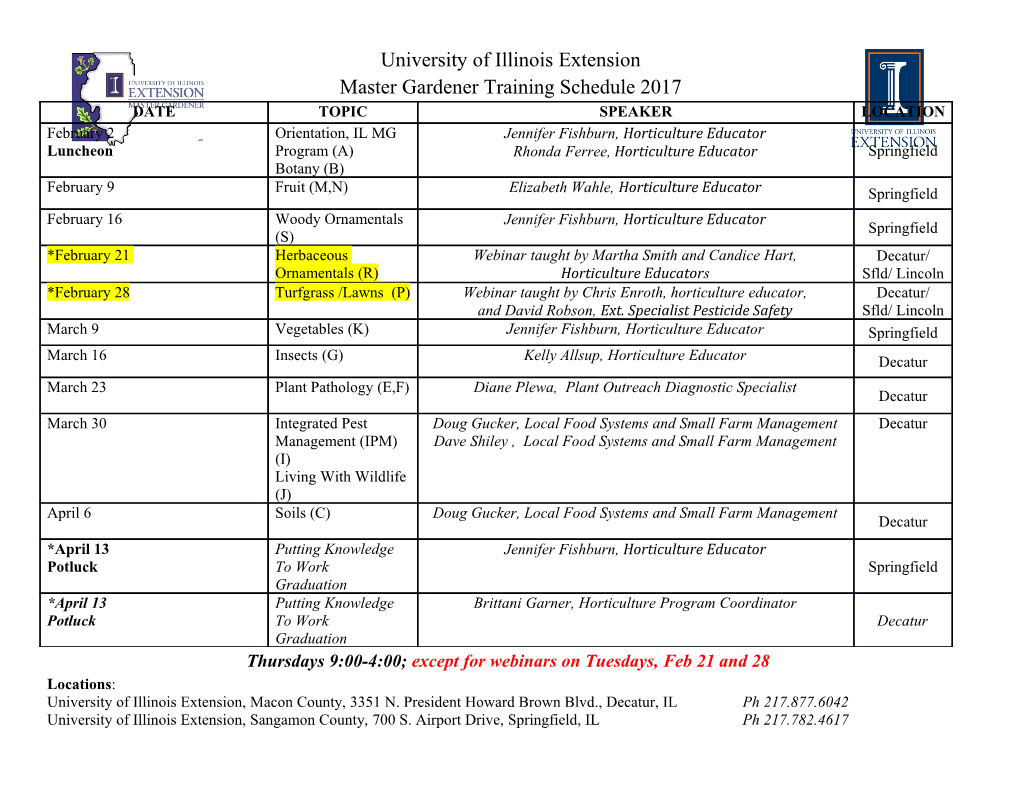
US 20100167547A1 (19) United States (12) Patent Application Publication (10) Pub. No.: US 2010/0167547 A1 KAMMURA (43) Pub. Date: Jul. 1, 2010 (54) POLISHING LIQUID (30) Foreign Application Priority Data (75) Inventor: Tetsuya KAMIMURA, Dec. 25, 2008 (JP) ................................. 2008-33O704 Shizuoka-ken (JP) Publication Classification (51) Int. Cl. Correspondence Address: HOIL 2/302 (2006.01) Solaris Intellectual Property Group, PLLC C09K I3/00 (2006.01) s E's, (52) U.S. Cl. ................... 438/693; 252/79.1; 257/E21.23 exandra, (US) (57) ABSTRACT (73) Assignee: FUJIFILM CORPORATION, A polishing liquid for a chemical mechanical polishing of a Tokyo (JP) semiconductor device includes (a) a carboxylic acid com pound having one or more carboxy groups, (b) colloidal silica particles having a potential of -10 mV to -35 mV when (21) Appl. No.: 12/639,015 used in the polishing liquid, (c) a benzotriazole derivative, (d) an anionic Surfactant, and (e) an oxidizing agent, and the (22) Filed: Dec. 16, 2009 polishing liquid has a pH of from 5.0 to 8.0. US 2010/0167547 A1 Jul. 1, 2010 POLISHING LIQUID should be formed in which level differences due to dishing, erosion, and the like are ultimately reduced by regulating the CROSS-REFERENCE TO RELATED polishing rate of the metal wiring portion and the polishing APPLICATION rate of the barrier metal portion. Specifically, in barrier metal 0001. This application claims priority under 35 USC 119 CMP, it is preferable that the polishing rates of the barrier from Japanese Patent Application No. 2008-330704 filed on metal and insulation layer are moderately high, since dishing Dec. 25, 2008, the disclosure of which is incorporated by due to over-polishing of the wiring portion and erosion result reference herein. ing from dishing may occur when the polishing rates of the barrier metal and the inter-layer dielectric are relatively low when compared with to the polishing rate of the metal wiring BACKGROUND OF THE INVENTION material. Not only does this have the advantage of improving 0002 1. Field of the Invention the barrier metal CMP throughput, but there is a requirement 0003. The present invention relates to a polishing liquid to relatively increase the polishing rates of the barrier metal employed in a manufacturing process for a semi-conductor and the insulation layer for the above reasons, since dishing is device. More specifically, the present invention relates to a often caused by metallic film CMP in practice. polishing liquid which is preferably employed to polish a 0010. A metal polishing liquid employed in CMP gener barrier layer consisting mainly of a barrier metallic material ally includes abrasive particles (for example, aluminum oxide and an insulating layer consisting of an insulating material, or silica) and an oxidizing agent (for example, hydrogen for planarizing during a process for forming wiring on a peroxide or persulfuric acid). The basic polishing mechanism semi-conductor device. is thought to be that the metal surface is oxidized with the 0004 2. Related Art oxidizing agent, and then the oxide film formed thereby is 0005. In recent years, in the development of semi-conduc removed with the abrasive particles. tor devices such as semi-conductor integrated circuits (here 0011. However, when a polishing liquid including these inafter, referred to as “LSI), increased density and integra sorts of solid abrasive particles is used in a CMP process, tion have been sought by reducing the thickness of wiring and problems such as polishing damage (scratching), a phenom creating multiple layers thereof in order to miniaturize and enon in which the entire polishing Surface is over-polished increase the speeds of such devices. Moreover, various types (thinning), a phenomenon in which the polished metallic of technologies, such as chemical mechanical polishing Surface is dished (dishing), and a phenomenon in which plural (hereinafter, referred to as “CMP) and the like have been metallic wiring surfaces are dished due to over-polishing of employed in order to achieve this objective. CMP is an essen the insulator placed between the metallic wiring layers (ero tial technology for Surface planarization of processed layers, sion), and the like, may occur. Such as an inter-layer dielectric, for plug formation, for for 0012. In addition, there are cost-related problems, such as mation of embedded metal wiring, and the like. CMP per complicating a conventionally employed cleaning process for forms smoothing of a substrate and eliminates excessive eliminating residual polishing liquid from a semi-conductor metallic thin films from wiring formation, and eliminates Surface when a polishing liquid including Solid abrasive par excessive barrier layer on the Surface of insulating films. ticles is used, and Such as the requirement that Solid abrasive 0006. A conventional method of CMP is a method in particles must be precipitated when disposing of liquid after which a polishing pad is fixed to the Surface of a circular polishing table (polishing platen), the Surface of the polishing Such cleaning (waste liquid). pad is impregnated with a polishing liquid, the Surface of the 0013 The following investigations have been conducted substrate (wafer) is pressed onto the pad, and both the polish with regard to a polishing liquid including solid abrasive ing platen and the wafer are rotated while a predetermined particles. amount of pressure (polishing pressure) is applied from the 0014 For example, a CMP polishing agent and a polishing backsides thereof, such that the surface of the wafer is thereby method that aim to achieve a high polishing rate, with virtu planarized via the mechanical abrasion produced therefrom. ally no occurrence of Scratching is proposed (for example, 0007 When semi-conductor devices such as LSIs are pro Japanese Patent Application Laid-Open (JP-A) No. 2003 duced, fine wiring is formed in multiple wiring layers, and a 17446), a polishing composition and a polishing method for barrier metal such as of Ta, TaN. Ti or TiN is pre-formed in improving washability in CMP is proposed (for example, order to prevent diffusion of the wiring material into an inter JP-A No. 2003-142435), and a polishing composition that layer dielectric, and in order to improve adhesion of the aims to prevent agglomeration of abrasive particles is pro wiring material, when forming the metal wiring, such as posed (for example, JP-A No. 2000-84832). copper wiring, in each of these layers. 0015. However, even in these polishing liquids, there is 0008. In order to form each wiring layer, in general, a still no method for achieving a high polishing rate when CMP process on metallic film (hereinafter, referred to as polishing a barrier layer, while inhibiting scratching caused “metallic film CMP) is first performed at a single stage or at by the agglomeration of Solid abrasive particles. multiple stages to remove excess wiring material that has 0016. In order to improve insulation properties of wiring, been deposited by plating or the like, and thereafter, a CMP low dielectric constant Substrate materials (Low-k materials) process is carried out to remove barrier metal material (barrier are required to be developed in the future. However, Low-k metal) that has been exposed on the surface of the metallic materials are easily damaged by CMP and the insulation film (hereinafter, referred to as “barrier metal CMP). How properties thereof may be seriously deteriorated by CMP. ever, metallic film CMP may cause over-polishing, referred to This problem is very serious when conventional polishing as dishing, or cause erosion of the wiring portions. methods carried out in the acidic or alkaline region are used. 0009. In order to reduce such dishing, in such barrier metal Thus, a polishing liquid used in the pH neutral region has also CMP, which follows the metallic film CMP, a wiring layer been proposed (JP-A No. 2008-78233). It is hoped that this US 2010/0167547 A1 Jul. 1, 2010 problem can be solved through use of the neutral region 0033 <8> The polishing liquid according to any one of because a reactions tend not to occur in the neutral region. <1> to <7>, further including a polysaccharide. 0017. However, there have been no methods that achieve a 0034) <9>The polishing liquid according to <8>, in which practical polishing rate with neutral polishing liquids. Since the polysaccharide is at least one selected from the group reactions tend not to occur in the neutral region, it is difficult consisting of pullulan, cellulose, agarose, pectin, starch, and to achieve a Sufficient polishing rate for a barrier material and derivatives thereof an insulating material. Therefore, the only method for 0035) <10> A chemical mechanical polishing method of increasing a polishing rate in the neutral region has been to polishing a Surface of a semiconductor device, including: increase the concentration of abrasive particles. However, 0036 polishing the surface of the semiconductor device when the concentration of the abrasive particles is increased by relative movement of a polishing pad and the surface of the to, for example, about 10% by mass in order to achieve a semiconductor device while Supplying a polishing liquid to Sufficient polishing rate, although the polishing rate the polishing pad, improves, physical damage or defects are caused in the Low-k 0037 the polishing liquid including: materials. 0038 (a) a carboxylic acid compound having one or more carboxy groups, SUMMARY OF THE INVENTION 0039 (b) colloidal silica particles having a potential of 0018. The present invention provides a polishing liquid -10 mV to -35 mV when used in the polishing liquid, including Solid abrasive particles to polish a barrier layer 0040 (c) a benzotriazole derivative, consisting of a barrier metallic material and an insulating 0041 (d) an anionic surfactant, and layer consisting of an insulating material, which can achieve 0042 (e) an oxidizing agent, a high polishing rate when polishing the barrier and insulating the polishing liquid having a pH of from 5.0 to 8.0.
Details
-
File Typepdf
-
Upload Time-
-
Content LanguagesEnglish
-
Upload UserAnonymous/Not logged-in
-
File Pages14 Page
-
File Size-