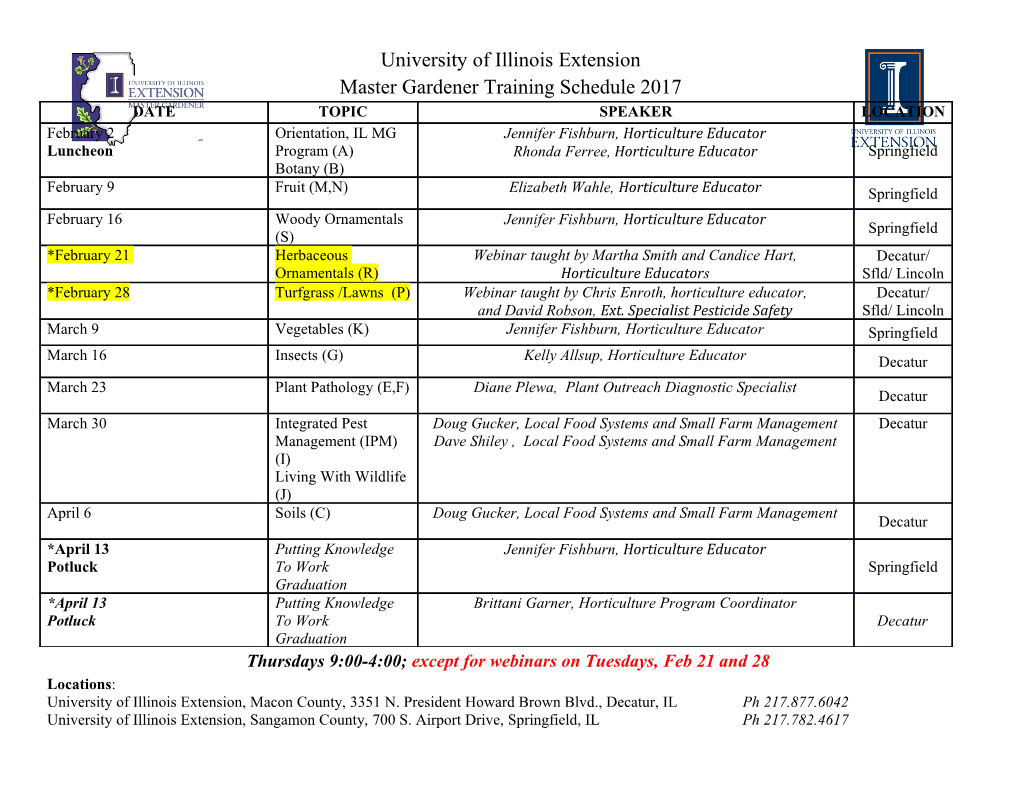
IEEE/CSC & ESAS SUPERCONDUCTIVITY NEWS FORUM (global edition), January 2016. MT-24 preprint 4OrAA_01. Submitted to IEEE Trans. Appl. Supercond. for possible publication. 1 In-depth Induction Heating of Large Steel Slabs by means of DC Saturating Field produced by SC Coils Antonio Morandi, Senior Member, IEEE, and Massimo Fabbri Abstract —The feasibility of an innovative in-depth AC metals such as aluminum, copper, silver or brass thanks to the induction heating method for large steel slabs is investigated. large penetration depth, which allows the heat to penetrate Beside the AC field, which induces the heating currents, a large deep within the material, combined with the high thermal DC magnetic field is also applied which brings the material to conductivity. Thanks to the in-depth heating, satisfactory saturation. Due to the saturation the permeability is reduced by orders of magnitude and the penetration depth is drastically uniformity and productivity can also be obtained for non- increased, thus making it possible a much faster and uniform magnetic metals with poor thermal conductivity (stainless heating. In order to produce the field needed for the saturation of steel, titanium and tungsten), provided that appropriate common steels work piece, lossless DC superconducting magnets geometry and operating frequency are chosen for the AC coil need to be employed. [4]. However, when common steels, which are ferromagnetic The possible layout of the AC induction heater which employs from room temperature up to the Curie temperature (770°C), magnetic saturation (Saturated AC Induction Heater) is are considered, a very low penetration depth is obtained and discussed. The concept design of the superconducting magnet needed is carried out based on present state of the art heat generation is mostly confined at the surface. The heating superconducting materials. The performance of the saturated AC of the work-piece’s core is obtained via thermal diffusion induction heater is investigated numerically and compared with only. This leads to slow process and large temperature the case of no magnetic saturation. gradients from surface to core. The process is further slowed down by the need to arrest it periodically and/or to reduce the Index Terms—Induction heating, Temperature control, Steel power to allow homogenization and to avoid that excessive slab, Saturation magnetization, Superconducting magnets, MgB2. temperature is reached at the surface. This prevents cracking or even local melting, especially for high alloyed steels [5] and I. INTRODUCTION is particularly important for work-pieces with rectangular NDUCTION HEATING is widely used in industry for heating cross sections where electromagnetic end- and edge-effects Imetals before hot workings (hot rolling, forming, extrusion, can produce intense power concentration [1], [2], [6] - [9]. forging, etc.) [1]. The advantages of the induction heating over Due to these reasons, when real-world magnetic steel slabs or the heating by gas furnaces include absence of on-site CO2 blooms with typical thickness in the range 0.2 - 0.3 m, width emission, fast operation, high surface quality, possibility to in the range 0.9 - 1.5 m and length in the range 4 – 11 m are work in any processing atmosphere (including vacuum), considered [10], the heating by gas furnaces is the common contact-less operation and controllability [1]-[4]. solution [5], [11]-[16]. Metal work-pieces (slabs, blooms, bars, and billets) are The feasibility of an innovative induction heating method heated by induction until they reach a high enough for large steel slabs is investigated in this paper. The idea is to temperature which creates proper conditions for plastic apply, beside the AC field which induces the heating currents, deformation [2]. Due to the skin effect, 87 % of thermal power a large DC magnetic field which brings the material to injected during the process is produced in a layer located at the saturation. Due to the saturation the permeability is reduced by surface of the work-piece. The thickness of this layer is the orders of magnitude and the penetration depth is increased by penetration depth δ, which depends on the frequency f of the a factor from 50 to 100 (depending on the temperature and the applied AC field and the electric resistivity ρ and the magnetic frequency), thus making it possible a much faster and uniform permeability µ of the processed material [3]: heating. It is be considered, however, that in order to produce saturation of common steels, a magnetic field of at least 2 T / fµπρ=δ (1) must be applied all over the volume of the processed slab. High temperature uniformity at the end of the process is a Such a relatively high field over such a large volume cannot mandatory requisite in industrial heating for hot workings. be produced by means of permanent magnets. Furthermore, its Short heating time is also strictly required in order to achieve generation by means of conventional electromagnets would high productivity. Appropriate uniformity and productivity require unpractical amount of copper and supply power. can be easily reached in induction heating of non-magnetic Fortunately, the saturating field can effectively be produced by means of superconducting magnets. Thanks to the DC operation no significant AC loss is generated in the magnet, Manuscript received October 20, 2015. A. Morandi, and M. Fabbri are with DEI - “Guglielmo Marconi” which can hence be maintained in operation with affordable Department of Electrical, Electronic and Information Engineering, University cooling power. Therefore, superconductivity is the enabling of Bologna, Italy (Corresponding Author e-mail: [email protected]). IEEE/CSC & ESAS SUPERCONDUCTIVITY NEWS FORUM (global edition), January 2016. MT-24 preprint 4OrAA_01. Submitted to IEEE Trans. Appl. Supercond. for possible publication. 2 technology for induction heating of large steel slabs. equalization, that is to satisfy the primary requirement on ∆T This paper is organized as follow: the usual requirements of [2], [7]. A limit of 1 hour is usually set on the total heating the heating process of common magnetic steels are reviewed time in order to obtain acceptable productivity of the steel in section II. The physical properties of the steel are examined plant. Lower or greater bounds are possible depending on the in section III and the effect of applying magnetic saturation on type of steel, the geometry of the work-piece and the initial the penetration depth is quantitatively assessed. A possible temperature [7], [8], [12], [14], [17]. layout of the AC induction heater which employs magnetic saturation (hereafter Saturated AC Induction Heater) is TABLE I discussed in section IV. The concept design of the REQUIREMENTS OF THE HEATING PROCESS FOR MAGNETIC STEEL SLAB superconducting magnet needed for the implementation of the Primary objectives Average volume temperature at the end of heater is carried out in section V based on present state of the 1150 °C < T < 1250 °C the process V art superconducting materials. Finally, the performance of the Average surface temperature at the end of 1150 °C < T < 1250 °C saturated AC induction heater is investigated numerically and the process S compared with the case of no magnetic saturation. The main Temperature at the core at the end of the 1150 °C < T < 1250 °C assumptions of the numerical model are discussed in section process core VI. Results are presented in section VII. Maximum temperature during the process Tmax < 1350 °C Surface to core Temperature difference at ∆T < 25 °C II. REQUIREMENTS OF THE HEATING PROCESS the end of the process Surface to core Temperature difference ∆T < 380 °C The induction heating of a magnetic steel slab for hot during the process milling is considered in this paper. The average temperatures Secondary objectives on the volume and surface of the slab, denoted with T and T V S Maximum temperature at the end of the Tmax < 1300 °C respectively, are considered for evaluating the performance of process the heating process. The temperature Tcore at the center of the Minimum temperature at the end of the Tmin > 1100 °C slab is also considered. A further important indicator is the process surface-to-core temperature difference in the slab, denoted Heating time < 60 min with ∆T. Finally, the maximum and the minimum temperature at any point of slab during the heating process, denoted with III. PHYSICAL PROPERTIES OF THE STEEL Tmax and Tmim respectively, are also considered. We report that Common cast steel is considered for the present analysis. A conventional induction heating of magnetic steels is mass density of 7870 kg/m3 is assumed. All physical commonly subdivided in two (or more) stages with different properties of the processed steel strongly depend on the amplitude of the applied field, frequency and duration [2]. temperature. Electrical resistivity, specific heat and thermal Increased magnitude and frequency are used as soon as the conductivity of the considered steel have been taken from Curie temperature is reached at all point, in order to inject a [18]. The electrical resistivity increases non-linearly from 0.14 greater power in the slab and obtain a faster heating. The same µΩ·m at room temperature up to 1.26 µΩ·m at the melting field and frequency cannot be used below the Curie temperature, i.e. 1350°C. The specific heat increases from 455 temperature since excessive temperature gradients can occur J/kgK at room temperature up to 764 J/kgK at the melting near the surface which can produce cracking. temperature, exhibiting a pronounced maximum of 1130 The requirements of the heating process are listed in Table J/kgK near the Curie temperature, i.e. 770°C. The thermal I. The final temperature of the slab is between 1150°C and conductivity decreases from 71 W/m·K at room temperature 1 1250°C [12], [13]. This requirement must be fulfilled by the up to 33 W/m·K at the melting temperature, with a minimum average temperatures TV and TS, and by the core temperature of 27 W/m·K near the Curie point.
Details
-
File Typepdf
-
Upload Time-
-
Content LanguagesEnglish
-
Upload UserAnonymous/Not logged-in
-
File Pages7 Page
-
File Size-