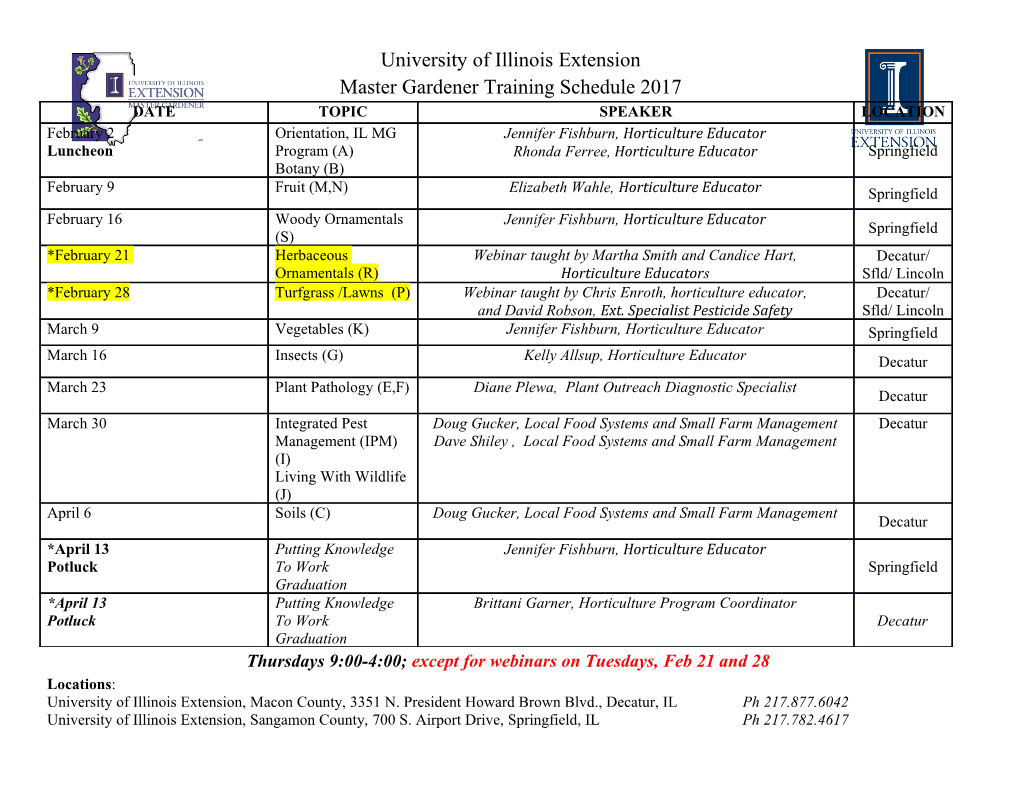
AUTEX Research Journal, Vol. 17, No 4, December 2017, DOI: 10.1515/aut-2016-0015 © AUTEX WEAR PROCESS ANALYSIS OF THE POLYTETRAFLUOROETHYLENE/KEVLAR TWILL FABRIC BASED ON THE COMPONENTS’ DISTRIBUTION CHARACTERISTICS Dapeng Gu1,2,*, Bingli Fan1,2, Fei Li1,2, Yulin Yang1,2, Suwen Chen3 1College of Mechanical Engineering, Yanshan University, Qinhuangdao 066004, Hebei, China 2Aviation Key Laboratory of Science and Technology on Generic Technology of Self-lubricating Spherical Plain Bearing, Yanshan University, Qinhuangdao 066004, Hebei, China 3Department of Environmental and Chemical Engineering, Yanshan University, Qinhuangdao 066004, Hebei, China *Corresponding author e-mail: [email protected] Abstract: Polytetrafluoroethylene (PTFE)/Kevlar fabric or fabric composites with excellent tribological properties have been considered as important materials used in bearings and bushing, for years. The components’ (PTFE, Kevlar, and the gap between PTFE and Kevlar) distribution of the PTFE/Kevlar fabric is uneven due to the textile structure controlling the wear process and behavior. The components’ area ratio on the worn surface varying with the wear depth was analyzed not only by the wear experiment, but also by the theoretical calculations with our previous wear geometry model. The wear process and behavior of the PTFE/Kevlar twill fabric were investigated under dry sliding conditions against AISI 1045 steel by using a ring-on-plate tribometer. The morphologies of the worn surface were observed by the confocal laser scanning microscopy (CLSM). The wear process of the PTFE/Kevlar twill fabric was divided into five layers according to the distribution characteristics of Kevlar. It showed that the friction coefficients and wear rates changed with the wear depth, the order of the antiwear performance of the previous three layers was Layer III>Layer II>Layer I due to the area ratio variation of PTFE and Kevlar with the wear depth. Keywords: Fabric, polytetrafluoroethylene (PTFE), Kevlar, wear process, confocal laser scanning microscopy (CLSM) 1. Introduction improve the interfacial bonding. Moreover, some researchers have reported that a variety of micro- or nano-particles [12,13], In the aviation industry, non-metal materials are just beginning which dispersed uniformly in the resin matrix, could improve the to be used alternatively instead of metals and alloys. High- antiwear performance of the fabric composites. In general, there performance fibers, fabrics, and their composites have are various factors controlling the antiwear performance of such been increasingly applied in some important parts as a fabric composites. By contrast, hybrid fabrics are interwoven class of triboengineering materials for their excellent load- with warp yarns and weft yarns together. Thousands of textile carrying capacity, friction reduction, antiwear properties, structures can be obtained by changing the textile process and light quality[1,2]. As one of the high-performance fibers, parameters. Recently, it has been demonstrated that the textile Polytetrafluoroethylene (PTFE) fibers exhibit ultra-low friction structures, such as weaves [14,15] and weft densities [16], coefficient and excellent chemical resistance, but poor wear showed an important impact on the wear performance of such resistance, whereas Kevlar fibers are characterized by high materials. However, even without considering the influence of modulus, high strength, and excellent wear resistance. the resin matrix, surface treatment, filling of particles, weaves, Combining the benefits of the PTFE fibers and Kevlar fibers and so on, just for a specific structure fabric, which we could into a single composite, The PTFE/Kevlar fabrics are woven consider as a two-component (weft and warp) material system, out and usually used as frictional materials in aviation textile structures will make the components’ distribution of bearings and bushings [3,4]. The antiwear performance is such materials uneven [17]. As shown in Figure 1, by taking one of the important indexes for the life evaluation of such a horizontal section, the wear geometry of warp and weft fabrics. Many researchers have made numerous attempts changes with the section height, which can be equivalently to enhance the antiwear performance of such fabrics. Such expressed as the wear depth (To distinguish clearly, the color fabrics being immersed in a resin matrix is a usual method; of the wear geometry is different from the yarns intentionally). thus, it becomes a multiple composite system composed of As we all know, the components’ distribution area ratios at the the fabric and resin matrix. However, the interfacial adhesion wear interface have an important influence on the antiwear between the fibers and the resin matrix is proved to be an properties. So, the wear behavior changes with the wear important factor in the antiwear performance [5-6]. Therefore, geometry variation caused by the textile structure during the various surface treatment methods, such as plasma treatment wear process [17,18]. [7-9], strong HNO3 oxidation [10], and silane coupling agent modification [11], were applied to increase the quantity of the However, hardly any literature is available on the study of the surface functional groups on the surface of the fibers, and thus, fabric wear process and behavior based on the components’ http://www.autexrj.com 295 AUTEX Research Journal, Vol. 17, No 4, December 2017, DOI: 10.1515/aut-2016-0015 © AUTEX Figure 1. Schematic showing the variation of the components’ area ratio on the worn surface area ratio on the worn surface. Hence, in this paper, the 2.3. Wear test and method components’ area ratio on the worn surface of the PTFE/Kevlar twill fabric was analyzed by the wear experiment and by the The wear test of the PTFE/Kevlar twill fabrics was done on the theoretical calculations with our previous wear geometry model MMU-5G wear testing apparatus. As shown in Figure 2, a ring- [17]. The wear process and behavior of the PTFE/Kevlar twill on-plate contact form was utilized. An ASTM 1045 steel ring, fabric were investigated under dry sliding conditions against outer diameter 26 mm, inner diameter 20 mm, and chamfer AISI 1045 steel by using a ring-on-plate tribometer. The 0.5 mm, was used as the upper specimen, and an ASTM morphologies of the worn surface were observed using a 1045 steel plate, diameter 43 mm and thickness 3 mm, was confocal laser scanning microscopy (CLSM). The relationship used as the lower specimen. The pre-treatment approaches of between the antiwear performance and the components’ area the upper and lower metal specimens were listed as follows. ratios on the worn surface was analyzed. The lower specimen was polished with 150# and 400# water sandpapers. The upper specimen was polished with 600#, 800#, and 1200# water sandpapers. Moreover, both of the 2. Experimental lower and upper specimens were cleaned for 15 min in alcohol by ultrasonic waves. Then, the PTFE/Kevlar fabric was bonded 2.1. Materials on the surface of the lower specimen with a small amount of the phenolic-acetal resin adhesive and cured at 180°C for 2 h The Kevlar fiber (density 1.44 g/cm3, tensile modulus 123 under the contact pressure of 0.2 MPa. When the test started, GPa, and tensile strength 3.4 GPa) was provided by Du Pont the load was applied downward through the upper specimen Corporation, USA. The PTFE fiber (linear density 500 den, against the lower specimen, on which the PTFE/Kevlar fabric break force 20 N, and tensile strength 4.0 g/den) was provided was bonded. The lower specimen was kept stationary and the by Shanghai Lingqiao Environmental Protection Equipment upper specimen was rotated for a certain period of time under Works Co., Ltd., China. The phenolic-acetal resin adhesive a prescribed set of working conditions. Then, the wear depth was provided by Shanghai Xinguang Chemical Plant, China. of the lower specimen was measured and the worn surface appearance was observed using a CLSM. Two different 2.2. Fabric working conditions (load 0.7 MPa, velocity 0.12 m/s, load 2.1 MPa, and velocity 0.36 m/s) were chosen for each test. Five The PTFE/Kevlar fabric was woven by a rapier loom. The samples were repeated. weave was twill, as shown in Figure 1. The warp density and the weft density were, respectively, 185 ends/10 cm and 323 The specific wear rates were calculated using the following picks/10 cm. The thickness was 0.46 mm. The PTFE/Kevlar equation: fabrics were dipped in acetone for 12 h, cleaned in the acetone solution, boiled for 20 min in distilled water, and then dried in ω = ΔV / FL (1) an oven at 80°C for 1 h. http://www.autexrj.com/ 296 AUTEX Research Journal, Vol. 17, No 4, December 2017, DOI: 10.1515/aut-2016-0015 © AUTEX Figure 2. Test setup and schematic diagram of the ring-on-plate contact form where, ω is the specific wear rate in m3/(Nm), ΔV is the volume 0.36 m/s. In Figure 3(b), the wear depths of all the five samples loss in m3, F is the applied normal load in N, and L is the total rise rapidly in the beginning and then rise slowly. The increase sliding distance in m. of load from 0.7 MPa to 2.1 MPa and velocity from 0.12 m/s to 0.36 m/s have a small effect on the wear depth. From Figure 3(c), it can be seen that the wear rates of five samples drop 3. Results and discussion fast, after keeping around a certain value under 0.7 MPa and 0.12 m/s. When the working conditions change to 2.1 MPa and 3.1 Tribological performance 0.36 m/s, the wear rates of five samples drop markedly. This is because the wear depth increment is less than the increment Figure 3 shows the relationship of the friction coefficients and of load and velocity; from equation (1), the wear rates decrease wear depths, and the wear rates changing with the wear time with the increase in load and velocity.
Details
-
File Typepdf
-
Upload Time-
-
Content LanguagesEnglish
-
Upload UserAnonymous/Not logged-in
-
File Pages8 Page
-
File Size-