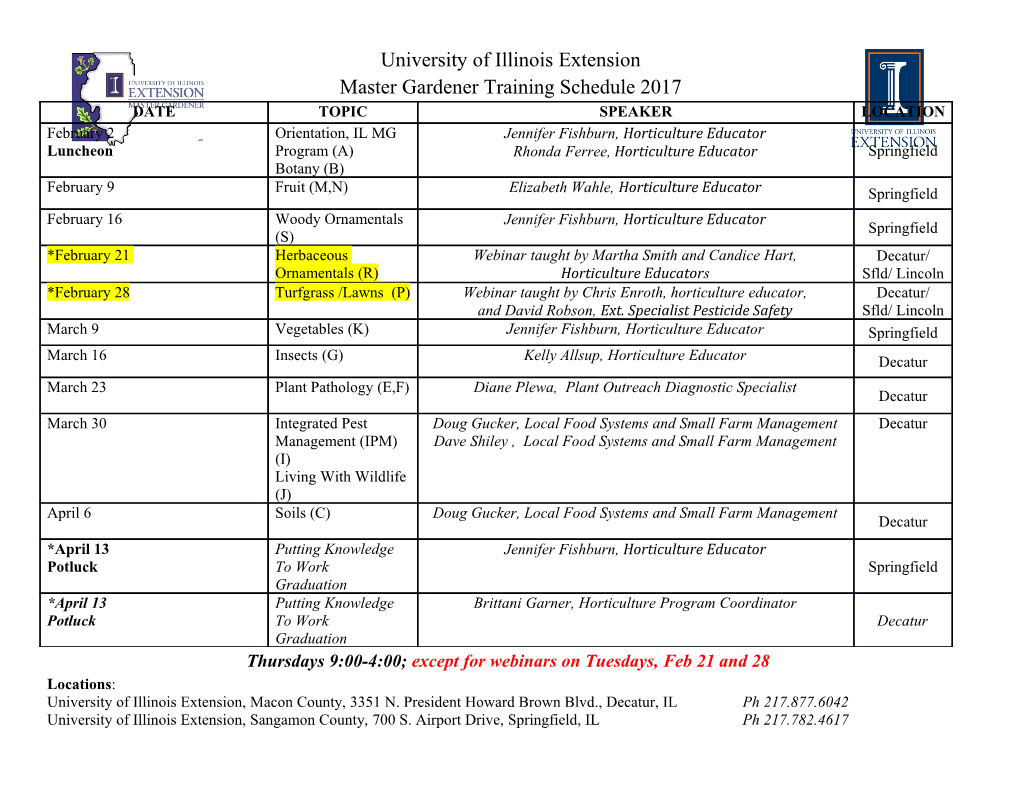
Low cost concrete bricks using marble slurry as a raw material Manpreet Singh1*, Anshuman Srivastava2*, Pratyaksh Agarwal3* 1 Research Scholar, Department of Civil Engineering, BITS-PILANI, Pilani, India 2 Associate Professor, Department of Civil Engineering, BITS-PILANI, Pilani, India 3 Under Graduate Student, Department of Civil Engineering, BITS-PILANI, Pilani, India *Email: [email protected] TP: +919780508420 ABSTRACT: Marble has been used in the construction industry for a long time. The processing of marble leaves behind a waste at quarry or at the sizing industry generally left unattended. This waste has reached as high as millions of tons. In this paper the utilization of waste marble slurry as an additive in industrial concrete brick production has been the main objective. Marble Slurry wastes were collected from marble processing units in Rajasthan area, India and brick mortars were prepared with varying proportions of cement, sand and marble dust. Varying percentages of dried marble slurry from 75 to 90 percent as a replacement of natural sand in the mortar were used. The crushing strength was achieved in the range of 7 to 10.5 M Pa. The water absorption was in the range of 12 to 15 % by weight which lies well within the range of second class bricks according to Indian and American standards. The results conclude that the bricks containing Marble slurry as a raw material prove to be 10 % less costly compared to the bricks from the normal mortar mix. This would help in reducing the environmental hazards caused due to dumping of waste marble slurry and help building sustainable infrastructure, also promoting low cost housing. Keywords: Crushing strength, Low cost housing, Marble Slurry Waste, Sustainable Infrastructure, Water absorption. INTRODUCTION Sustainable development is the prime concern of the present world. There has been a constant depletion of natural resources and an increase in global warming. In the construction industry, cement is the most extensively used building material and has a very high carbon footprint. With the ever-increasing rise in buildings, its use has created a big environmental concern. Thus, various researches are being conducted to find out alternative construction materials in the wastes generated by various industries. One such waste is the marble slurry. There has been a widespread increase in the demand of marble products giving a boost to marble industry. It has increased the waste generation during quarrying and processing in form of marble slurry. Marble slurry can lead to water clogging, increasing alkalinity of the topsoil and loss of soil fertility. It can also harm the water environment creating hazards to water animals and plants. The dust generated can also blanket the surroundings and cause breathing problems. Thus, a widespread need has been observed in order to make this industry environmentally sustainable. Rajasthan state in India is known as mineral majestic State as it produces more than 50 types of mineral and rocks. The state is blessed with vast deposits of natural rocks known as “stones” and a few essentials are Granite, Marble, Sandstone, Limestone, Slate and Quartzite. Perhaps, nowhere in the world, any other society is found to be so engraved with stone and stone based products as it is in Indian state of Rajasthan. The ever increasing popularity of the marbles of Rajasthan, growing demand for finished and unfinished products, discovery of new marble deposits and growing private and public supports have led to a significant growth in Marble Industry of this State. As a result, number of marble quarries as well as marble processing units has significantly gone up mainly during last one decade. However, whereas there is significant growth in production of finished and unfinished marble products, there is also simultaneous rise in waste generation as well; thereby causing concern towards the deteriorating environmental quality. A wide spread need is being felt to make this industry environmentally sustainable. In a specific case of Orosei Marble district in NE Sardinia studied by Marras. et al. (2011) the use of marble slurry along with the other traditional constituents has resulted in improvement of quality of bricks. Aukor (2009) studied possibility of using marble sludge powders (MSPs) as a substitute for limestone in bricks. Interpretation of the results have shown that appropriate incorporation of MSP can result in favorable characteristics in terms of compressive strength 9 N/mm2 at 28 days, and water absorption (7%), anticipating a complimentary usage of sludge as a by-product instead of being disposed as a waste. Hamza et al., (2011) utilized marble and granite waste of different sizes in the manufacturing of concrete bricks,. The produced bricks with full replacement of conventional coarse and fine aggregates with marble waste scrapes and slurry powder of content up to 40%. Bilgin et al., (2012) investigated the usability of waste marble dust as an additive material in industrial brick. It was found that the amount of marble dust additive had positive effect on the physical, chemical and mechanical strength of the produced industrial brick. Waste marble is well usable instead of the usual aggregate in the paving block production (Gencela et al., 2012). Indian Environmental Society (IES) has been working on the problem of Marble slurry for the last few years in Udaipur, Rajasthan. They demonstrated and validated the technology for manufacturing of marble slurry bricks. Dhanapandian, et al. (2009) has worked to characterize and evaluate the possibilities of using the granite and marble sawing wastes, as alternative raw materials in the production of bricks. The results showed that granite and marble wastes can be added up to 50% weight into the raw clay material in the production of bricks. EXPERIMENTAL PROGRAM A number of trial mix designs were used to study the effect of replacement of natural sand, lime or clay with marble dust with minimum cement content in producing mortar bricks. The cement used was OPC 43 grade and dried waste marble slurry was used as a replacement of sand. LABORATORY TRIALS Bricks of size 9’ X 4.5’ X 3’ with 4 mix designs were casted with varying percentages of dried marble slurry from 75 to 90 percent as a replacement of natural sand in the mortar. The strength in direct compression and water absorption test for the casted bricks were conducted conforming to IS 3495 – 1992 and ATSM C-140. The strengths are also compared to the normal cement mortar bricks without any replacement of cement or sand with waste marble slurry. PHYSICAL PROPERTIES The cement used was OPC 43 conforming to ASTM type 1. The mixing water was ordinary tap water. Locally available sand with a fineness modulus of 2.80 was used conforming to grading zone II of Table of IS 383-1970. Marble slurry was procured from a mining site in Kishangarh, Rajasthan, India. The slurry was dried in oven at 110 °C for 2 days to remove the absorbed moisture. The waste marble slurry had a Blaine’s fineness of 261.1 m2/kg and moisture content of 4 %. Around 80% percent of the weight passed through 300 micron sieve. The specific gravity determined using Le Chatelier’s flask in accordance with ASTM C188-95 “standard test method for determining density of hydraulic cement” was 2.68. CASTING OF BRICKS Cement mortar bricks of 9’ X 4.5’ X 3’ with 4 mix designs were casted with varying percentages of dried marble slurry from 75 to 90 percent as a replacement of natural sand in the mortar using a hydraulic brick press applying 100 tones of force during compaction by Hydraulic toggle Indexing. The mixes were named as M-1 – M-4 with increasing percentage of marble dust. 20 samples of each mix were casted and tested. The ingredients were thoroughly mixed and casted in the brick making machine. The mix design compositions are tabulated in Table 1. Table 1. Percentage Mix Compositions Mix Marble dust Sand Cement Lime design % Kg/m3 % Kg/m3 % Kg/m3 % Kg/m3 M-1 75% 3.03 10% 0.4 10% 0.4 5% 0.2 M-2 80% 3.05 12.50% 0.48 7.50% 0.28 - - M-3 85% 3.16 7.50% 0.28 7.50% 0.28 - - M-4 90% 3.24 - - 10% 0.36 - - TESTING OF BRICKS The casted bricks were cured for 28 days. Compressive Strength and water absorption test conforming to IS 3495 and ASTM C-140 were conducted. Table 2. Standard Classes of Bricks (as per IS 1077 Burnt Clay Bricks) Class designation Average compressive strength not less than (MPa) 5 5 7.5 7.5 10 10 Table 3. Standard Grades of Bricks (as per ASTM C – 55 Concrete Block) Grade Compressive strength Compressive strength (MPa), avg. of 3 units (MPa), individual unit N 24.1 20.7 S 17.3 13.8 RESULTS AND DISCUSSIONS The results for compressive strength and water absorption are shown below in Table 4. Table 4. Compressive Strength and Water Absorption of Bricks Mix Design Average Average Average compressive Compressive Water absorption strength strength (kg/cm2) (MPa) M-1 80 7.85 12.65% M-2 86.11 8.45 11.24% M-3 84.15 7.04 10.22% M-4 98.15 9.74 10.93% Compressive Strength Compressive strength test was performed according to IS 3495 part 1 (1992) and ASTM C-140. According to IS 1077 (1992) the average compressive strength of 10 blocks should not be less than 7.5 MPa for 2nd class bricks. All the samples prepared give an average compressive strength of more than 7.5 MPa thus making them suitable for construction practices like low cost housing and other housing projects. However, according to ASTM C-55 compressive strength for S class bricks for an individual unit must be 13.8 MPa.
Details
-
File Typepdf
-
Upload Time-
-
Content LanguagesEnglish
-
Upload UserAnonymous/Not logged-in
-
File Pages8 Page
-
File Size-