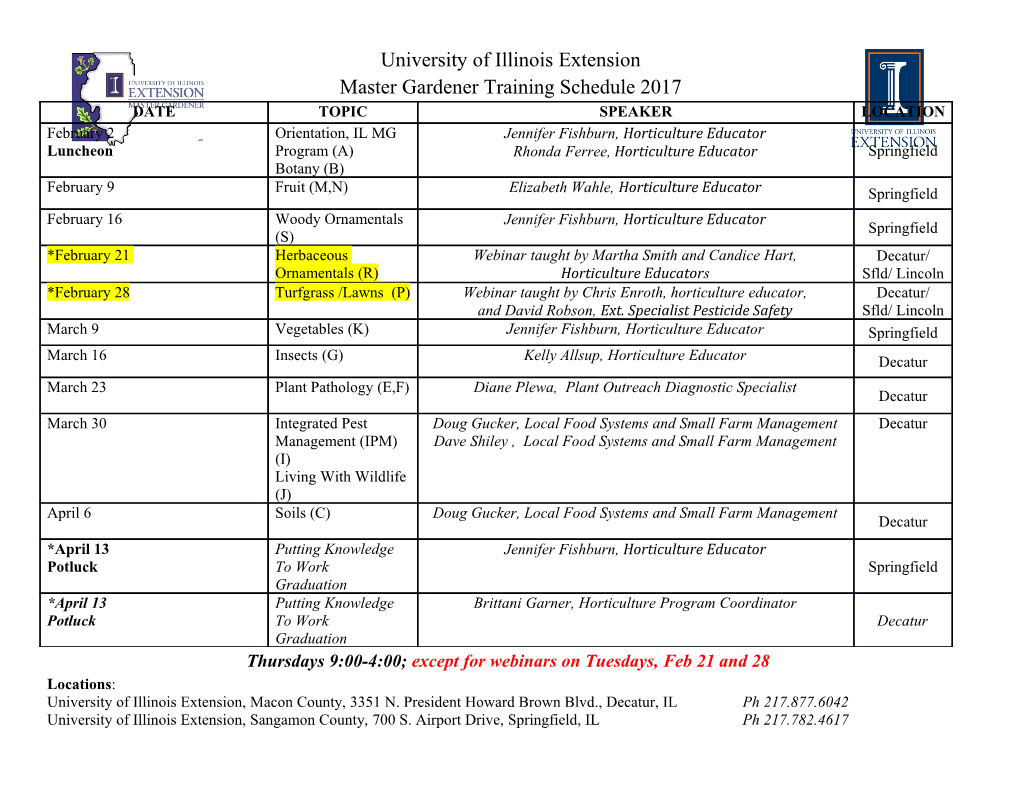
metals Article Microstructural Investigation of Stress Corrosion Cracking in Cold-Formed AISI 304 Reactor Ihho Park *, Eun-Young Kim and Won-Jon Yang Department of Materials Analysis & Evaluation, Korea Institute of Materials Science, Changwon 51508, Korea; [email protected] (E.-Y.K.); [email protected] (W.-J.Y.) * Correspondence: [email protected]; Tel.: +82-55-280-3156 Abstract: The aim of this study was to investigate cracking behavior of AISI 304 stainless steel that had been exposed to a high temperature MgCl2 solution for several years. The microstructure of the cracked area of the reactor was studied by in-depth microstructural characterization. Transgranular stress corrosion cracking only occurred at the cold-formed part of the reactor. It was observed that approximately 10–20% of the austenite matrix was transformed into alpha prime martensite due to cold forming at the lower head of the reactor. The preferential path for crack propagation was found to be strain-induced alpha prime martensite. The present study reveals that strain-induced martensitic transformation in austenitic stainless steel has a negative effect on stress corrosion cracking. Keywords: transgranular stress corrosion cracking; AISI 304; strain-induced martensite; electron backscattered electron microscopy; transmission electron microscopy 1. Introduction Austenitic stainless steels have been widely used as a reactor material for chemical plants due to their great corrosion resistance and workability along with good weldability. Since the 3XX series of austenitic stainless steels contain a minimum of 11 wt% of Cr content, they have a thin passive oxide film of chromia (Cr O ) and it allows the alloys to be highly Citation: Park, I.; Kim, E.; Yang, W. 2 3 resistant to general corrosion in an aqueous solution. However, austenitic stainless steels Microstructural Investigation of Stress Corrosion Cracking in Cold-Formed such as AISI 304 and 316 are known to suffer from SCC (stress corrosion cracking) [1–8]. AISI 304 Reactor. Metals 2021, 11, 7. SCC is considered to be one of the main damage mechanisms to cause failures of the com- https://dx.doi.org/10.3390/met1101 ponents in petrochemical industries. These failures have the potential to release hazardous 0007 substances or lead to a catastrophic event such as massive fires [9–13]. Research involved in stress corrosion cracking has been reported for decades, still the exact mechanism of Received: 7 December 2020 stress corrosion cracking is not fully understood since its occurrence and the type of cracks Accepted: 21 December 2020 widely vary under various environments. SCC could occur in susceptible alloys under Published: 23 December 2020 simultaneous exposure to a corrosive environment and sustained stress and the combina- tion of those three factors produce diverse cases of SCC. Accordingly, constant efforts to Publisher’s Note: MDPI stays neu- analyze cases of SCC in the industry field should be made and based on that, we would be tral with regard to jurisdictional claims able to approach a deep understanding of the SCC mechanism. Sometimes, a practical in published maps and institutional case provides us with valuable insights for understanding the phenomenon rather than a affiliations. well-designed laboratory experiment. The present study introduces a case of damage on a AISI 304 reactor for producing a PVC (polyvinyl chloride) stabilizer. An interesting point in this case is that only the bottom part of the reactor suffered from cracking. On the other Copyright: © 2020 by the authors. Li- hand, the column part of the reactor remained crack free. The column part of the pressure censee MDPI, Basel, Switzerland. This vessel reactor was fabricated by plate rolling and welding, and the concave shaped bottom article is an open access article distributed and top part of the pressure vessel reactor were manufactured by the cold forming process. under the terms and conditions of the Stress itself is a very important factor for inducing SCC. Depending on how we manipulate Creative Commons Attribution (CC BY) stress on the material, it could improve the susceptibility of the material or function in license (https://creativecommons.org/ the opposite way. It is known that introducing compressive stress to materials such as licenses/by/4.0/). shot peening aids in sustaining the occurrence of SCC [14–17]. In contrast, residual tensile Metals 2021, 11, 7. https://dx.doi.org/10.3390/met11010007 https://www.mdpi.com/journal/metals Metals 2021, 11, x FOR PEER REVIEW 2 of 10 Metals 2021, 11, 7 2 of 10 stress to materials such as shot peening aids in sustaining the occurrence of SCC [14–17]. In contrast, residual tensile stress from welding is known to promote SCC. However, cold workingstress from could welding have an is effect known on to SCC promote in both SCC. ways. However, Many studies cold workingrelated to could the influence have an ofeffect cold on forming SCC in or both cold ways. work Many on the studies SCC of related austenitic to the stainless influence steel of coldhave forming been reported or cold [18–23].work on The the results SCC of of austenitic the literature stainless survey steel showed have been a contrary reported tendency[18–23] .depending The results on of the the materialliterature and survey strain. showed For AISI a contrary 304 stainless tendency steel, depending it has been on agreed the material that the and resistivity strain. For of SCCAISI improves304 stainless if thesteel, applied it has beenstrain agreed level thatis above the resistivity 35% [19]. of However, SCC improves it is reported if the applied that thestrain susceptibility level is above of SCC 35% could [19]. However, increase drastically it is reported from that the the initial susceptibility to certain of low SCC level could of coldincrease working drastically [18,21]. from The the present initial case to certain could low be levelmeaningful of cold workingsince both [18 the,21 ].cold The worked present partcase and could rolled be meaningful and annealed since part both had the been cold exposed worked to part the andsame rolled corrosive and annealedenvironment part andhad showed been exposed cracking to the at sameonly the corrosive cold formed environment area during and showed service. cracking The present at only study the cold fo- cusedformed on area the microstructure during service. of The Cl-SCC present on studythe cold focused worked on regions, the microstructure especially the of Cl-SCCprefer- entialon the site cold and worked path of regions, cracking especially with the theaid of preferential microscopy. site Figure and path 1 exhibits of cracking a photograph with the ofaid the of actual microscopy. reactor Figurefor producing1 exhibits a PVC a photograph (polyvinyl of chloride) the actual stabilizer. reactor forA total producing of 14 re- a actorsPVC (polyvinyl made of AISI chloride) 304 stainless stabilizer. steel A totaloperated of 14 in reactors the plant. made Every of AISI reactor 304 stainlesshas been steel ex- posedoperated to the in thesame plant. environment Every reactor with hasa pressure been exposed of 9 bar, to 50~180 the same °C. environment To produce a with PVC a pressure of 9 bar, 50~180 ◦C. To produce a PVC multiple stabilizer, MgCl , Al(OH) , NaOH, multiple stabilizer, MgCl2, Al(OH)3, NaOH, water, etc. is mixed with agitation2 in3 the re- actor.water, The etc. pH is mixed level of with the agitationmixture compounds in the reactor. in the The reactor pH level is known of the mixtureto be a neutral compounds level. Duringin the reactor the period is known of turn to around, be a neutral surface level. cracks During were found the period in two of reactors turn around, that had surface been operatedcracks were for foundtwo years. in two However, reactors thatthe hadlife ti beenme of operated those two for tworeactors years. was However, much shorter the life thantime the of thoselife expectancy two reactors of a was reactor, much which shorter is 20 than years. the In life addition, expectancy other of reactors a reactor, with which no cracksis 20 years. have operated In addition, for otherover 10 reactors years in with service. no cracks To determine have operated the reason for over for shortening 10 years in service. To determine the reason for shortening the life time of the reactor and prevent the the life time of the reactor and prevent the recurrence of cracking, the following failure recurrence of cracking, the following failure analysis was conducted. analysis was conducted. Figure 1. (a) Photographs of polyvinyl chloride (PVC) stabilizer reactors. (b) Top part of the reactor was the cutoff. Even Figure 1. (a) Photographs of polyvinyl chloride (PVC) stabilizer reactors. (b) Top part of the reactor was the cutoff. Even though it is not shown in this image, the bottom part of the reactor cutoff was the same way as the failure analysis. though it is not shown in this image, the bottom part of the reactor cutoff was the same way as the failure analysis. 2. Materials and Methods 2. MaterialsFigure 1 andshows Methods the actual reactors in the plant and the top part of the reactor top area was cutFigure off. 1The shows bottom the part actual of the reactors reactor in wa thes plantcut off and in the the same top part way. of Figure the reactor 2 shows top a samplearea was achieved cut off. from The the bottom bottom part of of the the reactor. reactor The was thickness cut off in of the the samereactor way. was Figure 20 mm2 andshows cracks a sample from inner achieved surface from could the bottom be observed of the visually. reactor. TheDepth thickness of propagation of the reactor was con- was firmed20 mm to and be approximately cracks from inner 5 mm, surface ofcould the total be observedthickness visually.of the reactor.
Details
-
File Typepdf
-
Upload Time-
-
Content LanguagesEnglish
-
Upload UserAnonymous/Not logged-in
-
File Pages10 Page
-
File Size-