acoustic 36 37 filtering properties. As shown by Liu et al. [16, 17] and Kuang et al. [18], the struc- 38 39 ture and width of acoustic BGs of a porous material with geometrically ordered pores are 40 41 strongly dependent on the shape of the pores and their volume fraction. In principle, the 42 43 Robocasting method enablesfine tailoring of both the porosity and the geometry of pores. 44 45 There have been several experimental demonstrations of phononic crystals reported in 46 47 the literature so far [19, 20, 21, 22], typically exhibiting bandgaps in a 100 Hz 100 kHz 48 − 49 frequency range, as the spatial periodicity in these structures appeared at the millimeter 50 51 (or even longer) length-scales. In contrast, the robocast scaffolds reported in this paper 52 53 have the periodicity at approximately ten to hundred times smaller characteristic length- 54 55 scales; this, together with the high acoustic impedance of fully dense ceramics, enables 56 57 the robocast materials to exhibit BGs and other metamaterial-like features at ultrasonic 58 frequencies 5 10 MHz, which has rarely been reported in the literature yet [23]. 59 ∼ − 60 61 62 63 64 2 65 1 2 3 4 1. Experimental 5 6 1.1. Materials 7 8 9 The examined SiC micro-scaffolds were fabricated by Robocasting using a similar 10 11 additive manufacturing process as described in [3, 24]. In brief, an aqueous colloidal 12 13 paste (containing attrition milled SiC powders with 7 wt.% Al2O3 and Y2O3 sintering 14 additives plus organic additives) was printed through a robotically controlled nozzle into 15 16 an oil bath, so that a regular architecture was obtained layer-by-layer, consisting of a 17 18 linear array of parallelfilaments in each layer. By different mutual rotations between 19 20 these layers and different spacings between the rods, four different micro-architectures 21 22 were obtained, according to CAD computer designs shown in Fig.1(a). Two samples were 23 24 of tetragonal symmetry (LS and SS), differing only in the in-plane spacings between the 25 26 rods; similarly, two samples were of hexagonal arrangements (LH and SH). Hereafter, we 27 28 will use the acronyms (LS, SS, LH, and SH) to denote the samples. 29 30 Each structure was then slowly dried at room temperature and subsequently heat 31 32 treated at 600 ◦C to burn out the organic additives. As afinal step, the 3D structures were 33 34 densified by pressureless Spark Plasma Sintering (SPS) at 1700 ◦C in Ar. As shown in 35 36 [24], these sintering conditions lead to full densification of the ceramic materials. Scan- 37 38 ning Electron Microscopy (SEM) images and optical micrographs of thefinal sintered 39 40 micro-lattices are shown in Figs. 1(b) and 1(c), respectively. From the four prepared 41 42 micro-architectures, samples for ultrasonic measurement were prepared by cutting out 43 the non-periodic parts of the scaffolds (Fig. 1(d)). 44 45 46 1.2. Experimental Methodology 47 48 The acoustic properties of the samples were studied using a through-transmission 49 50 method (see Fig.2 for an outline). Each sample was contacted by a CrystalBond wax 51 52 onto two 0.5 mm thin glass plates to ensureflat co-planar faces for contacting of ultra- 53 54 sonic probes. 55 56 Then, narrow-band longitudinal ultrasonic pulses were sent through the sample, each 57 58 consisting of ten harmonic periods at given frequency inside of an amplitude-envelope 59 60 (’input signal’ curve in Fig.2). Glass plates were always glued onto two lateral faces of 61 62 63 64 3 65 1 2 3 4 5 6 7 8 9 10 11 12 13 14 15 16 17 18 19 20 21 22 23 24 25 26 27 Figure 1: The four different micro-architectures used in the experiments: (a) initial computer CAD designs; 28 (b) SEM images of the resulting sintered architectures; (c) optical micrographs of these architectures; (d) 29 samples for ultrasonic measurements cut from the central parts of the robocast structures. 30 31 32 the sample and oriented such that they enabled measurements of waves propagating along 33 34 one of the orientations of the rods. According to the coordinate system outlined in Fig.1, 35 36 the measurements were performed in thex 1 direction for all samples. 37 38 For the generation of the input signals and the acquisition of the transmitted signals, 39 40 a National Instruments NI-PXI card system was used, including a functional generation 41 42 card 5422 (16 bits/40 MHz) employed for burst signal generation, and an acquisition card 43 44 5122 (14 bits/100 MHz) for signal recording. The generated as well as the recorded sig- 45 46 47 output signal 48 receiver 49 probe 50 glass bonding 51 wax transmitted amplitude 52 sample 53 glass 54 PMMA bu� er 55 source 56 probe 57 58 input signal 59 60 Figure 2: Outline of the experimental set-up. 61 62 63 64 4 65 1 2 3 4 5 6 7 8 9 10 11 12 13 14 15 16 17 18 19 Figure 3: Results of a preliminary reference measurement for a bulk plexiglass sample. The solid (blue) 20 line is a plot the transmitted amplitude with respect to the set input frequencyf in of the transmitter probe, 21 the vertical (red) bars represent the plot of the same amplitude with respect to the dominant frequency of 22 the output signalf out. 23 24 25 nals were amplified by a high power ultrasonic system Ritec RAM 5000. This system was 26 27 equipped by a gated amplifier (nominal frequency range 50 kHz - 22 MHz, output RMS 28 29 power 5 kW at 50 ohms/2.5 MHz) and a broadband receiver (frequency band 40 kHz - 30 / 31 80 MHz 72dB gain).
Details
-
File Typepdf
-
Upload Time-
-
Content LanguagesEnglish
-
Upload UserAnonymous/Not logged-in
-
File Pages20 Page
-
File Size-