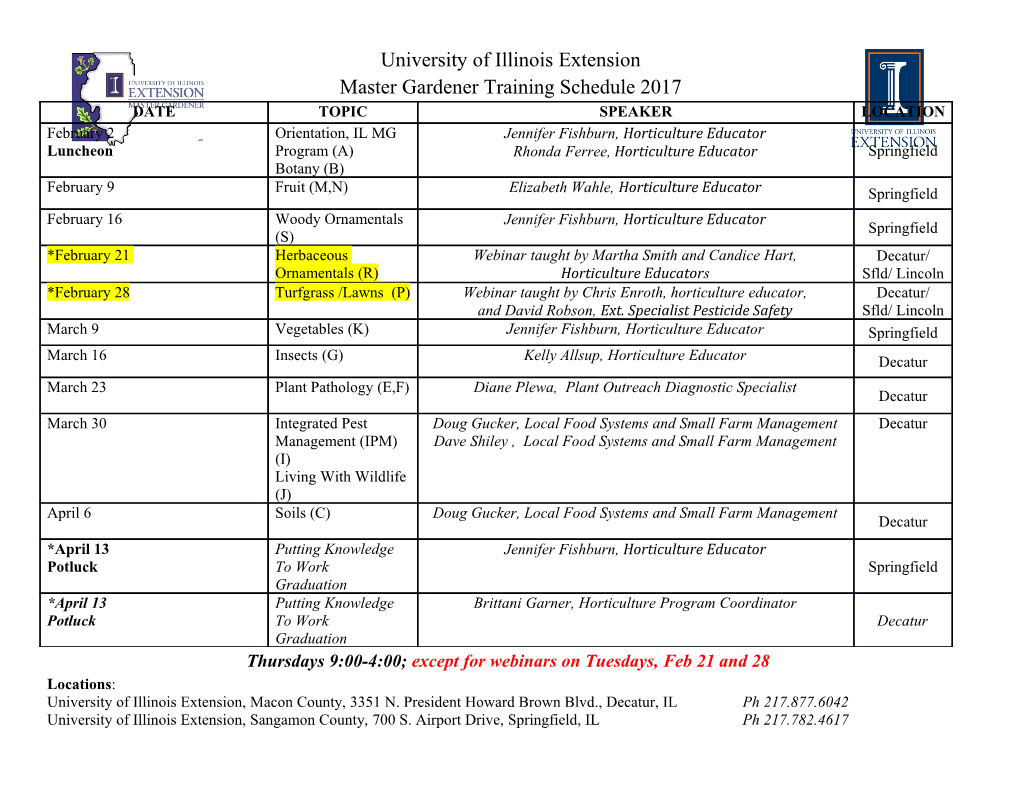
University of Tennessee, Knoxville TRACE: Tennessee Research and Creative Exchange Doctoral Dissertations Graduate School 5-2004 Laser Induced Surface Modification of Aluminium Alloys Subhadarshi Nayak University of Tennessee - Knoxville Follow this and additional works at: https://trace.tennessee.edu/utk_graddiss Part of the Materials Science and Engineering Commons Recommended Citation Nayak, Subhadarshi, "Laser Induced Surface Modification of Aluminium Alloys. " PhD diss., University of Tennessee, 2004. https://trace.tennessee.edu/utk_graddiss/2983 This Dissertation is brought to you for free and open access by the Graduate School at TRACE: Tennessee Research and Creative Exchange. It has been accepted for inclusion in Doctoral Dissertations by an authorized administrator of TRACE: Tennessee Research and Creative Exchange. For more information, please contact [email protected]. To the Graduate Council: I am submitting herewith a dissertation written by Subhadarshi Nayak entitled "Laser Induced Surface Modification of Aluminium Alloys." I have examined the final electronic copy of this dissertation for form and content and recommend that it be accepted in partial fulfillment of the requirements for the degree of Doctor of Philosophy, with a major in Materials Science and Engineering. Narendra B. Dahotre, Major Professor We have read this dissertation and recommend its acceptance: David C. Joy, Carl McHargue, Easo P. George Accepted for the Council: Carolyn R. Hodges Vice Provost and Dean of the Graduate School (Original signatures are on file with official studentecor r ds.) To the Graduate Council: I am submitting herewith a dissertation written by Subhadarshi Nayak entitled "Laser Induced Surface Modification of Aluminum Alloys". I have examined the final paper copy of this dissertation for form and content and recommend that it be accepted in partial fulfillment of the requirements for the degree of Doctor of Philosophy, with a major in lVlaterials Science and Engineering. Narendra B. Dahotre, Major Professor We have read this dissertation and recommend its acceptance: Accepted for the Council: Vice Chancellor 0 ·.j. .. ··· · ..•. I• •• ',' ,, ,. : � ' " ·.. .. •.. :, ' . · ' -·,"! . ;_.. ··:·. • !•: .,· Laser Induced Surface Modification of Aluminum Alloys A Dissertation Presented for the Doctor of Philosophy Degree The University of Tennessee, Knoxville Subhadarshi Nayak May 2004 To my alma mater Indian Institute of Technology, Kharagpur. ii Acknowledgments If I have seen further than others, it is by standing upon the shoulders of giants. -Newton. I am not sure if I have seen any further than others, but I know that without help, support, and encouragement from several persons, I would never have been able to finish this work. First of all, I would like to thank my adviser Dr. Narendra B. Dahotre, for helping me during the whole work with this dissertation. Thank you for providing me direction when I needed most I am very grateful to Drs David C. Joy, Carl McHargue and Easo P. George for serving in my committee, and providing valuable inputs. I also give a special thanks to Dr. Ian M. Anderson, Dr. Harry M. Meyer, lli, Ms. Laura Reister, Dr. Edward A. Kenik and Dr. Hsin Wang for fruitful collaboration and as co-authors and Dr. George M. Pharr for helping me understand nanoindentation. I acknowledge Ford Motor Company for partial funding of the research project. I appreciate Dr. Oludele Popoola of Ford Research Laboratory (presently with Zimmer Inc.) for his support and encouragement. Also GRA support from UTSI in the last semester is greatly appreciated. Thanks to Dr. Indranil Manna, Dr. B.S. Murty and Dr. K.K. Ray for instilling curiosity in me during undergraduate studies that led me to explore the fascinating world of materials little further. Thanks also to all my colleagues, especially Abhijeet, Anil, Anshul, Greg, Raghuvir, my friends and wing-mates from IIT-Kharagpur, roommate Kiran for all their support and help. At last, to my wife Jyoti, thanks for supporting me with your love and understanding, and also in mathematical concepts, programming and in LaTeX. I could not have finished this work without your support and help. iii Abstract Purpose of this work is to improve surface related properties of aluminum alloys by employing a laser based technique. Two approaches were taken to achieve this goal. First approach involves a rapid solidification induced by laser without any deliberate change in chemical composition. In second approach, laser was used to deposit Fe304 on A319, producing an Fe30.JAl reaction composite coating. In-situ high-speed infrared thermographs captured during laser surface melting of A319 enabled estimation of maximum temperature, temperature gradient and cooling rate. In light of limited spatial and time resolutions of the infrared camera, one­ dimensional heat transfer model was adopted for estimating the cooling rate The cooling rate thus estimated provided a range of cell size that closely matched with the experimentally observed cell size The high cooling rate (> 105 °C/s) resulted in extensive refinement of microstructure in the laser melted layer. Instrumented indentation technique was used to measure hardness (H) and elastic modulus (E) of the laser-melted layer. Berkovich tip was used to indent the material for 100-nm, 200-nm, 500-nm, and 1000-nm depths. The H and the E were found to be 1.22 GPa and 78.2 GPa, respectively, for 1000-nm indentation depths. The variances associated with H and E were minimal, whereas, the same for substrate possessed significant scattering. Also, H and E increased with decreasing depth of indentation. Closer examination suggested that when the heterogeneity in the material was in the scale of indentation depth, significant scattering took place and the hard.phase Si influenced the average hardness. However, the effect of indentation depth on elastic modulus was not statistically significant.The improvement in mechanical properties manifested in better wear resistance. IV Aluminum and Fe304 reacts readily in what is known as Thermite reaction. Infrared thermography was employed for diagnosing the thermal conditions during laser processing. Scanning Auger microscopy, transmission electron microscopy and x-ray diffraction techniques indicated a reaction between oxide particles and aluminum - forming FeAI intermetallic compounds, Ah03, and various intermediate reaction products. Analysis of the coating region, fractured in vacuuo, indicated substantial toughness of the material due to extremely refined microstructure with finelydistributed oxide and intermetallic particles and strong interfacial bonding between particles and the matrix. Mechanical properties of the coating were evaluated by nanoindentation techniques employing both Berkovich and cube-comer indenters. Hardness and elastic modulus values were found to be uniform at 1.24 and 76 GPa, respectively. No radial cracking was observed for either the Berkovich or cube-comer indenters. These results indicate that the laser-induced rapidly solidified composite material is tough and fracture resistant. v Contents 1 Introduction 1 2 Background and Hypothesis 3 2. 1 Surface and Surface Engineering 3 2.2 Aluminum Alloys 5 2.2.1 Cast Aluminum Alloys 6 2.2.2 Modification of Microstructure 20 2.2.3 Surface Engineering of Aluminum Alloys 23 2.3 Laser as a Engineering Tool 30 2.3.1 Laser as a Surface Engineering Tool 32 2.3.2 Surface Properties 36 3 Experimental Concepts 40 3.1 Materials and Processing 40 3.2 Process Diagnosis 42 3.3 Microscopyand Microanalysis 49 3.3.1 Energy Dispersive X-Ray (EDS) Microanalysis 51 3.3.2 Scanning Auger Microanalysis 52 3.3.3 Transmission Electron Microscopy 53 3.4 Mechanical Properties 54 3.4.1 Instrumented Indentation Technique 55 3.4.2 Abrasion and Wear 60 3.5 ThermoCalc 61 vi 4 Results and Analysis 63 4.1 Laser Melting and Rapid Solidification 63 4.1.1 Thermal Conditions During Processing 63 4.1.2 Evolution of Microstructure in Laser Melting 72 4.1.3 Improvement in Properties 79 4.2 Reaction Coating 92 4.2.1 Observation of Exothermic Reaction 92 4.2.2 Evolution of Microstructure in Reaction Coating 105 4.2.3 Mechanical Properties 125 5 Conclusion 140 Bibliography 142 Appendix 151 Vita 156 vii List of Tables 2.1 Properties of aluminum. 6 2.2 Alloying elements in aluminum casting. II 2.3 Chemical composition of A3 19. 18 2.4 Mechanical properties of A3 19. 19 4.1 Maximum temperatures during laser melting. 67 4.2 Surface cooling rate under non-steady state. 70 4.3 Surface cooling rate under steady state. 71 4.4 Properties derived from liT for 1000 run indentation depth. 81 4.5 Properties derived from liT w.r.t. indentation depth. 84 4.6 Scratch hardness (GPa). 89 4. 7 Maximum temperature during laser treatment. 95 4.8 Maximum temperature gradients at the periphery of laser melt-pool in the directions parallel and perpendicular to laser traverse. 101 4.9 Temperature corresponding to maximum gradients, Tmg· 101 4.10 Non-steady state cooling rates. 101 4.1 1 Steady state cooling rate in the directions opposite to laser traverse. 102 4.12 Reactions between Fe and AI [x Fe+ (1-x) AI-+ FexAio-x>l· 109 4.13 Summary of Auger spectroscopy data. 118 4.14 Nanoindentation (Berkovich) data fo r Fe304 coating. 126 4.15 Analysis of unloading data in liT. 131 4.16 Scratch hardness (GPa). 138 viii List of Figures 2.1 Al-Si phase diagram. 9 2.2 Schematic representing dendritic growth during solidification. 14 2.3 Flow diagram of the current work. 39 3 .I Schematic of the infrared thermography during laser processing. 43 3.2 Pixels of an infrared thermographduring laser processing. 45 3.3 Calibration of temperature vs. infrared intensity. 48 3.4 Indentation impressions on cross-section of the laser modified samples. 58 4.1 Temperature profile along the laser traverse path. 65 4.2 Optical micrographs of as-received A3 19. 72 4.3 SEM of the interface between laser melted layer and the substrate.
Details
-
File Typepdf
-
Upload Time-
-
Content LanguagesEnglish
-
Upload UserAnonymous/Not logged-in
-
File Pages170 Page
-
File Size-