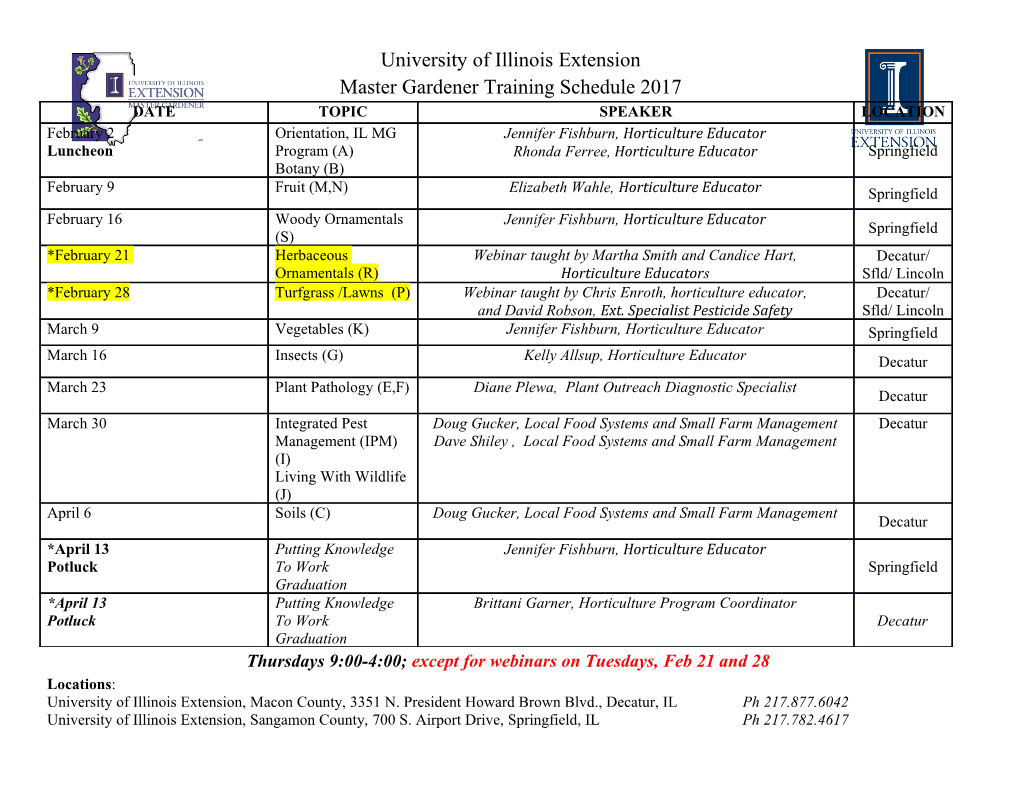
FACILITIES INSTRUCTIONS, STANDARDS, AND TECHNIQUES Volume 3-3 ELECTRICAL CONNECTIONS FOR POWER CIRCUITS Internet Version of This manual Created August 2000 FACILITIES ENGINEERING BRANCH DENVER OFFICE DENVER, COLORADO The Appearance of the Internet Version of This Manual May Differ From the Original, but the Contents Do Not UNITED STATES DEPARTMENT OF THE INTERIOR BUREAU OF RECLAMATION NOVEMBER 1991 CONTENTS Section Page 1. Purpose ........................................................... 1 2. Scope ............................................................ 1 3. Characteristics of Conductors ......................................... 1 3.1. Properties of conductor metals ................................... 1 3.2. Oxidation of conductors ......................................... 3 3.3. Corrosion of conductors ......................................... 3 3.4. Expansion of conductors ........................................ 4 3.5. Annealing of conductors ........................................ 4 3.6. Plating of conductors ........................................... 4 3.7. Anodizing of aluminum .......................................... 5 4. Preparation of Conductors ........................................... 5 4.1. Cleaning conductors ............................................ 5 4.2. Joint compounds .............................................. 5 5. Connections ....................................................... 6 5.1. General ....................................................... 6 5.2. Fusion connections ............................................. 6 5.3. Pressure connections ........................................... 7 5.4. Selection of connectors ......................................... 7 6. Procedure for Making Connections .................................... 9 6.1. Aluminum-to-aluminum bus ...................................... 9 6.2. Aluminum-to-copper or -bronze (tinned or untinned) bus .............. 9 6.3. Copper-to-copper or bronze-to-bronze connections .................. 9 6.4. Aluminum cable to connector joints .............................. 10 6.5. Cable joints .................................................. 10 6.6. Torque moments and procedures for bolted connections ............. 11 7. Temperature Considerations ......................................... 12 7.1. Current and temperature limitations . ............................. 12 7.2. Temperature of connections .................................... 12 7.3. Measurement of connection temperature ......................... 13 7.4. Thermographic (infrared) surveys ............................... 13 Bibliography ........................................................ 17 i (FIST 3-3 11/91) CONTENTS (Cont.) TABLES Page 1. Properties of conductors ............................................. 2 2. Electrolytic series .................................................. 4 3. Recommended electrical connectors ................................... 8 4. Recommended tightening torque on aluminum and silicon bronze bolts ..... 11 5. Temperature sensitive paints, crayons, and other materials ............... 14 6. Some infrared testing services ....................................... 17 FIGURES Page 1. Electrolytic current density diagram .................................... 8 2. Clamp tightening sequences ......................................... 11 (FIST 3-3 11/91) ii 1. Purpose which is both impermeable and protective in nature, forms quickly on exposed Operating experience with high-voltage power aluminum. Once stabilized, the oxide systems has shown that defective electrical prevents further oxidation. For highly connections are involved in many circuit or corrosive environments, a proper equipment failures. This chapter is designed to selection of alloy or anodization may be be used as a guide in the assembly and used. preventive maintenance of efficient electrical connections for power circuits. An efficient Arcing effects: Aluminum resists pitting connection being defined as one which from arcs better than any other metal. exhibits minimum resistance, both at initial assembly and in the long run. Galvanic action: Aluminum is one of the most anodic metals. When placed with 2. Scope copper or steel in an electrolyte (e.g., water) the potential difference between Data and experience gained through years of the conductors varies proportionally with testing and actual usage on power circuits by the distance between them in the both manufacturers and field organizations are electrolyte series (see table 2, section included. The actual test and procedures are 3.3.1). This difference causes a flow of beyond the scope of this chapter, however, electrons pitting the aluminum but leaving their results are incorporated in the the cathodic material unharmed. recommendations. Properties of conductor metals and recommended methods of making Insulation compatibility: Aluminum ex­ connections are discussed to illustrate the hibits none of the sulfur combining need for the proper selection of connectors; properties of copper nor does it produce the proper preparation of conductors; and the soaps by combining with oil. Usual proper application of fusion, compression, and insulating materials do not adhere to the bolted connectors. aluminum. 3. Characteristics of Conductors Advantages: For equal ampere ratings, an aluminum conductor must have 1.66 3.1. PROPERTIES OF CONDUCTOR times the cross-sectional area of a copper METALS.- conductor. At this gauge, aluminum has 75 percent the tensile strength and 55 3.1.1 Aluminum.- Aluminum, the most percent of the weight of copper. The abundant of all metals, is never found in larger size, in spite of its higher its pure state because of its affinity for resistance, keeps the conductor cooler other elements. This affinity enables a and also helps keep the corona loss wide range of alloying characteristics; down. However, its required larger size however, it also increases refinement restricts its use in applications (i.e., costs and lowers the conductivity. enclosed switchgear, etc.) where there are space limitations to be considered. Ductility: Easily worked by rolling, drawing, spinning, extruding, or forging. 3.1.2. Copper.- Copper, a reddish material, is plentiful in nature and easy to process. Corrosion resistance: Very good except in Because of the abundance, ease of a saline atmosphere. A tough, very hard, manufacture, and, therefore, low cost, invisible, and high resistance oxide, 1 (FIST 3-3 11/91) copper was once the most widely used When the copper is heated (e.g., by bad electrical conductor. Currently copper has connection), more oxides are formed. increased in cost considerably and its These high-resistance oxides will availability is limited causing aluminum to be continue to increase the heat until the used more readily as an electrical conductor. conductor breaks. At temperatures above 88 EC (180 EF), copper oxidizes in dry air. Ductile: Can be cast, forged, rolled, Copper is oxidized in an ammonium drawn, and machined. Hardens when environment and is also affected by sulfur worked, however, annealing will restore dioxide. soft state. Alloying: Manganese, nickel, zinc, tin, and Corrosion resistance: Copper oxide forms aluminum harden copper and diminish its immediately upon exposure to the ductility. Manganese, phosphorous, and atmosphere. Once stabilized, this oxide tin increase the tensile strength. prevents further oxidation of the copper. Table 1. - Properties of conductors Properties Pure aluminum Pure Copper Low-alloy steel Electrical conductivity 62 percent 100 percent 12 percent (by volume at 20 EC). Electrical conductivity 214 percent 100 percent – (by mass at 20 EC). Thermal conductivity 218 391 59.8 [W/(m.K)]. Corrosion resistance. Good2 (depending on Very good. Poor. atmosphere and alloy). Tensile strength. 89 600 MPa 172 400 MPa 517 000 to 620 500 MPa (13 000 lb/in2) (25 000 lb/in2) (75 000 TO 90 000 lb/in2) Elastic limit1 34 500 Mpa 55 200 Mpa 60 to 80 percent of maxi­ (5000 lb/in2) (8000 lb/in2) mum tensile strength. Density (g/cm3). 2.70 8.96 7.83 Linear density (kg/mm2)/m. 2.70 x 10-3 8.96 x 10-3 7.83 x 10-3 Thermal expansion 23.6 x 10-6/OC 16.5 x 10-6/OC 11.0 x 10-6/OC coefficient. Resistivity, MO, M 0.28 0.17 0.7 to 1.2. Melting point. 667 OC 1084 OC 1484 OC (1233 OF) (1983 OF) (2793 OF) 1Cold flow, deformation as a result of exceeding the elastic limit by either compression or elongation may occur if this stress is exceeded. 2Aluminum has excellent resistance to atmospheric corrosion; however, galvanic erosion is included in its resistance. (FIST 3-3 11/91) 2 Brass: Low-conductivity, high 3.2.1. Copper oxide.- Copper oxide is strength alloy. generally broken down by reasonably low values of contact pressure. Unless Bronze: Good conductor and atmo­ the copper is very badly oxidized, good sphere corrosion resistance. contact can be obtained with minimum cleaning. Copper chromium: Eighty percent conductivity of pure copper; 496,000- 3.2.2. Silver oxide.- Silver oxide is to 552,000-MPa (72,000- to 80,000- easily broken down by contact pressure 1b/in2) tensile strength. and forms less readily at elevated temperature. Thus it is good practice to Copper beryllium: Forty-eight percent silverplate copper contact surfaces that conductivity; (593,000-MPa (86,000- must be operated at elevated lb/in2) tensile strength. temperatures. Advantages: Because of copper's 3.2.3. Aluminum oxide.- Aluminum small size per current-carrying capac­ oxide is a hard, high-resistance film ity, second to silver, copper is widely
Details
-
File Typepdf
-
Upload Time-
-
Content LanguagesEnglish
-
Upload UserAnonymous/Not logged-in
-
File Pages20 Page
-
File Size-