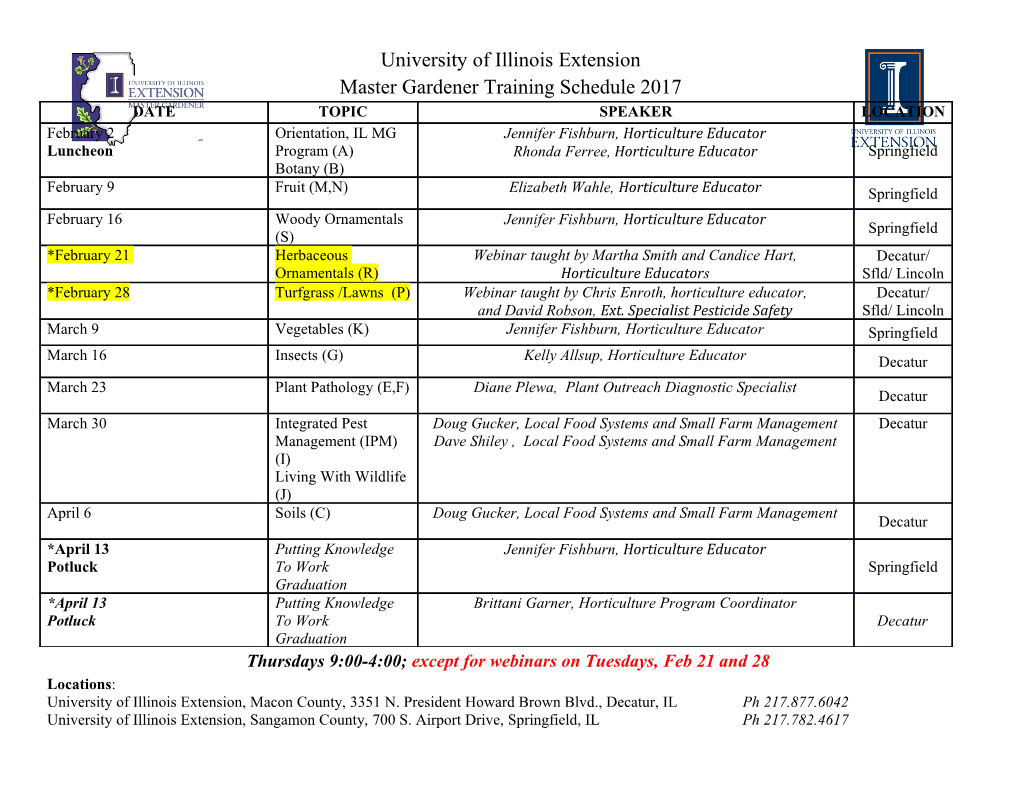
WELDING RESEARCH m SUPPLEMENT TO THE WELDINC JOURNAL, MARCH 1986 Sponsored by the American Welding Society and the Welding Research Council Readers are advised that all papers published in the Welding Journal's Research Supplement undergo Peer Review before publication for: 1) originality of the contribution; 2) technical value to the welding community; 3) prior publication of the material being reviewed; 4) proper credit to others working in the same area; and 5) justification of the conclusions based on the results. The names of the more than 160 individuals serving on the AWS Peer Review Panel are published periodically. All are experts in their respective technical areas, and all are volunteers in the program. Development of a Weldability Test for Pulsed Laser Beam Welding Relatively easy test can predict cracking sensitivity in laser beam welded alloys BY L. A. WEETER, C. E. ALBRIGHT AND W. H. JONES ABSTRACT. A weldability test designed a rating of a material's weldability is dency to hot crack (Refs. 1, 2). However, specifically for small component pulsed obtained. The results of the 796 data none of these previously developed tests laser beam welding was developed and points collected were consistent and consider the unique characteristics of tested on thirteen alloys and two dissimi­ reproducible. A crack susceptible alloy pulsed laser beam welding. lar alloy combinations. The weldability will begin to crack at a much smaller Pulsed laser beam welds are smaller test consists of drilling small holes of cavity depth than a crack insensitive alloy, and cool much more rapidly than other various diameters (0.343-0.572 mm/ due to the inability of the susceptible types of welds. As a result of the small 0.013-0.023 in.) and depths (0.127-0.508 alloy to cope with the increased degree sizes, low residual stresses are produced mm/0.005-0.02 in.) in the alloys or of restraint and solidification stresses of in pulsed laser beam weldments. These between the dissimilar alloys. Then, a the deeper cavities. low magnitude residual stresses reduce single YAG laser pulse is impinged directly The pulsed laser beam weldability test the effectiveness of the self-restraining on each of the drilled holes. The absence rated the alloys and alloy combinations weldability tests (Ref. 2) (such as the of metal in the hole causes the solidified from least crack sensitive to most crack circular patch and T-joint tests) in rating spot weld to have a concave contour. sensitive as follows: Hastelloy B2, Hastel­ the cracking sensitivity of alloys. The Varying the diameter and depth of the loy S, Hastelloy C4, stainless 304A, stain­ rapid cooling rates of pulsed laser beam drilled holes changes the depth of the less 304B, Inconel 625, Inconel 718, stain­ welds also reduce the accuracy and con­ cavity produced in the spot weld. By less 316A, stainless 316B, stainless 310, sistency of the augmented strain weld­ recording the depth of the cavity at Modified Inconel 600, stainless 330, Has­ ability tests (Ref. 2) (such as the Vares­ which the alloy exhibits incipient cracking, telloy X. traint and Murex tests). The application of Dissimilar alloy results indicated that strain at a reproducible instance in a Hastelloy B2 joined to modified Inconel weld's solidification cycle is critical for the 600 was a crack insensitive combination, accuracy of the augmented strain tests. L A. WEETER and W. H. JONES are with while stainless 304(A) to Inconel 718 was Pulsed laser beam welds cool so rapidly Monsanto Research Corporation, Miamisburg, crack sensitive. that the accurate, reproducible applica­ Ohio. Monsanto Research Corporation is tion of strain during solidification is not operated for the U. S. Department of Energy feasible. under contract No. DE-AC04-76-DP00053. Introduction C. E. ALBRIGHT is with The Department of In addition, pulsed laser beam welds Welding Engineering, Ohio State University, Many weldability tests have been are usually made on small components Columbus, Ohio. developed for evaluating an alloy's ten­ which are fabricated from small bars or WELDING RESEARCH SUPPLEMENT 151-s pools is very similar to the solidification of weld craters. Depending on the circumstances, either increased segregation (Ref. 10) or lack of sufficient flow to fill the round crater (Ref. 10) can be responsible for crater cracking. For whatever reason, it is widely documented (Refs. 10, 11) that unless proper welding techniques are implemented, even a normally weldable alloy can exhibit crater cracking. Pulsed laser beam welds solidify very similarly to weld craters; thus, pulsed laser beam welds would be expected to be more crack sensitive than continuous wave IBHHHHI welds. Because pulsed laser welding can sig­ nificantly alter the cracking tendencies of alloys, a weldability test specifically designed for small component pulsed f laser beam welding is needed. The objec­ tive of this study was to develop a weldability test for pulsed laser beam Fig. 2 — Various weld pool solidification pat­ welding that would use a small sized weld terns: (A) elliptical (B) tear-dropped (C) round sample and that would be relatively easy B 100X (crater) to perform and evaluate. Fig. 1 — Cross-sections of a (A) continuous wave electron beam weld and a (B) pulsed laser beam weld on the same sample of less steels. They found that in two of the Experimental Procedure stainless 316. Note the extensive cracking in stainless steels, the most rapidly cooled the pulsed laser beam weld areas of the laser beam welds deviated Alloy Composition and Sample Preparation from the expected microstructures. Stain­ Table 1 lists the chemical compositions less type 308, which normally has 5-7% of the alloys used in this study. These ferrite in the final weld microstructure, sheet stock. It is often desirable to evalu­ alloys were chosen for testing because was completely austenitic. Type 312 ate each lot of stock for crack sensitivity most of them are commonly used in stainless steel, which normally has 35- in welding precision components, be­ industry and because they provide a 40% ferrite, was completely ferritic. Vitek cause lot-to-lot metallurgical variations in wide range of hot cracking tendencies. hypothesized that the large undercool­ alloys can cause variations in cracking Arc welding weldability studies and the ings generated in laser beam welding tendency. Many weldability tests use alloy manufacturer's welding information produced massive transformations (Refs. large welding samples; thus, they are not rate the weldability of the alloys (Refs. 4, 5), which modified the microstruc­ easily adaptable to the smaller dimen­ 12-14) in descending order from most to tures. sions encountered in pulsed laser beam least weldable as follows: welding. Molian and Wood (Ref. 6) demonstrat­ Most Weldable The motivation for developing a weld­ ed that laser processing can produce Hastelloy S ability test for pulsed laser beam welding massive transformations in Fe-Cr-Ni Hastelloy B2 was derived through experience at the alloys. The Fe-6%Cr-2%Ni alloy they stud­ Hastelloy C4 Monsanto Research Corporation (Mound ied exhibited a structure of both massive Stainless 304A* Facility). Researchers observed that in ferrite and martensite. Stainless 316A* some cases pulsed laser beam welds tend The effect of massive transformations Inconel 718 to crack more prevalently than other on the crack sensitivity of alloys has not Inconel 625 types of welds. Cross-sections of a con­ been investigated. However, if, as Vitek Stainless 304B* tinuous wave electron beam and a demonstrated, massive transformations Stainless 316B* pulsed laser beam weld are shown in Fig. produce a completely austenitic or ferritic Stainless 310 1. These welds were made adjacent to matrix, massive transformations could Modified Inconel 600 each other on the same sample of stain­ alter the hot cracking tendencies in stain­ Hastelloy X less steel, type 316. Each weld was cross- less steel. Stainless 330 Least Weldable sectioned at four locations and examined. Another possible explanation for the The modified Inconel 600 has an exces­ No cracks were found in any of the increased cracking in pulsed laser beam sive amount of copper (0.41% compared electron beam weld cross-sections, but welds is an alteration of the weld pool to 0.25% maximum for Inconel 600). every cross-section of the pulsed laser shape. Continuous wave welds assume Because of the excess copper, modified beam weld exhibited cracking. At this either an elliptical or a tear-drop shaped Inconel 600 was expected to be crack time, the reason for the increased crack­ pool (Ref. 8)-Figs. 2A, 2B. In both of sensitive. ing in pulsed laser beam welds is not these shapes, growth of the solidification The two stainless 304 alloys and the completely understood. However, it is boundary occurs only from the trailing two stainless 316 alloys were chosen thought that an alteration of the final edge of the weld pool into the liquid. because of the differences in their pre- weld microstructure and/or of the weld Pulsed laser beam welds have a nearly pool shape caused the cracking. round shape, and, when solidification is Vitek, ef al. (Ref. 3), studied the effects complete between pulses, they solidify * These are different alloys with compositions of laser beam welding in modifying the from all sides of the pool —Fig. 2C. The within the specifications for stainless 304 and microstructures of three austenitic stain- solidification of these round individual stainless 316. 52-s | MARCH 1986 Table 1—Chemical Compositions of the Experimental Alloys Alloys C Mn Si Cr Ni Cu Mo Fe Co Ti Al Cb + Ta SN W Q. Stainless 304A .065 .89 .41 .015 .028 18.33 8.20 .44 .45 Bal .15 .052 - - - - - — o -I Stainless 304B .023 1.7 .41 .001 .007 18.3 11.4 , - .04 Bal .04 .037 - - - - - — LU Stainless 310 .050 1.65 .48 .009 .030 25.10 19.90 .22 .26 Bal - .08 - - - - - — > Stainless 316A .050 1.55 .51 .0015 .010 17.8 10.9 2.55 Bal .01 LU — - — - - - - - O Stainless 316B .050 1.46 .44 .021 .017 16.25 13.11 .11 2.23 Bal .04 .065 — - - - - - Mod.
Details
-
File Typepdf
-
Upload Time-
-
Content LanguagesEnglish
-
Upload UserAnonymous/Not logged-in
-
File Pages12 Page
-
File Size-