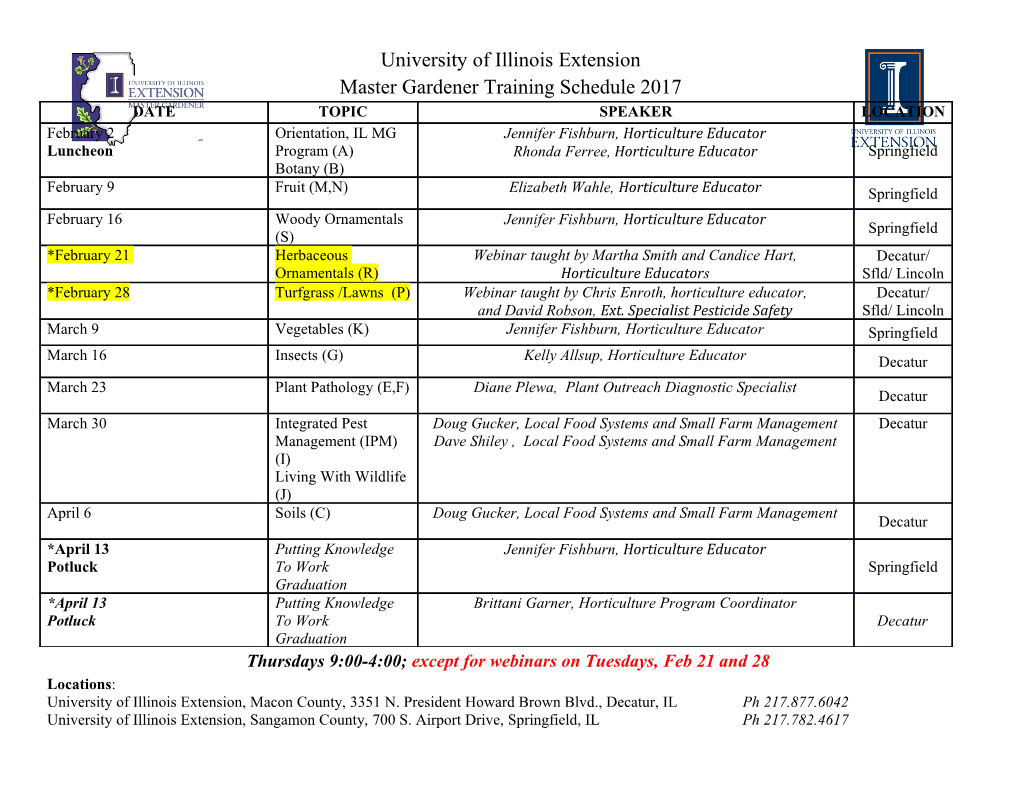
US005248818A United States Patent (19) 11 Patent Number: 5,248,818 Werle et al. 45) Date of Patent: Sep. 28, 1993 (54) PROCESS FOR THE PRODUCTION OF Derwent Publications Ltd., AN 89-315554 and CALCUM FORMATE SU-A-1474 157 (English abstract) (mentioned on p. 3, 75 Inventors: Peter Werle, Gelnhausen; Martin line 20-p. 4, line 19). Trageser, Gelnhausen-Hoechst; "Calcium', Part B, No. 28, Verlag Chemie GmbH, pp. Ulrike Duderstadt, Hasselroth, all of 160-162 (mentioned on p. 2, lines 9-12 of the present Fed. Rep. of Germany application) 1956. 73) Assignee: Degussa Aktiengesellschaft, Fed. Primary Examiner-Arthur C. Prescott Rep. of Germany Attorney, Agent, or Firm-Beveridge, DeGrandi, (21) Appl. No.: 856,649 Weilacher & Young 22 Filed: Mar. 24, 1992 57) ABSTRACT (30) Foreign Application Priority Data Calcium formate is produced in aqueous phase by reac Apr. 25, 1991 (DE) Fed. Rep. of Germany ....... 4113470 tion of calcium hydroxide with formaldehyde in the presence of hydrogen peroxide or by reaction of cal 51) Int, C. .............................................. CO7C 53/06 cium peroxide with formaldehyde. The molar ratio of 52 U.S. Cl. .................................................... 562/531 CaO or Ca(OH)2 to H2CO to H2O2 is 1 to 2 to 1-1.2 and 58) Field of Search ......................................... 562/531 the molar ratio of CaO2 to H2CO is 1 to 2. Calcium 56) References Cited formate is obtained in an almost substantially quantita U.S. PATENT DOCUMENTS tive yield and in highly pure form. The process avoids the disadvantages of prior processes for the production 3,864,369 2/1975 Isa et al. .......................... 562/531 X of calcium formate from calcium hydroxide and formal 4,549,025 10/1985 Dalcanale et al. .............. 562/531 X dehyde. OTHER PUBLICATIONS Soviet Inventions Illustrated, Week 8943, Dec. 1989, 17 Claims, No Drawings 5,248,818 1. 2 Accordingly, it has not hitherto been possible to iso PROCESS FOR THE PRODUCTION OF CALCUM late calcium formates in high yields by reaction of milk FORMATE of lime, for example, with formaldehyde in accordance with the following equation: BACKGROUND AND INTRODUCTION 5 The present invention relates to a process for the production of calcium formate in aqueous phase by because, after a certain incubation period dependent on reaction of formaldehyde with calcium hydroxide in the the particular reaction temperature and on any impuri presence of hydrogen peroxide or by reaction of formal 10 ties present, the self-catalytic formaldehyde condensa dehyde with calcium peroxide. tion which begins at the same time converts any formal Calcium formate, the calcium salt of formic acid, is dehyde still present almost instantaneously into for presently obtained almost exclusively as a by-product in moses in a highly exothermic reaction and thus removes the manufacture of the polyhydric alcohols (polyols) it from the formate-forming reaction. pentaerythritol, trimethylol ethane, trimethylol pro 15 Russian patent 1474157 describes a process for the pane and neopentylglycol. It is formed during the reac production of calcium formate by Cannizzaro reaction tion of 3-hydroxyaldehydes obtained by aldol condensa from calcium hydroxide and formaldehyde, in which tion of formaldehyde in the presence of calcium hy saccharification of the formaldehyde is largely pre droxide. Accordingly, calcium formate is the oxidation vented by addition of the metal salts MnSO4, FeSO4, product of a mixed Cannizzaro reaction. Sodium for 20 Cu2Cl2 or Ce(NO3)2. Although the yields of calcium mate is also obtained as a by-product in the manufacture formate obtained in this process are far better than the of polyols. yields obtained in the absence of inhibitors, reaching Calcium formate is used for various purposes, for around 89% in the best Example (Example 6), disadvan example as a tanning auxiliary, for the production of tages lie in the very long reaction times (5 h), which formic acid, as a setting accelerator in the cement indus 25 cause poor volume/time yields, and the high dilutions try, as a silaging auxiliary and, to an increasing extent, which result in the cost-intensive evaporation of large as a nutritive supplement in animal feeds. The last of quantities of water. In addition, the formaldehyde re these applications, where calcium formate is used to maining in the solution (in Example 6, approximately improve feed utilization, to reduce digestive problems, 8% of the quantity used was not reacted) has to be to avoid microbial feed decay (see brochure of Degussa 30 AG, "Calcium formiat'-Ch 608-1-105-988 DD) imposes separated from the calcium formate. This generally particular quality requirements to ensure that the feed requires distillation under pressure on account of the containing calcium formate is not refused by the ani particular properties of the formaldehyde. This incom mals. plete reaction makes the basically simple Cannizzaro The disadvantages of producing calcium formate as a 35 reaction unusable in this form for the synthesis of cal by-product of polyol synthesis is that an increase in the cium formate on an industrial scale because the problem production of formate can only be obtained in connec posed by the excess formaldehyde is not solved and tion with an increase in the production of the particular calcium formate cannot be crystallized out from such polyol (which presupposes corresponding marketing solutions sufficiently free from formaldehyde. In addi possibilities for the polyol). 40 tion, 2 mol methanol are obtained per mol calcium for It is also known that calcium formate can be pro mate under the reaction conditions, leading on the one duced by carbonylation of calcium hydroxide (cf., for hand to a high input of formaldehyde and, on the other example, Gmelin's Handbuch, Vol. Ca(B), pages hand, to expense in removing the methanol from the 161-162 and Ullmann's Encyclopedia, 4th Ed., Vol. A reaction mixture. 12, pages 23-24). These processes generally require 45 SUMMARY OF THE INVENTION technically complicated reactors, high pressures, high temperatures and generally long reaction times. An object of the present invention is to provide a The Cannizzaro reaction of formaldehyde with process for the production of calcium formate in an strong inorganic bases takes place in accordance with economic manner. without the disadvantages mentioned 50 above. the following scheme: According to the present invention, this and other objects are achieved by reaction of formaldehyde with a calcium compound in aqueous phase at a temperature n = 1 for Me= K, Na of 20' to 90' C. and isolation of the formate from the n=2 for Me=Ca, Ba 55 aqueous phase, characterized in that the reaction is The course of this reaction is determined by the metal carried out in the presence of hydrogen peroxide and hydroxide used. Numerous studies have shown that /or calcium peroxide, calcium oxide or calcium hydrox certain metal hydroxides do not promote the Canniz ide, formaldehyde and hydrogen peroxide in a molar zaro reaction, but rather self-condensation of the form ratio of 1 to 2 to 1-1.2 or calcium peroxide and formal aldehyde. Although the formaldehyde molecule does dehyde in a molar ratio of 1 to 2 being used as reactants not have an a-H atom and, accordingly, cannot enter for the reaction. into a normal aldol condensation, hydroxyaldehydes and ketones (particularly pentoses and hexoses, the DETAILED DESCRIPTION OF THE so-called formoses) are formed by a substantially analo INVENTION gous reaction (T. Mizuno, A. Weiss, Adv. Carbohyd. 65 Without being bound by theory, the process accord Chem. Biochem. 29 173 (1974)). Formose-forming hy ing to the invention is based on the following reaction droxides include in particular Pb(OH)2, Sn(OH)2, equations: TIOH and Ca(OH)2. 5,248,818 3 4. cig-H,Co-Ho-chcoo-H+. (l) TABLE-continued Activities of various inhibitors for inhibiting the formation CaO2+2H2CO-Ca(HCOO)2 + H2 (2) of formoses Stabilization Stabilization According to equation (2), the peroxide undergoes Inhibitor (min.) Inhibitor (min.) hydrolysis in the aqueous phase with formation of LiBr 13 MnSO4 29 H2O2 and Ca(OH)2, so that the reactions according to KIO4 13 MnSO4 (3.8) 2 (l) and (2) can even take place at the same time as one SN t Es tate another. In practice, equation (2) may acquire signifi- 10 ine), 5 Militic 30 cance for the production of calcium formate because B2O3 26 Mn(II) acetyl- 45 calcium peroxide can also be formed in situ from Ca- 2 : te 20 (OH), and H2O: 8 Aliso), 20 Fees) 20 The reaction is carried out at temperatures of 20 C. 6, 16 Co(III) acetate 15 to 90° C., preferably at temperatures of 30° C. to 70° C. 15 2S4 >90 NiSO4 14 and, more preferably, attemperatures of 40 C. to 60° C. ZrCl4 (3.8) >90 Cu powder (3.8) 18 The formation of so-called formoses from the sacchari- S; SEe 8 : fication of formaldehyde can be minimized by cooling V8So, 20 &Sess) 26 the exothermic reaction to limit the temperature. NbCls 20 AgNO3 14 To carry out the reaction according to equation (1), 20 K2CrO4 15 an aqueous formaldehyde solution and an aqueous hy- NM3 drogen peroxide solution may be simultaneously intro- Wö. 4 5 duced into an aqueous solution or suspension of the Test conditions: 15.2Ca(OH)2 (97%) + 32.5g CH2O (37% by weight); T = 70' C.; calcium hydroxide. The addition is accompanied by rp.m. = 200 thorough mixing, for example by stirring or pump-cir Inhibitor input: 7.6 mg, based on central atom; tests with half the quantity of initiator culation of the reaction mixture. After they have been 25 (3.8 mg) were identified in the Table.
Details
-
File Typepdf
-
Upload Time-
-
Content LanguagesEnglish
-
Upload UserAnonymous/Not logged-in
-
File Pages5 Page
-
File Size-