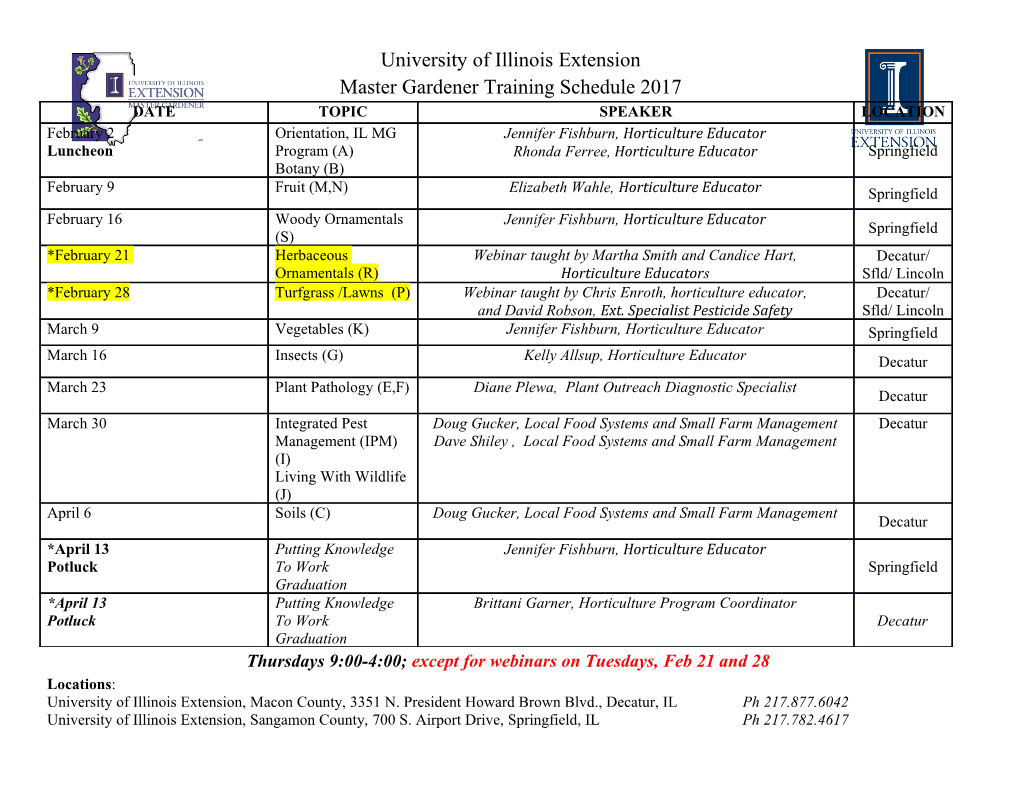
Glass Technol.: Eur. J. Glass Sci. Technol. A, December 2015, 56 (6), 203–213 Alkali salt vapour deposition and in-line ion exchange on flat glass surfaces Stefan Karlsson,1,2* Sharafat Ali,3 René Limbach,2 Michael Strand3 & Lothar Wondraczek2 1 Glafo – the Glass Research Institute, PG Vejdes väg 15, SE-351 96 Växjö, Sweden 2 Otto Schott Institute of Materials Research, Friedrich Schiller University of Jena Fraunhoferstraße 6, D-07743 Jena, Germany 3 Faculty of Technology, Linnæus University SE-351 95 Växjö, Sweden Manuscript received 16 January 2015 Revision received 20 May 2015 Manuscript accepted 10 June 2015 This study suggests a different route for the modification of flat/float glass surfaces; i.e. exchange of ionic species originat- ing from in-line vapour deposition of salt as compared to the conventional route of immersing the glass in a molten salt bath. The aim of this work is to develop a more flexible and, eventually, more rapid process for improving the mechanical strength of flat glass by introducing external material into the surface. We discuss how chemical strengthening can be performed through the application of potassium chloride on the glass surface by vapour deposition, and in-line thermally activated ion exchange. The method presented here has the potential to be up-scaled and to be used in in-line produc- tion in the future, which would make it possible to produce large quantities of chemically strengthened flat glass at a considerably lower cost. 1. Introduction the defect resistance of this surface.(1–3) As a conse- Glassy materials provide a unique set of properties, quence, the practical use of glass is often limited by its such as transparency, high hardness and good chemi- brittleness, which is associated with statistical failure. cal durability, forming ability, low cost production There exist a variety of ways to increase the and the possibility of recycling. They are therefore strength of glass;(1) most of them involve modifica- used in a wide range of applications, e.g. windows, tions of the glass surface.(5) A method, which has containers, displays, thermal insulation, optical received much attention, is chemical strengthening. lenses, data transport, or, e.g. as bioactive materials. It is based on the exchange of smaller ions in the The fact that glass is a relatively hard material origi- glassy matrix by larger ions from a molten salt, e.g. nates from the nature and the alignment of bonds of Na+ is replaced by K+, see Figure 2. The larger ions are the vitreous network. The mechanical strength, on literally squeezed into the sites of the smaller ions, the other hand, mainly depends on the presence of generating compressive stresses in the glass surface, defects in the glass surface, see Figure 1, and, hence, which counteract external tensile stresses. 6 The most commonly described route of chemical + + + micro-cracks visual cracks strengthening is K –(Li ,Na ) ion exchange, which was discovered independently by Kistler(6) and Acloque.(7) 5 Chemical strengthening of glass has recently been Theoretical strength ) 4 a P M / Strength of glass fibres σ ( 3 og l 2 Processed flat glass 1 -9 -8 -7 -6 -5 -4 -3 -2 -1 0 log(effective flaw depth/mm) Figure 1. The effect of surface flaws on the tensile strength of soda–lime–silica glass(4) 1 Corresponding author. Email [email protected] Figure 2. Schematic ion exchange process for the modifica- DOI: 10.13036/1753-3546.56.6.203 tion of glass surfaces [Colour available online] Glass Technology: European Journal of Glass Science and Technology Part A Volume 56 Number 6 December 2015 203 S. KARLSSON ET AL: ALKALI SALT VAPOUR DEPOSITION AND IN-LINE ION EXCHANGE ON FLAT GLASS Figure 3. Schematic illustration of the in-line vapour deposition of salt for chemical strengthening of flat glass [Colour available online] reviewed by several authors.(5,8–11) Although this manufactured by immersing a flat glass sheet into a method was introduced more than half a century ago, molten salt bath. However, there are also other meth- it has failed to be widely adopted in the market for a ods for chemical strengthening such as salt-spray as long time. However, in recent years, large specialty has been both studied(20) and commercialised, in the glass companies launched chemically strengthened former GDR(21,22) and recently.(23) In this study we flat glass, e.g. Corning Gorilla Glass,(12) Schott Xensa- suggest vapour deposition and in-line alkali metal tion,(13) AGC Dragontrail(14) and NEG CX-01.(15) Nowa- ion exchange, see Figure 3. This method is based on days, most touchscreens in commercially available an earlier study by Sil’vestrovich et al.(24,25) However, smartphones are made of chemically strengthened in contrast to the approach of Sil’vestrovich et al, flat glass,(16) regardless of the considerably higher cost where the vapour deposition and the ion exchange which is associated with the production process of process were separated into two different steps, we such glass. However, for other applications, where combine both processes into one step, which enables a larger glass sheets are required, such as covers for novel route for the fabrication of low-cost chemically photovoltaic cells, car windows, facades or furniture, strengthened glass. the production cost of chemically strengthened glass is still too high. Recently, alternative approaches have 2. Experimental Procedure been presented, where the glass is spray-coated with a salt mixture and subsequently dried as well as heat The glass used here was a conventional soda–lime– treated.(17) silica float glass provided by Pilkington Floatglas AB, Chemical strengthening of glass is complex and with a nominal thickness of 4 mm, denoted as ‘Ref’ in many parameters affect the ion exchange process as this paper. The chemical composition was analysed well as the resulting strength:(18) using different wet chemical methods, e.g. atomic i. The effect of temperature on the interdiffusion absorption spectroscopy (AAS). The dissolution of coefficient, the sample and quantification followed BS 2649,(26) ii. The time of exchange, except for TiO2 and SO3. Due to safety reasons nitric iii. The interfacial energy between the glass and the acid and hydrochloric acid replaced perchloric acid. salt The normalised chemical composition of the float iv. The phase boundary reaction barrier and adsorp- glass used in the experiments is given in Table 1. tion enthalpy at the glass surface, v. The glass composition, Table 1. Normalised chemical composition of the float glass vi. The exchanging pair of ions, used in the experiments vii. The influence of temperature on relaxation. wt% mol% With the present knowledge, many of these param- SiO2 72·80 71·32 eters have been optimised for specific products. There Na2O 13·39 12·72 is, however, another possibility for a further cost re- K2O 0·04 0·03 Al2O3 0·12 0·07 duction in the fabrication of chemically strengthened MgO 4·07 5·94 glass namely by optimising the large-scale process. CaO 9·25 9·71 Optimisation of industrial processes is most often Fe2O3 0·10 0·04 SO 0·21 0·16 performed by an automation of the process.(19) 3 TiO2 0·02 0·01 In principal, chemically strengthened flat glass is Sum 100 100 204 Glass Technology: European Journal of Glass Science and Technology Part A Volume 56 Number 6 December 2015 S. KARLSSON ET AL: ALKALI SALT VAPOUR DEPOSITION AND IN-LINE ION EXCHANGE ON FLAT GLASS to Green’s function,(27) where C is the concentration, x the depth and t the time: Axæö- 2 ç ÷ C = expç ÷ (1) t çèø4Dt÷ Reflectance,R %, was determined with an Agilent Technologies UV-VIS-NIR spectrometer; model Cary 5000, equipped with an integration sphere. The reflectance was measured at the hot-end of the glass Figure 4. Schematic illustration of the experimental setup samples in a range of 200–2500 nm and with scan rate of the vapour deposition and in-line ion exchange [Colour of 10 nm/s. The refractive index was calculated from available online] the reflectance spectra using to Equation (2), wheren s is the refractive index of the glass at 520 nm. It should The experimental setup is given in Figure 4. An be noted that other equations can be used to calculate aerosol generator from PALAS Particle Technology the refractive index from the reflectance spectra; as model AGK 2000 was used. It was consistently run consequence, the current results are comparable to at 2 bar pressurised air in the experiments. The each other, but not to other published results. tube furnace was a Carbolite Tube Furnace model 1++RR 12/65/550 with a maximum temperature of 1200°C. n = (2) s - The temperature distribution was measured with 1 R thermocouples – in the centre of the furnace it was Infrared reflectance spectra (IR-RS) were measured 800°C (initially 700°C), while the specimen was with a Shimadzu Scientific Instruments spectrometer, placed at the cold end of the furnace where the tem- model IRAffinity-1. The reflectance spectra were perature was around 450°C. For the ion exchange, recorded over the range 400–4000 cm−1, with a resolu- the glass specimens were cut into pieces of 2×10 cm, tion of 4 cm−1. All spectra were averaged over 64 scans cleaned with ethanol and distilled water, and subse- and transformed according to the Kramers-Kronig quently dried for weighing. Reagent grade quality transformation. Aluminium mirror was used was KCl delivered by Scharlau Chemie SL was mixed with used as a baseline. The IR-RS spectra were measured distilled water to obtain solutions of 10, 15 and 20 g at the hot end of the glass samples.
Details
-
File Typepdf
-
Upload Time-
-
Content LanguagesEnglish
-
Upload UserAnonymous/Not logged-in
-
File Pages11 Page
-
File Size-