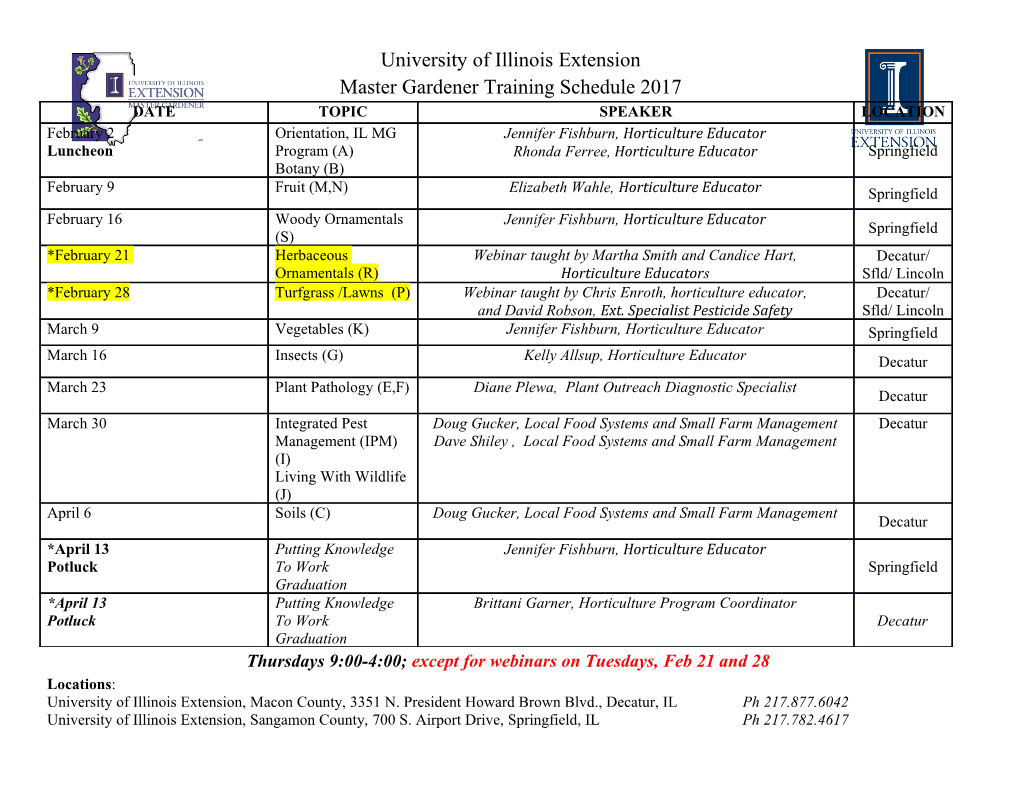
School of Innovation, Design and Engineering Demand Driven Material Requirements Planning Master thesis work 30 credits, Advanced level Product and process development Production and Logistics Arakatla Adarsh Report code: xxxx Commissioned by: Tutor (university): Yuji Yamamoto Examiner: ABSTRACT Manufacturing industries used to develop their operation strategies focusing on cost of manufacturing, high volume production and stabilizing the customer demand. But due to advancements in technology and evolving customer needs, the market demand became highly volatile, dynamic and customers expected customization, low volume products and faster deliveries. This evolution in customer needs has pushed the companies to improve their operating systems to be more flexible, agile and adaptable to market’s dynamic character. In order to effectively evolves themselves and achieve more flexibility, manufacturing companies had to implement effective manufacturing, planning and control systems. The first break through in planning systems came in the year 1975 where a systemic approach called material requirements planning was introduced by Orlicky. MRP has become the global for production planning and inventory management in manufacturing industries. Later, over the years, research on the planning systems has brough modifications in MRP and it was evolved into closed loop MRP. Further into late 1980’s availability of technology led to an introduction of new evolved system called the Manufacturing resource planning which resulted in a holistic approach in material planning involving, financial and accounting functions which improved the planning efficiency. Further advancement in technology resulted in advanced planning systems like Enterprise resource planning and Advanced planning and scheduling. On the contrary, though there has been a lot of advancement in technology and effective production planning methods, there are still discrepancies in obtained results when compared to theory. This is because, the existing systems were based on either solely on push production or pull production strategy. There is a lack of hybrid system which includes the positives of both production strategies and negate the MRP conflict. However, in the year 2011, a new concept called demand driven material requirements planning was introduced by Ptak & Smith, which was a fusion of the core MRP, theory of constraints and Lean principles. Since the introduction DDMRP has seen a increase in implementation across industries which claimed a significant improvement in performance, on-time delivery, reduction in inventory and reduced stock outs. DDMRP has received very less attention in academia due to lack of awareness among researchers and industries. A literature review approach was used to collect and analyze the data on DDMRP and its advantages. The objective of this thesis was to shed light on the process of DDMRP, its pros and cons in implementing the new material planning system. Keywords: Material planning, MRP, Manufacturing resource planning, ERP, Lean, DDMRP ACKNOWLEDGEMENTS I want to express my appreciation and thanks Mr. Yuji Yamamoto, my supervisor at MDH for his help and advice during the thesis. Contents 1. INTRODUCTION .......................................................................................................................................... 6 1.1. BACKGROUND ......................................................................................................................................... 6 1.2. PROBLEM FORMULATION ......................................................................................................................... 8 1.3. AIM AND RESEARCH QUESTIONS .............................................................................................................. 9 1.4. PROJECT LIMITATIONS ............................................................................................................................. 9 2. RESEARCH METHOD ............................................................................................................................... 10 2.1. RESEARCH METHOD .............................................................................................................................. 10 2.2. LITERATURE REVIEW ............................................................................................................................. 11 2.3. DATA ANALYSIS .................................................................................................................................... 11 2.4. VALIDITY AND RELIABILITY .................................................................................................................. 12 3. THEORETIC FRAMEWORK ................................................................................................................... 13 3.1. MANUFACTURING PLANNING AND CONTROL (MPC) ............................................................................. 13 3.2. PLANNING, EXECUTION AND CONTROL ................................................................................................. 14 3.3. MRP NERVOUSNESS AND SUPPLY CHAIN BULLWHIP EFFECT ................................................................. 15 3.4. DECOUPLING AND DECOUPLING POINTS ................................................................................................ 15 3.5. MASTER PRODUCTION SCHEDULE (MPS) .............................................................................................. 16 3.6. MATERIAL REQUIREMENT PLANNING SYSTEM ...................................................................................... 16 3.6.1. MRP Inputs and Outputs .................................................................................................................. 17 3.6.2. Cons of MRP .................................................................................................................................... 17 3.7. MANUFACTURING RESOURCE PLANNING (MRP II) ............................................................................... 19 3.7.1. Pros of MRP II ................................................................................................................................. 21 3.8. JUST-IN-TIME (JIT) ................................................................................................................................ 21 3.9. THEORY OF CONSTRAINTS (TOC).......................................................................................................... 22 3.10. ENTERPRISE RESOURCE PLANNING (ERP) ............................................................................................. 23 3.11. DEMAND DRIVEN MANUFACTURING RESOURCE PLANNING (DDMRP) ................................................ 25 3.11.1. Components and steps for implementation of DDMRP ...................................................................... 27 3.11.2. Shortcomings of DDMRP and its effects ........................................................................................... 32 4. ANALYSIS .................................................................................................................................................... 34 5. CONCLUSIONS AND RECOMMENDATIONS ...................................................................................... 42 6. DISCUSSION ................................................................................................................................................ 44 7. REFERENCES ............................................................................................................................................. 45 ABBREVIATIONS ADU Average daily usage APS Advanced planning and scheduling ASRLT Actively synchronized replenishment lead time BOM Bill of material CLT Cumulative lead time CSF Critical success factors DLT Delivery lead time DDMRP Demand driven material requirement planning ERP Enterprise resource planning IO Map Intermediate objective map JIT Just in time MAX Maximum MIN Minimum MLT Manufacturing lead time MOQ Minimum order quantity MPC Manufacturing planning and Control MRP Materials requirement planning MRPII Manufacturing resource planning NFP Net flow position OMAX Over maximum OTOG Over top of green OUT Stocked out ROI Return of investment TOC Theory of constraints TOCSCRS Theory of constraints supply chain replenishment systems TOR Top of red TOY Top of yellow WIP Work in progress 1. INTRODUCTION This section of thesis presents the background of the problem, the aim of the study, formulated research questions, scope and limitations of the research. 1.1. Background Before four decades from now, the driving force for companies was cost of manufacturing and all their strategies were based on high-volume production, cost minimization and achieving stable demand conditions. However, from the 1980’s, quality and satisfying customer needs has given a competitive edge in manufacturing industry (Kortabarria, et al., 2018). To achieve this advantage, companies had to work on operations of their supply chain network to obtain an optimization among various objectives which include on time delivery, reducing lead times, optimized work in progress(WIP) resulting in reducing costs of final product (Miclo, et al., 2016). In order to adapt to these changes, companies had to bring a paradigm shift in their ways of working to create a dynamic production environment where frequent changes in products, processes and production schedule can take place (Kortabarria, et al., 2018).
Details
-
File Typepdf
-
Upload Time-
-
Content LanguagesEnglish
-
Upload UserAnonymous/Not logged-in
-
File Pages48 Page
-
File Size-