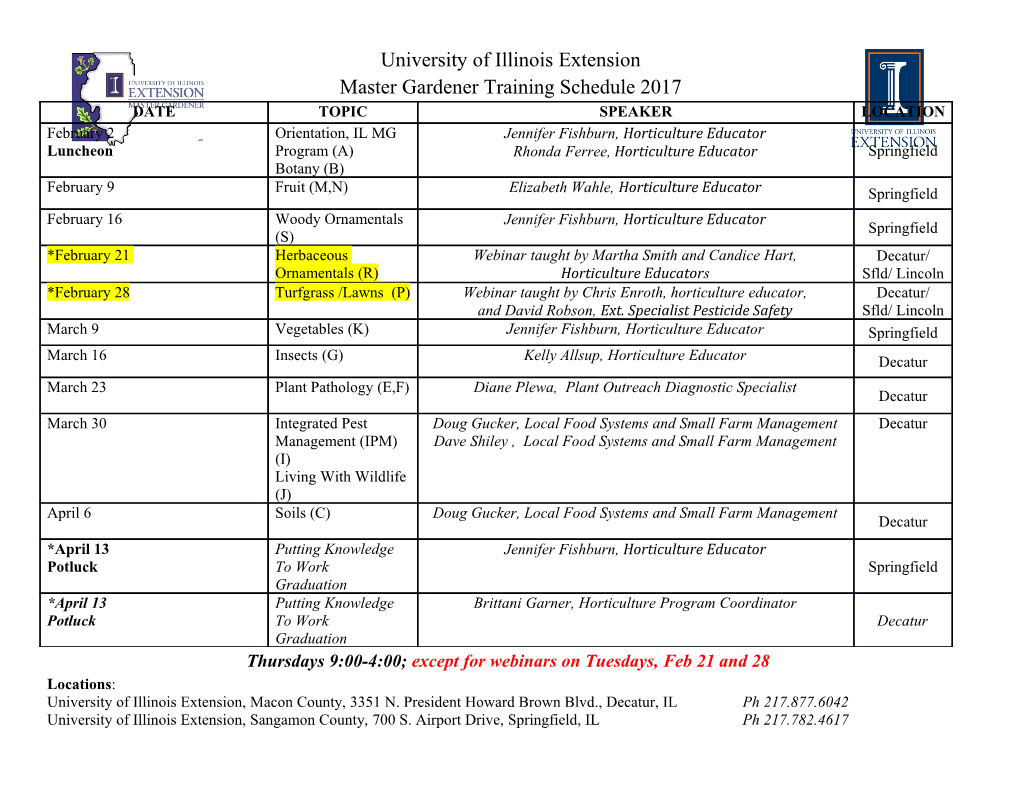
Technical Forum How Plasma-Enhanced Surface Modification Improves the Production of Microelectronics and Optoelectronics ABSTRACT Over the past 30 years, plasma, the fourth state of matter, has become a very useful method for surface modification and deposition of various materials. In IC packaging applications, plasma is employed to prepare surfaces for die attach, wirebonding and mold/encapsulation. Moreover, plasma-enhanced contamination removal and surface activation processes improve the reliability and yield, and also enhance the manufacture of advanced technology products. In many optoelectronic devices, plasma-enhanced contamination removal is used to prepare surfaces prior to eutectic die attach and wirebonding. This article examines examples of plasma surface modification in both the microelectronic and optoelectronic industries. By Dr. James D. Getty, March Plasma Systems, Concord, Calif. ubstrate materials and the adhe- S sives employed for attachment often do not possess the needed physical or chemical properties to allow for good adhesion, and require surface modification.1 Plasma surface modification involves the interaction of the plasma-generated excited species with a solid interface. The plasma process results in a physical and/ or chemical modification of the first few molecular layers of the surface, while maintaining the properties of the bulk. Typical materials employed in the microelectronics and optoelectronics industries include ceramics, glass, polymers and metals—such as gold, copper, alu- minum, nickel, palladium, tungsten, and silver. The effectiveness of the plasma on This single strip, compact plasma chamber processes BGA-type substrates with argon plasma. these complex interfaces is determined by the plasma source gases, the configuration as well as by the ensuing process required. popularity due to the consistency they offer. of the plasma system and the plasma The plasma process and the subsequent The lead photo displays the single strip, operating parameters. processing steps must also be considered. compact plasma chamber, which processes Surface modification processes can be Surface modification is often sensitive BGA-type substrates with argon plasma. classified into four categories: to time and environmental exposure, where The characteristic photon emission of the • Contamination Removal the surface may lose its plasma-induced argon plasma can be seen through the •Surface Activation physical and chemical properties. chamber window. (Process applications •Etch Automated in-line plasma systems are shown in the table.) • Cross Linking (Figure 1), which allow the surface mod- Selection of a specific process is deter- ification process to be performed indi- Contamination Removal mined by the physical and chemical com- vidually—immediately prior to the next Surface contamination removal involves position of the material to be processed, step in the assembly process—have gained the use of the plasma’s physical and/or 72 Reprinted from the January-February issue of Chip Scale Review. Used by permission; all rights reserved. ©2002 Chip Scale Review. Technical Forum Process Applications for Plasma Surface Enhancements Plasma Surface Modification Advanced Technology Source Gas Processes Application Argon (Ar) Contamination Removal–Ablation Wirebond Die Attach Cross Linking Substrate Polymer–Metal Adhesion Oxygen (O2) Contamination Removal–Chemical Wirebond Oxidation Process (Organic Removal) Die Attach Surface Activation Mold and Encapsulant Adhesion Etch Photoresist Removal Nitrogen (N2) Surface Activation Mold and Encapsulant Adhesion Hydrogen (H2) Contamination Removal–Chemical Wirebond Reduction Process (Metal Oxide Eutectic Die Attach Removal) Carbon Tetrafluoride Etch Polymer Etch–Fiber Stripping (CF4) and Oxygen (O2) Photoresist Removal or Sulfur Hexafluoride Thin Film Etch–Oxides, Nitrides (SF6) and Oxygen (O2) chemical energy to remove micron-level The success of an oxygen plasma for Figure 1. This automated, in-line plasma tool is contamination. removal of die bond epoxy bleed has designed for surface modification processes. This process employs ablation, where been widely demonstrated.3 The upstream and downstream transfer mech- the positive ions bombard the surface. In cases where oxidation is of concern, anisms and the compact high-density plasma The ablation process can dislodge con- a physical process can be employed to chamber are contained within a single enclosure. tamination from the surface, and can prepare the bond pad surfaces. An argon roughen the surface on an atomic scale, plasma treatment of PBGA strips has been tional groups on the surface. as revealed by atomic force microscopy.2 shown to improve the wirebond pull The different functional groups modify The chemical process is widely employed strength by as much as 24.3 percent.4 the chemical activity of the surface. The to remove residual materials, typically Metal oxidation can act as a physical new functional groups have strong less than a few microns, such as organic barrier for both wirebonding and solder chemical bonds with the bulk material and films, and oxidation. The chemical process reflow. A combined physical and chemi- have the capability to further bond with employs either reduction or oxidation cal process using argon and hydrogen can adhesives to promote better adhesion. chemistry via the gas-phase radicals. reduce the metal oxides. For example, The functional groups also increase the Specific contamination issues in micro- reduction of copper oxide to copper is surface area available for the adhesive electronic and optoelectronic package achieved in a hydrogen plasma via the and thus will distribute the load over a reliability are poor wirebond pull reaction of the hydrogen radicals with larger area resulting in improved adhesive strength and voiding, due to insufficient the metal oxide. strength. Gas selection and surface type solder reflow in eutectic die attach. determine the functional group that will → 4 Wirebond pad contamination can be a CuO + 2H• Cu + H2O be substituted on the surface. by-product from previous processing In microelectronic applications, plasma steps such as die attach epoxy bleed or Even in the absence of a contamination surface activation prior to die attach environmental exposure (i.e., bond pad source, ablation will roughen the surface provides better contact, improved heat metal oxidation). and provide a larger surface area for wire- transfer and minimal voiding. A physical, chemical or combined bonding, resulting in improved wire- The purpose of the mold/encapsulant physical-chemical process using argon and bond uniformity bond to bond.4 material for semiconductor applications oxygen source gases can be employed to is to provide adequate mechanical strength, prepare the bond pads. An oxygen-based Surface Activation adhesion to various package components, plasma will take advantage of the oxygen Plasma surface activation employs gases, good corrosion and chemical resistance, radicals to chemically react with the epoxy, such as oxygen, nitrogen, hydrogen, and matched CTE to the materials it interfaces producing volatile gas-phase by-products ammonia, which, when exposed to the with, high thermal conductivity and high that can be pumped from the vacuum plasma, will dissociate and react with the moisture resistance in the temperature chamber. surface, creating different chemical func- range used. Reprinted from the January-February issue of Chip Scale Review. Used by permission; all rights reserved. ©2002 Chip Scale Review. 73 Technical Forum semiconductor and optoelectronic pro- Stripping the buffer is required for cessing, including photoresist removal, thin various applications, including hermetic film etch, and polymer etch. sealing, pigtailing of laser diodes, fiber In optoelectronic manufacturing, arrays, fiber Bragg gratings, and amplifier plasma etch has been employed to produce seeding. stripped fibers through the controlled Fiber Bragg gratings, for example, are removal of the urethane acrylate buffer widely used in the fabrication of devices coating. for dense wavelength division multiplex- Figure 2. Illustration displays a fiber with the Conventional optic fibers are com- ing (DWDM). buffer material removed, and the glass cladding posed of a cylindrical core covered by a Figure 2 displays a fiber with the buffer and core exposed. cladding material and a buffer material material removed and the glass cladding that encases the cladding. The core is the and core exposed. A critical requirement The ability to form good adhesion light-carrying element, and the cladding in the removal of the fiber buffer is to with package components and to remain promotes the total internal reflection in completely remove the urethane acrylate bonded is of paramount importance, the fiber. polymer while maintaining the intrinsic since delamination along the interfaces is a major reliability issue for plastic-encap- sulated microcircuits. The Fourth State of Matter Plasma treatment has been demon- Gas phase plasma is an electrically species are capable of physical work strated to improve the bond strength at neutral mixture of electrons, ions, rad- through sputtering. the plastic encapsulant, gold-plated icals, photons, recombination products Photon emission within a plasma is a copper leadframe interface via an and neutrals created by the application result of the excited neutrals, ions and free enhanced chemical compatibility with of energy, such as radio frequency radicals formed
Details
-
File Typepdf
-
Upload Time-
-
Content LanguagesEnglish
-
Upload UserAnonymous/Not logged-in
-
File Pages4 Page
-
File Size-