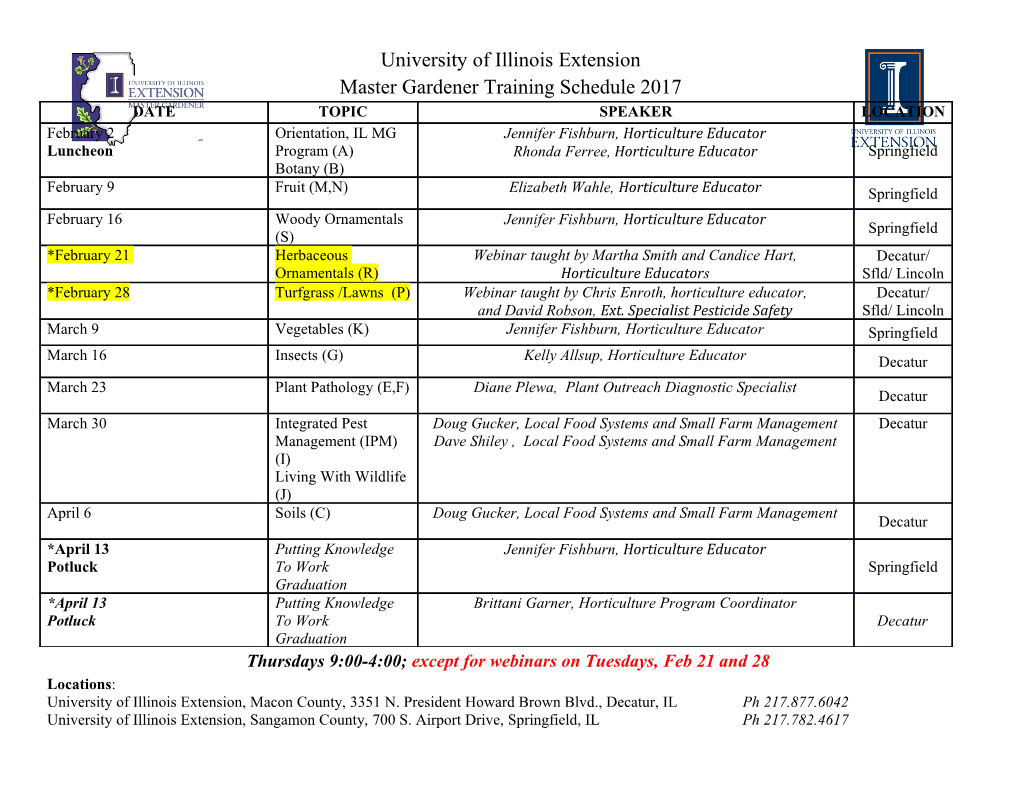
A Thesis entitled Monitoring of Surface Grinding process using Acoustic Emission (AE) with emphasis on Cutting Fluid selection by Tejas V. Nisal Submitted to the Graduate Faculty as partial fulfillment of the requirements for the Master of Science Degree in Industrial Engineering ________________________________________ Dr. Ioan D. Marinescu, Committee Chair ________________________________________ Dr. Efstratios Nikolaidis, Committee Member ________________________________________ Dr. Matthew Franchetti, Committee Member ________________________________________ Dr. Patricia R. Komuniecki, Dean College of Graduate Studies The University of Toledo August 2014 © Copyright 2014, Tejas V. Nisal This document is copyrighted material. Under copyright law, no parts of this document may be reproduced without the expressed permission of the author. An abstract of Monitoring of Surface Grinding process using Acoustic Emission (AE) with emphasis on Cutting Fluid selection by Tejas V. Nisal Submitted to the Graduate Faculty as partial fulfillment of the requirements for The Master of Science Degree in Industrial Engineering The University of Toledo August 2014 Correct selection of cutting fluid is an important step in all machining operations. In this study, experiments were designed and conducted on AISI 52100 steel to determine the effects of using different cutting fluids in Surface Grinding. The grinding parameters varied were wheel speed, feed, depth of cut and type of cutting fluid. The grinding responses studied here were Acoustic Emission (AE) Signals, Normal and Tangential Forces on the workpiece surface, Grinding Temperature and Surface Roughness. Potential of Acoustic Emission technique as a tool to provide efficient real-time knowledge and monitoring of the grinding process, is tested in this research. AERMS values were used to analyses the process characteristics. This paper proposes four different statistical models for predicting Grinding Temperature, Force, Acoustic Emission (AERMS) and Roughness, based on grinding parameters. This research concludes that the selection of Cutting Fluids influence the Surface finish, AE signals, Temperature iii and grinding Forces measured. Further, prediction of surface roughness during the grinding process using AE signal monitoring is demonstrated in this work. iv Acknowledgements First of all, I would like to express my sincere gratitude to my advisor, Dr. Marinescu, for giving me opportunity to do research under his supervision and for his exemplary guidance during my studies at The University of Toledo. I learned a lot through all the expert ideas provided by Dr. Marinescu. He always motivated me by giving me a couple of extra things to do in my research, just to keep me on my toes. I am also grateful to the thesis defense committee members Dr. Nikolaidis and Dr. Franchetti for spending time to read this thesis and providing useful suggestions. Special thanks to the faculty and staff at the MIME department for giving me the opportunity to continue my education here and kindly guiding me in maintaining the academic progress. I express my gratitude towards Mr. Todd Gearig, and Mr. John Jaegley, for the technical assistance throughout the research, in fabricating the fixtures and running the grinding machine. I would also like to thank Dr. Weismiller from Master Chemical Corp. for providing the grinding fluids and also for his useful suggestions. I highly appreciate the prompt technical support and friendly guidance provided by Mr. Tom Gigliotti and Dr. Ronnie Miller of Physical Acoustic Corp for using Acoustic Emission (AE) system. v A vote of thanks to all my colleagues-cum-friends at Precision Micro- Machining Center (PMMC), especially to Mr. Yin Guoxu and Mr. Aditya Dhulubulu, as we always worked together, and I believe that we made a good team. Last but not least, for always supporting me and keeping me motivated I specially thank my family and close friends in Toledo and elsewhere. vi Contents Abstract . iii Acknowledgments . v Table of Contents . vii List of Tables . x List of Figures . xi List of Abbreviation . xiii List of symbols . xiv 1. Introduction 1.1 Overview . 1 1.2 Objective . 2 2. Fundamentals and Literature Review 2.1 Cutting Fluids . 4 2.1.1 Neat cutting oils . 4 2.1.2 Gaseous cutting fluids . 6 2.1.3 Synthetic Fluids . 7 2.1.4 Emulsions cutting Fluids . 7 vii 2.1.5 Semi-synthetic fluids . 7 2.2 Monitoring of Surface grinding process . 8 2.3 Acoustic Emission . 2.3.1 Introduction to Acoustic Emission (AE) . 12 2.3.2 Use of Acoustic Emission in Manufacturing . 14 2.3.3 Acoustic Emission Signal recording and analysis 16 2.3.4 Acoustic Emission Setup a. Sensors. 22 b. Calibration . 24 c. Sensor Coupling . 25 d. Silicon rubber sealant . 26 2.4 AE Vs. Grinding Mechanism (theoretical) 2.4.1 Overview . 27 2.4.2 AE Vs. MRR (Literature review). 30 2.4.3 AE Vs. Forces (Literature review). 32 2.4.4 AE Vs. Temperature (Literature review) . 33 2.4.5 AE Vs. Surface roughness (Literature review). 35 2.4.6 AE Vs. Fluids (Literature review) . 38 2.5 Literature Review of use of AE related to Grinding Mechanism 40 3. Experimentation . 43 4. Results and Analysis . 50 viii 4.1 Effect of cutting fluid selection on AE, Normal forces, Roughness and Temperature . 55 4.2 Effect of grinding parameters on AE, Normal Forces, Roughness and Temperature . 63 4.3 Regression Modeling . 70 4.3.1 Grinding Force Model . 74 4.3.2 Acoustic Emission (AERMS) Model . 77 4.3.3 Surface Roughness Model . 80 4.3.4 Grinding Temperature Model . 83 4.4 Prediction of Surface Roughness (Ra) based on AERMS monitoring 86 4.5 Validation of Model . 88 5. Conclusion . 90 Reference . 94 ix List of Tables Table 1.1 Effects of different factors on AE . 15 Table 3.1 The specifics of the grinding conditions . 44 Table 3.2 Configuration parameters for AE monitoring system . 46 Table 3.3 Physical properties of four fluids used for the study . 49 Table 4.1 Design of Experiment . 52 Table 4.2 Grinding fluid characteristics . 59 Table 4.3 Physical properties of four fluids used for the study . 55 Table 4.4 Composition/information on ingredients . 60 Table 4.6 Validation of experiments . 89 x List of Figures Figure 1.1 Classification of Cutting fluids . 7 Figure 2.1 Parameters used to characterize emission events . 18 Figure 2.2 AE signals and power spectrum graphs . 20 Figure 2.3 Block diagram of Acoustic Emission system . 22 Figure 2.4 Schematic Cut section diagram of piezoelectric sensor . 23 Figure 2.5 Photo of actual sensors available in different sizes . 23 Figure 2.6 Sources of AE in Grinding at the grinding wheel-workpiece contact area . 28 Figure 3.1 Experiment set-up schematic . 44 Figure 3.2 Photo of the complete set-up for the experiments . 44 Figure 3.3 Photo of the workpiece and fixture set-up for experiment . 44 Figure 4.1 AERMS Values of two different grinding parameters and four xi replicates . 57 Figure 4.2 Shows variation in AE, Surface roughness, Normal Forces, and Temperature measurement with selection of four different cutting fluids . 58 Figure 4.3 Shows variation in AE, Surface roughness, Normal Forces, and Temperature measurement with increase in Depth of cut . 66 Figure 4.4 Shows variation in AE, Surface roughness, Normal Forces, and Temperature measurement with increase in Cutting speed . 67 Figure 4.5 Shows variation in AE, Surface roughness, Normal Forces, and Temperature measurement with increase in Feed rate . 68 Figure 4.6 Graph of Cutting force vs. DOC Vs. Feed and viscosity (Fluid) 75 Figure 4.7 Normal probability plot for normal force (F) . 76 Figure 4.8 Graph of AERMS vs. DOC vs. Feed and viscosity (Fluid) . 78 Figure 4.9 Normal probability plot for normal AERMS . 79 Figure 4.10 Graph of AERMS vs. DOC Vs. Feed and viscosity (Fluid) . 81 Figure 4.11 Normal probability plot for Surface roughness (Ra) . 82 xii Figure 4.12 Graph of Temperature vs. DOC vs. Feed and viscosity (Fluid) 84 Figure 4.13 Normal Probability plot for Temperature (˚F) . 85 Figure 4.14 Correlation Graphs of Acoustic Emission (AERMS) Vs. Surface roughness (Ra) . 87 xiii List of Abbreviations AE Acoustic Emission AET Acoustic Emission Technology RMS Root Mean Square AERMS Root Mean Square of the AE signal CNC Computerized Numerical Controls ASTM American Society of Testing and Materials NDT Non-Destructive testing xiv List of symbols η Fluid viscosity mPa S F Normal force in Newton (N) C Regression Constant α Regression constant β Regression constant γ Regression constant δ Regression constant Ra Average Surface Roughness d Depth of cut Vc Grinding wheel peripheral speed f Feed rate, or workpiece speed E Young’s modulus xv Chapter 1. Introduction 1.1 Overview Surface Grinding is a machining process that employs an abrasive grinding wheel which rotates at high speed to remove material from a comparatively softer workpiece surface. Surface grinding is a widely used machining process in the industry; because it can produce unparalleled surface quality, precise geometry, and better surface finish; with lower costs and higher material removal rates. Surface grinding machines can produce perfectly flat and/or smooth machine-part surfaces. In order to produce precision parts, these grinding machines must use grinding wheels whose dimensions are perfectly suited to the task. The grinding machine spins the grinding wheel very fast and holds it perfectly in place as the machine’s precision translation table moves the part being ground underneath the grinding wheel. Surface grinders are capable of removing as little as one ten-thousandth of an inch or less of material on each pass over a part. 1 1.2 Objective In the past, researchers have worked towards implementing real time monitoring of the grinding process, using different techniques like measurement of - grinding forces, surface temperature, vibrations, ultrasonic emissions and acoustic emissions.
Details
-
File Typepdf
-
Upload Time-
-
Content LanguagesEnglish
-
Upload UserAnonymous/Not logged-in
-
File Pages116 Page
-
File Size-