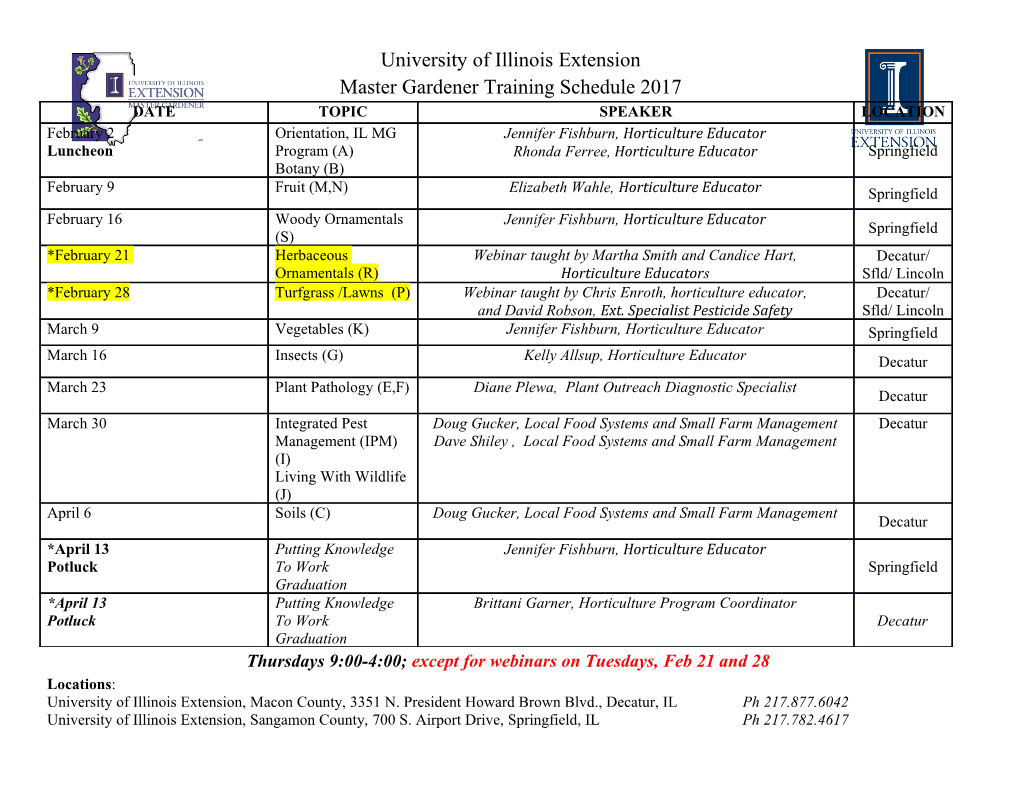
materials Article Influence of Process Fluctuations on Residual Stress Evolution in Rotary Swaging of Steel Tubes Svetlana Ishkina 1,* , Dhia Charni 2, Marius Herrmann 1, Yang Liu 1,2,Jérémy Epp 2,3 , Christian Schenck 1,3, Bernd Kuhfuss 1,3 and Hans-Werner Zoch 1,2,3 1 Bremen Institute for Mechanical Engineering-bime, University of Bremen, Badgasteiner Str. 1, 28359 Bremen, Germany; [email protected] (M.H.); [email protected] (Y.L.); [email protected] (C.S.); [email protected] (B.K.); [email protected] (H.-W.Z.) 2 Leibniz Institute for Materials Engineering-IWT, Badgasteiner Str. 3, 28359 Bremen, Germany; [email protected] (D.C.); [email protected] (J.E.) 3 MAPEX Center for Materials and Processing, University of Bremen, Bibliothekstr. 1, 28359 Bremen, Germany * Correspondence: [email protected] Received: 8 February 2019; Accepted: 8 March 2019; Published: 14 March 2019 Abstract: Infeed rotary swaging is a cold forming production technique to reduce the diameter of axisymmetric components. The forming is achieved discontinuously by a series of radial strokes that are spread over the shell of the part. Due to tolerances within the rotary swaging machine, these strokes perform individually and the resulting stroke pattern is not homogeneous with regards to circumferential and longitudinal distribution. Nevertheless, in combination with the high number of performed strokes and the large contact area between the dies and the part, the external part properties, such as diameter, roundness and surface roughness, show even values along the finished part. In contrast, strength-defining internal part properties, like microstructure and residual stress components, are more sensitive to the actual pattern and temporal sequence of the individual strokes, which is investigated in this study. The impact of process fluctuations during the conventional process, which are induced by the tolerances of machine tool components, was verified by numerical simulations, physical tests and measurements of residual stress distributions at the surface and at depth. Furthermore, a method is introduced to maintain the stroke following angle D' at zero by flat dies, and thus the actual pattern and temporal sequence of the strokes was homogenized. The results show that the residual stress fluctuations at the surface could be controlled and reduced. Furthermore, it is demonstrated that the depth profile of the residual stresses at a distance of 300 µm from the surface developed independently from the process fluctuations. Keywords: finite element method; incremental bulk forming; cold forging; X-ray diffraction 1. Introduction Rotary swaging is an incremental cold forming process for reducing and profiling the cross section of axisymmetric components, such as bars and tubes. It is established in the automotive and aerospace manufacturing industries [1]. This production technique provides several advantages such as high static and dynamic strength due to strain hardening [2]. Additionally, by the use of hollow shafts and by the advantageous development of the wall thickness during rotary swaging, cost-effective production of lightweight components is possible due to the optimal use of material resources [3]. In infeed rotary swaging, the part is axially fed into the swaging head with the feed velocity vf (see Figure1). The diameter is reduced incrementally by a revolving and radially oscillating motion of (four) dies. This motion is induced by the rotating swaging axle that entrains the base jaws with cams on the top surface. These cams pass the cylinder rollers and push the tools inwards. The swaging head Materials 2019, 12, 855; doi:10.3390/ma12060855 www.mdpi.com/journal/materials Materials 2019, 12, x FOR PEER REVIEW 2 of 13 Materials 2019, 12, 855 2 of 13 of (four) dies. This motion is induced by the rotating swaging axle that entrains the base jaws with cams on the top surface. These cams pass the cylinder rollers and push the tools inwards. The swaging exhibitshead exhibits 12 cylinder 12 cylinder rollers. rollers. The oscillation The oscillation of the of dies the is dies initiated is initiated and controlled and controlled by the dimensionsby the anddimensions proportions and proportions of machine toolof machine components tool components in the swaging in the head swaging that constitute head that the constitute pressure the column betweenpressure thecolumn part between and outer the ring part of and the machineouter ring frame. of the Thesemachine components frame. These include components the dies, include the spacers, the basedies, jawsthe spacers, with cams the and base the jaws cylinder with cams rollers. and All the of thesecylinder machine rollers. parts All of feature these technicalmachine tolerances.parts Hence,feature thetechnical geometrical tolerances. deviation Hence, of thethe pressuregeometrical columns deviation that reassembleof the pressure with everycolumns single that stroke generatereassemble a scatterwith every within single the stroke impact generate pattern aon sca thetter surfacewithin the of theimpact part. pattern on the surface of the part. FigureFigure 1. 1. IllustrationIllustration of ofthe the swaging swaging head head for forinfeed infeed rotary rotary swaging. swaging. During the the closing closing of of the the swaging swaging dies, dies, the the part part may may be shifted be shifted backwards backwards due dueto the to die the angle die angle in the the reduction reduction zone zone that that is too is too steep steep to ensure to ensure self-locking. self-locking. When Whenthe plas thetic plasticdeformation deformation starts, the starts, thematerial material flows flows mainly mainly in the feed in the direction feed direction (positive (positivematerial flow), material but also flow), in the but negative also in direction the negative direction[4]. The resulting [4]. The sum resulting of the backward sum of theshift backward of the part shiftand the of thenegative part material and the flow negative constitutes material the flow constitutesaxial back pushing. the axial This back back pushing. pushing can This be backmeasured pushing during can the be process measured [5]. It duringis strictly the related process to [5]. the actual tribological conditions in the contact area between the part and dies. Consequently, the It is strictly related to the actual tribological conditions in the contact area between the part and impact pattern is further distorted. Despite this inhomogeneity and the discontinuous nature of the dies. Consequently, the impact pattern is further distorted. Despite this inhomogeneity and the process, the combination of the axial feed per stroke value lst of the part and the circumferential shift discontinuous nature of the process, the combination of the axial feed per stroke value l of the part of the dies between consecutive strokes allows for producing parts with constant external properties,st and the circumferential shift of the dies between consecutive strokes allows for producing parts with like final diameter, length, roundness and surface roughness, over the entire formed length [6]. constantDuring the external process, properties, every spot likeof the final finished diameter, part experiences length, roundness about 100 and effective surface strokes. roughness, over the entireSeveral formed studies length have [6 ].been During carried the out process, to establish every optimal spot process of the conditions finished part concerning experiences surface about 100quality effective and geometry, strokes. e.g., by analyzing the influence of dry process conditions [5], feed per stroke valuesSeveral [6], radial studies feed have per been stroke carried values out during to establish plunge optimal rotary process swaging conditions [7] or true concerning strain [8]. surface qualityFurthermore, and geometry, the internal e.g., properties by analyzing of the the part, influence such as ofits drymicrostructure, process conditions hardness [5 ],and feed residual per stroke valuesstress components, [6], radial feed which per strokeare important values during for its stre plungength, rotary have swagingbeen investigated: [7] or true Lim strain found [8]. Furthermore,that the thehardness internal at propertiesthe outer surface of the part,increased such aswith its microstructure,increasing diameter hardness reduction and residual of steel stresstubes components,[9] and whichKocich arestated important that rotary for its swaging strength, induces have been a strong investigated: fiber texture Lim foundin tungsten that the heavy hardness alloys at [10]. the outer surfaceSimulations increased are used with to investigate increasing the diameter process reduction and the material of steel behavior tubes [9 ]during and Kocich rotary statedswaging. that For rotary swagingexample, inducesthe material a strong flow fiber [4], plastic texture strain in tungsten [11] and heavy strain alloysrates [12] [10]. have Simulations been investigated. are used toThe investigate von theMises process equivalent and thestress material was examined behavior by during Ameli rotaryet al., swaging.who found For it to example, be directly the related material to flowthe [4], plastic strain [11] and strain rates [12] have been investigated. The von Mises equivalent stress was examined by Ameli et al., who found it to be directly related to the residual stresses [13]. They found that the residual stresses were mostly affected by the feed per stroke. Furthermore, Ghaei found, in his Materials 2019, 12, 855 3 of 13 finite element
Details
-
File Typepdf
-
Upload Time-
-
Content LanguagesEnglish
-
Upload UserAnonymous/Not logged-in
-
File Pages13 Page
-
File Size-